- お役立ち記事
- Key points for predicting fatigue life and verifying reliability of solder joints through structural analysis
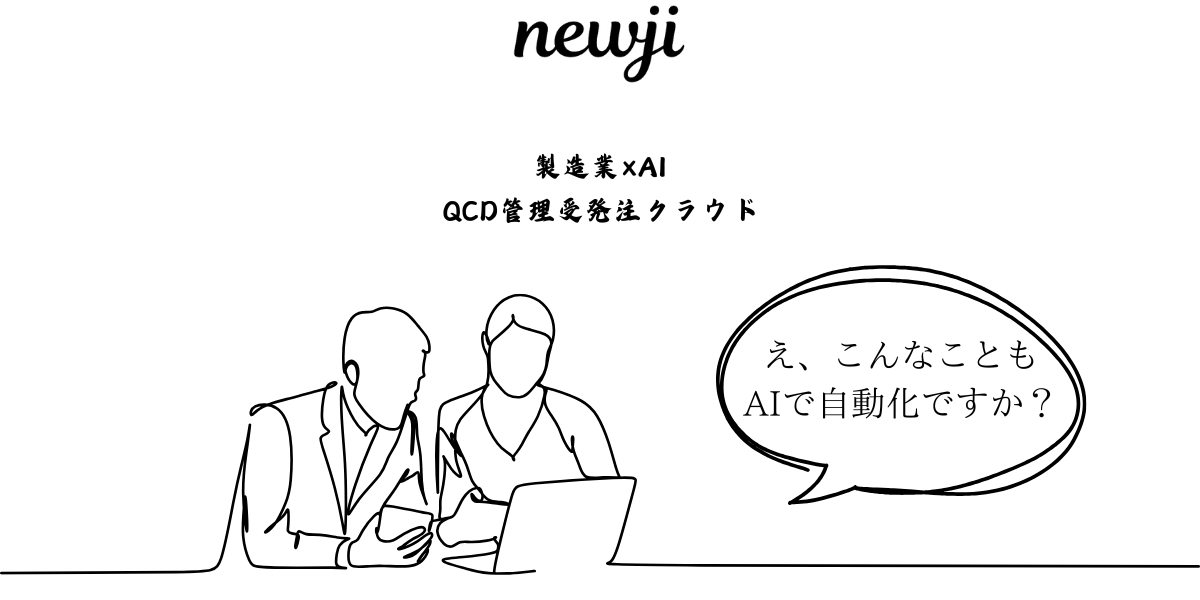
Key points for predicting fatigue life and verifying reliability of solder joints through structural analysis
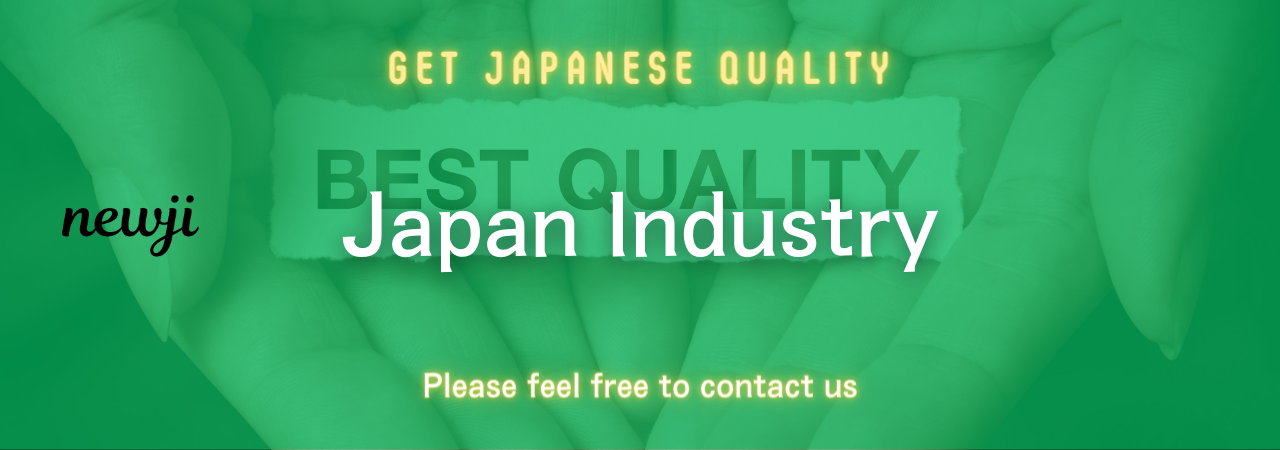
目次
Understanding Solder Joints
Solder joints are crucial components in electronic devices, as they serve as the physical and electrical connection between different components within a circuit.
The durability and reliability of these joints can significantly impact the overall performance of the electronic device.
Due to their importance, predicting the fatigue life and verifying the reliability of solder joints through structural analysis is vital for engineers and manufacturers.
Properly functioning solder joints ensure that circuits operate seamlessly, transferring signals without interruption.
However, like all materials, solder joints are susceptible to fatigue and failure over time due to thermal, mechanical, and environmental stress.
Understanding how to accurately predict these factors can extend the life of electronic devices, reduce maintenance costs, and improve product performance.
