- お役立ち記事
- Basic theory of rotating machine vibration, vibration reduction method using Excel, and its practice
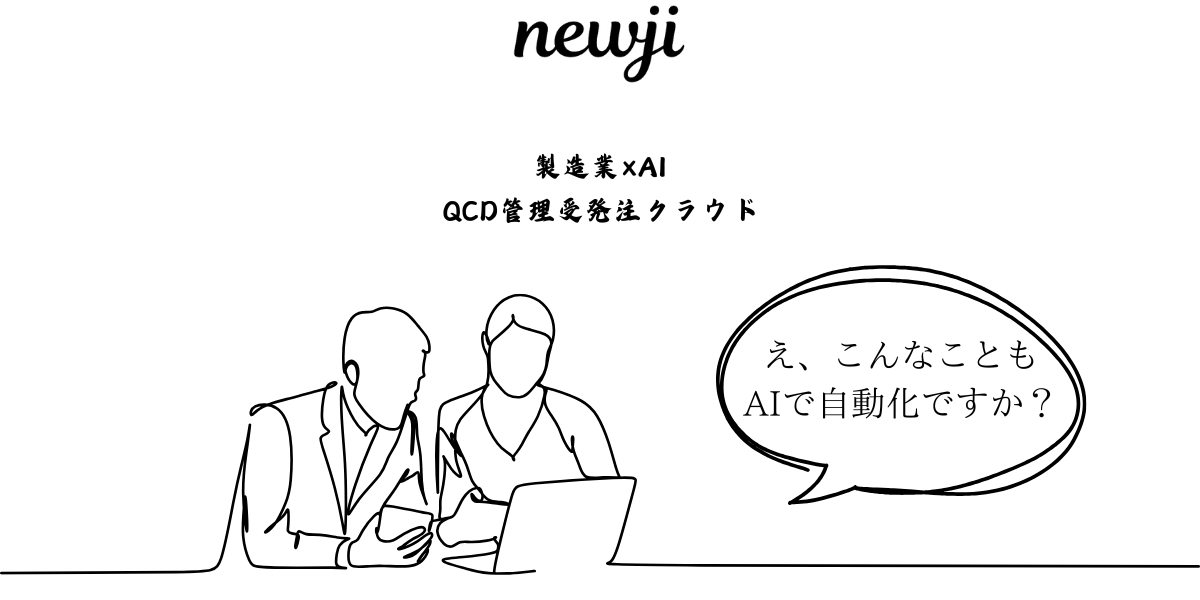
Basic theory of rotating machine vibration, vibration reduction method using Excel, and its practice
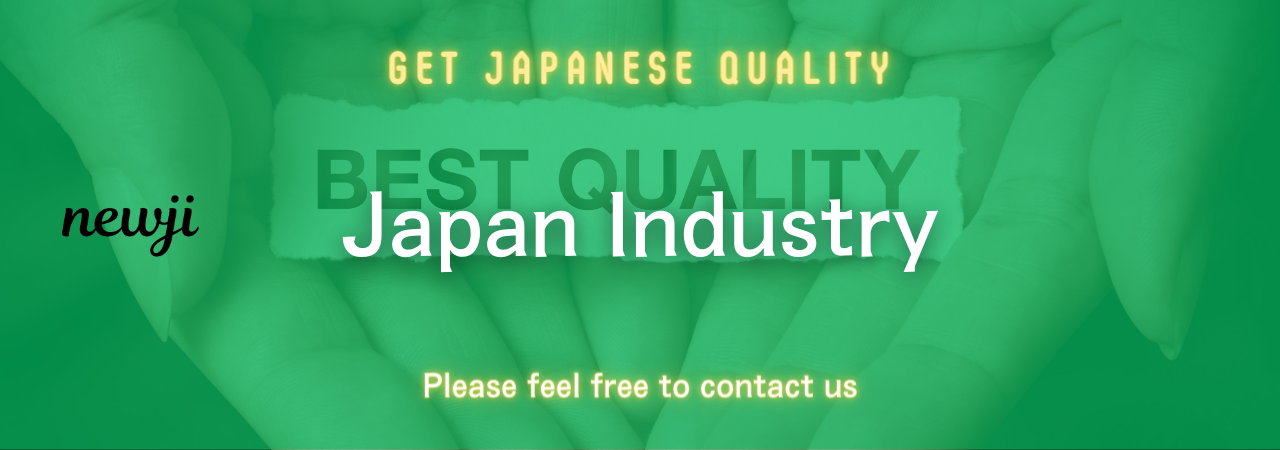
目次
Understanding the Basics of Rotating Machine Vibration
Rotating machines are prevalent in various industries, playing an integral role in processes that involve manufacturing, power generation, and more.
However, these machines often have to cope with a significant challenge – vibration.
Understanding the basics of rotating machine vibration is essential for anyone looking to maintain and optimize these crucial pieces of equipment.
Rotating machine vibration refers to the oscillatory motions that occur as the machine components turn.
These vibrations can arise from several sources, such as imbalance, misalignment, wear and tear, or resonance.
Imbalance is one of the most common causes, occurring when the center of mass of the rotating part does not match the axis of rotation, leading to periodic forces that cause vibrations during operation.
Vibration can have various effects on rotating machinery.
In the short term, it can lead to increased noise and energy consumption.
