- お役立ち記事
- Fundamentals of plastic injection molding, troubleshooting, and effective use of CAE
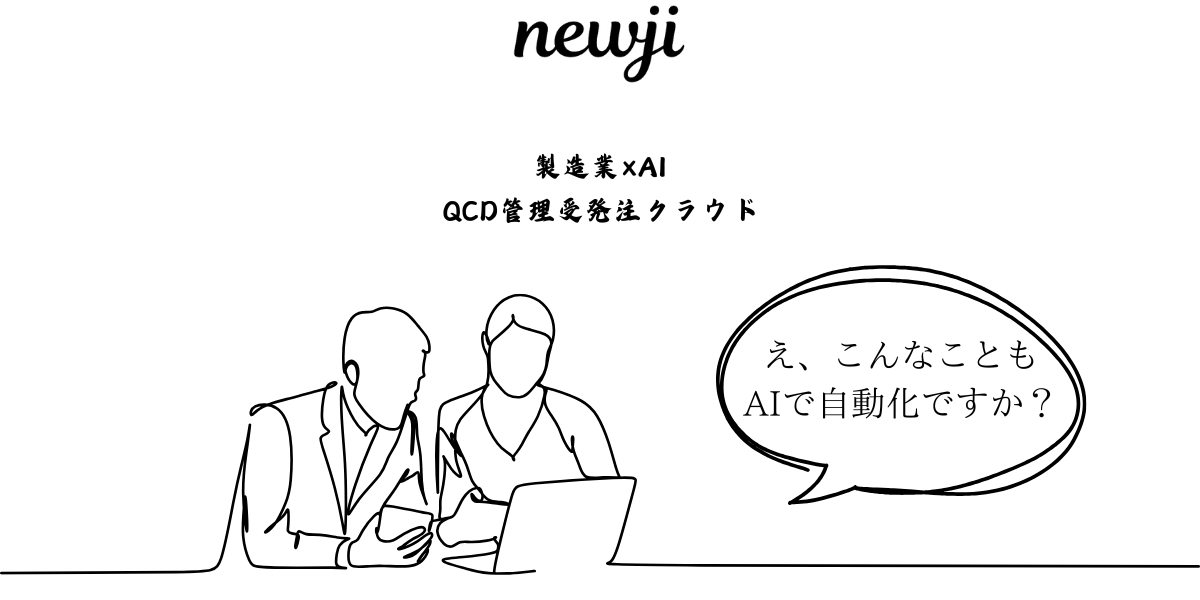
Fundamentals of plastic injection molding, troubleshooting, and effective use of CAE
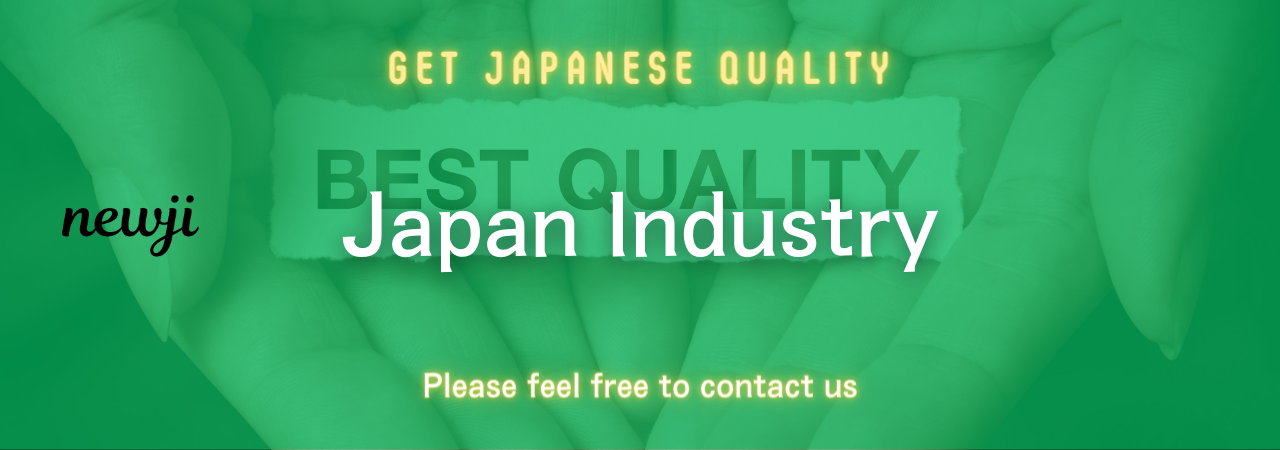
目次
Understanding Plastic Injection Molding
Plastic injection molding is a popular manufacturing process where plastic pellets are melted and injected into a mold to form various products and components.
This process is widely used in industries such as automotive, consumer goods, electronics, and medical devices due to its ability to produce high-quality, consistent parts quickly and cost-effectively.
Understanding the fundamental principles of plastic injection molding is crucial for anyone involved in product design or manufacturing.
The process starts with plastic granules being fed into a heated barrel, where they melt and become a liquid.
This molten plastic is then injected into a highly detailed mold cavity using a screw or plunger.
Once the plastic cools and solidifies, the mold opens, and the finished part is ejected.
