- お役立ち記事
- A must-read for production engineers in the oil filter manufacturing industry for forging press machines! Technology for high efficiency and durability
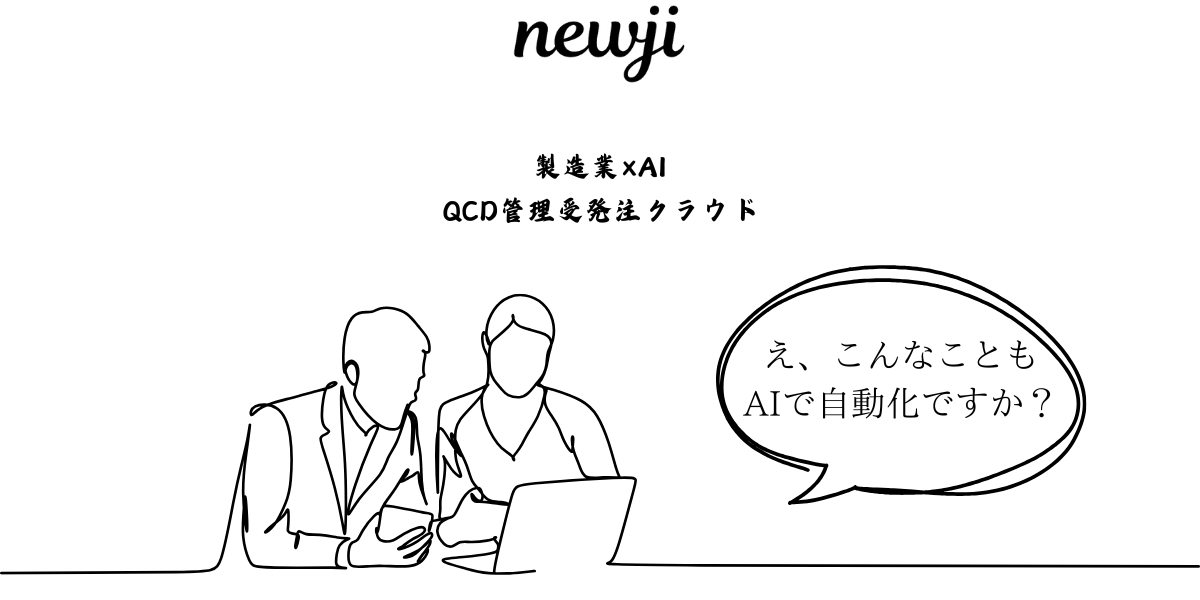
A must-read for production engineers in the oil filter manufacturing industry for forging press machines! Technology for high efficiency and durability
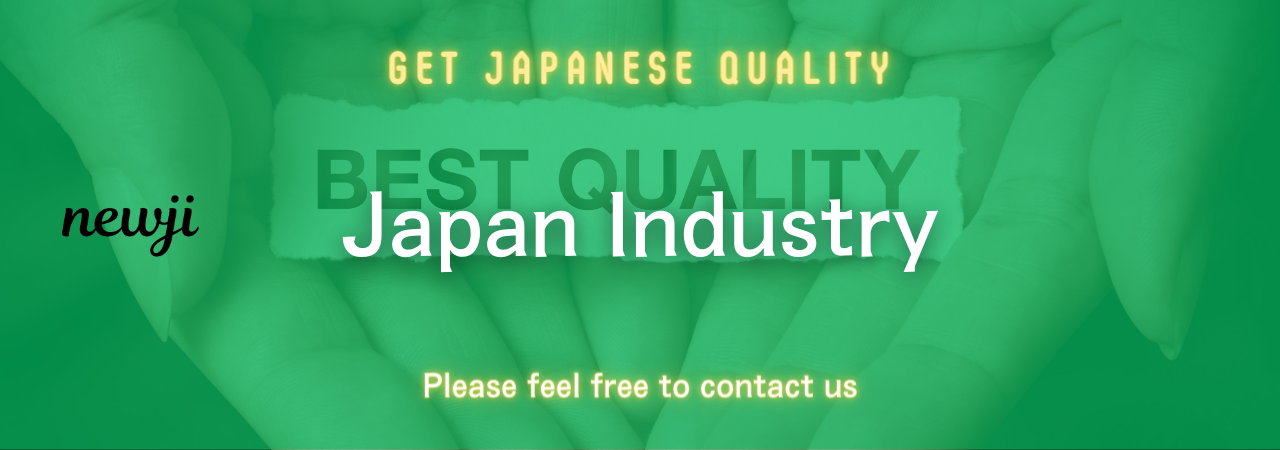
目次
Introduction to Oil Filter Manufacturing
The production of oil filters is a crucial process that ensures vehicles and machinery operate smoothly by maintaining clean engine oil.
Oil filter manufacturing involves several intricate steps, including material selection, fabrication, and quality testing.
Production engineers in this industry must focus on efficiency and durability to produce high-performance filters that meet industrial standards.
Oil filters are vital components that trap dirt and debris that could damage engines, hence the emphasis on effective manufacturing techniques is essential to the production engineers who lead these processes.
Understanding Forging Press Machines
Forging press machines are pivotal in creating robust and durable components used in oil filter manufacturing.
