- お役立ち記事
- A framework for purchasing departments to evaluate suppliers’ ability to provide stable supply
A framework for purchasing departments to evaluate suppliers’ ability to provide stable supply
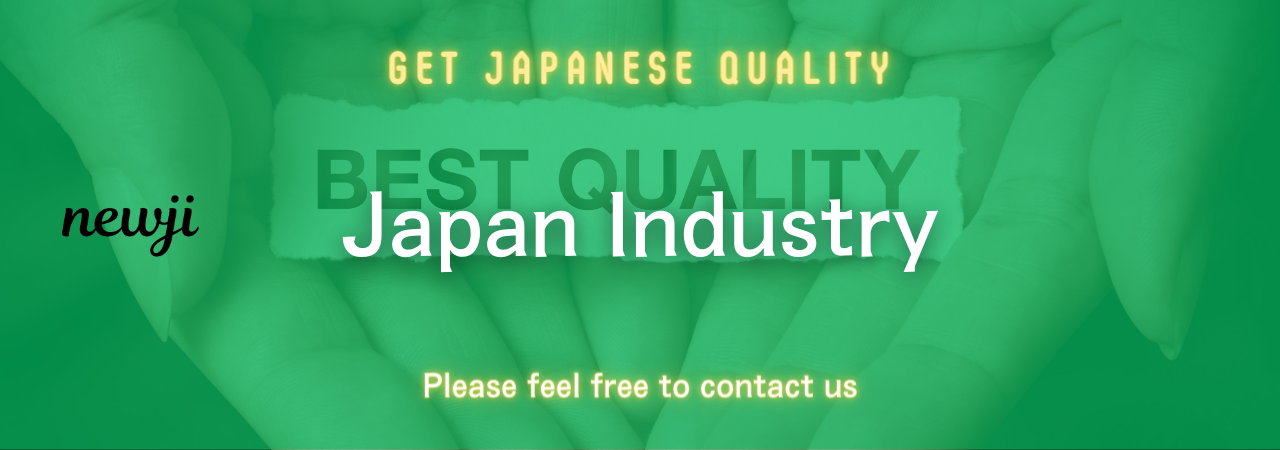
目次
Understanding the Importance of Supply Stability
Every purchasing department in any organization understands the critical role that suppliers play in ensuring smooth business operations.
One of the most essential aspects of a supplier’s reliability is their ability to provide a steady supply of products or services consistently.
This stability ensures that businesses can meet their own production timelines and satisfy customer demands without interruptions.
A stable supply chain minimizes risks associated with delays and shortages, which can otherwise have cascading effects on the entire business.
Key Criteria for Evaluating Supplier Stability
To evaluate a supplier’s ability to provide a stable supply, purchasing departments need to adopt a structured approach.
Here are some crucial criteria to consider:
1. Historical Performance
Examining a supplier’s past performance is one of the most reliable ways to predict their future behavior.
Review the supplier’s delivery timelines, quality of goods or services delivered, and their financial stability over a set period.
A consistent track record is often a strong indicator of future reliability.
2. Production Capacity
Understanding the supplier’s production capacity is crucial.
It includes the volume of goods they can produce within specific timeframes and their flexibility to scale up or down based on demand.
Suppliers with robust production capabilities are more likely to handle fluctuations in demand without compromising on delivery.
3. Supply Chain Diversification
Evaluate whether your supplier relies on a single source for their materials or if they have multiple sources.
Diversified supply chains are generally more resilient to disruptions, as they are not dependent on a single point of failure.
Suppliers with diversification strategies are usually better positioned to maintain stable supply.
4. Financial Health
A supplier’s financial stability is a cornerstone of their ability to provide a stable supply.
Assess their financial statements for liquidity, profitability, and debt levels.
Financially healthy suppliers are more likely to invest in quality control, efficient logistics, and other areas critical for maintaining stability.
5. Relationship Management
The strength of the relationship between you and your supplier can greatly impact the stability of the supply chain.
Suppliers who prioritize strong partnerships tend to be more communicative and proactive in managing potential disruptions.
