- お役立ち記事
- 工場の効率的なレイアウト設計と改善方法およびそのポイント
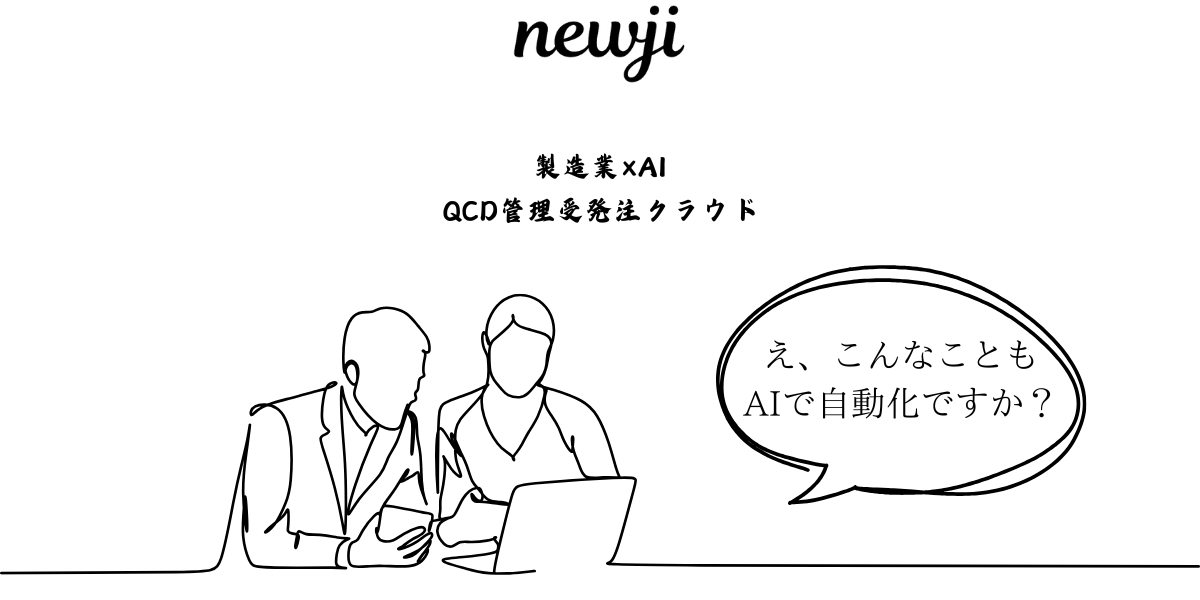
工場の効率的なレイアウト設計と改善方法およびそのポイント
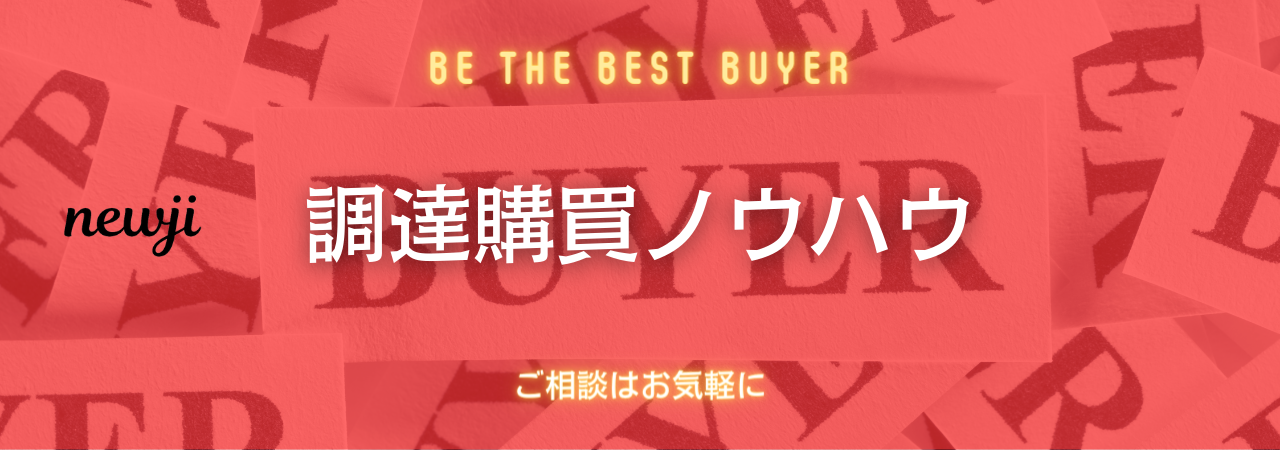
目次
工場レイアウト設計の重要性と基本的な考え方
製造業において、工場のレイアウト設計は生産効率や品質管理に直結する重要な要素です。
適切なレイアウトは生産工程をスムーズに進行させるだけでなく、労働環境の改善や不良品の減少、安全性の向上にも寄与します。
まずは基本的な考え方を押さえ、レイアウト設計の基本を理解しておきましょう。
レイアウトの主な目的は、材料の流れを効率的に管理することです。
そのためには、プロセスの連続性を確保し、異なる作業間の待ち時間を最小限に抑える必要があります。
さらに、作業員の動線をスムーズにし、無駄な移動を減らすことで生産性を向上させることが求められます。
レイアウト設計における基本的な5S活動
5S活動(整理、整頓、清掃、清潔、しつけ)は、工場内の規律を維持し、レイアウト設計を行う際の基礎的な原則です。
この取り組みは、作業環境を整えることで、生産効率を高めるだけでなく、品質や安全性の向上にも繋がります。
整理と整頓を徹底することで、必要なものをすぐに見つけて使用することができ、清掃と清潔により、設備の故障を防ぎ、最適な稼働状態を維持できます。
しつけはこのサイクルを定着させるために重要です。
効率的なレイアウト設計のステップ
レイアウト設計を始める前に、現状の工場内の問題点を洗い出し、改善ポイントを明確にすることが重要です。
目指すべき理想のレイアウトは、工場の生産性を最大化し、不良品率を下げることを基準に考えます。
1. 現状の分析
最初に行うべきは、現状分析です。
実際にどのような作業がどのような手順で行われているのか詳細に観察し、プロセスごとの時間や移動距離を把握します。
この際、作業者からのヒアリングを行い、彼らの実感や提案を反映させるとよいです。
現状のムダを洗い出し、具体的な改善策を練る材料にします。
2. 理想のプロセスフローを設計
次に、理想的なプロセスフローを設計します。
材料や製品の流れをスムーズにするためには、プロセス間の待ち時間を極力なくすようにします。
また、作業者の動線を短くし、安全な作業ができるように配慮する必要もあります。
3. レイアウト案の具体化とシミュレーション
設計段階では、複数のレイアウト案を作成し、それぞれのメリットとデメリットを比較します。
シミュレーションツールを用いて、実際の作業効率や人員配置、資材の流れを可視化し、最良の案を選出します。
4. 試験運用と調整
選んだレイアウト案を小規模で試験運用し、実運用における問題点を洗い出します。
この段階で得られたフィードバックを元に、必要な調整を施します。
5. 導入と再評価
最終的に、全体でレイアウトを導入し、その成果を定期的に評価します。
レイアウトは固定的なものではなく、状況に応じて柔軟に調整することが重要です。
改善方法とその実践ポイント
工場のレイアウト改善において重要なことは、一度設計を終えたからといってそこで終わりではなく、常に改善を続けることです。
変化する市場環境や技術革新と共に、工場のレイアウトも環境に適応する必要があります。
