- お役立ち記事
- Corrosion basics and test methods
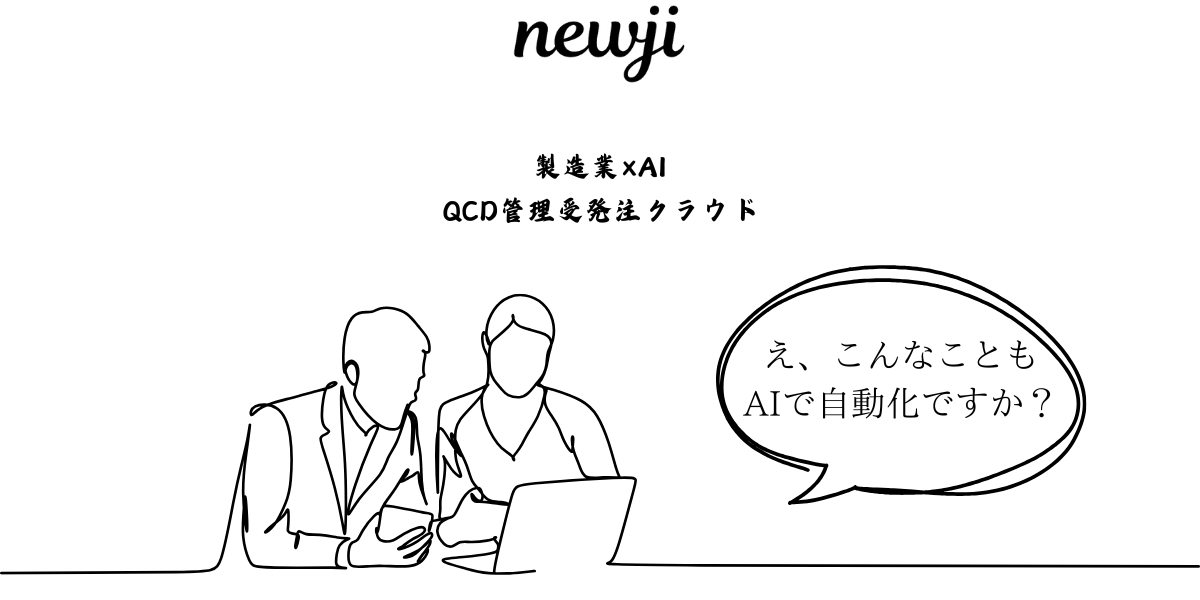
Corrosion basics and test methods
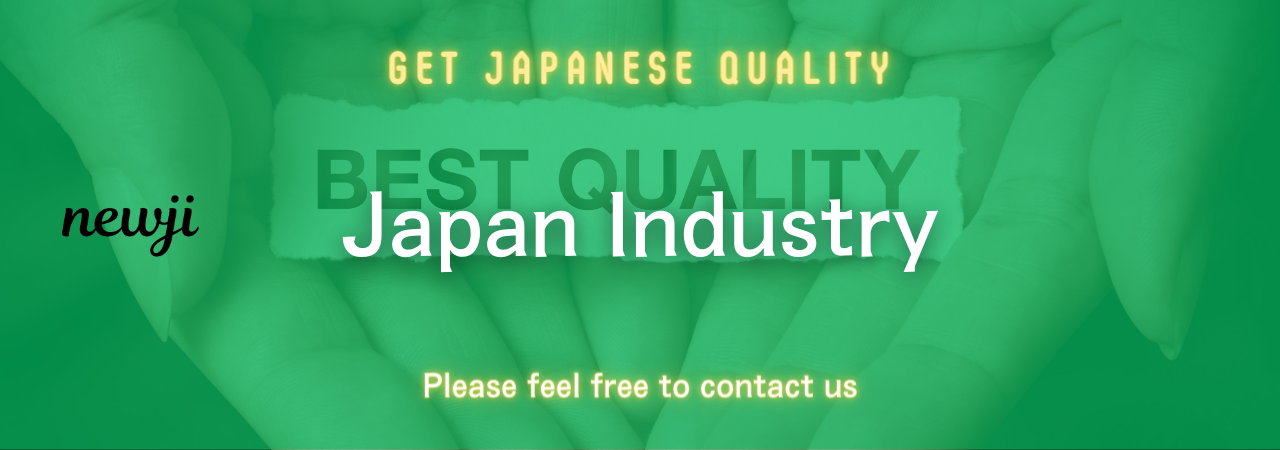
目次
Understanding Corrosion
Corrosion is a natural process that gradually destroys materials through chemical or electrochemical reactions with their surroundings.
It primarily affects metals, causing them to deteriorate over time.
The most common type of corrosion is rust, which affects iron and its alloys.
When these metals react with oxygen and moisture, they form iron oxide, commonly known as rust.
Corrosion is not limited to metals; it can also affect non-metals like ceramics and polymers.
However, metals are more prone to corrosion due to their reactive nature.
Understanding corrosion is crucial because it can lead to significant economic losses, structural failures, and safety hazards.
Causes of Corrosion
Corrosion occurs due to various factors, which can be broadly categorized into chemical, electrochemical, and environmental causes.
Chemical Causes
Chemical corrosion happens when metals react directly with chemicals.
For example, exposure to acids or alkalis can lead to corrosion.
Industries that use or produce chemicals, such as chemical manufacturing plants, are particularly susceptible to this type of corrosion.
Electrochemical Causes
Electrochemical corrosion is the most common form and involves the transfer of electrons between materials.
