- お役立ち記事
- A Comprehensive Explanation of the Industrial Robot Assembly Process
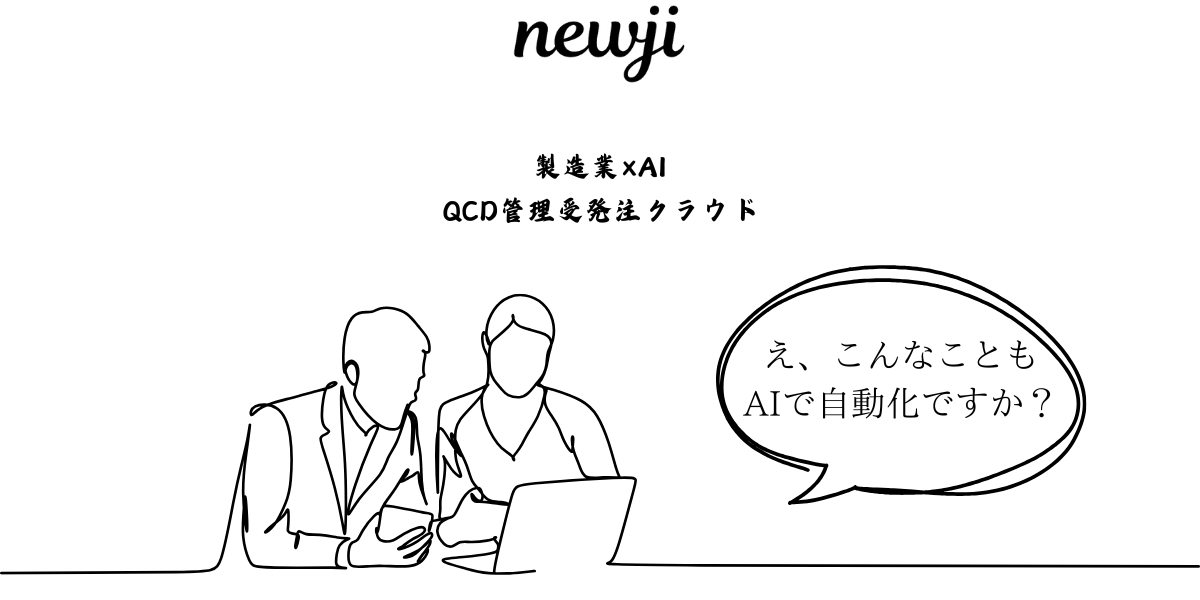
A Comprehensive Explanation of the Industrial Robot Assembly Process
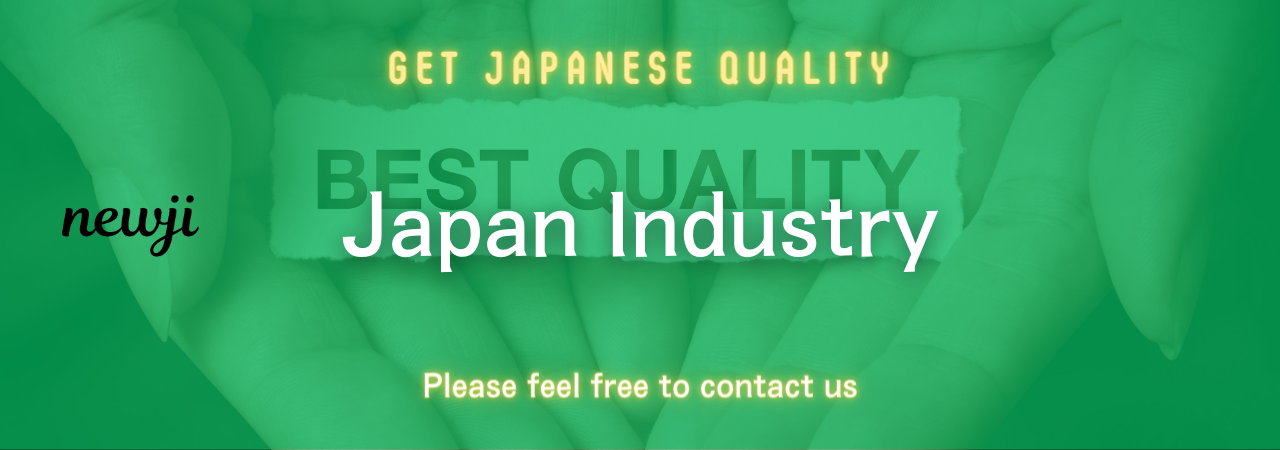
Industrial robots have become an integral part of modern manufacturing processes.
Their ability to perform repetitive tasks with high precision and efficiency makes them invaluable assets in various industries.
Understanding the industrial robot assembly process is crucial for optimizing production and ensuring high-quality outputs.
目次
The Components of an Industrial Robot
Before delving into the assembly process, it’s essential to understand the key components that make up an industrial robot.
Manipulator
The manipulator, often referred to as the robot arm, is the primary component responsible for executing tasks.
Its design mimics a human arm, featuring joints that provide a wide range of motion.