Key Components of the Injection Molding Process
The plastic injection molding process consists of several key components and steps, all of which play essential roles in producing a successful product.
The Mold
The mold is the core component of the injection molding process.
It is typically made from robust materials such as steel or aluminum and consists of two halves: the cavity and the core.
The design of the mold determines the final shape and features of the product.
Careful consideration of the mold design is crucial to ensure the quality and precision of the finished part.
The Injection Unit
The injection unit is responsible for heating and injecting the plastic material into the mold.
It comprises a hopper that feeds plastic granules into a heated barrel.
The material is heated until it melts and is then delivered into the mold through a nozzle using either a reciprocating screw or a plunger.
The Clamping Unit
The clamping unit holds the mold halves together during the injection process.
It also opens and closes the mold for part ejection.
A robust clamping unit ensures that the mold remains tightly shut, preventing plastic from leaking out and adversely impacting the quality of the manufactured part.
The Cooling System
The cooling phase is crucial in the injection molding process because it affects the cycle time and quality of the part.
Cooling channels are integrated into the mold to allow for uniform heat dissipation, helping the molten plastic solidify uniformly and minimizing warping or shrinkage.
Troubleshooting Common Injection Molding Problems
Despite its advantages, the injection molding process is susceptible to various issues that can compromise the quality of the final product.
Understanding and addressing these common problems is essential for anyone involved in this field.
Sink Marks
Sink marks occur when the surface of the molded part shows depressions or dimples.
This is often caused by uneven cooling, insufficient packing pressure, or inadequate mold design.
Solutions include optimizing cooling channels, adjusting packing pressure settings, or revisiting the mold design.
Warping
Warping can occur when different sections of a part cool at inconsistent rates, causing the finished product to bend or twist.
Addressing warping can involve modifying the mold design for more uniform thickness or enhancing the cooling and packing settings.
Short Shots
Short shots happen when the mold cavity is not completely filled, leading to incomplete parts.
Possible causes include inadequate injection pressure, incorrect material viscosity, or improper venting of the mold.
To resolve this, manufacturers can increase injection pressure, use a different plastic material, or improve mold venting.
Flash
Flash is the excess plastic that protrudes out of the parting line of the mold.
It often results from excessive injection pressure, poor mold clamping, or defects in the mold itself.
To remedy flash, it’s important to adjust the injection pressure, ensure proper clamping, or refine the mold design.
The Role of Computer-Aided Engineering (CAE) in Injection Molding
Computer-Aided Engineering (CAE) tools have revolutionized the plastic injection molding process, facilitating better design, simulation, and optimization of molds and processes.
Simulation and Analysis
CAE software can simulate the entire injection molding process, allowing engineers to analyze and predict potential issues before they occur.
With features like flow analysis, cooling analysis, and warpage analysis, CAE tools help optimize mold design, material selection, and processing parameters.
Optimizing Design
During the product design phase, CAE tools enable designers to refine designs to ensure manufacturability and performance.
Engineers can use simulations to test various design variations and alterations, ultimately selecting the most efficient and effective design.
Improving Efficiency
By utilizing CAE software, companies can significantly reduce the time and cost associated with developing new injection-molded parts.
Through virtual testing and optimization, the cycle of prototyping and manufacturing is shortened, and productivity is greatly enhanced.
Reducing Waste
CAE tools contribute to minimizing material waste by allowing more precise control over production parameters.
Optimized simulations can identify the ideal material usage and processing conditions, reducing scrap and saving resources.
Conclusion
Plastic injection molding is a highly efficient and versatile manufacturing process that plays a crucial role in modern production.
Understanding its fundamentals, as well as common troubleshooting techniques, ensures the high-quality production of parts.
Furthermore, the innovation of Computer-Aided Engineering continues to advance the capabilities of injection molding, offering precision, efficiency, and environmental sustainability.
By leveraging these tools and strategies, manufacturers can continue to push the boundaries of design and production, ensuring success in the competitive market.
資料ダウンロード
QCD調達購買管理クラウド「newji」は、調達購買部門で必要なQCD管理全てを備えた、現場特化型兼クラウド型の今世紀最高の購買管理システムとなります。
ユーザー登録
調達購買業務の効率化だけでなく、システムを導入することで、コスト削減や製品・資材のステータス可視化のほか、属人化していた購買情報の共有化による内部不正防止や統制にも役立ちます。
NEWJI DX
製造業に特化したデジタルトランスフォーメーション(DX)の実現を目指す請負開発型のコンサルティングサービスです。AI、iPaaS、および先端の技術を駆使して、製造プロセスの効率化、業務効率化、チームワーク強化、コスト削減、品質向上を実現します。このサービスは、製造業の課題を深く理解し、それに対する最適なデジタルソリューションを提供することで、企業が持続的な成長とイノベーションを達成できるようサポートします。
オンライン講座
製造業、主に購買・調達部門にお勤めの方々に向けた情報を配信しております。
新任の方やベテランの方、管理職を対象とした幅広いコンテンツをご用意しております。
お問い合わせ
コストダウンが利益に直結する術だと理解していても、なかなか前に進めることができない状況。そんな時は、newjiのコストダウン自動化機能で大きく利益貢献しよう!
(Β版非公開)