The Importance of Structural Analysis
Structural analysis plays a critical role in determining the fatigue life of solder joints.
By simulating the conditions under which the joints will operate, engineers can estimate how they will respond to various stress factors over time.
This process provides insights into potential points of failure, allowing for modifications in design before manufacturing takes place.
Structural analysis involves using sophisticated software to evaluate the mechanical properties and stress distribution within solder joints.
These simulations consider various load types, from thermal cycles to mechanical shocks, to predict how the joint will perform under real-world conditions.
By identifying stress concentration points, manufacturers can enhance joint designs for improved reliability.
Without structural analysis, understanding how joints respond to environments can be speculative at best.
This analysis allows for the development of reliable solder joints that are less likely to fail in demanding scenarios.
Predicting Fatigue Life
Predicting the fatigue life of solder joints involves understanding the cumulative damage these joints might experience over time.
Typically, fatigue life prediction models consider several factors, such as:
- Thermal cycles: Changes in temperature cause expansion and contraction, which can lead to joint fatigue.
- Mechanical stress: Forces from vibrations and shocks can stress solder joints.
- Material properties: The makeup of solder materials influences how they withstand stress over time.
Fatigue life predictions incorporate these elements by using both deterministic and probabilistic methods to estimate the longevity of solder joints under various conditions.
Finite Element Analysis (FEA) is often used to perform this prediction, providing a detailed insight into stress distribution and fatigue failures.
Understanding these predictions allows engineers to identify the optimal material combinations and joint designs for enhanced durability and performance.
Factors Affecting Fatigue Life
Several factors affect the fatigue life of solder joints.
Temperature variations, for instance, play a significant role since electronics generate heat that can expand and contract materials.
Repetitive heating and cooling cycles can introduce micro-cracks over time, weakening the solder joint.
Mechanical loading also impacts fatigue life.
Pressure from physical forces such as vibrations or shocks can accelerate joint deterioration.
Products, therefore, need to be designed with the right balance of flexibility and strength to withstand these loads without failure.
Lastly, the choice of solder material is crucial.
Lead-free solders, though environmentally preferred, often have different mechanical properties compared to traditional leaded solders, which might affect joint longevity.
Understanding these differences is crucial in predicting how solders perform under extended use.
Verifying Reliability
Reliability verification is the process of testing solder joints to ensure they meet specified performance standards.
This step is crucial in the manufacturing stage, as it ensures products can operate under intended conditions without premature failure.
Testing methods for solder joint reliability include:
- Thermal Aging Tests: Testing joints at high temperatures to simulate life long-term effects.
- Thermal Cycling Tests: Stressing the joint with alternating temperatures to observe its durability.
- Mechanical Stress Tests: Applying forces to evaluate how the joint withstands stress.
By implementing these tests, manufacturers can confirm that their products are built to last and function effectively in real-world applications.
Improving Reliability
Reliability of solder joints can be improved through several strategies.
Enhancing the design involves optimizing joint geometry to reduce stress concentrations.
Choosing the right solder alloy that balances mechanical and thermal properties to match operating conditions is another method.
Additionally, using underfill materials can support joints on PCBs, helping distribute mechanical stresses more evenly.
Innovative techniques, such as embedding joints with nano-particles, have shown promise in improving mechanical strength and thermal fatigue resistance.
These improvements ensure that solder joints can withstand prolonged exposure to operational conditions, thereby improving the reliability of the entire device.
Conclusion
Predicting the fatigue life and verifying the reliability of solder joints are essential steps in ensuring the durability and performance of electronic devices.
Structural analysis provides engineers with the tools to foresee potential joint failures and implement necessary design changes before production.
By considering factors such as thermal and mechanical stresses, as well as material properties, manufacturers can extend the fatigue life of solder joints, ensuring reliability in the long term.
Ultimately, rigorous testing and innovation in materials and design strategies will continue to advance the reliability of solder joints, paving the way for the development of more durable electronic devices.
資料ダウンロード
QCD調達購買管理クラウド「newji」は、調達購買部門で必要なQCD管理全てを備えた、現場特化型兼クラウド型の今世紀最高の購買管理システムとなります。
ユーザー登録
調達購買業務の効率化だけでなく、システムを導入することで、コスト削減や製品・資材のステータス可視化のほか、属人化していた購買情報の共有化による内部不正防止や統制にも役立ちます。
NEWJI DX
製造業に特化したデジタルトランスフォーメーション(DX)の実現を目指す請負開発型のコンサルティングサービスです。AI、iPaaS、および先端の技術を駆使して、製造プロセスの効率化、業務効率化、チームワーク強化、コスト削減、品質向上を実現します。このサービスは、製造業の課題を深く理解し、それに対する最適なデジタルソリューションを提供することで、企業が持続的な成長とイノベーションを達成できるようサポートします。
オンライン講座
製造業、主に購買・調達部門にお勤めの方々に向けた情報を配信しております。
新任の方やベテランの方、管理職を対象とした幅広いコンテンツをご用意しております。
お問い合わせ
コストダウンが利益に直結する術だと理解していても、なかなか前に進めることができない状況。そんな時は、newjiのコストダウン自動化機能で大きく利益貢献しよう!
(Β版非公開)