- お役立ち記事
- How to achieve both quality and productivity by improving manufacturing processes
How to achieve both quality and productivity by improving manufacturing processes
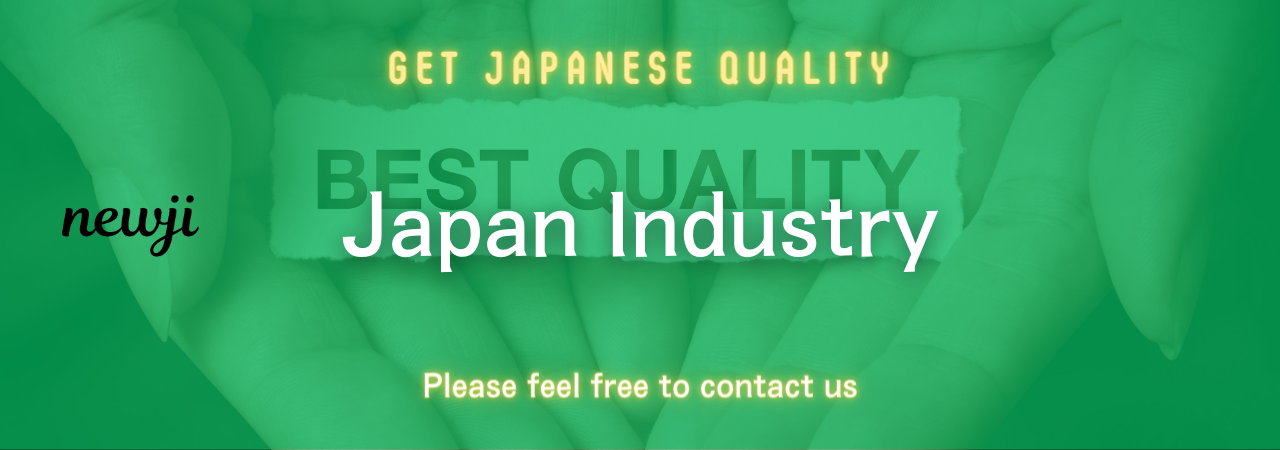
目次
Understanding the Importance of Quality and Productivity
Manufacturing is an intricate process involving multiple stages, from raw materials to final products.
Ensuring both high-quality output and maintaining productivity is vital for any manufacturing business aiming for success and sustainability.
But how can companies effectively balance these two critical components without one compromising the other?
In today’s competitive market, achieving quality and productivity simultaneously is not just a goal but a necessity.
Quality ensures customer satisfaction and loyalty, while productivity helps in maximizing profits and reducing costs.
The challenge lies in optimizing the manufacturing processes to enhance quality and boost productivity concurrently.
By reevaluating and refining these processes, manufacturers can discover potential areas of improvement that can lead to better overall performance.
Analyzing Current Manufacturing Processes
The first step in achieving this balance is to thoroughly analyze current manufacturing processes.
This involves understanding every stage of production, from procurement of raw materials to the delivery of the final product.
It’s crucial to identify the areas where quality issues arise or where productivity is below par.
Observing each phase closely will highlight inefficiencies and potential risks that could affect the production line.
Managers should collect data on equipment effectiveness, workflow, employee performance, and product quality.
This data-driven approach will provide valuable insights into the strengths and weaknesses of the current system.
Implementing Lean Manufacturing Techniques
One effective way to enhance both quality and productivity is by implementing lean manufacturing techniques.
Lean manufacturing focuses on minimizing waste within the production processes while maximizing productivity.
By adopting these techniques, manufacturers can streamline operations, reduce costs, and improve product quality.
Lean manufacturing encourages practices such as just-in-time production, which reduces inventory levels and lowers waste, and continuous improvement (Kaizen), which emphasizes constant small changes in the manufacturing process leading to improvements in efficiency and quality.
Utilizing Advanced Technology
Incorporating advanced technology is another critical strategy for improving manufacturing processes.
Automation, robotics, and artificial intelligence can significantly enhance efficiency and quality control.
These technologies offer precise control over manufacturing operations, reducing the likelihood of human error and standardizing production quality.
Automation and robotics can help speed up repetitive tasks, freeing workers to focus on more complex and quality-focused tasks.