This type occurs in the presence of an electrolyte, which conducts electricity.
A classic example is the corrosion of metal pipes buried underground, where moisture in the soil acts as an electrolyte.
Environmental Causes
Environmental factors such as temperature, humidity, and air pollution can accelerate the corrosion process.
For instance, in coastal regions, salt in the air can enhance corrosion, especially in vehicles and infrastructure.
Additionally, industrial emissions can lead to acidic rain, further contributing to corrosion.
Types of Corrosion
Corrosion manifests in various forms, each with distinct characteristics and implications.
Uniform Corrosion
Uniform corrosion, also known as general corrosion, affects a metal surface uniformly.
It results in an even layer of rust or corrosion product over the surface.
While it causes material thinning, it is predictable and can be monitored with regular inspections.
Pitting Corrosion
Pitting corrosion is a localized form that creates small, deep pits on the material’s surface.
Despite minimal surface damage, pits can lead to unexpected and catastrophic failures.
Detecting pitting corrosion can be challenging, making it a more dangerous form of corrosion.
Galvanic Corrosion
Galvanic corrosion occurs when two dissimilar metals come into contact in the presence of an electrolyte.
The less noble metal, known as the anode, corrodes faster, while the more noble metal, the cathode, is protected.
This is commonly seen in situations where different metals are used together, such as in plumbing systems.
Crevice Corrosion
Crevice corrosion takes place in shielded areas or crevices where access to the environment is limited.
These areas can trap moisture, leading to aggressive localized corrosion.
Crevice corrosion is common in joints, gaskets, and other assembled metal components.
Stress Corrosion Cracking (SCC)
Stress corrosion cracking is the result of the combined effect of tensile stress and corrosive environments.
It leads to the formation of cracks, which can propagate rapidly, resulting in sudden failure.
SCC is particularly concerning for industries where high-stress components are exposed to corrosive environments.
Corrosion Prevention Methods
Preventing corrosion requires a combination of material selection, protective coatings, and environmental control.
Material Selection
One of the most effective ways to prevent corrosion is to choose materials resistant to corrosion.
For instance, stainless steel contains chromium, which forms a passive layer, protecting it from corrosion.
Similarly, non-metallic materials like plastics and ceramics can be used in corrosive environments.
Protective Coatings
Applying protective coatings is a common method to prevent corrosion.
These coatings act as a barrier between the metal and the environment.
Common coatings include paint, galvanization (zinc coating), and anodizing (aluminum oxide layer).
Regular maintenance of these coatings is essential to ensure long-term protection.
Cathodic Protection
Cathodic protection is a technique used to control electrochemical corrosion.
This method involves connecting the metal to be protected to a more easily corroded sacrificial metal (anode).
The sacrificial anode corrodes instead, shielding the main metal from damage.
This technique is widely used in pipelines and ship hulls.
Environmental Control
Controlling the environment is another effective way to prevent corrosion.
This includes reducing humidity, removing pollutants, and maintaining a stable temperature.
Industries can implement ventilation and dehumidification systems to create a less corrosive environment.
Corrosion Testing Methods
To assess the corrosion resistance of materials, various testing methods are employed.
Salt Spray Test
The salt spray test evaluates a material’s resistance to salt-induced corrosion.
Materials are exposed to a salt-laden mist in a controlled chamber.
The test duration ranges from hours to weeks, providing insights into the material’s long-term performance in saline environments.
Electrochemical Testing
Electrochemical testing involves measuring the electrochemical properties of materials, such as potential and current density.
These tests provide information about the corrosion rate, helping predict material performance in specific conditions.
Immersion Testing
Immersion testing involves immersing materials in a corrosive solution for a specified period.
This test simulates real-world exposure conditions, allowing for the assessment of long-term corrosion behavior.
Environmental Testing
Environmental testing subjects materials to simulated environmental conditions, such as humidity, temperature fluctuations, and pollutants.
These tests help evaluate how materials perform under various environmental factors.
Conclusion
Understanding the basics of corrosion and testing methods is essential for preventing damage and extending the life of materials.
By implementing appropriate prevention techniques and conducting regular tests, industries can mitigate the risks associated with corrosion and ensure the safety and longevity of their products and infrastructure.
資料ダウンロード
QCD調達購買管理クラウド「newji」は、調達購買部門で必要なQCD管理全てを備えた、現場特化型兼クラウド型の今世紀最高の購買管理システムとなります。
ユーザー登録
調達購買業務の効率化だけでなく、システムを導入することで、コスト削減や製品・資材のステータス可視化のほか、属人化していた購買情報の共有化による内部不正防止や統制にも役立ちます。
NEWJI DX
製造業に特化したデジタルトランスフォーメーション(DX)の実現を目指す請負開発型のコンサルティングサービスです。AI、iPaaS、および先端の技術を駆使して、製造プロセスの効率化、業務効率化、チームワーク強化、コスト削減、品質向上を実現します。このサービスは、製造業の課題を深く理解し、それに対する最適なデジタルソリューションを提供することで、企業が持続的な成長とイノベーションを達成できるようサポートします。
オンライン講座
製造業、主に購買・調達部門にお勤めの方々に向けた情報を配信しております。
新任の方やベテランの方、管理職を対象とした幅広いコンテンツをご用意しております。
お問い合わせ
コストダウンが利益に直結する術だと理解していても、なかなか前に進めることができない状況。そんな時は、newjiのコストダウン自動化機能で大きく利益貢献しよう!
(Β版非公開)