- お役立ち記事
- Revitalizing Japan: The Future of Employment in the Manufacturing Industry
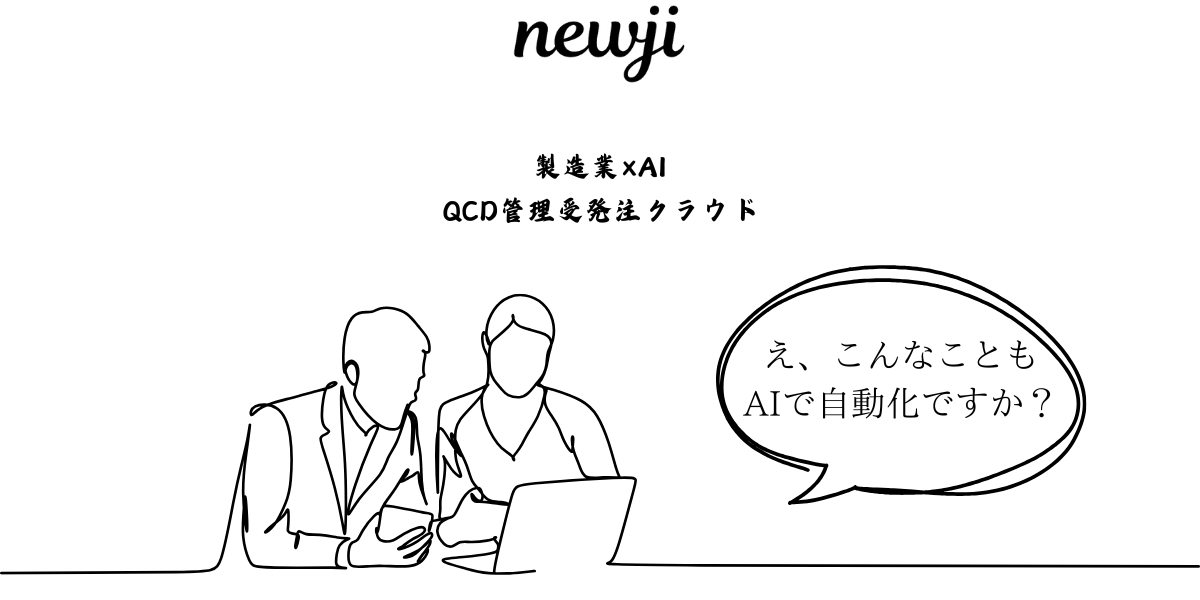
Revitalizing Japan: The Future of Employment in the Manufacturing Industry
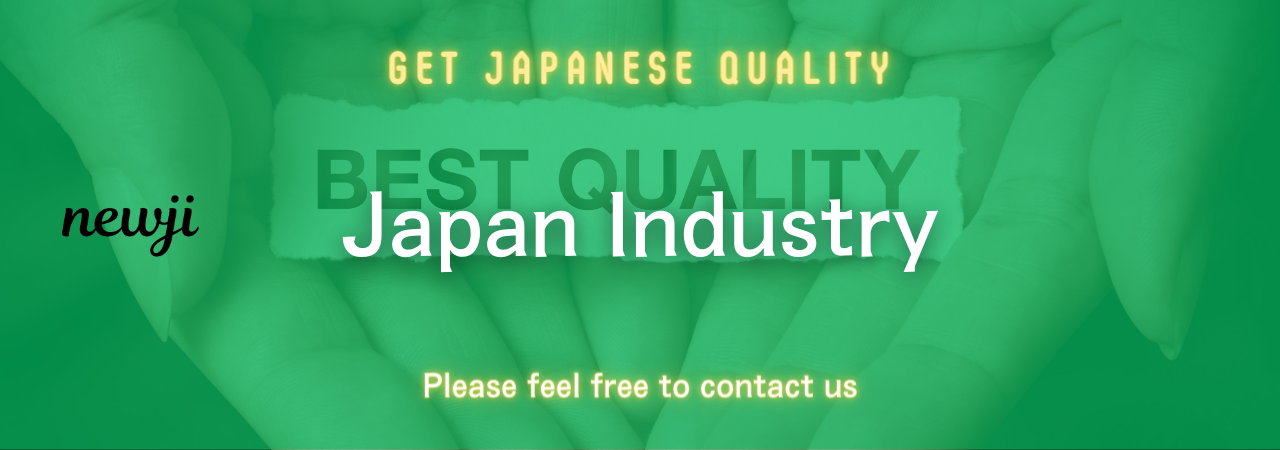
目次
Introduction
Japan’s manufacturing industry has long been a cornerstone of its economy.
The sector is renowned for its precision, quality, and innovation.
As global markets evolve, the future of employment within this industry faces both challenges and opportunities.
This article explores the revitalization of Japan’s manufacturing employment landscape.
