- お役立ち記事
- A must-see for new employees in the production technology department of the metal processing industry! Basics of deep draw molding and processing methods for highly difficult shapes
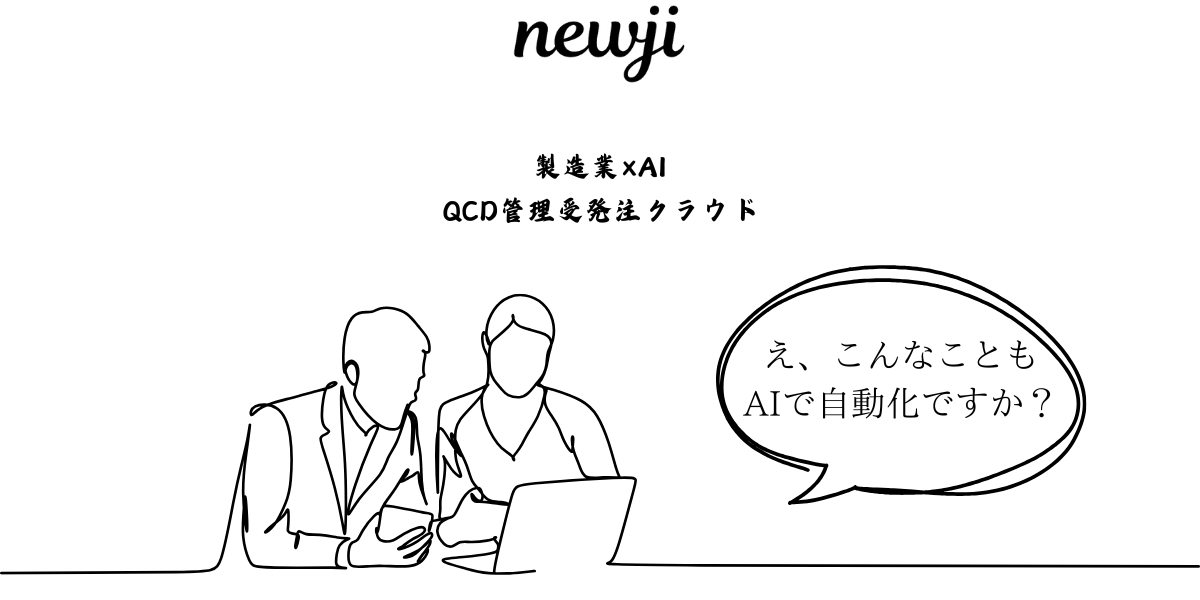
A must-see for new employees in the production technology department of the metal processing industry! Basics of deep draw molding and processing methods for highly difficult shapes
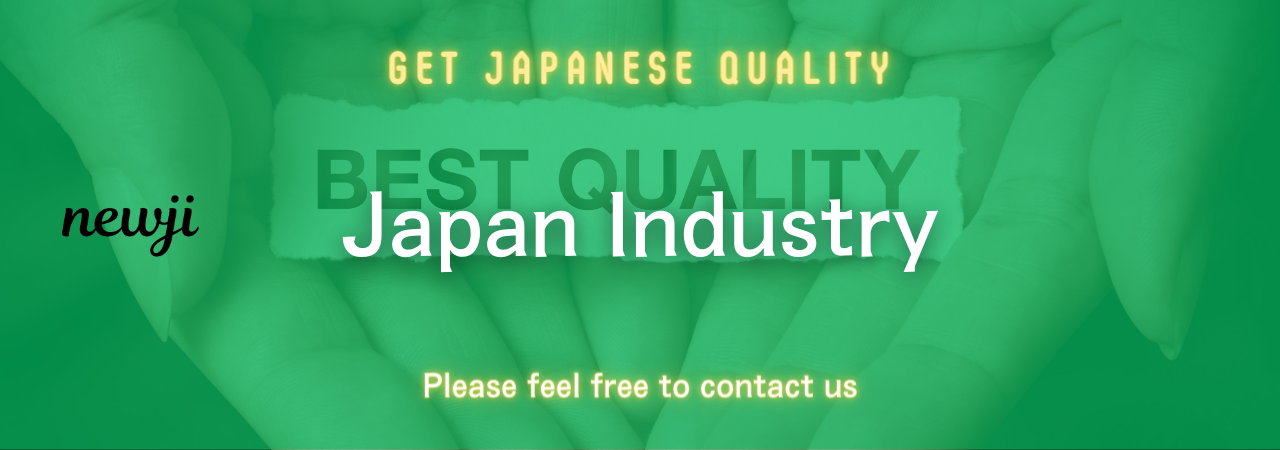
目次
Understanding Deep Draw Molding
Deep draw molding is a crucial process in the metal processing industry, especially for new employees in the production technology department.
Understanding its fundamentals will give you a significant advantage as you start your career.
But what exactly is deep draw molding?
Deep draw molding is a sheet metal forming process in which a flat sheet of metal is gradually formed into a three-dimensional shape by mechanical action.
This technique is extensively used to create metal parts, ranging from simple shapes like cups and cylindrical containers to more complex shapes such as automobile components and kitchen appliances.
Why is Deep Draw Molding Important?
The importance of deep draw molding lies in its ability to produce strong, seamless metal products with minimal waste.
