- お役立ち記事
- 不良の発生要因とトラブル対策・事例
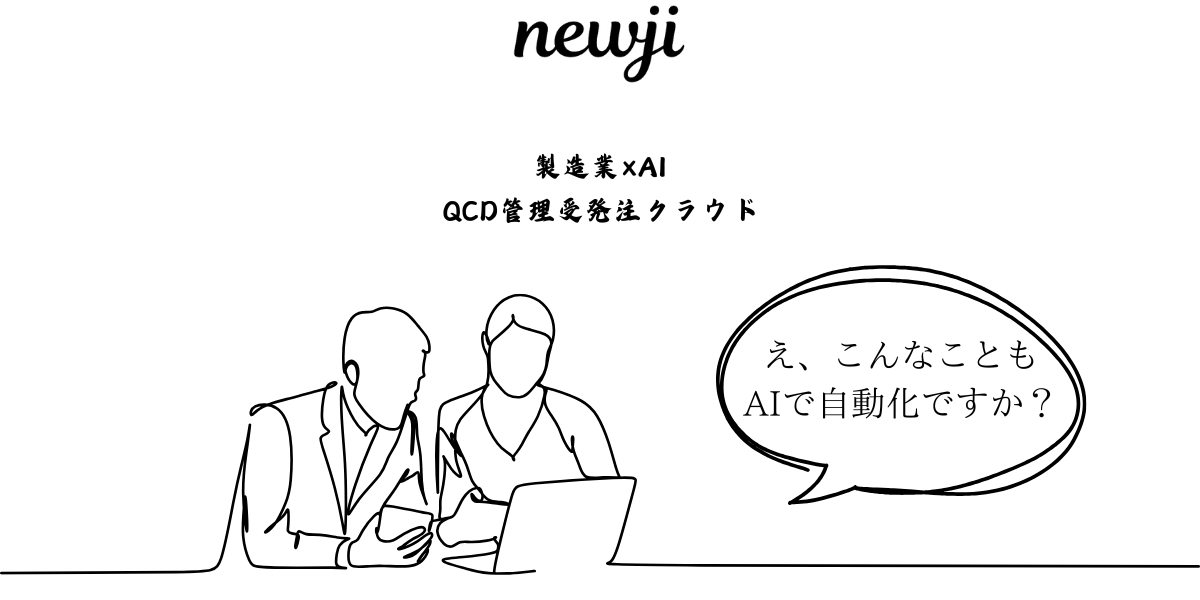
不良の発生要因とトラブル対策・事例
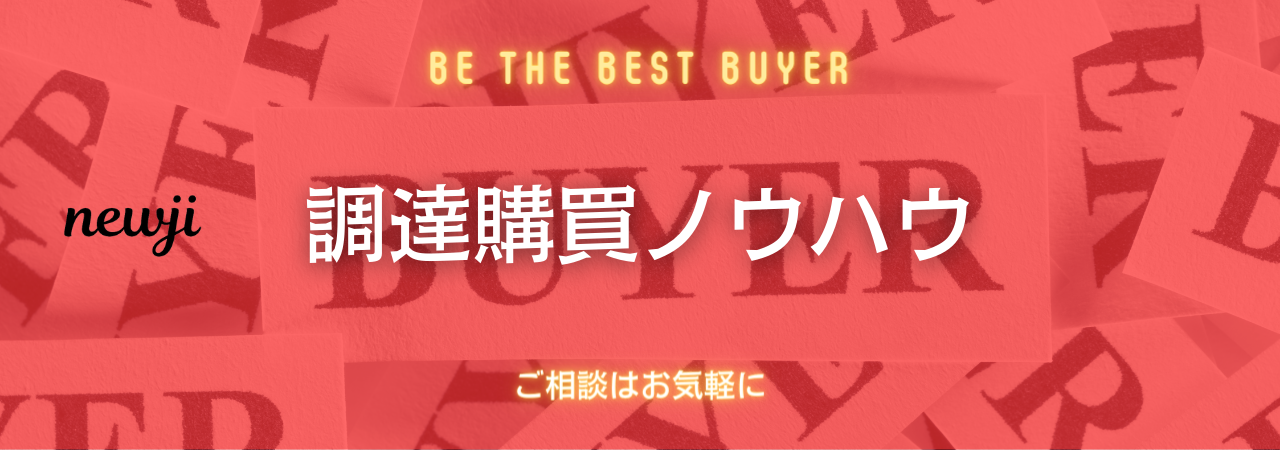
目次
製造業における不良の発生要因
製造業の現場では、不良品の発生は避けて通れない問題となっています。
不良品が発生する要因は一つではなく、複数の要因が絡み合うことで発生することが多いです。
以下に代表的な不良の発生要因を挙げ、理解を深めていきたいと思います。
人的要因
製造現場における人の作業ミスや不注意は、不良品の大きな要因のひとつです。
特に新入社員や異部署からの異動者など、経験が不足している際に発生することが多いです。
また、マニュアル通りではなく作業員の独自解釈により、意図しない手順で作業を進めてしまうケースもあります。
これを防ぐためには、継続的な教育訓練や作業標準の明確化が必要になります。
設備要因
製造設備の老朽化や故障も不良の原因となります。
特にメンテナンスが不十分な場合、設備の誤動作が発生し、結果的に不良品が生産されることがあります。
また、新しい設備を導入した際にも、初期段階での調整不良や操作ミスが原因となることがあります。
定期的なメンテナンスや設備のチェックシートによる管理が重要です。
材料要因
使用する材料自体に問題がある場合も、不良品の発生要因となります。
材料の品質が一定でない場合や、適切な保管がされていない場合、製品の品質に影響を及ぼします。
サプライヤーとの密接なコミュニケーションと、受け入れ時の厳密な品質チェックが不良防止に寄与します。
工程要因
工程設計やプロセスフローに問題がある場合も、不良発生の原因となります。
例えば、工程間での手間が多すぎる場合や複雑すぎる作業は、不良発生のリスクが増加します。
生産ラインの最適化や、工程の見直しを定期的に行うことで、効率化と不良品の削減が期待できます。
トラブル対策の基本戦略
不良品の発生を完全にゼロにすることは難しいかもしれませんが、発生を最小限に抑えるための対策を実施することは可能です。
以下に、一般的なトラブル対策の基本戦略を紹介します。
原因分析
不良が発生した際には根本原因を特定することが重要です。
なぜその不良が発生したのかを追求し、適切な対策を立てるために、5 Why分析や魚の骨図(特性要因図)などの手法を用いることが有効です。
これにより、表面的な対応だけでなく、根本的な問題解決が可能となります。
品質管理システムの整備
ISO 9001などの品質管理システムを導入し、全社的な品質管理体制を整えることも有効です。
標準作業書の整備や、作業手順の統一、トラブル発生時の対応手順を明確にすることで、組織全体の品質レベルを向上させることができます。
定期的な教育訓練
人的要素が関与する場面では、従業員の教育訓練が不可欠です。
定期的な研修や勉強会、技能検定を講じることで、作業者の意識を高め、ミスの発生を未然に防ぐことができるでしょう。
設備保全活動の強化
設備が不良の原因となる場合、設備保全活動を強化することが考えられます。
予知保全や予防保全、TPM(総合的生産管理活動)などの手法を導入し、設備故障を未然に防ぐ取り組みを重視することが重要です。
サプライヤーとの連携強化
材料要因による不良を防ぐためには、サプライヤーとの連携が不可欠です。
