- お役立ち記事
- FMEAとDRBFMの本質的な違い
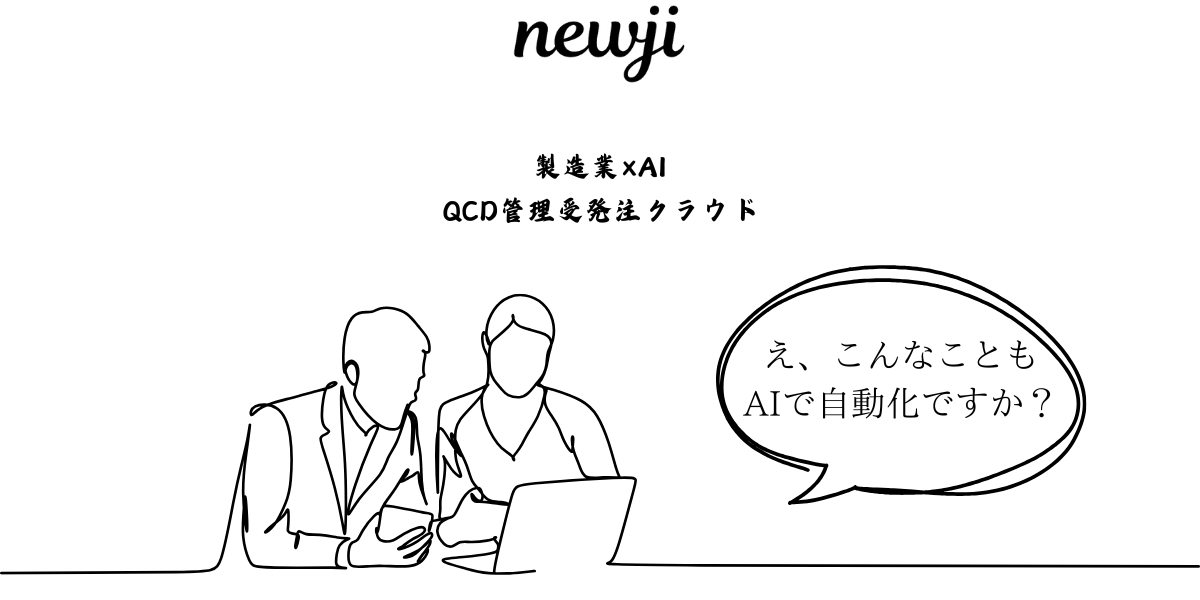
FMEAとDRBFMの本質的な違い
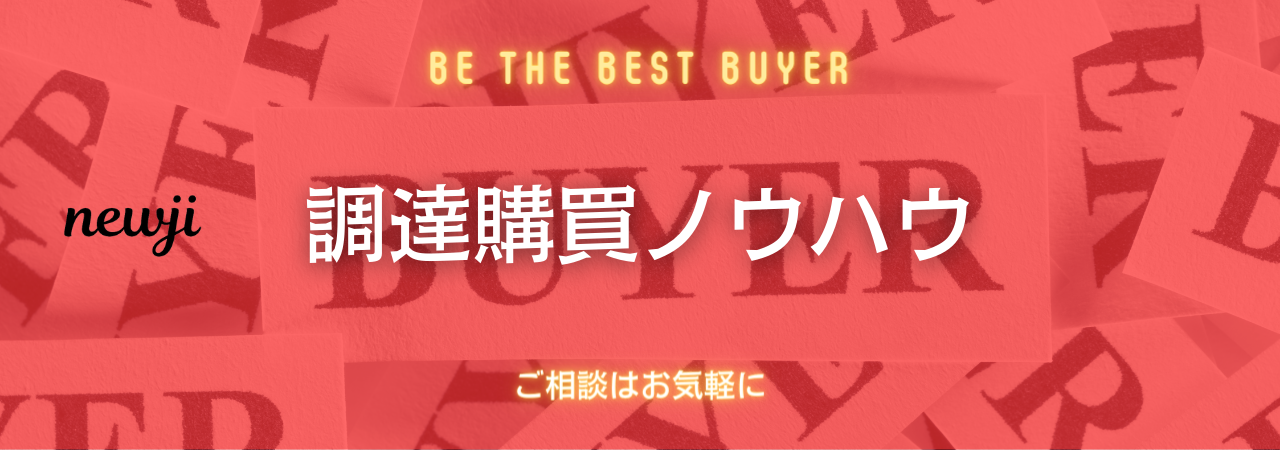
目次
はじめに
製造業界では、リスクアセスメントと品質保証のためにさまざまな手法が用いられています。
その中でも特に重要なのがFMEA(Failure Modes and Effects Analysis: 障害モード影響解析)とDRBFM(Design Review Based on Failure Modes: 障害モードに基づく設計レビュー)です。
これらの手法は、製品開発プロセスの中で潜在的な問題を特定し、製品の信頼性と品質を向上させるために不可欠です。
本記事では、FMEAとDRBFMの本質的な違いについて深く掘り下げ、製造業に携わる方々がどのようにこれらの手法を適用すべきかについて解説していきます。
FMEAの概要
FMEAの目的と適用範囲
FMEAは、製品やプロセスの設計段階から使用される手法で、潜在的な故障モードとその影響を評価し、リスクを最小化する方法を検討します。
特に航空宇宙、自動車、医療機器など、高い安全性が要求される業界でよく使用されています。
FMEAは、製品やプロセスに潜む問題を未然に回避し、製品の設計や製造プロセスの品質を向上させることを目的としています。
FMEAの実施プロセス
FMEAの実施は通常、以下のステップに分かれます。
1. システムやプロセスの範囲を決定し、分析を行う対象を明確にする。
2. 異なる故障モードを特定し、それによる影響を評価する。
3. 各故障モードの発生確率、検出可能性、影響の重大性を評価し、リスク優先数(RPN)を計算する。
4. リスクの高い項目に対する対策を検討し、実施する。
5. 実施した対策の効果を評価し、FMEAを更新する。
FMEAの利点と限界
FMEAは、潜在的な問題を予測し、未然に対応策を立てることで、製品やプロセスの品質を向上させるために有効です。
また、リスクを数値化することで、優先すべき問題を明確にすることができます。
しかし、FMEAの限界として、チームメンバーの経験や知識に依存する点や、膨大なデータの管理が必要になることが挙げられます。
DRBFMの概要
DRBFMの目的と適用範囲
DRBFMは、主に設計の変更に伴うリスクを管理するために用いられる手法です。
「変更を伴うデザインレビュー」に焦点を当て、設計変更が製品に及ぼす潜在的な影響を徹底的に分析します。
特に自動車業界で活用されており、デザイン変更を行った際の問題発生を未然に防ぐための手法とされています。
DRBFMの実施プロセス
DRBFMは、次のようなステップで実施されます。
1. 変更内容を明確にし、変更による影響を受けそうな要素を特定する。
2. 既存の設計や過去のデータを基に、新たに発生しうる故障モードを洗い出す。
3. 各故障モードの影響を評価し、リスクを分析する。
4. 詳細な設計レビューを行い、改善策を検討し実施する。
5. 実施後のフォローアップを行い、再発防止策を確立する。
DRBFMの利点と限界
DRBFMは、設計変更による潜在的なリスクを事前に評価し、問題を未然に防ぐ点で非常に有効です。
特に、チーム間のコミュニケーションを促進し、設計変更に伴う影響を全員で共有することができます。
しかし、FMEA同様、プロセスが複雑になりがちな点と、経緯の詳細な記録が必要になり、コストと労力がかかる場合があります。
FMEAとDRBFMの本質的な違い
対象とする範囲