Controller
The controller acts as the robot’s brain.
It processes inputs, executes programmed instructions, and directs the manipulator’s movements.
End Effector
Attached to the end of the manipulator, the end effector is the tool that interacts with the environment.
It can be a gripper, welding torch, painting gun, or any other tool required for specific tasks.
Power Supply
The power supply provides the necessary energy for the robot to operate.
This can be electrical, hydraulic, or pneumatic, depending on the robot’s design and application.
Sensors
Sensors gather data from the robot’s environment, enabling it to adjust its actions accordingly.
Common sensors include vision systems, force sensors, and proximity sensors.
The Assembly Process
Now that we have an understanding of the essential components, let’s explore the step-by-step assembly process of an industrial robot.
Step 1: Frame Construction
The assembly process begins with constructing the robot’s frame.
This frame serves as the skeleton of the robot, providing structural support for all other components.
The frame is typically made from durable materials such as steel or aluminum to withstand the rigors of industrial environments.
Step 2: Installing the Manipulator
Once the frame is ready, the next step is to install the manipulator.
This involves mounting the robot arm onto the frame and securing it in place.
The joints and actuators within the manipulator are then connected to ensure they can move fluidly and accurately.
Step 3: Attaching the End Effector
With the manipulator in place, the end effector is attached at the robot arm’s terminal end.
Depending on the robot’s intended application, the end effector can vary significantly.
For example, a welding robot would have a welding torch, while a pick-and-place robot would have a gripper.
Step 4: Installing the Controller
The controller is the next component to be installed.
It is typically housed in a separate enclosure to protect it from environmental factors and potential damage.
The controller is connected to the manipulator and end effector, allowing it to send commands and receive feedback from these components.
Step 5: Integrating Sensors
Sensors are then integrated into the robot to provide it with the ability to perceive its environment.
This step involves mounting sensors on the manipulator and end effector, as well as running the necessary wiring to connect them to the controller.
Calibration is often required to ensure the sensors provide accurate data.
Step 6: Connecting the Power Supply
The next step is to connect the power supply to the robot.
This involves attaching the power cables to the controller and other components that require energy.
For hydraulic or pneumatic systems, this step also includes connecting hoses and ensuring proper pressure levels.
Step 7: Programming
Once all physical components are in place, the robot needs to be programmed to perform its intended tasks.
This involves writing code that instructs the robot on how to move, when to activate the end effector, and how to respond to sensory inputs.
Modern industrial robots often use user-friendly programming interfaces, allowing technicians to design complex routines without advanced coding knowledge.
Step 8: Testing
With the robot fully assembled and programmed, it undergoes a series of tests to ensure everything is functioning correctly.
This includes verifying the accuracy and repeatability of movements, checking sensor inputs, and validating end effector operations.
Any issues identified during testing are addressed to ensure the robot performs to specifications.
Advanced Considerations
Beyond the basic assembly process, there are advanced considerations to optimize industrial robot performance.
Safety Features
Incorporating safety features is paramount in industrial settings.
This can include implementing physical barriers, emergency stop buttons, and advanced safety algorithms to prevent accidents.
Maintenance Protocols
Regular maintenance is essential to prolong the life of an industrial robot.
This involves routine inspections, lubrication of moving parts, and updating software to ensure optimal performance.
Integration with Other Systems
Industrial robots often work alongside other machinery and systems.
Ensuring seamless integration with production lines, conveyor systems, and quality control mechanisms is crucial for maximizing efficiency.
Conclusion
The industrial robot assembly process is a meticulous and multi-step endeavor.
Understanding each component and its role in the overall system is vital for creating robots that can meet the high demands of modern manufacturing.
With the right approach, these mechanical marvels can significantly enhance productivity, precision, and safety in various industrial applications.
資料ダウンロード
QCD調達購買管理クラウド「newji」は、調達購買部門で必要なQCD管理全てを備えた、現場特化型兼クラウド型の今世紀最高の購買管理システムとなります。
ユーザー登録
調達購買業務の効率化だけでなく、システムを導入することで、コスト削減や製品・資材のステータス可視化のほか、属人化していた購買情報の共有化による内部不正防止や統制にも役立ちます。
NEWJI DX
製造業に特化したデジタルトランスフォーメーション(DX)の実現を目指す請負開発型のコンサルティングサービスです。AI、iPaaS、および先端の技術を駆使して、製造プロセスの効率化、業務効率化、チームワーク強化、コスト削減、品質向上を実現します。このサービスは、製造業の課題を深く理解し、それに対する最適なデジタルソリューションを提供することで、企業が持続的な成長とイノベーションを達成できるようサポートします。
オンライン講座
製造業、主に購買・調達部門にお勤めの方々に向けた情報を配信しております。
新任の方やベテランの方、管理職を対象とした幅広いコンテンツをご用意しております。
お問い合わせ
コストダウンが利益に直結する術だと理解していても、なかなか前に進めることができない状況。そんな時は、newjiのコストダウン自動化機能で大きく利益貢献しよう!
(Β版非公開)