定期的な品質監査や、双方向の情報共有を行うことで、原材料の品質を安定させることが可能です。
不良対策事例
実際に不良を未然に防ぐための対策を講じた事例をいくつか紹介します。
事例1: 自動車部品メーカーの工程改善
ある自動車部品メーカーでは、組み立て工程での不良発生率が高かったため、工程改善プロジェクトを立ち上げました。
現場の工程を再チェックし、ボトルネックの解消や一部分の自動化を図ることで、完了時点での不良発生率を30%削減することができました。
この事例は、生産ラインの流れを見直し、効率性を追求することで不良が減少した成功例です。
事例2: 電子機器製造業の品質管理の見直し
電子機器製造業では、製品の特性上、微細な不良が後の大きなトラブルにつながる可能性がありました。
そこで、品質管理体制を見直し、検査装置の導入とともに、AIを活用した不良検出システムを採用しました。
結果として、最小の不良を早期発見が可能となり、大幅に返品率を低下させることができました。
事例3: 化学工場での材料管理改善
ある化学工場では、原料の水分含有量にばらつきがあり、最終製品にばらつきが生じていたため、材料管理を強化することにしました。
原料の受け入れ時に水分計を使用し、適正な数値であることを確認した後、保管場所の温湿度管理を严格化しました。
この改善活動により、製品品質の安定性が向上し、顧客からのクレームが大幅に減少しました。
まとめ
製造業における不良発生は様々な要因が絡み合って起こるため、統一的で広範囲な解決策が求められます。
人的、設備、材料、工程といった異なる角度からのアプローチが必要です。
また、事例からも分かるように、各企業で採られているトラブル対策は、その製品や業種に応じた独自の対策が存在しています。
不良発生を未然に防ぐだけでなく、発生した際の迅速な原因特定と対策立案を行うことが重要です。
これにより、製品品質の維持・向上が図れ、ひいては企業の信頼性と競争力の向上につながるでしょう。
製造業界に従事する皆様が、日々の業務においてこれらの知見を活かすことを願っております。
資料ダウンロード
QCD調達購買管理クラウド「newji」は、調達購買部門で必要なQCD管理全てを備えた、現場特化型兼クラウド型の今世紀最高の購買管理システムとなります。
ユーザー登録
調達購買業務の効率化だけでなく、システムを導入することで、コスト削減や製品・資材のステータス可視化のほか、属人化していた購買情報の共有化による内部不正防止や統制にも役立ちます。
NEWJI DX
製造業に特化したデジタルトランスフォーメーション(DX)の実現を目指す請負開発型のコンサルティングサービスです。AI、iPaaS、および先端の技術を駆使して、製造プロセスの効率化、業務効率化、チームワーク強化、コスト削減、品質向上を実現します。このサービスは、製造業の課題を深く理解し、それに対する最適なデジタルソリューションを提供することで、企業が持続的な成長とイノベーションを達成できるようサポートします。
オンライン講座
製造業、主に購買・調達部門にお勤めの方々に向けた情報を配信しております。
新任の方やベテランの方、管理職を対象とした幅広いコンテンツをご用意しております。
お問い合わせ
コストダウンが利益に直結する術だと理解していても、なかなか前に進めることができない状況。そんな時は、newjiのコストダウン自動化機能で大きく利益貢献しよう!
(Β版非公開)