- お役立ち記事
- Implementation using optimal control technology and digital control and application to DC motor control
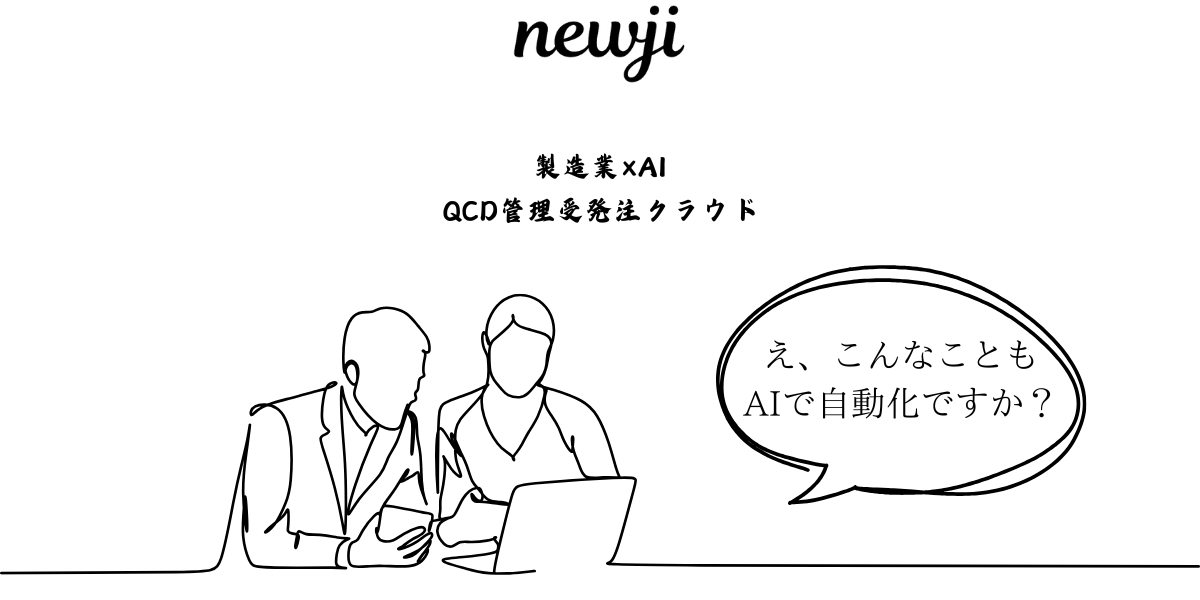
Implementation using optimal control technology and digital control and application to DC motor control
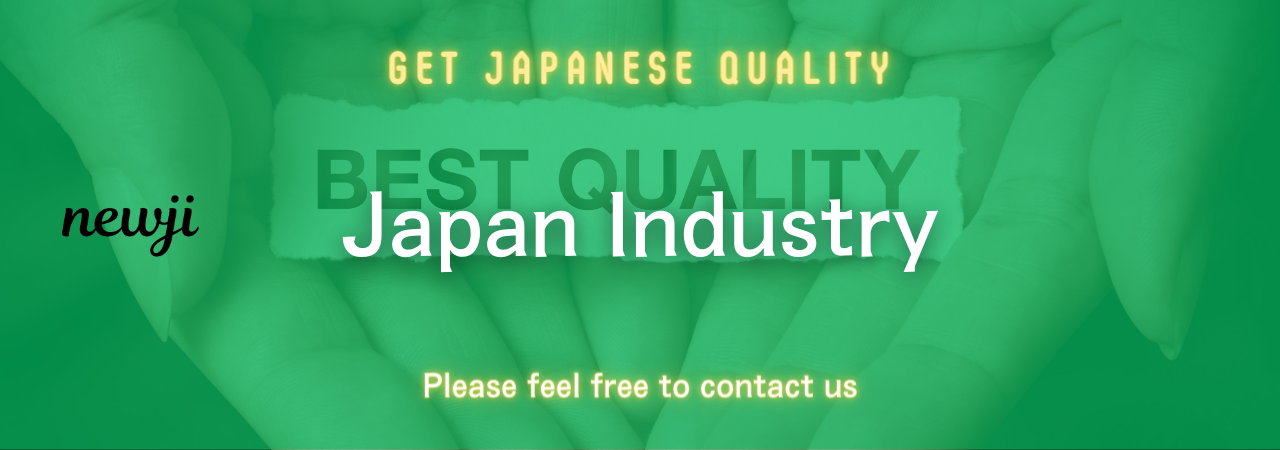
目次
Understanding DC Motor Control
DC motors are vital components in various applications due to their simplicity and ease of use.
They are widely used in electric vehicles, industrial machinery, robotics, and household appliances.
The ability to control these motors effectively is crucial for optimizing performance, ensuring energy efficiency, and extending the lifespan of the machinery.
Basics of DC Motor Control
DC motor control involves the regulation of motor speed, direction, and torque.
This is typically achieved by managing the voltage and current supplied to the motor.
