- お役立ち記事
- Accelerating Product Development with QFD! Innovation Strategies for Manufacturing
Accelerating Product Development with QFD! Innovation Strategies for Manufacturing
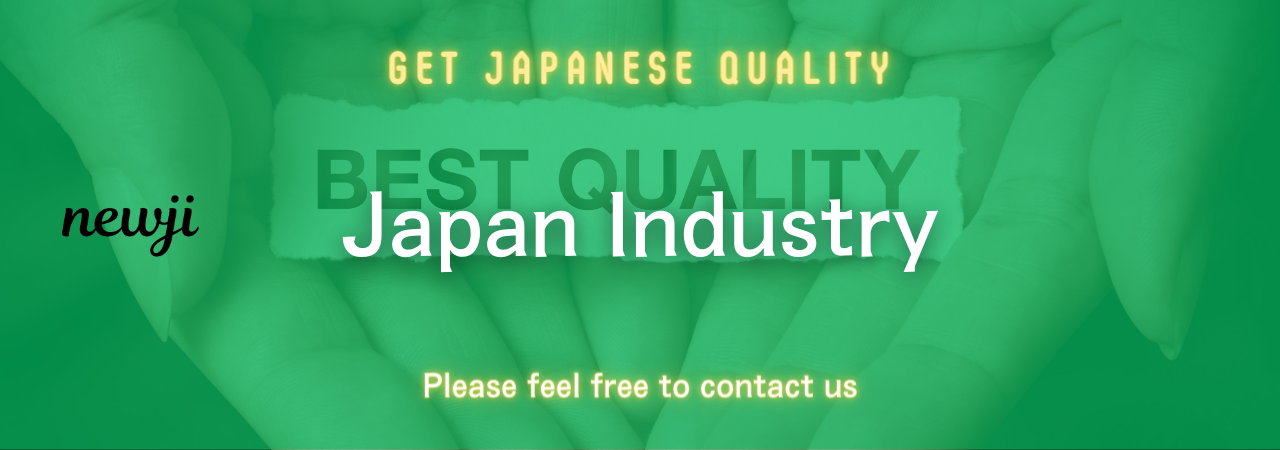
Quality Function Deployment (QFD) is an incredibly effective tool for enhancing product development processes.
It helps businesses deliver high-quality products that meet customer expectations.
With QFD, manufacturers can prioritize customer needs and translate them into specific engineering characteristics.
This structured approach accelerates the product development cycle, paving the way for innovation and competitive advantage.
目次
What is Quality Function Deployment (QFD)?
QFD is a technique that originated in Japan in the late 1960s, primarily for improving product design and quality.
The primary goal is to ensure that customer requirements are the focal point throughout the product development process.
By using QFD, manufacturing teams can systematically analyze and prioritize these requirements.
The process involves creating a series of matrices, often referred to as the “House of Quality.”
These matrices link customer needs (what customers want) to design specifications (how the company will achieve these needs).
Overall, QFD serves as a bridge between the market and manufacturing, ensuring that what is being produced is aligned with what customers are demanding.
Importance of Customer Voice in QFD
In any competitive market, understanding the voice of the customer is crucial.
QFD places immense value on capturing customer feedback and needs.
This information is then used to guide the entire product development process.
By aligning product features with customer needs, manufacturers can deliver solutions that precisely meet market demands.
Engaging with customers early in the development process can yield numerous benefits.
It can help identify pain points, preferences, and unmet needs.
This insight can drive innovation, leading to the creation of highly differentiated products.
Thus, QFD is not just a tool for product improvement; it’s a powerful innovation strategy.
Building the House of Quality
The cornerstone of QFD is the House of Quality, a comprehensive matrix that organizes customer needs and technical requirements.
Here’s a step-by-step guide to building this matrix:
1. Identify Customer Requirements
Start by conducting surveys, focus groups, and interviews to gather detailed customer feedback.
What features do customers find valuable?
What issues are they experiencing with current products?
This data forms the foundation of the House of Quality.
2. Translate Requirements into Technical Specifications
Next, translate these customer requirements into specific, actionable technical specifications.
For example, if customers want a more durable product, identify the materials and design changes needed to achieve this.
3. Prioritize Requirements
Not all customer needs are equally important.
Prioritize these requirements based on factors such as importance to the customer, technical feasibility, and competitive analysis.
4. Address Competitive Products
Analyze competitors’ products to see how they meet customer needs.