FMEAは製品やプロセスの設計全体に焦点を当て、広範囲にわたるリスク評価を行います。
一方、DRBFMは主に設計の変更部分に特化してアプローチし、変更がもたらす影響を集中的に検討します。
リスクアセスメントのアプローチ
FMEAは定量的なリスク評価を行い、リスク優先数(RPN)を使用して優先すべき課題を特定します。
これに対し、DRBFMは質的な分析を重視し、チームディスカッションを通じて問題の潜在的な影響を深く探る手法です。
プロセスの目的
FMEAは一般的な製品やプロセスのリスク管理を目的としており、製品全体の安全性と信頼性を確保するために使用されます。
一方、DRBFMは設計変更時のリスク最小化に特化しており、変更による新たなリスクを回避することを主な目的としています。
製造業におけるFMEAとDRBFMの活用法
製造業がFMEAとDRBFMを効果的に活用することで、製品の品質を向上させると同時に、リスクマネジメントを強化することが可能です。
チーム体制の整備
製品開発プロセスにおいて、両手法を適用するためには、各プロジェクトの目的に応じたチームの編成が不可欠です。
各チームメンバーが手法の目的や適用法を理解し、適切に活用できるようにするためのトレーニングが求められます。
情報共有の促進
FMEAとDRBFMを効果的に運用するためには、プロジェクト全体での情報共有が鍵となります。
特に、設計変更時には、変更内容やリスクに関する情報を迅速かつ正確に共有し、問題発生を未然に防ぐことが重要です。
連携したリスクマネジメント戦略
企業は、FMEAとDRBFMを互いに補完し合う戦略として位置付けることができ、製品ライフサイクル全体でのリスク管理を強化します。
FMEAで全体的なリスクを評価し、基本設計の段階での予防策を講じ、DRBFMで細かな設計変更に対応することで、製品の信頼性をさらに高めることができます。
まとめ
FMEAとDRBFMは、製造業においてリスク管理と品質保証のために欠かせない手法です。
それぞれの手法には異なる特性と目的がありますが、共に製品の安全性と信頼性を向上させるための重要な役割を果たします。
製造業に従事する方々は、これらの手法を効果的に活用することで、変化する市場のニーズや技術革新に対応し、持続可能な成長を実現することができます。
資料ダウンロード
QCD調達購買管理クラウド「newji」は、調達購買部門で必要なQCD管理全てを備えた、現場特化型兼クラウド型の今世紀最高の購買管理システムとなります。
ユーザー登録
調達購買業務の効率化だけでなく、システムを導入することで、コスト削減や製品・資材のステータス可視化のほか、属人化していた購買情報の共有化による内部不正防止や統制にも役立ちます。
NEWJI DX
製造業に特化したデジタルトランスフォーメーション(DX)の実現を目指す請負開発型のコンサルティングサービスです。AI、iPaaS、および先端の技術を駆使して、製造プロセスの効率化、業務効率化、チームワーク強化、コスト削減、品質向上を実現します。このサービスは、製造業の課題を深く理解し、それに対する最適なデジタルソリューションを提供することで、企業が持続的な成長とイノベーションを達成できるようサポートします。
オンライン講座
製造業、主に購買・調達部門にお勤めの方々に向けた情報を配信しております。
新任の方やベテランの方、管理職を対象とした幅広いコンテンツをご用意しております。
お問い合わせ
コストダウンが利益に直結する術だと理解していても、なかなか前に進めることができない状況。そんな時は、newjiのコストダウン自動化機能で大きく利益貢献しよう!
(Β版非公開)