- お役立ち記事
- Elastoplastic fracture simulation
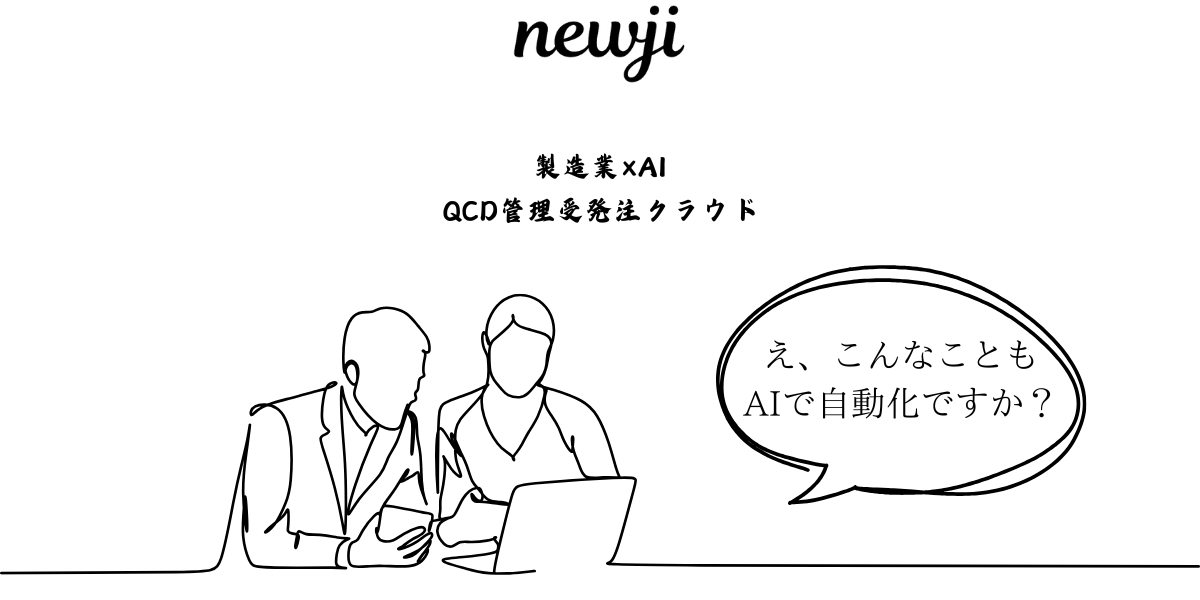
Elastoplastic fracture simulation
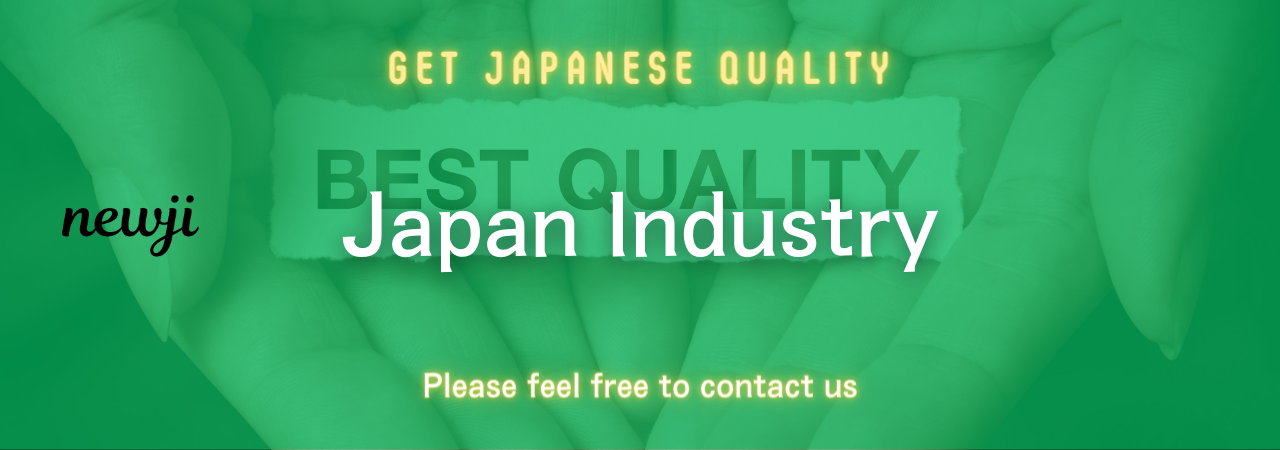
Understanding Elastoplastic Fracture Simulation
Elastoplastic fracture simulation is a sophisticated process used to predict how materials will behave under stress, particularly when those materials undergo both elastic and plastic deformation before fracturing.
This simulation is crucial in various industries such as aerospace, construction, and automotive, where material failure can lead to catastrophic consequences.
For a better understanding, it’s essential to explore the concepts of elasticity, plasticity, and how simulation plays a role in fracture analysis.
Elasticity and Plasticity: Key Concepts
In materials science, elasticity refers to a material’s ability to return to its original shape after the stress causing the deformation is removed.
Think of a rubber band stretching and bouncing back once you let go.
Materials with elastic properties can endure some deformation and still return to their original form.
