- お役立ち記事
- 設計FMEAによる品質問題の完璧な未然防止とそのポイント
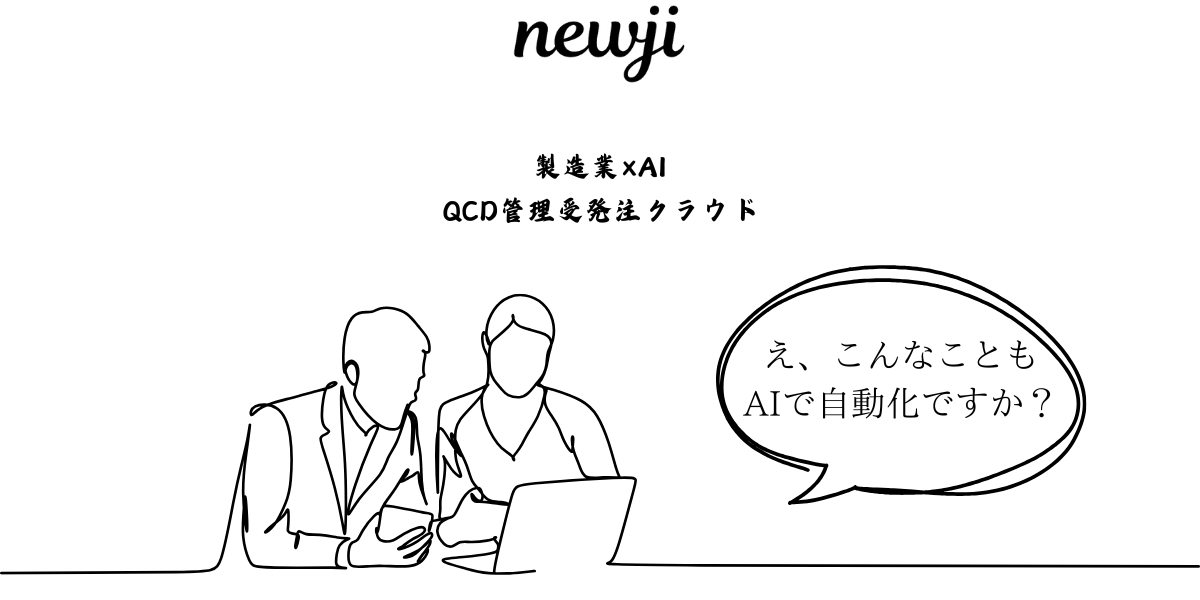
設計FMEAによる品質問題の完璧な未然防止とそのポイント
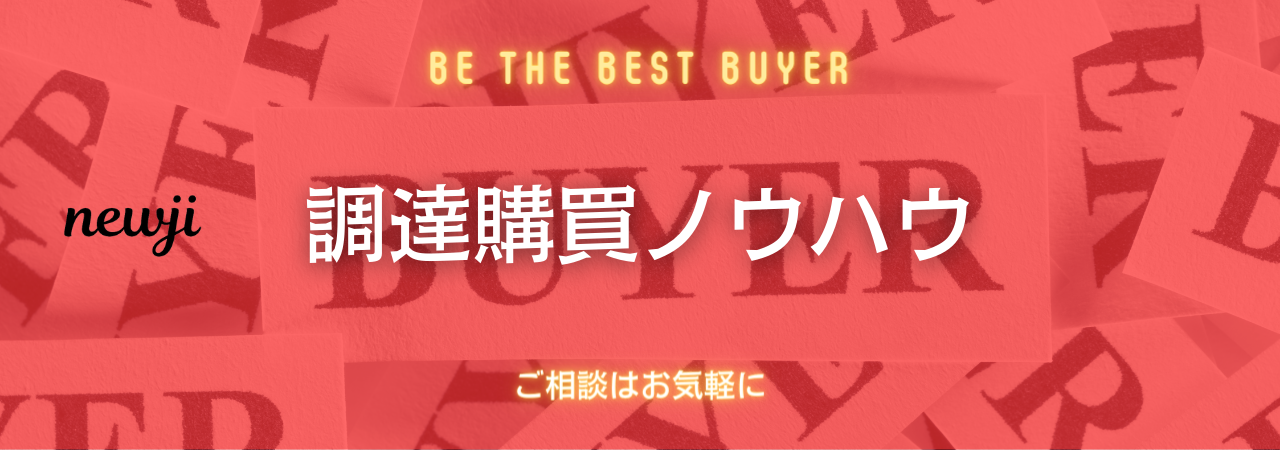
目次
設計FMEAとは何か?
