- お役立ち記事
- Reliability evaluation method for lead-free solder joints
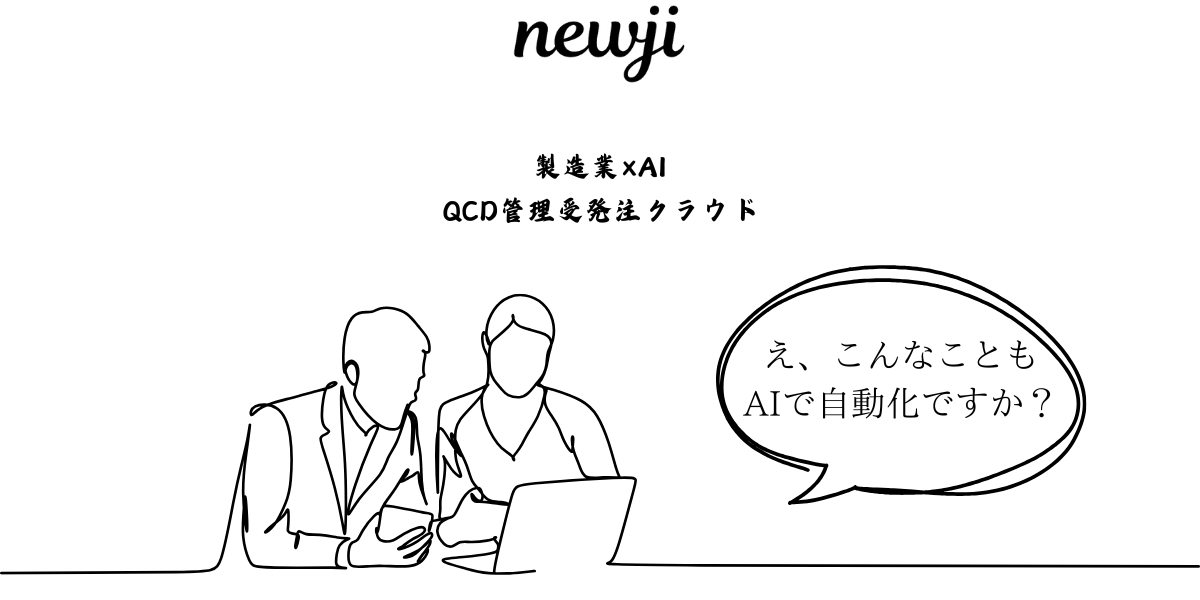
Reliability evaluation method for lead-free solder joints
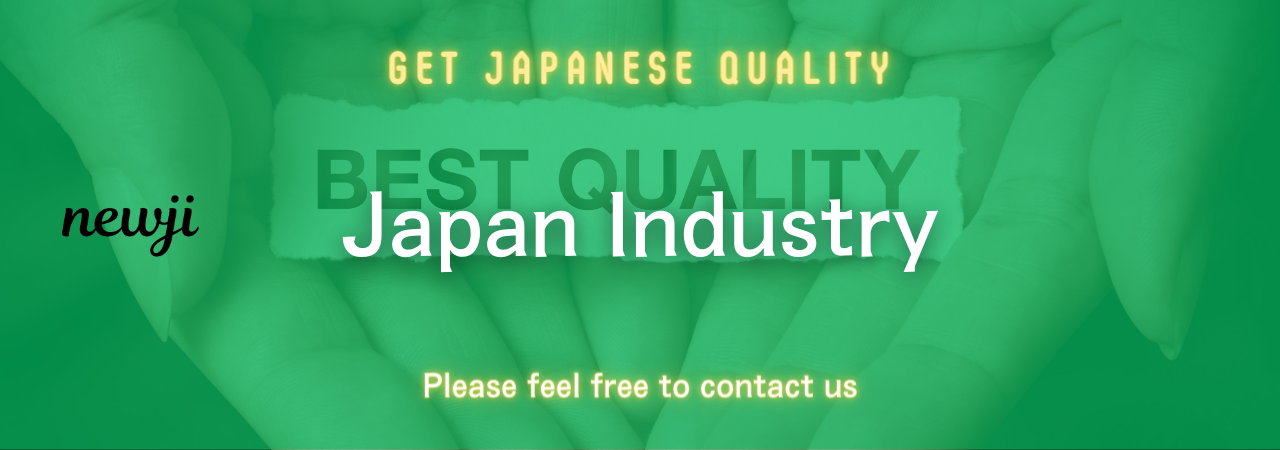
目次
Understanding Lead-Free Solder Joints
Lead-free solder joints have become increasingly important in modern electronics manufacturing.
With the introduction of stricter environmental regulations, such as the Restriction of Hazardous Substances (RoHS) directive, the use of traditional lead-based solders has been significantly reduced.
Lead-free solders are used as a safer alternative, but they come with their own set of challenges in terms of reliability and performance.
Lead-free solder joints are primarily composed of tin (Sn) and various other metals, such as silver (Ag), copper (Cu), bismuth (Bi), or antimony (Sb).
The most common alloy used in lead-free soldering is Sn-Ag-Cu (SAC), particularly SAC305, which consists of 96.5% tin, 3.0% silver, and 0.5% copper.
These compositions are selected to offer a balance of melting point, mechanical strength, and wettability, to meet manufacturing requirements.
