- お役立ち記事
- Mechanisms and mitigation measures for winding problems, skew and creases
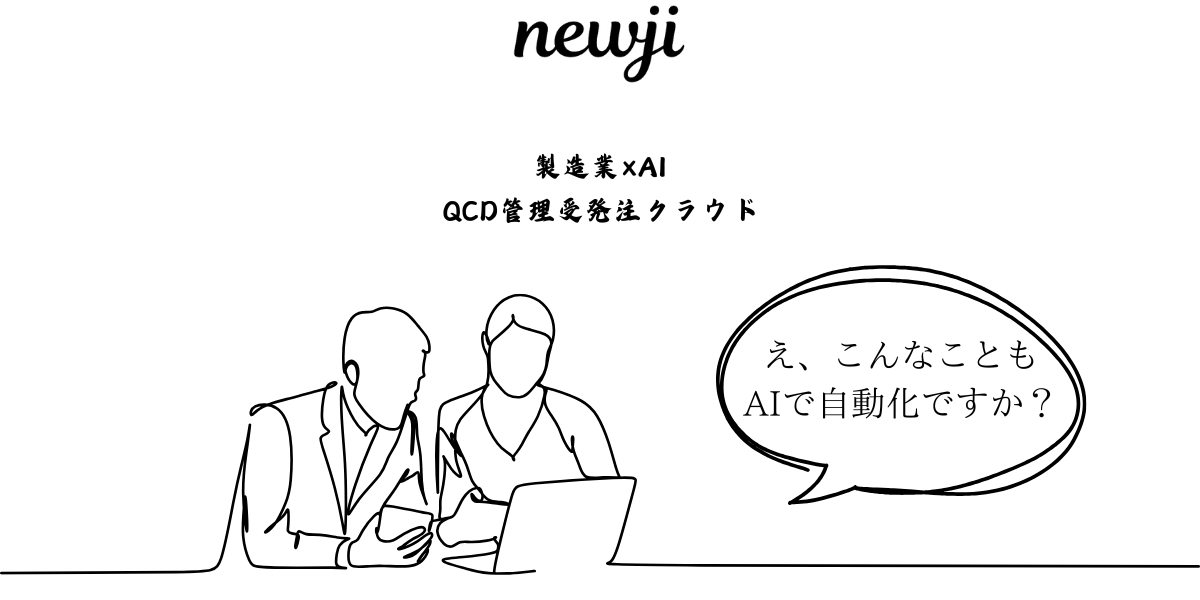
Mechanisms and mitigation measures for winding problems, skew and creases
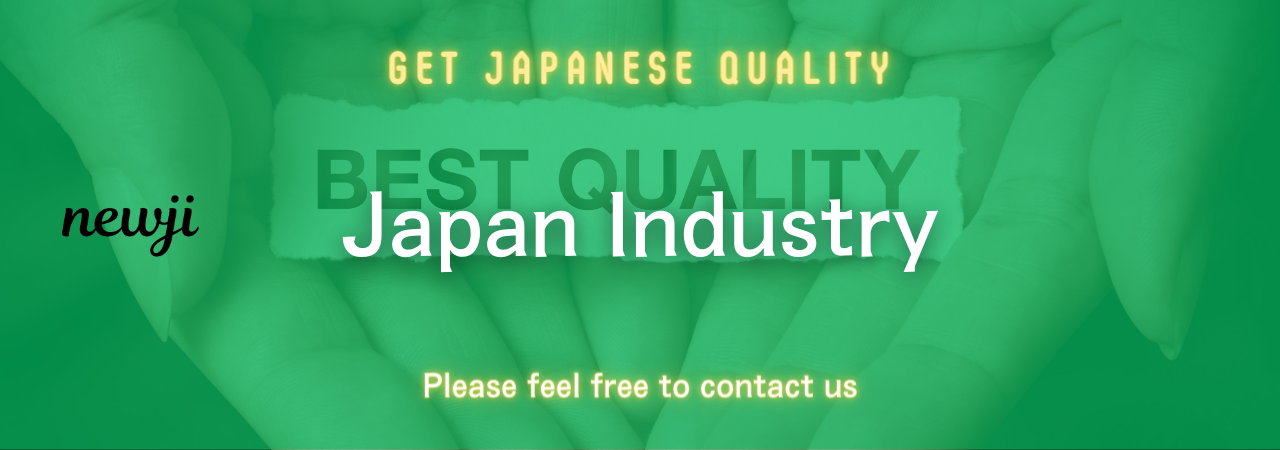
Understanding Winding Problems
Winding is a crucial process in industries where materials are rolled or coiled, such as in textile, paper, and plastic film manufacturing.
However, this process often encounters issues like skew, creases, and other winding problems that can affect the quality and efficiency of production.
Understanding these problems is essential to implementing effective mitigation measures.