設計FMEA(Failure Mode and Effects Analysis)は、製品設計段階での潜在的な不具合を予測し、未然に防止するための手法です。
FMEAは、「潜在故障モードとその影響を分析する」という意味で、特に新製品の開発時に用いられます。
FMEAは、製品やプロセスの信頼性を向上させることで、製造業の品質問題を未然に防ぐ重要な役割を果たします。
それには、設計や製造過程で発生し得る故障モードの特定、各故障の影響評価、故障原因の特定、そして対策の検討と実施が含まれます。
設計FMEAは特に、設計プロセスの初期段階で適用されることで、設計ミスを未然に防ぎ、後工程での手戻りを大幅に削減することが期待できます。
設計FMEAを導入するメリット
設計FMEAを正しく実施することにより、製造業においていくつかの顕著なメリットが得られます。
コスト削減
問題が発生した場合、それを後工程で修正するのには莫大な費用がかかります。
不具合を未然に発見し、ひと手間かけることで、後々の手戻りを最小化することが可能です。
品質向上
設計段階で問題を特定し、改善策を講じることにより、高品質な製品を提供することができます。
これにより顧客満足度の向上が期待できます。
リスクの最小化
FMEAを通じて潜在的なリスクを洗い出し、分類し、優先順位をつけることで、リスク管理が効率的に行われます。
設計FMEAのプロセス
設計FMEAを実施する際の基本的なプロセスを以下に示します。
1. チームの編成
FMEAを効果的に実施するためには、多様な専門知識を持つ人材からなるチームが必要です。
設計者、品質管理者、生産技術者などの専門家を含め、クロスファンクショナルなチームを組織します。
2. システムや製品の理解
対象となる製品やシステムの機能、特性、利用環境について十分に理解しておくことが重要です。
これにより、どの部分で故障が発生しやすいかを予測することができます。
3. 潜在的故障モードと影響の特定
設計における潜在的な故障モード(どのような不具合が発生しうるのか)をリストアップします。
各故障モードが起きた場合にどのような影響が生じるかを評価します。
4. 故障の原因と発生確率の評価
それぞれの故障モードに対する原因を特定し、それが発生する確率を評価します。
このステップは、どの故障モードに重点的に対策を講じるべきかを決定するのに重要です。
5. 優先度の決定
故障モードの影響度、発生確率、検出の難易度を総合的に評価し、優先度(リスク優先数: RPN)を決定します。
RPNが高い故障モードに対して、最初に対策を講じることが推奨されます。
6. 改善策の検討と実施
特定された優先度の高い故障に対し、効果的な改善策を検討し、実施します。
必要に応じて、設計やプロセスを修正し、リスクを低減するための措置を講じます。
7. 結果のレビューと続けること
FMEAの結果を定期的にレビューし、改善策の有効性を確認します。
新たな発見や変更点が生じた場合は、FMEAのエントリーを更新し、継続的な改善を図ります。
設計FMEA成功の鍵となるポイント
設計FMEAを効果的に活用するためのポイントを以下に示します。
チーム全体での協力
FMEAはチームで行うプロセスです。
異なる専門分野からの知見を取り入れることで、多角的な視点での分析が可能となります。
円滑なコミュニケーションと協力体制が成功の鍵です。
データの活用
以前のプロジェクトや類似製品での知見を活用することで、FMEAの精度が向上します。
過去の設計データや故障データを有効活用し、仮説を検証する際の指針とします。
客観的な評価
FMEAの評価は、できるだけ客観的なデータや情報に基づいて行うことが重要です。
主観的な評価に偏ることなく、データに基づいた分析を心がけましょう。
定期的な見直しと更新
設計が変更された場合や新たな知見が得られた場合には、FMEAを定期的に見直し、更新するプロセスを導入します。
不断の改善と最新情報の反映が重要です。
設計FMEAの事例
設計FMEAが実際の製造業でどのように適用されたか、具体的な事例を紹介します。
例えば、自動車メーカーでは新型エンジンの設計においてFMEAを適用しました。
複雑なエンジンシステムの中で、特定の部品が熱による劣化で故障しやすいことが発見されました。
FMEAの結果に基づき、耐熱性の高い材料を使用することで、長期の信頼性を確保しました。
このようなFMEAの導入により、設計段階での問題発生を未然に防ぎ、後工程のコスト削減と製品の品質向上を達成しました。
まとめ
設計FMEAは、製造業において品質問題を未然に防止するための強力な手法です。
効果的なFMEAの実施には、組織内での協力体制、データの活用、客観的な評価、そして定期的な見直しと更新が重要となります。
製造業の現場では、設計段階での品質確保が競争力強化に直結します。
設計FMEAの実施を通じて、より高品質な製品の提供を目指し、顧客の信頼を得ることが求められます。
また、FMEAのプロセスを継続的に改善することで、製品ライフサイクル全体にわたって持続的な品質向上を図ることができます。
資料ダウンロード
QCD調達購買管理クラウド「newji」は、調達購買部門で必要なQCD管理全てを備えた、現場特化型兼クラウド型の今世紀最高の購買管理システムとなります。
ユーザー登録
調達購買業務の効率化だけでなく、システムを導入することで、コスト削減や製品・資材のステータス可視化のほか、属人化していた購買情報の共有化による内部不正防止や統制にも役立ちます。
NEWJI DX
製造業に特化したデジタルトランスフォーメーション(DX)の実現を目指す請負開発型のコンサルティングサービスです。AI、iPaaS、および先端の技術を駆使して、製造プロセスの効率化、業務効率化、チームワーク強化、コスト削減、品質向上を実現します。このサービスは、製造業の課題を深く理解し、それに対する最適なデジタルソリューションを提供することで、企業が持続的な成長とイノベーションを達成できるようサポートします。
オンライン講座
製造業、主に購買・調達部門にお勤めの方々に向けた情報を配信しております。
新任の方やベテランの方、管理職を対象とした幅広いコンテンツをご用意しております。
お問い合わせ
コストダウンが利益に直結する術だと理解していても、なかなか前に進めることができない状況。そんな時は、newjiのコストダウン自動化機能で大きく利益貢献しよう!
(Β版非公開)