- お役立ち記事
- Fundamentals of die casting, high quality technology, effective defect/trouble countermeasures, and their key points
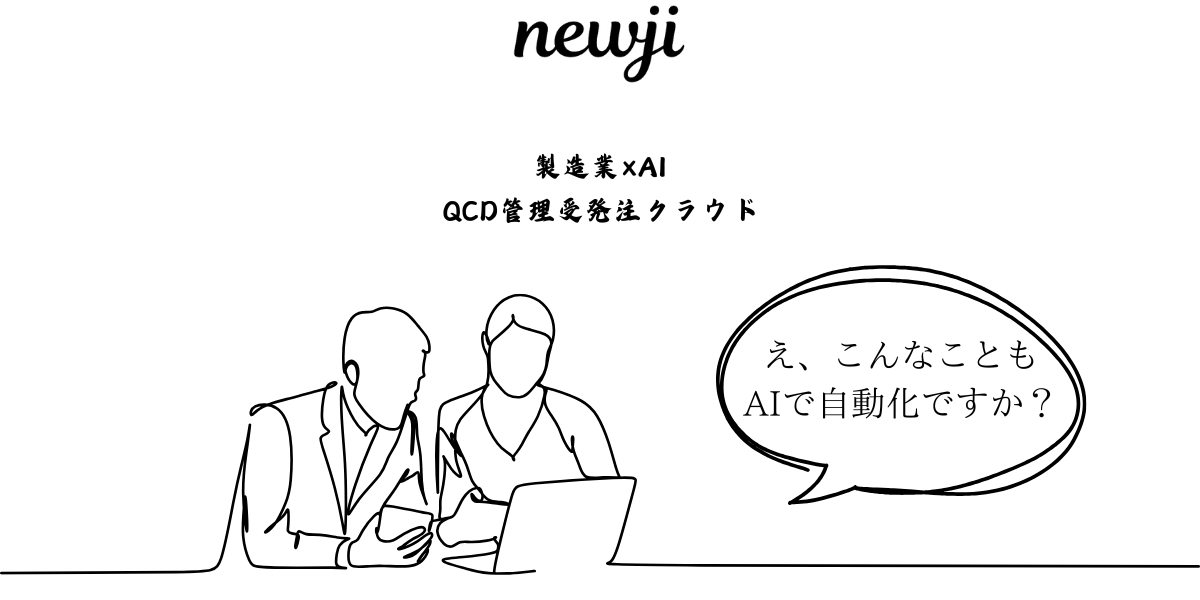
Fundamentals of die casting, high quality technology, effective defect/trouble countermeasures, and their key points
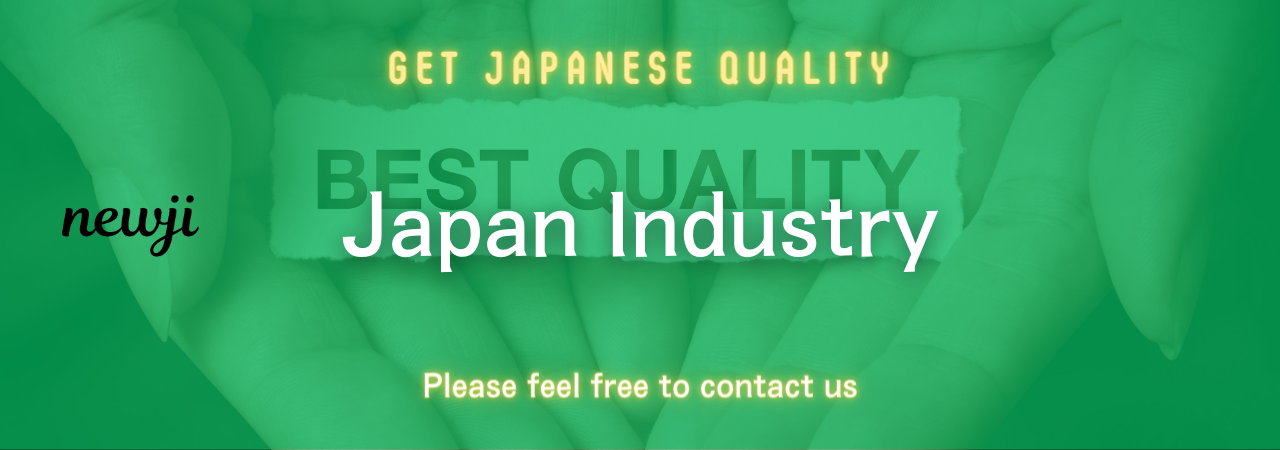
目次
Understanding Die Casting
Die casting is a manufacturing process that involves pushing molten metal into a mold cavity under high pressure.
This method is used to produce metal parts with stunning dimensional accuracy and smooth surface finishes.