Plasticity, on the other hand, describes the tendency of a material to undergo permanent deformation under stress.
When a material reaches the plastic stage, it doesn’t return to its original shape even after the stress is removed.
A good example is a piece of metal wire that stays bent when you shape it into a loop.
Elastoplastic Behavior
Many materials exhibit both elastic and plastic behavior when subjected to stress.
Initially, they respond elastically, meaning they can return to their original shape.
However, with increased stress, they reach a yield point where plastic deformation begins.
Beyond this, the material will not fully recover its shape, demonstrating elastoplastic behavior.
Understanding this duality is crucial for materials engineering because it influences how materials perform under different conditions.
For engineers, knowing the limits of elastic behavior and the onset of plastic deformation helps in designing safer and more efficient structures.
Fracture Mechanics
Fracture mechanics is the field that studies the formation and propagation of cracks in materials.
It aims to predict when and how a material will fail due to crack formation.
This is particularly important in structures that need to maintain their integrity under high stress, such as buildings, bridges, and aircraft.
The focus here is on identifying the stress intensity at which a crack becomes unstable, leading to material failure.
By understanding the relationship between stress, crack size, and material properties, engineers can predict fracture behavior.
The Role of Simulation in Fracture Analysis
Simulating elastoplastic fracture is vital for predicting material behavior accurately.
Computer simulations allow engineers to model how materials will respond under various stress conditions without the need for costly experiments.
This process involves creating a mathematical model that integrates material properties, geometry, and loading conditions to predict fractures.
Steps in Elastoplastic Fracture Simulation
1. **Defining Material Properties**: The first step is to input the material’s characteristics, including its elastic modulus, yield strength, and hardening properties.
These properties determine how a material behaves under stress.
2. **Establishing Geometry and Boundary Conditions**: Engineers define the shape and size of the material under consideration.
Boundary conditions specify how the material is held or loaded in a simulation.
3. **Loading Conditions**: This involves applying forces or displacement to the structure as it would experience in real-world conditions.
The loading can be static or dynamic, depending on the scenario being analyzed.
4. **Numerical Analysis**: With parameters set, numerical methods such as the Finite Element Method (FEM) are used to solve the equations governing material behavior.
FEM discretizes the structure into a finer mesh and calculates the distribution of stress and strain across it.
5. **Result Interpretation**: Engineers analyze the output from the simulation, which includes the distribution of stress, the onset of yielding, and the fracture propagation.
This data helps in determining the material’s performance under specified conditions.
Applications of Elastoplastic Fracture Simulation
Elastoplastic fracture simulations have broad applications across various fields:
– **Aerospace Industry**: Ensures the integrity of components subjected to extreme pressure and temperature fluctuations.
– **Automotive Design**: Assists in developing crash-resistant and lightweight vehicles.
– **Civil Engineering**: Used in the design of earthquake-resistant structures and assessing the durability of materials like concrete and steel.
– **Manufacturing**: Optimizes materials for durability and cost-efficiency, especially in metal forming processes.
Advancements and Challenges
While elastoplastic fracture simulation is a powerful tool, it comes with its challenges.
Accurately predicting material behavior necessitates detailed knowledge of material properties and comprehensive computational resources.
Recent advancements in computational power and sophisticated algorithms have improved the precision and efficiency of simulations.
Furthermore, the integration of artificial intelligence and machine learning is helping in automating parts of the simulation process, offering faster and potentially more accurate predictions.
However, challenges remain in accurately modeling complex materials and fracture mechanisms that occur at micro and nano scales.
Conclusion
Elastoplastic fracture simulation stands at the forefront of modern engineering, providing critical insights into material performance and safety.
As technology advances, the ability to predict and mitigate material failure becomes even more robust, influencing countless industries towards safer and innovative designs.
Understanding the nuances of elastic and plastic behavior, along with fracture mechanics, positions engineers to face future challenges with confidence.
資料ダウンロード
QCD調達購買管理クラウド「newji」は、調達購買部門で必要なQCD管理全てを備えた、現場特化型兼クラウド型の今世紀最高の購買管理システムとなります。
ユーザー登録
調達購買業務の効率化だけでなく、システムを導入することで、コスト削減や製品・資材のステータス可視化のほか、属人化していた購買情報の共有化による内部不正防止や統制にも役立ちます。
NEWJI DX
製造業に特化したデジタルトランスフォーメーション(DX)の実現を目指す請負開発型のコンサルティングサービスです。AI、iPaaS、および先端の技術を駆使して、製造プロセスの効率化、業務効率化、チームワーク強化、コスト削減、品質向上を実現します。このサービスは、製造業の課題を深く理解し、それに対する最適なデジタルソリューションを提供することで、企業が持続的な成長とイノベーションを達成できるようサポートします。
オンライン講座
製造業、主に購買・調達部門にお勤めの方々に向けた情報を配信しております。
新任の方やベテランの方、管理職を対象とした幅広いコンテンツをご用意しております。
お問い合わせ
コストダウンが利益に直結する術だと理解していても、なかなか前に進めることができない状況。そんな時は、newjiのコストダウン自動化機能で大きく利益貢献しよう!
(Β版非公開)