This can provide valuable insights into strengths and weaknesses, guiding your design decisions.
5. Develop a Relationship Matrix
Create a matrix that shows the relationship between customer requirements and technical specifications.
This helps teams understand which technical changes will have the most significant impact on customer satisfaction.
6. Rate the Degree of Customer Satisfaction
Use a rating system to evaluate how well your product meets customer needs compared to competitors.
This can help identify areas for improvement.
Accelerating Product Development with QFD
QFD can significantly speed up the product development cycle.
Here’s how:
1. Enhanced Collaboration
QFD promotes cross-functional collaboration, bringing together teams from marketing, engineering, and production.
This integrated approach ensures that everyone is on the same page, reducing the risk of miscommunication and costly errors.
With a clear focus on customer needs, teams can work seamlessly towards common goals.
2. Efficient Resource Allocation
By prioritizing customer requirements, QFD helps allocate resources more efficiently.
Teams can concentrate on features that matter most to customers, avoiding unnecessary development efforts.
This focus on high-impact areas results in faster development cycles and optimized use of resources.
3. Reduced Time-to-Market
QFD’s structured approach helps streamline the entire development process.
By systematically addressing customer needs and technical requirements, teams can avoid time-consuming iterations and revisions.
This leads to a shorter time-to-market, giving businesses a competitive edge.
4. Improved Product Quality
By emphasizing customer satisfaction, QFD naturally leads to higher-quality products.
When products are designed with customer needs in mind, they are more likely to meet or exceed expectations.
This focus on quality can enhance brand reputation and customer loyalty.
Driving Innovation through QFD
QFD is not just about improving existing products; it’s a catalyst for innovation.
By understanding customer needs deeply, manufacturers can uncover opportunities for groundbreaking solutions.
Here’s how QFD drives innovation:
1. Identifying Unmet Needs
QFD helps identify gaps in the market that competitors may have overlooked.
By addressing these unmet needs, businesses can introduce innovative products that solve real problems.
This can lead to market disruption and the creation of new product categories.
2. Encouraging Creative Solutions
The structured nature of QFD provides a clear framework for brainstorming and problem-solving.
Teams can explore creative solutions to meet customer needs, leading to innovative features and functionalities.
This systematic approach fosters a culture of continuous improvement and creativity.
3. Fostering a Customer-Centric Culture
QFD embeds the voice of the customer into the fabric of the organization.
This customer-centric mindset encourages teams to think like their customers, driving innovation from a user perspective.
By putting customer needs at the forefront, businesses can develop products that truly resonate with the market.
Conclusion
Quality Function Deployment (QFD) is a powerful methodology for accelerating product development and driving innovation.
By focusing on customer needs, QFD helps businesses create products that align with market demands.
The structured approach of QFD enhances collaboration, optimizes resource allocation, and reduces time-to-market.
Furthermore, QFD’s emphasis on customer satisfaction naturally leads to higher-quality products.
Most importantly, QFD is a catalyst for innovation, helping businesses identify unmet needs and explore creative solutions.
By adopting QFD, manufacturers can stay ahead of the competition and deliver exceptional products that delight customers.
資料ダウンロード
QCD調達購買管理クラウド「newji」は、調達購買部門で必要なQCD管理全てを備えた、現場特化型兼クラウド型の今世紀最高の購買管理システムとなります。
ユーザー登録
調達購買業務の効率化だけでなく、システムを導入することで、コスト削減や製品・資材のステータス可視化のほか、属人化していた購買情報の共有化による内部不正防止や統制にも役立ちます。
NEWJI DX
製造業に特化したデジタルトランスフォーメーション(DX)の実現を目指す請負開発型のコンサルティングサービスです。AI、iPaaS、および先端の技術を駆使して、製造プロセスの効率化、業務効率化、チームワーク強化、コスト削減、品質向上を実現します。このサービスは、製造業の課題を深く理解し、それに対する最適なデジタルソリューションを提供することで、企業が持続的な成長とイノベーションを達成できるようサポートします。
オンライン講座
製造業、主に購買・調達部門にお勤めの方々に向けた情報を配信しております。
新任の方やベテランの方、管理職を対象とした幅広いコンテンツをご用意しております。
お問い合わせ
コストダウンが利益に直結する術だと理解していても、なかなか前に進めることができない状況。そんな時は、newjiのコストダウン自動化機能で大きく利益貢献しよう!
(Β版非公開)