It is a preferred technique in industries like automotive, aerospace, and electronics due to its ability to produce complex shapes with tight tolerances.
During the process, two halves of a steel mold, known as a die, are clamped together, and molten metal is injected into the cavity.
Once the metal cools and solidifies, the die is opened, and the finished part is ejected.
High-Quality Die Casting Technology
To achieve high-quality results in die casting, several factors must be meticulously controlled.
The technology has evolved to improve efficiency, quality, and precision.
Material Selection
Choosing the right material is crucial for die casting.
Common alloys include aluminum, zinc, magnesium, and copper.
Aluminum is popular due to its lightweight, corrosion resistance, and excellent mechanical properties.
Zinc offers enhanced fluidity, making it ideal for intricate designs.
Advanced Mold Design
Mold design is a critical factor influencing the quality of the die-cast part.
Designing the mold requires understanding the behavior of the molten metal and accounting for thermal expansion.
Advanced techniques like computer-aided design (CAD) software are used to create precise die designs.
Proper cooling channels and venting systems are incorporated to ensure consistent quality.
Precision in Temperature Control
Maintaining the right temperature throughout the process is vital.
The molten metal, die, and casting equipment temperatures are carefully monitored and controlled.
This helps prevent defects such as soldering or misruns.
Automation and Robotics
Automation in die casting has vastly improved the quality and efficiency of production.
Robotic systems are used to handle repetitive tasks, ensuring consistency and reducing human error.
They also help in post-casting operations such as trimming and finishing.
Effective Defect and Trouble Countermeasures
Despite its advantages, die casting is not without challenges.
Various defects can occur, but with effective countermeasures, these issues can be minimized.
Addressing Porosity
Porosity is a common defect caused by trapped air bubbles or shrinkage cavities.
To counteract this, vacuum die casting is employed to reduce air entrapment.
Optimizing the die design and maintaining proper metal pressure further reduces porosity risks.
Preventing Cold Shuts
Cold shuts occur when two streams of molten metal do not fuse properly, leaving a visible line or surface depression.
Ensuring adequate mold filling speed and correct temperature can help prevent this defect.
Eliminating Flash
Flash refers to excess material that seeps out of the die cavity.
It can be minimized by keeping the die-matching surfaces tight and maintaining proper clamping forces.
Controlling Cracks
Cracks can form if the component cools unevenly or experiences thermal stresses.
Using a uniform cooling rate and thermal simulations helps in predicting and reducing crack formation.
Key Points to Consider
To achieve the best results in die casting, several key points should be considered:
Optimize Process Parameters
Regular monitoring and optimization of process parameters such as injection speed, pressure, and cooling rate are essential.
Advanced sensors and control systems can aid in real-time adjustments.
Regular Maintenance
Routine maintenance of die machines and equipment ensures consistent quality.
Cleaning, inspection, and regular servicing prevent unexpected breakdowns and extend the lifespan of the machinery.
Employee Training
Training personnel in the latest techniques and safety measures enhances the overall quality of die casting operations.
Skilled operators can identify and rectify potential issues swiftly.
Quality Assurance
Implementing a robust quality assurance program helps in maintaining high standards.
Regular inspection and testing of die-cast parts ensure compliance with required specifications.
Conclusion
Die casting is a versatile and efficient manufacturing process that delivers high-quality metal parts.
By understanding its fundamentals and implementing advanced techniques, industries can achieve superior results.
Addressing common defects and focusing on key optimization strategies are crucial steps towards enhancing die casting processes.
With continuous advancements in technology, die casting will continue to play a vital role in various manufacturing sectors.
資料ダウンロード
QCD調達購買管理クラウド「newji」は、調達購買部門で必要なQCD管理全てを備えた、現場特化型兼クラウド型の今世紀最高の購買管理システムとなります。
ユーザー登録
調達購買業務の効率化だけでなく、システムを導入することで、コスト削減や製品・資材のステータス可視化のほか、属人化していた購買情報の共有化による内部不正防止や統制にも役立ちます。
NEWJI DX
製造業に特化したデジタルトランスフォーメーション(DX)の実現を目指す請負開発型のコンサルティングサービスです。AI、iPaaS、および先端の技術を駆使して、製造プロセスの効率化、業務効率化、チームワーク強化、コスト削減、品質向上を実現します。このサービスは、製造業の課題を深く理解し、それに対する最適なデジタルソリューションを提供することで、企業が持続的な成長とイノベーションを達成できるようサポートします。
オンライン講座
製造業、主に購買・調達部門にお勤めの方々に向けた情報を配信しております。
新任の方やベテランの方、管理職を対象とした幅広いコンテンツをご用意しております。
お問い合わせ
コストダウンが利益に直結する術だと理解していても、なかなか前に進めることができない状況。そんな時は、newjiのコストダウン自動化機能で大きく利益貢献しよう!
(Β版非公開)