It delves into current market conditions, the impact of automation, and the strategies needed to sustain growth.
Additionally, it examines best practices in procurement and supplier negotiations that influence employment trends.
Current State of Japanese Manufacturing Employment
Industry Overview
Japan’s manufacturing sector is a major contributor to its GDP.
Key industries include automotive, electronics, machinery, and chemical production.
The sector is characterized by its high levels of productivity and technological advancement.
However, it faces significant challenges such as an aging workforce and declining domestic demand.
These factors create a pressing need for revitalization to maintain its global competitive edge.
Employment Trends
Employment in Japanese manufacturing has been steadily declining over the past decade.
This trend is primarily due to increased automation and the integration of advanced technologies.
While automation enhances efficiency, it reduces the demand for manual labor.
Moreover, the aging population results in a shrinking pool of skilled workers.
These dynamics necessitate a strategic approach to workforce development and retention.
Future Employment Prospects
Automation and Robotics
The adoption of automation and robotics is transforming the manufacturing landscape.
Robots are increasingly handling repetitive and hazardous tasks, improving safety and precision.
This shift allows human workers to focus on more complex and creative roles.
However, it also requires employees to possess new skill sets, emphasizing the need for continuous education and training programs.
Technological Advancements
Emerging technologies such as artificial intelligence, the Internet of Things (IoT), and additive manufacturing are reshaping the industry.
These technologies enhance production capabilities and enable smarter decision-making.
They also create new job opportunities in areas like data analysis, machine maintenance, and systems integration.
Embracing these advancements is crucial for sustaining employment growth in the manufacturing sector.
Strategies for Workforce Development
Training and Education
Investing in training and education is vital to equip the workforce with the necessary skills.
Collaborations between industry and educational institutions can facilitate curriculum development tailored to industry needs.
Vocational training programs focused on technical skills, such as robotics operation and maintenance, are essential.
Additionally, fostering a culture of lifelong learning ensures that employees can adapt to technological changes.
Attracting Young Talent
To counteract the aging workforce, attracting young talent is imperative.
Enhancing the appeal of manufacturing careers through positive branding and highlighting technological innovation can draw interest.
Offering competitive salaries, career advancement opportunities, and a conducive work environment are key factors in attracting younger generations.
Moreover, internships and apprenticeship programs provide hands-on experience and a pathway into the industry.
Procurement and Supplier Negotiation Techniques
Building Strong Supplier Relationships
Effective procurement is fundamental to the manufacturing industry’s success.
Building strong relationships with suppliers ensures a reliable supply chain and fosters collaboration.
Regular communication, mutual respect, and transparency are crucial components of successful supplier partnerships.
These relationships can lead to better terms, improved quality, and innovative solutions, positively impacting employment stability.
Negotiation Strategies
Successful supplier negotiations require strategic planning and understanding of market conditions.
Employing a win-win approach, where both parties benefit, enhances long-term partnerships.
Negotiators should be well-versed in market trends, pricing strategies, and the specific needs of their organization.
Techniques such as value-based negotiation and leveraging multiple suppliers can provide flexibility and favorable terms.
Best Practices in Procurement
Adopting best practices in procurement ensures efficiency and cost-effectiveness.
Implementing a centralized procurement system can streamline processes and improve oversight.
Utilizing technology, such as procurement software and data analytics, enhances decision-making and forecasting.
Additionally, fostering sustainability in procurement practices aligns with global standards and meets increasing consumer demands for responsible production.
Impact of Market Conditions on Employment
Global Competition
Japanese manufacturers face intense competition from global players, particularly in emerging markets.
To remain competitive, companies must continuously innovate and improve efficiency.
This necessity drives the demand for skilled workers capable of implementing and managing advanced technologies.
Maintaining a competitive edge is essential for sustaining and creating employment opportunities.
Economic Fluctuations
Economic cycles significantly influence manufacturing employment.
During economic downturns, production may be scaled back, leading to temporary job losses.
Conversely, economic growth stimulates demand for manufactured goods, creating employment opportunities.
Diversifying markets and products can mitigate the impact of economic fluctuations on employment.
Trade Policies
Trade policies and international relations play a critical role in the manufacturing sector.
Tariffs, trade agreements, and regulatory standards can affect the cost and accessibility of markets.
Navigating these policies effectively can open new opportunities and protect existing jobs.
Manufacturers must stay informed and adapt to policy changes to sustain employment levels.
Best Practices for Sustaining Employment Growth
Innovation and Continuous Improvement
Emphasizing innovation is key to sustaining employment growth.
Investing in research and development fosters new product development and process improvements.
Continuous improvement methodologies, such as Lean and Six Sigma, enhance efficiency and reduce waste.
These practices not only boost productivity but also create a dynamic work environment that attracts and retains talent.