In the long run, excessive vibration can result in more severe issues like component fatigue, decreased operational efficiency, and even total machine failure.
Thus, understanding and managing vibration is critical to ensuring the longevity and effective performance of rotating machines.
Approaches to Reducing Vibration in Rotating Machines
Reducing vibration in rotating machines is a critical aspect of maintenance and operational efficiency.
There are several methods used to achieve this, including balancing, alignment, and damping.
1. Balancing
Balancing is the process of adjusting the mass distribution of a rotating machine so that its center of mass coincides with its rotational axis.
This eliminates the periodic forces that cause vibration.
Balancing can be performed using static or dynamic techniques, depending on the complexity of the machine’s operation.
Static balancing is suitable for simpler, slower rotating parts, while dynamic balancing is typically used for high-speed applications and involves sophisticated analysis of the forces at play.
2. Alignment
Alignment ensures that the rotating components of a machine are set in precise relative positions.
Misalignment can cause increased wear and vibration as coupled parts move against each other in ways they should not.
Proper alignment involves meticulous adjustments to the setup of a machine, often monitored with laser alignment tools to achieve precise measurements and corrections.
3. Damping
Damping is the process of dissipating the energy of vibrations, thereby reducing their amplitude.
Damping materials or devices absorb vibrational energy, converting it into a form less harmful to the machine, like heat.
Using dampers or specific materials like rubber bushings in strategic parts of the machine can minimize vibrations significantly.
Using Excel for Vibration Analysis and Reduction
Excel is a powerful tool that can be employed to analyze and reduce vibrations in rotating machines by offering a straightforward platform for data collection, analysis, and visualization.
Excel spreadsheets can help ease the process of monitoring vibration data, identifying patterns, and implementing vibration control strategies.
1. Data Collection
Collecting data is the first step in understanding the nature and extent of vibrations in a system.
Excel can be used to create customized forms and tables to log vibration data systematically.
This includes recording parameters such as frequency, amplitude, and phase of vibrations, as well as machine load and operational conditions.
2. Data Analysis
Once data is collected, Excel’s analytical capabilities come into play.
Users can create formulas and functions to calculate key metrics such as vibration velocity, acceleration, and displacement.
Pivotal analyses such as Fast Fourier Transforms (FFT) can be conducted to convert time-domain vibration data into frequency domain insights.
Such analyses can point to specific issues like imbalance, misalignment, or component degradation based on identified vibration frequencies.
3. Visualization
Excel’s powerful charting features enable users to visualize the data in various forms like line graphs or scatter plots.
Simulation and trend charting can predict future vibration behavior and help in proactive machine maintenance.
Graphical representations make it easier to spot patterns and correlations that might not be immediately apparent with raw data alone.
Practical Application of Vibration Analysis with Excel
In practice, the application of vibration analysis using Excel requires careful execution.
Here is a simple step-by-step guide to put theory into practice:
1. **Set up a Data Template:**
Create a standardized Excel spreadsheet template for logging vibration data.
Include fields for machinery details, monitoring date, measurement location, and the specific vibration parameters being recorded.
2. **Input Historical Data:**
If available, input historical vibration data to understand baseline machinery behavior.
This will help in identifying any deviations over time reflecting issues.
3. **Perform Analysis:**
Use Excel functions to perform key analysis on vibration data for insights about possible underlying problems.
Develop formulas to automate calculations for metrics like vibration amplitude and frequency.
4. **Visualize Results:**
Employ Excel charts to convert analyzed data into visual forms.
Use different types of graphs to compare current data against historical trends.
5. **Identify & Implement Solutions:**
Based on insights from the analysis, identify necessary maintenance actions.
If persistent vibration issues are detected, schedule more sophisticated diagnostics or immediate corrective interventions based on severity.
Conclusion
Rotating machine vibration is a complex yet manageable phenomenon when approached with the right tools and techniques.
Understanding the basics and exploring methods of vibration reduction through practical applications like Excel modeling can enhance maintenance practices and preserve equipment integrity.
By implementing strategies to monitor, analyze, and address machine vibrations, operators can not only extend the lifespan of machinery but also optimize its performance and reliability.
資料ダウンロード
QCD調達購買管理クラウド「newji」は、調達購買部門で必要なQCD管理全てを備えた、現場特化型兼クラウド型の今世紀最高の購買管理システムとなります。
ユーザー登録
調達購買業務の効率化だけでなく、システムを導入することで、コスト削減や製品・資材のステータス可視化のほか、属人化していた購買情報の共有化による内部不正防止や統制にも役立ちます。
NEWJI DX
製造業に特化したデジタルトランスフォーメーション(DX)の実現を目指す請負開発型のコンサルティングサービスです。AI、iPaaS、および先端の技術を駆使して、製造プロセスの効率化、業務効率化、チームワーク強化、コスト削減、品質向上を実現します。このサービスは、製造業の課題を深く理解し、それに対する最適なデジタルソリューションを提供することで、企業が持続的な成長とイノベーションを達成できるようサポートします。
オンライン講座
製造業、主に購買・調達部門にお勤めの方々に向けた情報を配信しております。
新任の方やベテランの方、管理職を対象とした幅広いコンテンツをご用意しております。
お問い合わせ
コストダウンが利益に直結する術だと理解していても、なかなか前に進めることができない状況。そんな時は、newjiのコストダウン自動化機能で大きく利益貢献しよう!
(Β版非公開)