These machines apply pressure to metal materials, shaping them into desired specifications through force and heat.
Forging increases the strength of materials, making parts more resistant to wear and tear, which is critical for the durability of oil filters.
Incorporating forging press technology not only enhances the product’s lifespan but also improves performance, ensuring that manufacturing processes remain competitive and advanced.
Technological Advancements for High Efficiency
Modern oil filter manufacturing has seen significant advancements in technology, aimed at improving efficiency and output quality.
One such innovation is the integration of automation in forging press operations.
Automated systems streamline the production process by reducing manual intervention, improving consistency, and minimizing errors.
Moreover, advanced software solutions now enable engineers to better simulate and analyze the forging process, optimizing parameters for ideal conditions.
These systems can predict outcomes, adjust variables, and enhance precision, ultimately leading to faster cycle times and reduced energy consumption.
Smart Manufacturing Practices
Smart manufacturing practices, including the use of Internet of Things (IoT) and machine learning algorithms, have started to permeate the oil filter production industry.
These technologies offer real-time monitoring and predictive maintenance, which significantly reduces downtime.
IoT devices can collect data from machines during operation, providing insights into the health and efficiency of the equipment.
Engineers can use this data to make informed decisions, anticipate equipment failures, and schedule maintenance proactively.
Machine learning models further augment these capabilities by analyzing patterns and suggesting process improvements that increase efficiency and output.
The Role of Materials in Durability
The choice of materials plays an indispensable role in the durability and performance of oil filters.
Production engineers must select materials that withstand high pressure and temperatures encountered during pressing operations.
Traditionally, steel and aluminum alloys are popular choices due to their resilience and malleability.
However, with the advent of advanced materials science, composites and specialized alloys have become increasingly popular.
These materials not only enhance the strength and durability of filters but also contribute to lighter and more efficient designs.
Such designs are invaluable in creating filters that meet both environmental standards and customer demands for sustainable products.
Surface Treatments and Coatings
Applying suitable surface treatments and coatings is essential to further extend the lifespan and functionality of oil filters.
Coatings protect the filters from corrosion, high temperatures, and abrasive materials encountered during use.
Production engineers need to consider techniques such as anodizing, plating, and sputtering to enhance the filters’ properties.
These techniques help in reducing friction and wear on the moving parts within the oil filter, promoting smoother operation and extended service life.
Selecting the optimal coating solutions is a strategic decision that influences both the cost and performance efficiency of the final product.
Challenges and Solutions in Oil Filter Manufacturing
Manufacturing oil filters comes with its own set of challenges that engineers must skillfully navigate.
Some key issues include maintaining quality consistency, managing production costs, and meeting stringent regulatory standards.
Quality consistency can be addressed through robust quality control protocols and regular audits.
Engineers should invest in automated inspection systems to ensure each product meets the set standards before dispatch.
Managing production costs necessitates a strategic approach, often achievable through process optimization and waste reduction.
Implementing lean manufacturing techniques allows companies to minimize excess while maximizing productivity.
Finally, staying compliant with regulations requires a thorough understanding of industry standards and a proactive approach to meeting or exceeding these rules.
Future Trends in the Industry
Looking to the future, the oil filter manufacturing industry continues to evolve with new trends on the horizon.
One such trend is the focus on sustainable production practices.
This includes using recycled materials, reducing carbon footprints, and improving energy efficiency throughout the manufacturing process.
Another emerging trend is the customization of oil filters to suit specific client needs.
Advancements in manufacturing technologies allow for bespoke solutions that meet unique performance criteria.
By embracing these trends, production engineers can position themselves as innovators in the field, driving the industry toward a more efficient and sustainable future.
In conclusion, the intersection of technology, material science, and engineering practices plays a critical role in the oil filter manufacturing industry.
By focusing on enhancing efficiency and durability, production engineers can ensure their products remain competitive in an ever-evolving market.
As the industry progresses, embracing technological advancements and innovative manufacturing solutions will continue to be key factors in achieving excellence.
資料ダウンロード
QCD調達購買管理クラウド「newji」は、調達購買部門で必要なQCD管理全てを備えた、現場特化型兼クラウド型の今世紀最高の購買管理システムとなります。
ユーザー登録
調達購買業務の効率化だけでなく、システムを導入することで、コスト削減や製品・資材のステータス可視化のほか、属人化していた購買情報の共有化による内部不正防止や統制にも役立ちます。
NEWJI DX
製造業に特化したデジタルトランスフォーメーション(DX)の実現を目指す請負開発型のコンサルティングサービスです。AI、iPaaS、および先端の技術を駆使して、製造プロセスの効率化、業務効率化、チームワーク強化、コスト削減、品質向上を実現します。このサービスは、製造業の課題を深く理解し、それに対する最適なデジタルソリューションを提供することで、企業が持続的な成長とイノベーションを達成できるようサポートします。
オンライン講座
製造業、主に購買・調達部門にお勤めの方々に向けた情報を配信しております。
新任の方やベテランの方、管理職を対象とした幅広いコンテンツをご用意しております。
お問い合わせ
コストダウンが利益に直結する術だと理解していても、なかなか前に進めることができない状況。そんな時は、newjiのコストダウン自動化機能で大きく利益貢献しよう!
(Β版非公開)