- お役立ち記事
- 生産管理における効果的な現場改善・問題解決の実践ノウハウ
生産管理における効果的な現場改善・問題解決の実践ノウハウ
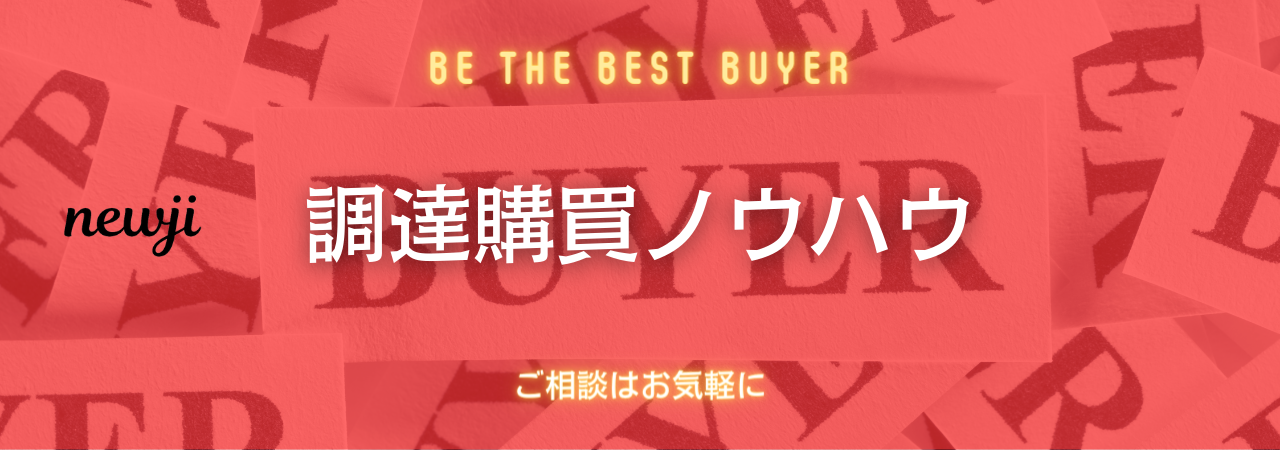
目次
生産管理の基本とその重要性
生産管理は製造業の心臓部とも言える存在で、生産活動を効率的に進めるための重要な役割を担っています。
適切な生産管理は、コスト削減や納期遵守、品質向上につながり、企業の競争力を高めます。
そこで重要となるのが、現場での問題を迅速に解決し、継続的な改善を行う能力です。
生産管理における改善や問題解決は、単なる対処療法ではありません。
現場目線の具体的な課題を理解し、根本原因を追求することが必要です。
昭和から続くアナログ的なアプローチを乗り越え、デジタル化や自動化を推進することも不可欠です。
現場改善のステップを理解する
現場改善は、課題の特定からスタートします。
課題を洗い出し、現状分析を行い、具体的な問題を見つけることが重要です。
ここでは、品質、コスト、納期の3つの視点から現場改善のステップを見ていきます。
問題の見える化
問題を正確に把握するためには、現場でのデータ収集と情報共有が基本です。
作業者からのフィードバックや、日常的に行う業務の中で何がネックになっているのかを観察することから始めましょう。
デジタルツールやIoT機器を活用して、リアルタイムでデータを収集し、視覚的に問題を見える化することが望まれます。
原因の特定と分析
問題が明らかになったら、次はその原因を細かく分析します。
品質やコストに関する問題は、多くの場合、作業手順や人員配置、設備の老朽化などが影響していることが多いです。
5W1H (Who, What, When, Where, Why, How) や、なぜなぜ分析を活用して、根本原因を探り出しましょう。
効果的な問題解決手法
問題解決には、緻密な計画と実行力が求められます。
効果的な問題解決手法には、PDCAサイクルと新QC七つ道具の活用があります。
PDCAサイクル
Plan(計画)、Do(実行)、Check(確認)、Act(改善)という4つの段階を繰り返すのがPDCAサイクルです。
計画段階では、目標を設定し、具体的な改善策を策定します。
次に実行段階で、計画に従い実際の改善活動を行います。
確認段階では、成果を評価し、問題点を再度洗い出します。
最後に改善段階で、新たに設定した対策を取り入れるという流れです。
新QC七つ道具
問題解決に役立つ「新QC七つ道具」は、ブレーンストーミング、親和図、連関図法、系統図法、マトリックス図法、アローダイアグラム法、PDPC法です。
これらは、複雑な問題を整理し、分析するための強力なツールとして活用されています。
特に、親和図や連関図法は複数の要因が絡み合う問題に対する理解を深める助けになります。
組織全体での改善文化の醸成
どんなに優れた個別の改善策も、組織全体での協力があってこそ効果を発揮します。
改善文化を醸成するためには、以下の要素が大切です。
現場力を高めるリーダーシップ
リーダーシップは、現場改善の成否を左右する重要な要素です。
管理職やリーダーが率先して改善活動を推進し、現場スタッフにフィードバックを与えることで、組織全体の改善意識を高められます。
また、リーダーは透明性のある情報共有と、スタッフの意見を積極的に取り入れる姿勢を持つことが求められます。
継続的な教育とトレーニング
継続的な教育とトレーニングにより、スタッフのスキルと問題解決能力を向上させることができます。
社内での勉強会や外部セミナーへの参加を奨励し、リーダーとなる人材を育てる仕組みを整備しましょう。