The process is highly efficient and can significantly reduce the need for welding and assembly, resulting in products that are more robust and durable.
This efficiency also translates into cost savings, making it an attractive option for manufacturers looking to maximize their output while minimizing expenses.
Moreover, deep draw molding is versatile and can accommodate a wide range of materials, including aluminum, steel, copper, and brass.
This adaptability makes it suitable for various industries, increasing the demand for skilled professionals in this field.
Key Considerations in Deep Draw Molding
To ensure successful deep draw molding, there are several key factors that new employees must consider.
Material Selection
The choice of material is critical in deep draw molding.
It’s essential to select a material that offers the right balance of ductility and strength.
Ductility refers to a material’s ability to deform without rupturing, which is crucial during the molding process.
Simultaneously, strength ensures the finished product maintains its integrity under stress.
Common materials used in deep draw molding include aluminum due to its lightweight and corrosion-resistant properties, and stainless steel for its durability and aesthetic appeal.
Design and Geometry
Understanding the complexity of the design and geometry of the part you’re planning to produce is another crucial aspect.
While simple shapes such as cylinders are easier to manufacture, more intricate designs might require advanced tooling and techniques.
Factors such as the draw ratio, which is the relationship between the diameter and depth of the draw, must be carefully calculated to avoid material failure.
Tooling and Equipment
Deep draw molding relies heavily on precise tooling and state-of-the-art equipment.
The tooling setup includes punches, dies, and blank holders, all of which must be meticulously designed to ensure optimal performance.
The choice of equipment, from mechanical presses to hydraulic presses, can affect the quality and efficiency of the molding process.
Processing Methods for Highly Difficult Shapes
Working with highly difficult shapes in deep draw molding requires advanced processing methods.
As a new employee, understanding these methods will allow you to tackle complex challenges effectively.
Progressive Die Stamping
Progressive die stamping is a sophisticated method used for producing complex shapes.
It involves multiple stages where the metal is formed, punched, and cut as it moves through a series of stations.
Each station performs a different operation until the final shape is achieved.
This method is ideal for high-volume production of intricate parts and helps improve efficiency and speed.
Hydroforming
Hydroforming is another technique used to create complex shapes, particularly those with non-axisymmetric features.
It uses a high-pressure hydraulic fluid to press the metal into the desired shape.
Hydroforming is known for its ability to produce lightweight yet strong components, making it popular for automotive and aerospace applications.
Multi-Slide Stamping
Multi-slide stamping employs multiple tools that approach the metal from different angles.
This technique is particularly useful for creating parts with intricate geometries that require numerous bends and angles.
It offers precise control over the forming process and is ideal for manufacturing parts with tight tolerances.
Challenges and Solutions in Deep Draw Molding
While deep draw molding offers numerous advantages, it also presents challenges that new employees should be prepared to address.
Wrinkling and Tearing
Wrinkling occurs when the metal is compressed in one area more than another, leading to unwanted folds.
To prevent this, a blank holder can be used to apply the appropriate pressure across the metal surface.
Tearing, on the other hand, happens when the material exceeds its tensile strength.
Using a material with higher ductility or adjusting the draw ratio can mitigate this issue.
Springback
Springback refers to the tendency of metal to return to its original shape after forming.
This can result in inaccuracies in the final product.
Compensating for springback with precise overbending during the design phase can help negate this effect.
Optimization Through Simulation
Using computer-aided design (CAD) and finite element analysis (FEA) software can greatly enhance the deep draw molding process.
These tools allow for the simulation of the molding process, enabling you to predict and rectify issues before actual production.
This proactive approach can lead to better product quality and reduced waste.
Conclusion
Deep draw molding is an essential process in the metal processing industry, and understanding its intricacies is vital for any new employee in the production technology department.
By mastering the basics of deep draw molding and familiarizing yourself with advanced processing methods, you can contribute to creating high-quality, durable products.
As you navigate the challenges of deep draw molding, remember that continuous learning and adaptation are key to success in this dynamic field.
資料ダウンロード
QCD調達購買管理クラウド「newji」は、調達購買部門で必要なQCD管理全てを備えた、現場特化型兼クラウド型の今世紀最高の購買管理システムとなります。
ユーザー登録
調達購買業務の効率化だけでなく、システムを導入することで、コスト削減や製品・資材のステータス可視化のほか、属人化していた購買情報の共有化による内部不正防止や統制にも役立ちます。
NEWJI DX
製造業に特化したデジタルトランスフォーメーション(DX)の実現を目指す請負開発型のコンサルティングサービスです。AI、iPaaS、および先端の技術を駆使して、製造プロセスの効率化、業務効率化、チームワーク強化、コスト削減、品質向上を実現します。このサービスは、製造業の課題を深く理解し、それに対する最適なデジタルソリューションを提供することで、企業が持続的な成長とイノベーションを達成できるようサポートします。
オンライン講座
製造業、主に購買・調達部門にお勤めの方々に向けた情報を配信しております。
新任の方やベテランの方、管理職を対象とした幅広いコンテンツをご用意しております。
お問い合わせ
コストダウンが利益に直結する術だと理解していても、なかなか前に進めることができない状況。そんな時は、newjiのコストダウン自動化機能で大きく利益貢献しよう!
(Β版非公開)