- お役立ち記事
- Basics of QFD and how to effectively utilize it for FMEA/DR for prevention
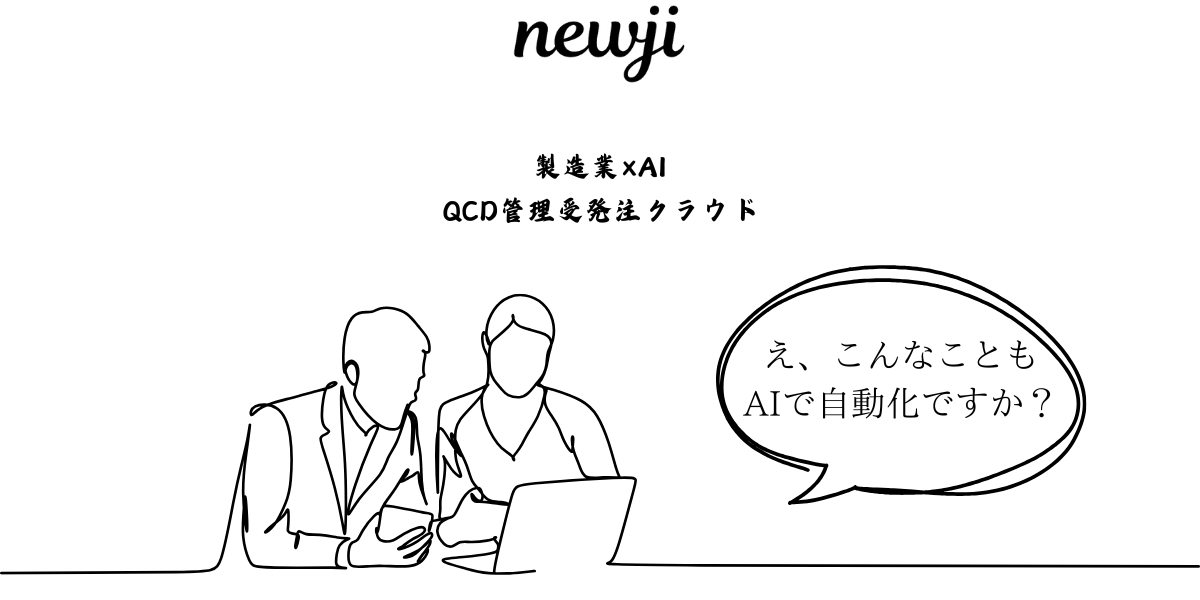
Basics of QFD and how to effectively utilize it for FMEA/DR for prevention
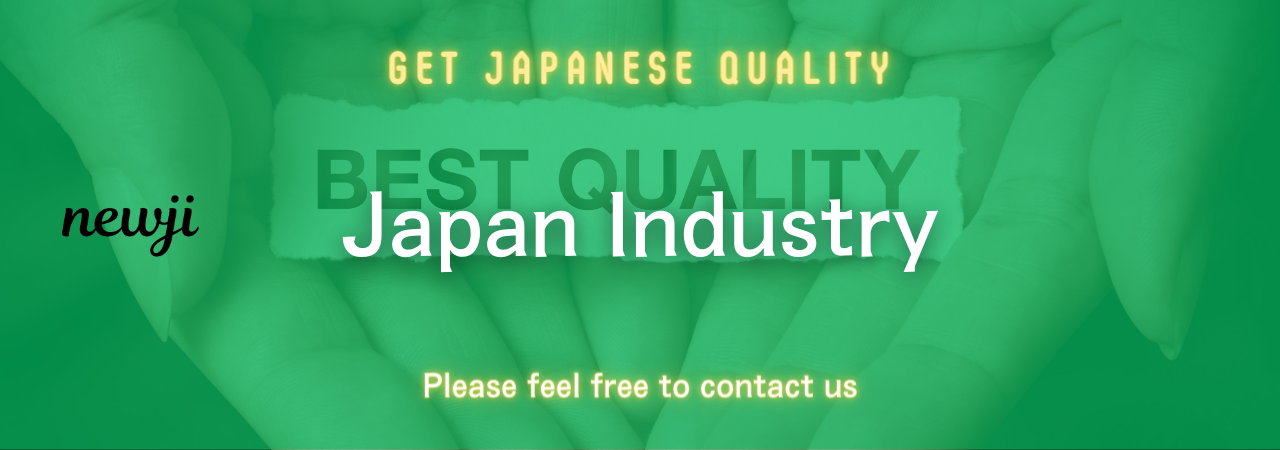
目次
Understanding the Basics of QFD
Quality Function Deployment (QFD) is a methodical approach used primarily by organizations to transform customer needs into engineering characteristics for a product or service.
It acts as a structured approach to defining customer requirements and aligning them with organizational functions and processes.
QFD is not solely about product features but ensuring that every aspect of the product or service aligns with what the customer truly wants.
This concept can significantly improve communication and decision-making within an organization by prioritizing these customer needs and wants.
The House of Quality
One of QFD’s primary tools is the House of Quality.
This device is used to translate customer requirements into appropriate company requirements at each stage, from research and product development to engineering and manufacturing.