レイアウト改善のためのPDCAサイクル
PDCAサイクル(計画、実行、評価、改善)は、継続的な改善活動のフレームワークとして有効です。
レイアウト改善の際もこのサイクルを回すことで、常に新たな課題を見つけ出し、改善策を実施します。
計画フェーズでは、新たな問題や課題を特定し、施策を計画します。
実行フェーズでは、計画した改善策を実行し、その影響をリアルタイムで観察します。
評価フェーズでは、改善策の効果を評価し、どこをさらに改善できるかを考えます。
最後に改善フェーズでは、得られた知見を元にさらなる改善を加えていきます。
デジタルツールの活用
製造業でもデジタル化は進んでおり、レイアウト設計や分析においてもデジタルツールは大いに役立ちます。
特にシミュレーションソフトウェアや3Dモデリングツールを活用することで、よりリアルな環境を想定でき、現実に近い判断が可能です。
デジタルツールを使うことで、試行錯誤の段階を強力にサポートし、短期間で効率的なレイアウト設計を行うことができます。
クラウドベースのツールを使えば、複数のステークホルダーが同時に情報を共有でき、チームでの協働も容易になります。
昭和から抜け出すための第一歩
日本の製造業は、未だに「前例に倣う」文化が強く残っており、新しい取り組みに二の足を踏む場合があります。
しかし、市場の競争が激化し、グローバルな視点での効率化が求められている現代において、柔軟かつ迅速な対応ができる企業が生き残る鍵となります。
工場レイアウトの効率化と改善は、昭和から抜け出し、デジタル時代に即応するための最初の一歩です。
過去の知識や経験を活かしつつ、新たな技術や方法論を積極的に導入する姿勢が求められます。
最終的には、組織全体での意識改革が必要です。
工場内のスタッフ全員が改善活動に積極的に参加し、継続的な改善を共に作り上げることで、真に強い組織文化が育まれるでしょう。
以上のポイントを踏まえて、効率的なレイアウト設計や改善を進めることで、製造業全体の発展に寄与していきましょう。
資料ダウンロード
QCD調達購買管理クラウド「newji」は、調達購買部門で必要なQCD管理全てを備えた、現場特化型兼クラウド型の今世紀最高の購買管理システムとなります。
ユーザー登録
調達購買業務の効率化だけでなく、システムを導入することで、コスト削減や製品・資材のステータス可視化のほか、属人化していた購買情報の共有化による内部不正防止や統制にも役立ちます。
NEWJI DX
製造業に特化したデジタルトランスフォーメーション(DX)の実現を目指す請負開発型のコンサルティングサービスです。AI、iPaaS、および先端の技術を駆使して、製造プロセスの効率化、業務効率化、チームワーク強化、コスト削減、品質向上を実現します。このサービスは、製造業の課題を深く理解し、それに対する最適なデジタルソリューションを提供することで、企業が持続的な成長とイノベーションを達成できるようサポートします。
オンライン講座
製造業、主に購買・調達部門にお勤めの方々に向けた情報を配信しております。
新任の方やベテランの方、管理職を対象とした幅広いコンテンツをご用意しております。
お問い合わせ
コストダウンが利益に直結する術だと理解していても、なかなか前に進めることができない状況。そんな時は、newjiのコストダウン自動化機能で大きく利益貢献しよう!
(Β版非公開)