- お役立ち記事
- A Must-Read for Production Management Departments! New Strategies for Process Efficiency Using IE Methods
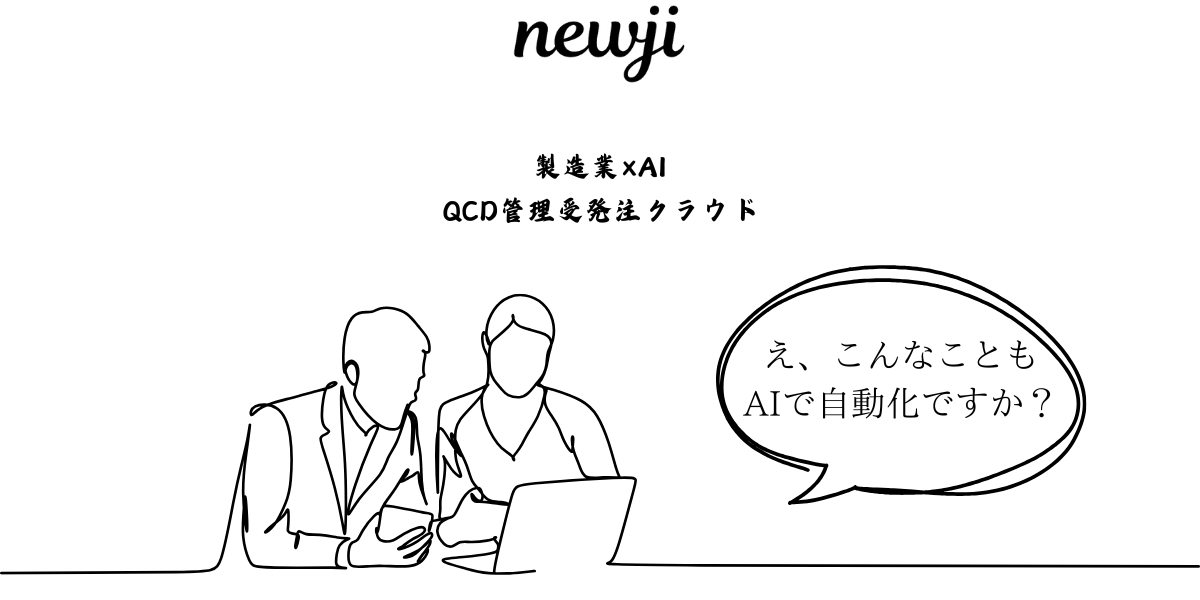
A Must-Read for Production Management Departments! New Strategies for Process Efficiency Using IE Methods
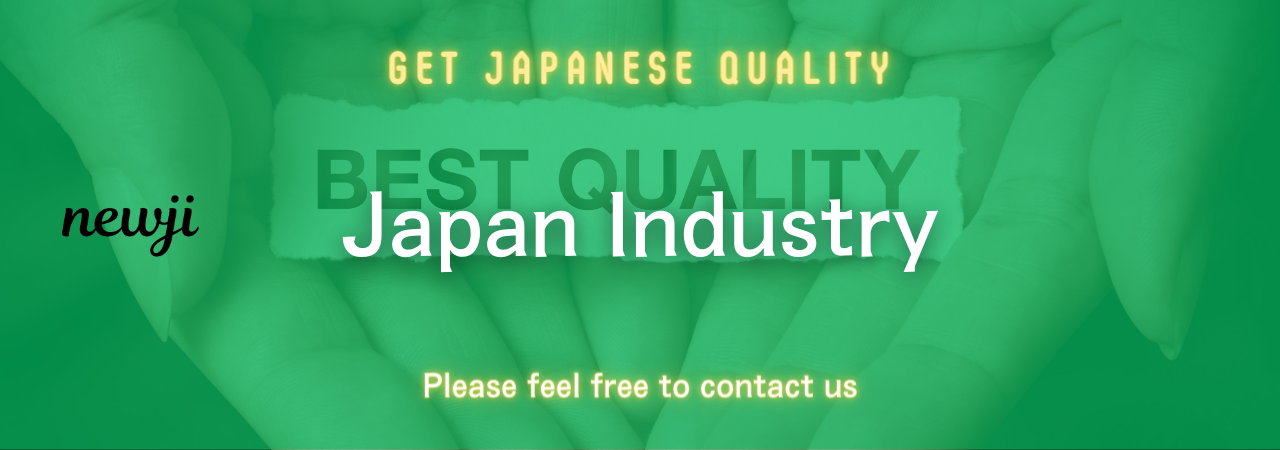
目次
Introduction to IE Methods
Industrial Engineering (IE) methods are systematic approaches used to enhance and optimize processes in production management.
These methods focus on improving efficiency, reducing waste, and increasing productivity, making them essential tools for manufacturing and production management departments.
In today’s competitive business environment, applying IE methods can lead to significant improvements in operational performance.
From time studies and motion analysis to ergonomic and safety enhancements, understanding and implementing these techniques is crucial for any organization aiming for excellence in production management.
Understanding Process Efficiency
Process efficiency is the ability to produce goods or deliver services using the least amount of resources without compromising quality.
It involves identifying and eliminating non-value-adding activities, thereby streamlining operations and maximizing throughput.