The House of Quality matrix helps ensure that there’s a direct alignment of customer desires with the available resources and organizational capabilities.
It has four main components: What (customer requirements), How (features and technical responses), Relationship (correlation between What and How), and Benchmarking (competition analysis).
By using this tool, organizations can focus on optimizing processes and strategies that truly matter to the clients, ensuring a better end-product or service.
Benefits of Implementing QFD
There are numerous advantages to implementing QFD within an organization.
Primarily, it enhances customer satisfaction as products and services are more likely to meet or exceed customer expectations.
Furthermore, QFD reduces the time required for new product development by improving communication among departments and streamlining processes.
Through QFD, organizations may experience reductions in development costs due to more precise requirements and fewer design changes later in the product development cycle.
Additionally, it fosters holistic thinking and prevents tunnel vision as it encourages teams to see the connection between various stages of production and how they impact the end-user.
By establishing clear priorities, QFD maximizes resource allocation and guides firms in focusing on innovative solutions rather than reactive measures.
FMEA and Its Importance
Failure Mode and Effects Analysis (FMEA) is a systematic method used for identifying potential failure modes within a system or process and understanding their impact on product performance.
The main goal of FMEA is to improve reliability by planning ahead for potential failures and taking action before they occur.
It’s an essential tool for risk management, serving to mitigate risks by providing a structured framework for analyzing risk domains and areas of concern.
Steps in Conducting an FMEA
Conducting an effective FMEA involves several key steps.
The first step is to identify all potential failure modes that could occur for each component or process step.
Next, one must assess the effects of these failures, determining how they can impact the system or customer.
Following identification, the failure causes or mechanisms are evaluated.
Once you have mapped this information, you can assign severity, occurrence, and detection ratings to each potential failure mode.
The culmination of these ratings helps organizations prioritize risks and determine where the most critical areas for attention lie.
Finally, improvement actions are taken to reduce the likelihood of failure and improve product or process reliability.
FMEA Benefits
FMEA contributes to improved system or product quality and reliability, resulting in enhanced customer satisfaction.
It enables organizations to be proactive in identifying areas that could potentially lead to significant problems and outline mitigation strategies.
Consequently, costs associated with defects or failures are reduced since remedial actions are outlined even before problems arise.
Moreover, FMEA enhances teamwork and communication as teams from various sectors of an organization work together to brainstorm and evaluate potential problems.
Ultimately, this leads to innovative solutions and improved system designs.
Utilizing QFD and FMEA Together
When integrated properly, QFD and FMEA can act as a synergy, boosting the effectiveness of risk management and product development strategies.
By employing QFD, businesses first capture customer requirements and align their key processes to meet those needs.
FMEA then provides a detailed analysis of potential failures within these processes and guides preventive measures.
This combination ensures both the innovation and reliability of products.
Steps for Integration
To combine QFD with FMEA, start by using the QFD process to establish a clear understanding of customer needs and product characteristics.
Organize these characteristics in the House of Quality to align them with prioritized objectives.
Once the QFD groundwork is laid, perform an FMEA to identify and prioritize potential failure modes of the planned product or process.
Highlight the failure modes that could directly impact priority customer requirements highlighted through the QFD.
This direct correlation between what customers value and how those values could be jeopardized equips organizations with actionable insights for risk mitigation.
After developing preventive strategies, continually update the QFD and FMEA documents to reflect evolving customer expectations and operational learnings.
Future Benefits
This integrated approach ensures a complete feedback system involving customer interaction, innovation, risk assessment, and solution evaluation.
It improves market competitiveness, as businesses are consistently applying best practices in product development and risk management.
Moreover, customer trust is bolstered as products and services continue to meet their expectations with reduced instances of faults or failures.
In a world where consumer demands evolve rapidly, such an integrated strategy empowers organizations to not only deliver quality today but remain agile and prepared for tomorrow’s challenges.
資料ダウンロード
QCD調達購買管理クラウド「newji」は、調達購買部門で必要なQCD管理全てを備えた、現場特化型兼クラウド型の今世紀最高の購買管理システムとなります。
ユーザー登録
調達購買業務の効率化だけでなく、システムを導入することで、コスト削減や製品・資材のステータス可視化のほか、属人化していた購買情報の共有化による内部不正防止や統制にも役立ちます。
NEWJI DX
製造業に特化したデジタルトランスフォーメーション(DX)の実現を目指す請負開発型のコンサルティングサービスです。AI、iPaaS、および先端の技術を駆使して、製造プロセスの効率化、業務効率化、チームワーク強化、コスト削減、品質向上を実現します。このサービスは、製造業の課題を深く理解し、それに対する最適なデジタルソリューションを提供することで、企業が持続的な成長とイノベーションを達成できるようサポートします。
オンライン講座
製造業、主に購買・調達部門にお勤めの方々に向けた情報を配信しております。
新任の方やベテランの方、管理職を対象とした幅広いコンテンツをご用意しております。
お問い合わせ
コストダウンが利益に直結する術だと理解していても、なかなか前に進めることができない状況。そんな時は、newjiのコストダウン自動化機能で大きく利益貢献しよう!
(Β版非公開)