The Importance of Evaluating Reliability
Reliability evaluation of lead-free solder joints is crucial for ensuring the long-term performance and safety of electronic devices.
A reliable solder joint must be able to withstand various mechanical stresses, thermal cycles, and environmental conditions throughout its service life.
As electronics are becoming more complex, the demands on solder joints are increasing.
Therefore, evaluating the reliability of these joints is essential to prevent failures that can lead to costly repairs or device malfunctions.
Methods for Evaluating Lead-Free Solder Joints
The reliability evaluation of lead-free solder joints involves several methods and tests.
These help identify potential issues and ensure that the joints meet the necessary performance standards.
Thermal Cycling Tests
Thermal cycling tests simulate the thermal stresses that solder joints experience in real-world applications.
During thermal cycling, the assembled electronic components are subjected to repeated heating and cooling cycles.
This induces stress on the solder joints due to the different coefficients of thermal expansion between various materials.
These tests are critical to evaluate how the solder joints can withstand temperature changes.
Inspecting the test results can reveal whether micro-cracks or voids are developing, which may compromise the joint’s integrity.
Mechanical Testing
Mechanical testing is used to assess the physical strength and durability of solder joints under different loading conditions.
Common tests include pull tests, shear tests, and bend tests, all of which apply mechanical stress to the joints.
The results from mechanical tests can provide insights into the joint’s ability to handle mechanical loads without breaking or failing.
This is particularly important for devices that are subjected to vibrations or physical impacts during use.
Accelerated Life Testing
Accelerated life testing is a method used to predict the long-term reliability of solder joints by exposing them to severe testing conditions over a short period.
These conditions are harsher than normal operating environments and include elevated temperatures and high humidity levels.
By accelerating the rate of solder joint degradation, manufacturers can estimate the joint’s lifespan and identify any potential reliability issues before the product hits the market.
Scanning Electron Microscopy (SEM)
Scanning Electron Microscopy (SEM) is a powerful imaging technique used to analyze the microstructure of lead-free solder joints.
SEM provides high-resolution images of the joint’s surface and cross-section, which helps in identifying defects such as cracks and voids that are not visible to the naked eye.
In addition to structural analysis, SEM can determine the composition of solder joints at a microscopic level, which is valuable for assessing the quality of the solder alloy and identifying any contamination issues.
X-Ray Inspection
X-ray inspection is a non-destructive testing method that allows the evaluation of the internal structure of solder joints without damaging the device.
X-ray imaging can detect internal defects, such as voids and flux residues, that could compromise the joint’s reliability.
Since these defects are not visible from the outside, X-ray inspection provides a comprehensive assessment of the joint’s integrity.
This method is especially useful for complex assemblies with multiple layers of components.
Challenges in Evaluating Lead-Free Solder Joints
Despite the advancements in evaluation methods, there are several challenges associated with assessing the reliability of lead-free solder joints.
Due to the different material properties compared to lead-based solders, lead-free joints may have different failure modes.
Manufacturers need to understand these failure mechanisms to improve the reliability of their products.
In addition, the miniaturization of electronic components poses significant challenges in evaluating solder joints.
As devices become smaller, solder joints also decrease in size, making it difficult to conduct traditional mechanical tests.
Finally, while evaluation methods can predict solder joint reliability under controlled conditions, real-world applications often involve complex and varied stresses.
This requires a combination of testing methods and in-field feedback to achieve a comprehensive evaluation.
Conclusion
Evaluating the reliability of lead-free solder joints is a multifaceted process that requires various testing and analysis methods.
With the transition toward lead-free solders, understanding how these joints perform under different stresses is critical to ensure the performance and safety of electronic devices.
Thermal cycling, mechanical testing, and advanced imaging techniques are essential tools to assess solder joint reliability.
By identifying potential issues early in the development process, manufacturers can enhance product quality and reduce the risk of failures in the field.
As technology evolves, so must the methods for evaluating the reliability of lead-free solder joints.
Continuous research and improvements in testing processes are necessary to meet the growing demands of modern electronics manufacturing.
資料ダウンロード
QCD調達購買管理クラウド「newji」は、調達購買部門で必要なQCD管理全てを備えた、現場特化型兼クラウド型の今世紀最高の購買管理システムとなります。
ユーザー登録
調達購買業務の効率化だけでなく、システムを導入することで、コスト削減や製品・資材のステータス可視化のほか、属人化していた購買情報の共有化による内部不正防止や統制にも役立ちます。
NEWJI DX
製造業に特化したデジタルトランスフォーメーション(DX)の実現を目指す請負開発型のコンサルティングサービスです。AI、iPaaS、および先端の技術を駆使して、製造プロセスの効率化、業務効率化、チームワーク強化、コスト削減、品質向上を実現します。このサービスは、製造業の課題を深く理解し、それに対する最適なデジタルソリューションを提供することで、企業が持続的な成長とイノベーションを達成できるようサポートします。
オンライン講座
製造業、主に購買・調達部門にお勤めの方々に向けた情報を配信しております。
新任の方やベテランの方、管理職を対象とした幅広いコンテンツをご用意しております。
お問い合わせ
コストダウンが利益に直結する術だと理解していても、なかなか前に進めることができない状況。そんな時は、newjiのコストダウン自動化機能で大きく利益貢献しよう!
(Β版非公開)