- お役立ち記事
- FMEAの効果的な進め方と品質トラブル未然防止の実践
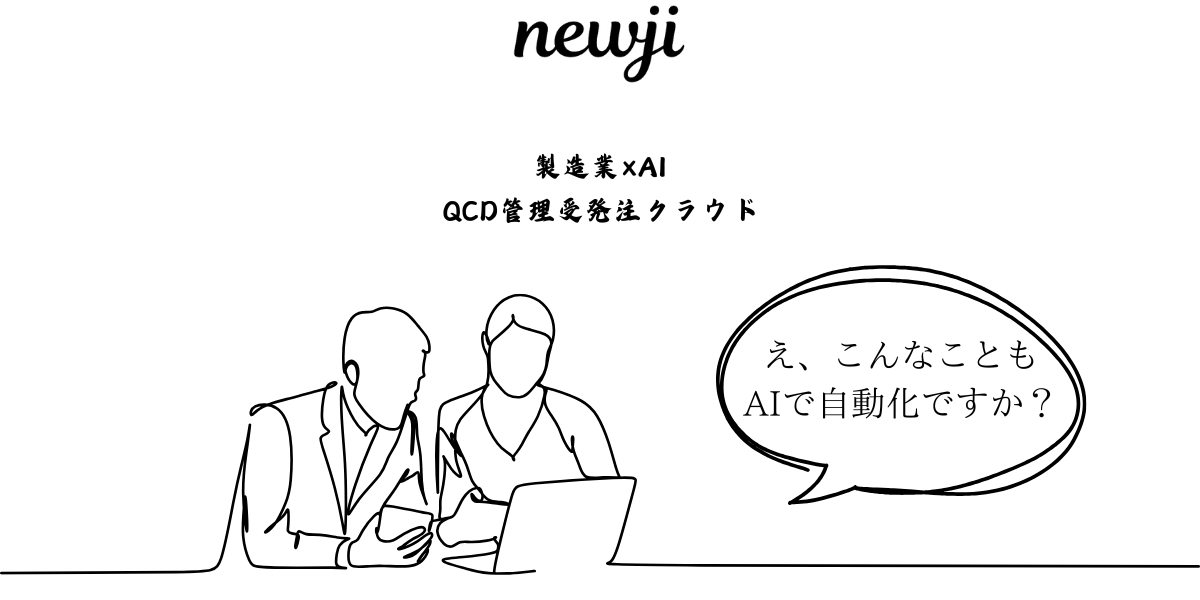
FMEAの効果的な進め方と品質トラブル未然防止の実践
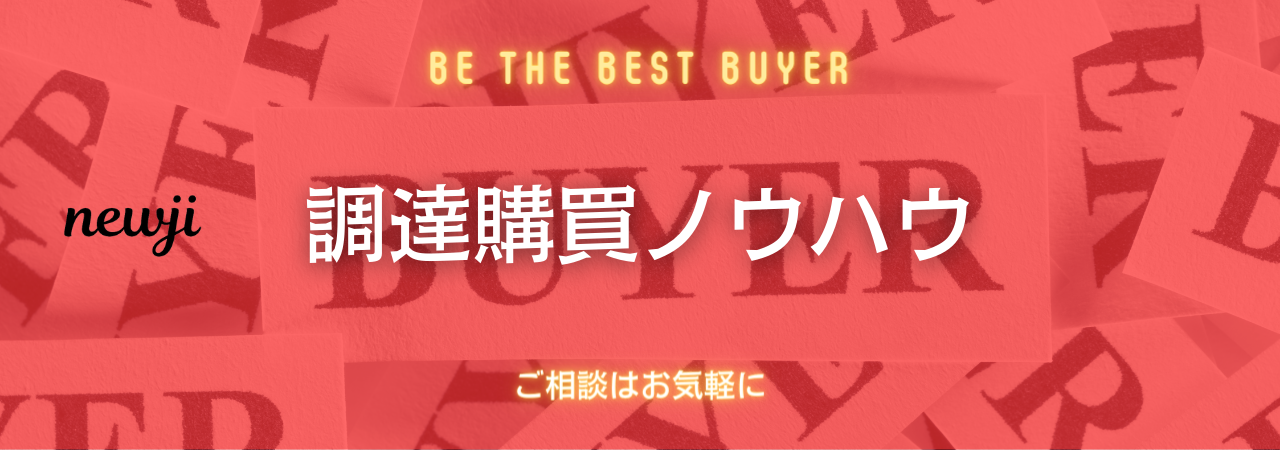
目次
はじめに
品質管理のプロセスにおいて重要な役割を果たすFMEA(Failure Mode and Effects Analysis、故障モード影響解析)は、製品やプロセスの潜在的な弱点を事前に特定し、それに対する対策を講じるための手法です。
適切に進めることで、トラブルの未然防止や品質の向上に大きな効果をもたらします。
本記事では、FMEAを効果的に進めるためのポイントと、品質トラブルを未然に防ぐための実践的な方法について解説します。
FMEAの基本とその重要性
FMEAは、製品やプロセスの各段階で発生しうる故障モードを洗い出し、その影響を評価し、優先順位をつけて対応策を考える手法です。
その目的は、設計段階での潜在的な問題を特定し、顧客に悪影響を及ばす前に対策を講じることです。
これにより製品やプロセスの信頼性を高めることが可能です。特に競争が激しい製造業界では、品質の向上は他社との差別化を図る上で非常に重要です。
FMEAの種類
FMEAには主に2つの種類があります。
1つ目は、DFMEA(Design FMEA)で、製品設計の初期段階において潜在的な故障モードを分析します。
2つ目は、PFMEA(Process FMEA)で、製造プロセスにおける潜在的なリスクを評価し、改善策を講じるものです。
両方共に、製品ライフサイクル全体を通じて品質を確保するために重視されています。
FMEAを効果的に進めるためのステップ
FMEAを効果的に進めるためには、いくつかのステップを踏む必要があります。
以下にそのステップを示します。
ステップ1: チームの編成
FMEAは一人で行うものではなく、関連する領域の専門家を含むチームで行うべきです。
設計、製造、品質保証など異なる視点を持つメンバーを含むことが重要です。
これにより、潜在的な故障モードを多角的に捉えることができます。
ステップ2: 製品・プロセスの理解
次に、製品やプロセスの詳細を理解する必要があります。
図面やフローチャート、仕様書などを用いて、どの部分が重要でどのような機能を持つのかを明確にします。
これにより、故障モードの特定がしやすくなります。
ステップ3: 故障モードの特定
ここでは、製品及びプロセスの各ステージで発生しうる故障モードを徹底的に洗い出します。
過去の失敗事例や取り扱いのマニュアル、標準化データなどを活用すると良いでしょう。
チームでブレインストーミングを行い、漏れのないようにします。
ステップ4: 故障モードの影響評価
特定された故障モードが実際に起こった場合の影響を評価します。
顧客への影響や安全性、法令遵守の観点から評価し、リスク優先度(RPN: Risk Priority Number)を算出します。
リスクの高いものから順に対応策を講じていくための指標となります。
ステップ5: 対策の検討と実施
優先度の高い故障モードから順に、具体的な対策を講じていきます。
設計変更、製造プロセスの見直し、品質管理の強化など、幅広い対策が考えられます。
また、対策の効果を確認するための試験や監査を計画することも重要です。