On the other hand, AI can be instrumental in quality control by identifying defects and ensuring products meet the desired standards.
Employee Training and Involvement
While technology and systems play a vital role in improving manufacturing processes, employees are equally crucial.
Training programs that focus on quality standards and productivity techniques can significantly enhance the workforce’s skills.
By involving employees in the decision-making process, they become more invested in the outcome, often leading to innovative ideas for process improvements.
Regular workshops and training sessions can help instill a culture of continuous improvement and quality focus amongst employees.
Quality Control and Monitoring
Implementing robust quality control systems is indispensable in maintaining high product standards.
Quality control ensures that products meet the specifications and standards before they reach the market.
Setting up regular quality monitoring systems can result in early detection of defects, reducing waste and the cost of rework.
Technological solutions, such as sensors and computer vision, can automate these quality checks, making them more efficient and effective.
Improving Supplier Relationships
The quality of the final product is often dependent on the raw materials used.
Maintaining a good relationship with suppliers can ensure the consistent supply of high-quality materials.
By collaborating closely with suppliers, manufacturers can achieve timely deliveries and reduce quality issues originating from raw materials.
A strong supplier relationship can also lead to shared innovations and cost reduction strategies, benefiting both parties.
Continuous Improvement Efforts
The journey towards achieving high quality and productivity is ongoing, requiring continuous assessment and improvement.
Manufacturers should regularly review their processes, adapting to new technologies, market demands, and feedback.
Implementing a culture of continuous improvement means staying ahead of potential issues and responding quickly to changes.
This approach leads to a dynamic manufacturing process capable of producing outstanding quality while maximizing productivity.
Balancing Cost and Quality
One of the critical challenges in manufacturing is balancing cost with quality.
Reducing costs typically implies cutting corners, which can compromise quality.
However, strategic improvements in production processes can simultaneously lead to cost savings and enhanced quality.
Identifying non-value adding processes and eliminating them can reduce unnecessary expenses.
Investing in technology and employee training, although initially costly, often results in significant long-term savings and improvement in quality.
Setting Clear Objectives
For process improvements to be successful, setting clear and achievable objectives is crucial.
Defining what constitutes quality and productivity within the organization allows for targeted improvements and measurement of success.
Objectives should be specific, measurable, achievable, relevant, and time-bound (SMART).
With clear goals in place, every member of the organization can work towards a common purpose, resulting in better alignment and achievement of desired outcomes.
Conclusion
Improving manufacturing processes to enhance quality and productivity requires a holistic approach involving technology, employee engagement, and systems thinking.
While balancing these two elements may seem challenging, the right strategies can lead to significant improvements.
By implementing lean manufacturing techniques, leveraging technology, fostering strong supplier relationships, and promoting continuous improvement, manufacturers can achieve outstanding product quality while maximizing productivity.
These efforts ultimately translate into increased customer satisfaction, competitive advantage, and robust bottom-line performance.
資料ダウンロード
QCD調達購買管理クラウド「newji」は、調達購買部門で必要なQCD管理全てを備えた、現場特化型兼クラウド型の今世紀最高の購買管理システムとなります。
ユーザー登録
調達購買業務の効率化だけでなく、システムを導入することで、コスト削減や製品・資材のステータス可視化のほか、属人化していた購買情報の共有化による内部不正防止や統制にも役立ちます。
NEWJI DX
製造業に特化したデジタルトランスフォーメーション(DX)の実現を目指す請負開発型のコンサルティングサービスです。AI、iPaaS、および先端の技術を駆使して、製造プロセスの効率化、業務効率化、チームワーク強化、コスト削減、品質向上を実現します。このサービスは、製造業の課題を深く理解し、それに対する最適なデジタルソリューションを提供することで、企業が持続的な成長とイノベーションを達成できるようサポートします。
オンライン講座
製造業、主に購買・調達部門にお勤めの方々に向けた情報を配信しております。
新任の方やベテランの方、管理職を対象とした幅広いコンテンツをご用意しております。
お問い合わせ
コストダウンが利益に直結する術だと理解していても、なかなか前に進めることができない状況。そんな時は、newjiのコストダウン自動化機能で大きく利益貢献しよう!
(Β版非公開)