Winding problems typically arise due to a variety of factors including equipment malfunction, improper material handling, and environmental conditions.
Skew and creases are among the most common issues that manufacturers face, each bringing its own set of challenges.
What is Skew?
Skew refers to the misalignment of materials as they are wound.
When materials are not aligned correctly during the winding process, it can lead to overlaps or gaps, affecting the uniformity and quality of the final product.
Skew commonly occurs when there’s an imbalance in tension across the width of the material.
This imbalance can be caused by faulty machinery, unequal material thickness, or improper loading of the material into the winding machine.
Causes of Creases
Creases, also known as wrinkles or folds, occur when materials are compressed or misaligned during winding.
These imperfections can weaken the structural integrity of the material and lead to defects in the finished product.
Creases are often the result of excessive tension, insufficient control during the winding or guiding phase, or external factors such as humidity and temperature fluctuations.
Managing these variables is key to preventing creases during the winding process.
Mitigation Measures for Skew and Creases
To mitigate winding problems like skew and creases, manufacturers can implement a variety of strategies.
These strategies often involve regular maintenance of equipment, improvements in process control, and adjustments to environmental conditions.
Equipment Maintenance
Regular maintenance and calibration of winding machinery are vital.
Ensuring that all equipment is functioning correctly can help reduce the likelihood of skew and creases.
This includes inspecting tension control devices, aligners, and rollers to detect and rectify any misalignments or malfunctions.
Routine maintenance not only helps in identifying potential problems early but also extends the lifespan of machinery, lowering long-term costs.
Process Control Improvements
Implementing advanced process control methods can significantly reduce winding problems.
Using automated systems with real-time feedback and sensor technology, manufacturers can maintain optimal tension and alignment throughout the winding process.
Integration of control systems that adjust speeds, tensions, and alignments instantly based on the material’s feedback can prevent skew and creases from forming.
These systems can also store process data for continual analysis and improvement.
Environmental Adjustments
Environmental factors like humidity and temperature can greatly affect the winding process.
Materials often respond to changes in the environment, impacting how they wind and leading to defects like skew and creases.
Control of the winding environment is critical to minimizing these problems.
This control involves maintaining stable temperature and humidity levels in the production area to ensure materials remain consistent in their properties.
Implementing air conditioning or humidity control systems can be an effective solution to environmental variability.
Material Handling and Selection
Proper material handling and selection are equally crucial in preventing winding problems.
Choosing high-quality, consistent materials can reduce the risk of skew and creases.
Moreover, stocking materials appropriately and ensuring they are handled with care throughout the delivery and production process can minimize damage and misalignment.
Investing in staff training to reinforce correct handling techniques further allows for a smoother winding process.
Innovative Technologies
Leveraging innovative technologies can also play a crucial role in preventing winding defects.
Adopting technologies like machine learning and artificial intelligence allows for predictive maintenance and process optimization.
These technologies can predict potential failures before they occur by analyzing patterns and anomalies in the production process, thus reducing downtime and enhancing productivity.
Conclusion
In conclusion, addressing winding problems such as skew and creases is essential to maintaining high-quality production standards.
By understanding the causes of these issues and implementing effective mitigation strategies, manufacturers can ensure a smoother, more efficient winding process.
Prioritizing equipment maintenance, process control improvements, environmental adjustments, diligent material handling, and innovative technology use comprises a comprehensive approach to minimizing winding problems.
Through these efforts, industries that rely on winding can improve product quality, increase efficiency, and reduce costs.
資料ダウンロード
QCD調達購買管理クラウド「newji」は、調達購買部門で必要なQCD管理全てを備えた、現場特化型兼クラウド型の今世紀最高の購買管理システムとなります。
ユーザー登録
調達購買業務の効率化だけでなく、システムを導入することで、コスト削減や製品・資材のステータス可視化のほか、属人化していた購買情報の共有化による内部不正防止や統制にも役立ちます。
NEWJI DX
製造業に特化したデジタルトランスフォーメーション(DX)の実現を目指す請負開発型のコンサルティングサービスです。AI、iPaaS、および先端の技術を駆使して、製造プロセスの効率化、業務効率化、チームワーク強化、コスト削減、品質向上を実現します。このサービスは、製造業の課題を深く理解し、それに対する最適なデジタルソリューションを提供することで、企業が持続的な成長とイノベーションを達成できるようサポートします。
オンライン講座
製造業、主に購買・調達部門にお勤めの方々に向けた情報を配信しております。
新任の方やベテランの方、管理職を対象とした幅広いコンテンツをご用意しております。
お問い合わせ
コストダウンが利益に直結する術だと理解していても、なかなか前に進めることができない状況。そんな時は、newjiのコストダウン自動化機能で大きく利益貢献しよう!
(Β版非公開)