Employee Engagement and Retention
Engaging employees and fostering a positive workplace culture are essential for retention.
Providing opportunities for career advancement, recognizing achievements, and ensuring work-life balance contribute to job satisfaction.
Implementing feedback mechanisms allows employees to voice their concerns and suggestions, leading to a more inclusive and motivated workforce.
Adopting Flexible Work Models
Flexible work models, including remote work and flexible hours, can enhance employee satisfaction and productivity.
Adapting to these models requires investment in technology and a shift in management practices.
However, the benefits include a broader talent pool, reduced turnover, and increased adaptability to changing market demands.
Government Initiatives and Support
Policy Support
Government policies play a pivotal role in the revitalization of the manufacturing sector.
Policies that support research and development, provide tax incentives, and encourage foreign investment can stimulate growth.
Additionally, initiatives focused on workforce development, such as funding for training programs, are critical for employment stability.
Infrastructure Development
Investing in infrastructure, including transportation, energy, and digital connectivity, supports the manufacturing industry’s needs.
Robust infrastructure enhances supply chain efficiency and reduces operational costs.
Government support in this area is vital for creating a conducive environment for manufacturing growth and, consequently, employment opportunities.
Collaborative Programs
Collaborative programs between the government, industry, and academia can drive innovation and workforce development.
Public-private partnerships facilitate the exchange of knowledge and resources, leading to the development of cutting-edge technologies and skilled labor.
These collaborations are essential for addressing the complex challenges facing the manufacturing sector and ensuring sustainable employment growth.
Challenges and Solutions
Addressing the Skills Gap
One of the primary challenges is the skills gap caused by rapid technological advancements.
To address this, companies must invest in training programs that focus on new technologies and methodologies.
Moreover, fostering collaboration with educational institutions ensures that curricula align with industry needs, preparing the workforce for future demands.
Managing Workforce Diversity
A diverse workforce brings a range of perspectives and ideas, fostering innovation.
However, managing diversity requires intentional strategies to ensure inclusion and equity.
Implementing diversity and inclusion programs, promoting cultural awareness, and addressing unconscious biases are essential for creating a harmonious and productive work environment.
Enhancing Job Security
Ensuring job security is crucial for employee morale and retention.
Companies can enhance job security by diversifying their product lines, exploring new markets, and investing in resilient supply chains.
Additionally, transparent communication regarding company performance and future prospects helps reassure employees and build trust.
Case Studies: Successful Revitalization Efforts
Toyota’s Workforce Transformation
Toyota has successfully revitalized its workforce by integrating advanced manufacturing technologies while maintaining a strong emphasis on employee training.
The company’s commitment to continuous improvement and employee development has resulted in increased productivity and job satisfaction.
Toyota’s approach serves as a model for balancing technological advancement with workforce stability.
Panasonic’s Innovation Strategy
Panasonic has revitalized its manufacturing employment by focusing on innovation and sustainability.
The company’s investment in renewable energy technologies and smart manufacturing has opened new employment opportunities.
Panasonic’s strategy highlights the importance of aligning business goals with broader societal trends to sustain employment growth.
Conclusion
Revitalizing Japan’s manufacturing industry is pivotal for the nation’s economic future.
The sector faces significant challenges, including an aging workforce and increased automation.
However, with strategic investments in training, embracing technological advancements, and fostering strong supplier relationships, Japan can sustain and grow employment in manufacturing.
Government support and industry collaboration are essential in this endeavor.
By adopting best practices and addressing current challenges, Japan’s manufacturing employment landscape can thrive, ensuring continued prosperity and global competitiveness.
資料ダウンロード
QCD調達購買管理クラウド「newji」は、調達購買部門で必要なQCD管理全てを備えた、現場特化型兼クラウド型の今世紀最高の購買管理システムとなります。
ユーザー登録
調達購買業務の効率化だけでなく、システムを導入することで、コスト削減や製品・資材のステータス可視化のほか、属人化していた購買情報の共有化による内部不正防止や統制にも役立ちます。
NEWJI DX
製造業に特化したデジタルトランスフォーメーション(DX)の実現を目指す請負開発型のコンサルティングサービスです。AI、iPaaS、および先端の技術を駆使して、製造プロセスの効率化、業務効率化、チームワーク強化、コスト削減、品質向上を実現します。このサービスは、製造業の課題を深く理解し、それに対する最適なデジタルソリューションを提供することで、企業が持続的な成長とイノベーションを達成できるようサポートします。
オンライン講座
製造業、主に購買・調達部門にお勤めの方々に向けた情報を配信しております。
新任の方やベテランの方、管理職を対象とした幅広いコンテンツをご用意しております。
お問い合わせ
コストダウンが利益に直結する術だと理解していても、なかなか前に進めることができない状況。そんな時は、newjiのコストダウン自動化機能で大きく利益貢献しよう!
(Β版非公開)