最新の調達、品質管理、自動化技術に関する情報を常にアップデートすることも重要です。
アナログからデジタルへの移行と自動化の推進
昭和からのアナログ手法がまだ根強く残る製造業界ですが、デジタル技術を導入することで、さらなる改善と効率化が可能になります。
デジタル化と自動化は、以下の方法で推進することができます。
IoTとスマートファクトリーの実現
IoT(インターネット・オブ・シングス)技術を活用すれば、作業のリアルタイム監視やデータ収集が可能となります。
これにより、設備の故障予測や、エネルギー使用量の最適化が進みます。
スマートファクトリーを目指し、工場内のシステム連携を促進しましょう。
AIによる予測と自動化の活用
AI(人工知能)技術を導入することで、需要予測や品質管理、在庫最適化などの高度な判断を自動化できます。
特に製品の不良率の予測や需給バランスの最適化において、AIの分析能力は顕著な結果をもたらします。
AIを利用したオートメーションにより、作業の精度を高め、生産性向上に寄与します。
現場改善の成功事例から学ぶ
現場改善の成功事例を知ることは、自社での取り組みへの大きなヒントになります。
ここでは、いくつかの成功事例を紹介し、そのエッセンスを学びましょう。
トヨタ生産方式の導入
トヨタ生産方式(TPS)は、ジャストインタイム(JIT)と呼ばれる生産方式で、多品種少量生産を効率的に行う手法です。
この方法の成功要因は、ムダを排除し、品質を第一に考えた柔軟な生産プロセスにあります。
TPSから学ぶべきは、問題を早期に発見し、柔軟に対応する姿勢です。
シックスシグマによる品質向上
シックスシグマとは、統計的方法を用いて製造工程の変動を最小化し、品質向上を図るための経営手法です。
この手法を導入することで、製品不良の発生率を劇的に低下させることが可能です。
成功事例からは、詳細なデータ分析と継続的な改善活動の重要性を学ぶことができます。
まとめ
生産管理における効果的な現場改善と問題解決は、競争力の維持と向上に欠かせない要素です。
問題の見える化やデジタル化の推進、組織全体での協力体制の構築が求められます。
過去の成功事例を基に改善のヒントを得ながら、現場の声に耳を傾け、絶え間ない改革を続けることが、製造業の持続的成長につながるでしょう。
資料ダウンロード
QCD調達購買管理クラウド「newji」は、調達購買部門で必要なQCD管理全てを備えた、現場特化型兼クラウド型の今世紀最高の購買管理システムとなります。
ユーザー登録
調達購買業務の効率化だけでなく、システムを導入することで、コスト削減や製品・資材のステータス可視化のほか、属人化していた購買情報の共有化による内部不正防止や統制にも役立ちます。
NEWJI DX
製造業に特化したデジタルトランスフォーメーション(DX)の実現を目指す請負開発型のコンサルティングサービスです。AI、iPaaS、および先端の技術を駆使して、製造プロセスの効率化、業務効率化、チームワーク強化、コスト削減、品質向上を実現します。このサービスは、製造業の課題を深く理解し、それに対する最適なデジタルソリューションを提供することで、企業が持続的な成長とイノベーションを達成できるようサポートします。
オンライン講座
製造業、主に購買・調達部門にお勤めの方々に向けた情報を配信しております。
新任の方やベテランの方、管理職を対象とした幅広いコンテンツをご用意しております。
お問い合わせ
コストダウンが利益に直結する術だと理解していても、なかなか前に進めることができない状況。そんな時は、newjiのコストダウン自動化機能で大きく利益貢献しよう!
(Β版非公開)