Achieving high levels of process efficiency means that a company can produce more with less, resulting in cost savings and increased profitability.
IE methods play a pivotal role in enhancing process efficiency by providing tools and techniques for analyzing and optimizing workflows.
The Importance of Process Efficiency
Process efficiency is a key driver of success in production management.
Efficient processes yield numerous benefits, including lower production costs, shorter lead times, higher product quality, and improved customer satisfaction.
Moreover, efficient processes better position companies to respond quickly to market demands and changes, giving them a competitive edge.
With rising global competition and customer expectations, improving process efficiency has never been more critical for businesses striving to succeed in today’s marketplace.
Implementing IE Methods for Process Improvement
The implementation of IE methods involves several steps that can significantly enhance process efficiency.
Step 1: Conducting a Process Analysis
The first step is conducting a thorough analysis of the current processes.
This involves mapping out every step involved in the production or service delivery chain.
By understanding the entire workflow, managers can identify bottlenecks, redundancies, and non-value-adding tasks.
Various tools, such as process flowcharts or value stream mapping, can facilitate this analysis, providing a clear visual representation of workflows.
Step 2: Identifying Improvement Opportunities
After analyzing the existing processes, the next step is to identify areas where improvements can be made.
This could involve eliminating redundant steps, redesigning workflows, or introducing automation technologies.
IE methods encourage innovative thinking and problem-solving to develop solutions that will enhance productivity and efficiency.
Step 3: Implementing Changes
Once improvement opportunities are identified, the next phase is implementing these changes.
It is essential to communicate these changes clearly to all employees involved.
Ensuring that staff are adequately trained on new processes and technologies is crucial for a smooth transition.
Moreover, engaging employees in the change process boosts morale and encourages buy-in, which is vital for the success of any process improvement initiative.
Step 4: Monitoring and Continual Improvement
Process improvement is not a one-time event but rather a continuous journey.
After implementing changes, it is important to regularly monitor the performance of the optimized processes.
Use key performance indicators (KPIs) to track progress and identify any further areas for improvement.
Regular feedback loops and open communication channels ensure ongoing refinement and development of processes over time.
Examples of IE Methods in Practice
There are several IE methods that production management departments can leverage for process efficiency.
Here are a few examples:
Time Study and Motion Analysis
Time studies and motion analysis are powerful techniques for improving efficiency.
By analyzing how tasks are performed and determining the optimal way to complete them, managers can eliminate wasted time and unnecessary motion.
This leads to faster production cycles and improved worker productivity.
Lean Manufacturing
Lean manufacturing focuses on reducing waste and optimizing processes.
It emphasizes value creation for the customer and encompasses principles such as just-in-time production, continuous improvement (Kaizen), and waste minimization.
By implementing lean principles, companies can achieve significant improvements in process efficiency and customer satisfaction.
Six Sigma
Six Sigma is a data-driven approach to improving quality and efficiency.
It uses statistical analysis to identify defects and variations in processes and seeks to eliminate them.
Organizations that implement Six Sigma methodologies often see dramatic improvements in process consistency, product quality, and overall efficiency.
Ergonomics and Safety Enhancements
Optimizing efficiency is not only about processes but also involves ensuring the well-being of workers.
Ergonomic improvements can lead to better workstation design and reduced physical strain on employees, enhancing productivity and reducing workplace injuries.
A focus on safety not only improves efficiency but also creates a more conducive working environment.
Conclusion
Adopting IE methods for process efficiency is essential for production management departments aiming to excel in today’s competitive marketplace.
By analyzing and optimizing workflows, identifying areas for improvement, and leveraging tools like time studies, lean manufacturing, and Six Sigma, companies can achieve significant gains in efficiency and productivity.
Implementing these strategies requires a commitment to continuous improvement and employee engagement, ensuring long-term success and a sustainable competitive advantage.
By embracing IE methods, production management teams can drive better business outcomes and meet the ever-evolving demands of the market.
資料ダウンロード
QCD調達購買管理クラウド「newji」は、調達購買部門で必要なQCD管理全てを備えた、現場特化型兼クラウド型の今世紀最高の購買管理システムとなります。
ユーザー登録
調達購買業務の効率化だけでなく、システムを導入することで、コスト削減や製品・資材のステータス可視化のほか、属人化していた購買情報の共有化による内部不正防止や統制にも役立ちます。
NEWJI DX
製造業に特化したデジタルトランスフォーメーション(DX)の実現を目指す請負開発型のコンサルティングサービスです。AI、iPaaS、および先端の技術を駆使して、製造プロセスの効率化、業務効率化、チームワーク強化、コスト削減、品質向上を実現します。このサービスは、製造業の課題を深く理解し、それに対する最適なデジタルソリューションを提供することで、企業が持続的な成長とイノベーションを達成できるようサポートします。
オンライン講座
製造業、主に購買・調達部門にお勤めの方々に向けた情報を配信しております。
新任の方やベテランの方、管理職を対象とした幅広いコンテンツをご用意しております。
お問い合わせ
コストダウンが利益に直結する術だと理解していても、なかなか前に進めることができない状況。そんな時は、newjiのコストダウン自動化機能で大きく利益貢献しよう!
(Β版非公開)