Regular communication and healthy relationships facilitate smoother problem-solving and negotiation processes.
Developing a Supplier Evaluation Framework
Creating a standardized framework for evaluating suppliers can greatly enhance the purchasing department’s ability to maintain stable supply chains.
Here’s a step-by-step guide to building an effective evaluation framework:
1. Define Evaluation Parameters
Start by clearly outlining the parameters you will use to evaluate suppliers.
These should align with the criteria mentioned above, such as historical performance, production capacity, supply chain diversification, financial health, and relationship management.
2. Develop a Scoring System
Once the parameters are defined, develop a scoring system.
Assign weights to each parameter according to its importance to your specific business needs.
For example, if your business is highly sensitive to delivery schedules, you might assign more weight to historical performance scores related to timely delivery.
3. Gather Data and Perform Analysis
Collect data on each supplier based on the defined parameters.
The data could come from internal records, supplier surveys, third-party reports, or financial analysis.
Once data collection is complete, apply your scoring system to evaluate each supplier objectively.
4. Review and Compare
Analyze the data to compare the stability potential across different suppliers.
This should give your purchasing team a clear perspective on which suppliers are most likely to offer a stable supply.
Strategies to Enhance Supplier Stability
Once evaluation is complete, consider implementing the following strategies to enhance supplier stability further:
1. Foster Strong Relationships
Maintain open and regular communication with your suppliers.
Building good rapport can often lead to preferential treatment and quicker resolutions to any disruption.
2. Implement Collaborative Planning
Engage in collaborative planning with your suppliers.
Shared forecasts and aligned production or delivery schedules can reduce misunderstandings and build trust.
3. Encourage Supplier Development Programs
Invest in supplier development programs to help your suppliers improve their processes and capacity.
This can also mean providing training or sharing technology that enhances their ability to supply consistently.
4. Monitor Continuously
Regular monitoring of your suppliers post-evaluation is crucial.
Establishing key performance indicators (KPIs) aligned with stability will help in ongoing monitoring
Benefits of a Structured Evaluation Framework
Adopting a structured framework helps purchasing departments in various ways:
– Enhanced decision-making capabilities based on detailed analysis.
– Reduced risk of disruptions due to a clear understanding of supplier capacities.
– Improved supplier relations and streamlined communication processes.
– Potential for cost savings by avoiding emergency procurements.
Conclusion
Building a resilient supply chain starts with selecting the right suppliers who are capable of maintaining a stable supply.
A well-designed evaluation framework serves as an effective tool to assess and ensure this stability.
By focusing on key criteria and continuously working with suppliers, purchasing departments can safeguard their organization against the uncertainties and risks inherent in supply chain operations.
Develop your evaluation framework today to secure a more reliable supply chain tomorrow.
資料ダウンロード
QCD調達購買管理クラウド「newji」は、調達購買部門で必要なQCD管理全てを備えた、現場特化型兼クラウド型の今世紀最高の購買管理システムとなります。
ユーザー登録
調達購買業務の効率化だけでなく、システムを導入することで、コスト削減や製品・資材のステータス可視化のほか、属人化していた購買情報の共有化による内部不正防止や統制にも役立ちます。
NEWJI DX
製造業に特化したデジタルトランスフォーメーション(DX)の実現を目指す請負開発型のコンサルティングサービスです。AI、iPaaS、および先端の技術を駆使して、製造プロセスの効率化、業務効率化、チームワーク強化、コスト削減、品質向上を実現します。このサービスは、製造業の課題を深く理解し、それに対する最適なデジタルソリューションを提供することで、企業が持続的な成長とイノベーションを達成できるようサポートします。
オンライン講座
製造業、主に購買・調達部門にお勤めの方々に向けた情報を配信しております。
新任の方やベテランの方、管理職を対象とした幅広いコンテンツをご用意しております。
お問い合わせ
コストダウンが利益に直結する術だと理解していても、なかなか前に進めることができない状況。そんな時は、newjiのコストダウン自動化機能で大きく利益貢献しよう!
(Β版非公開)