The basic components of a DC motor control system include the motor itself, a power source, and a controller that determines how the motor operates.
For simple projects, basic methods such as potentiometers or resistors can be used to control the motor.
However, for more sophisticated applications, digital control methods become necessary.
Introduction to Digital Control
Digital control systems have profoundly transformed how we manage DC motor operations.
These systems use digital signals for precise control and are often implemented with microcontrollers or digital signal processors (DSPs).
Digital control provides several advantages over analog control systems:
– Increased accuracy and precision
– Better noise immunity
– Flexibility to implement complex algorithms
– Easier integration with other digital systems
Components of a Digital Control System
A typical digital control system for DC motor control comprises several components.
Firstly, a microcontroller acts as the brain of the system, executing the control algorithm.
Sensors are used to provide feedback on motor position, speed, or current.
Finally, an actuator mechanism, usually an H-bridge, provides the necessary voltage and current to the motor.
Optimal Control Techniques
Optimal control is a mathematical approach aimed at designing control systems that minimize a certain performance criterion, such as energy usage or error from a setpoint.
Applying these techniques to DC motor control can significantly enhance the performance and efficiency of the motor.
Types of Optimal Control Techniques
Several optimal control methods can be implemented in digital control systems:
1. **Proportional-Integral-Derivative (PID) Control**: This is one of the most widely used control strategies due to its simplicity and effectiveness.
By tuning the proportional, integral, and derivative gains, a PID controller can maintain desired motor performance under varying conditions.
2. **Model Predictive Control (MPC)**: MPC leverages mathematical models to predict future motor states and optimizes the control inputs to achieve the best performance.
This method is beneficial for systems with multiple constraints or time-varying behavior.
3. **Linear Quadratic Regulator (LQR)**: LQR focuses on linear systems and optimizes the control input based on a quadratic cost function.
It is particularly useful for systems where the tradeoff between control efficiency and error needs balancing.
Application of Optimal Control in DC Motors
Implementing optimal control techniques using digital control methods in DC motors can offer several benefits:
Enhanced Efficiency
Optimal control allows for minimization of energy consumption while ensuring the motor performs tasks effectively.
By adjusting the motor drive signals accurately, optimal control algorithms can reduce power waste and increase overall system efficiency.
Improved Performance
With precise control over motor functions, optimal control techniques can improve dynamic performance, ensuring smooth acceleration and deceleration, and reducing overshoot and steady-state error.
Extended Motor Life
Properly controlling the DC motor using digital methods can lead to reduced wear and tear of mechanical components.
By limiting abrupt changes in speed and torque, these approaches help in prolonging motor life and reliability.
Implementing Digital Control Solutions
To harness these benefits, implementing digital control systems requires careful planning and design:
Choosing the Right Hardware
Selecting appropriate hardware components like microcontrollers or DSPs is essential.
The chosen control platform should support real-time processing capabilities and offer sufficient computational power for running complex algorithms.
Optimization and Tuning
Once the hardware is set, it is crucial to design the control algorithm and tune the parameters to suit the application.
Simulation tools can optimize these parameters before deploying the system to ensure effective real-world performance.
Integration and Testing
Before full-scale implementation, thorough testing needs to be done to ensure the integration of the digital control solution with existing systems is seamless.
Testing helps identify potential issues and ensures the solution is robust under operational conditions.
Conclusion
Optimal control technology, when combined with digital control systems, represents a powerful tool for enhancing DC motor performance.
It leads to improved efficiency, increased reliability, and longevity of the motors in diverse applications.
Understanding the fundamentals of both optimal and digital control is imperative for engineers and designers navigating the ever-evolving landscape of motor control technology.
資料ダウンロード
QCD調達購買管理クラウド「newji」は、調達購買部門で必要なQCD管理全てを備えた、現場特化型兼クラウド型の今世紀最高の購買管理システムとなります。
ユーザー登録
調達購買業務の効率化だけでなく、システムを導入することで、コスト削減や製品・資材のステータス可視化のほか、属人化していた購買情報の共有化による内部不正防止や統制にも役立ちます。
NEWJI DX
製造業に特化したデジタルトランスフォーメーション(DX)の実現を目指す請負開発型のコンサルティングサービスです。AI、iPaaS、および先端の技術を駆使して、製造プロセスの効率化、業務効率化、チームワーク強化、コスト削減、品質向上を実現します。このサービスは、製造業の課題を深く理解し、それに対する最適なデジタルソリューションを提供することで、企業が持続的な成長とイノベーションを達成できるようサポートします。
オンライン講座
製造業、主に購買・調達部門にお勤めの方々に向けた情報を配信しております。
新任の方やベテランの方、管理職を対象とした幅広いコンテンツをご用意しております。
お問い合わせ
コストダウンが利益に直結する術だと理解していても、なかなか前に進めることができない状況。そんな時は、newjiのコストダウン自動化機能で大きく利益貢献しよう!
(Β版非公開)