FMEA実施における成功事例と課題
成功事例: トヨタ生産方式におけるFMEAの活用
トヨタ自動車では、FMEAを製品設計や生産工程の初期段階で徹底して実施しています。
これにより、新車開発の初期段階から潜在的な問題を洗い出し、設計変更を行うことでトラブルを未然に防いでいます。
その結果として、高い品質を維持しつつ、製品ライフサイクル全体のコスト削減も実現しています。
課題: 業務フローとの調整
FMEAを実施する際の一つの課題は、業務フローとの調整です。
特に製品の投入時期がタイトな場合、FMEAに費やす時間が確保できないことが多々あります。
これを解消するためには、FMEAプロセスを標準業務の一部として組み込むことが有効です。
定期的なレビューや、組織全体での理解促進が求められます。
品質トラブル未然防止のための実践的アプローチ
トラブルの原因分析とフィードバックのループ化
品質トラブルを未然に防ぐために、過去のトラブルの原因を徹底的に分析し、その知見をフィードバックループとして活用することが重要です。
トラブルが発生した場合、その原因を詳細に調査し、設計やプロセスに反映させます。
これにより、同様のトラブルが再発するリスクを低減できます。
継続的な社員教育と意識向上
品質トラブルの未然防止のためには、社員の意識を高めることが不可欠です。
定期的な教育プログラムやトレーニングを行い、最新の技術や知識を習得させます。
また、品質に対する高い意識を持つことを組織全体で共有し、日常業務においても積極的に問題提起や改善提案ができる環境を構築します。
まとめ
FMEAは、製品やプロセスに潜在する問題を早期に特定し、品質トラブルを未然に防ぐための強力なツールです。
効果的に進めるためには、チームを編成し、詳細な分析を進め、実践的な対策を講じることが重要です。
また、継続的なフィードバックと社員教育を通じて、品質向上への取り組みを組織全体で進めることが求められます。
これにより、製造業における競争力を高め、持続的な成長を実現することができるでしょう。
資料ダウンロード
QCD調達購買管理クラウド「newji」は、調達購買部門で必要なQCD管理全てを備えた、現場特化型兼クラウド型の今世紀最高の購買管理システムとなります。
ユーザー登録
調達購買業務の効率化だけでなく、システムを導入することで、コスト削減や製品・資材のステータス可視化のほか、属人化していた購買情報の共有化による内部不正防止や統制にも役立ちます。
NEWJI DX
製造業に特化したデジタルトランスフォーメーション(DX)の実現を目指す請負開発型のコンサルティングサービスです。AI、iPaaS、および先端の技術を駆使して、製造プロセスの効率化、業務効率化、チームワーク強化、コスト削減、品質向上を実現します。このサービスは、製造業の課題を深く理解し、それに対する最適なデジタルソリューションを提供することで、企業が持続的な成長とイノベーションを達成できるようサポートします。
オンライン講座
製造業、主に購買・調達部門にお勤めの方々に向けた情報を配信しております。
新任の方やベテランの方、管理職を対象とした幅広いコンテンツをご用意しております。
お問い合わせ
コストダウンが利益に直結する術だと理解していても、なかなか前に進めることができない状況。そんな時は、newjiのコストダウン自動化機能で大きく利益貢献しよう!
(Β版非公開)