- お役立ち記事
- A must-see for production engineers in the coolant nozzle manufacturing industry for precision cutting machines! Latest technology that achieves both cooling effect and wear resistance
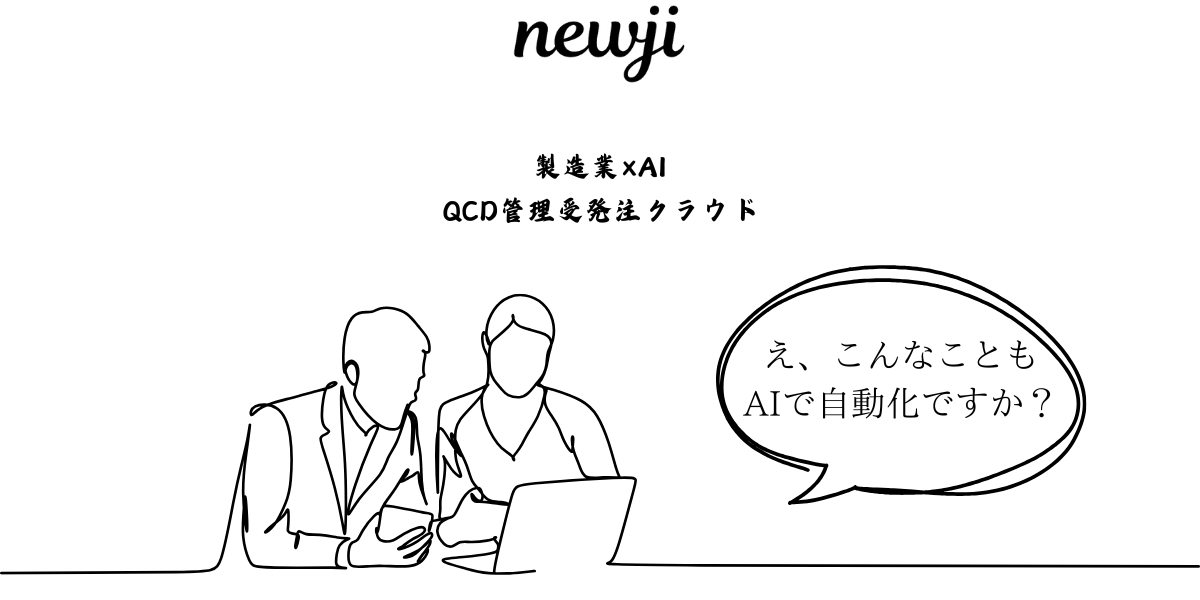
A must-see for production engineers in the coolant nozzle manufacturing industry for precision cutting machines! Latest technology that achieves both cooling effect and wear resistance
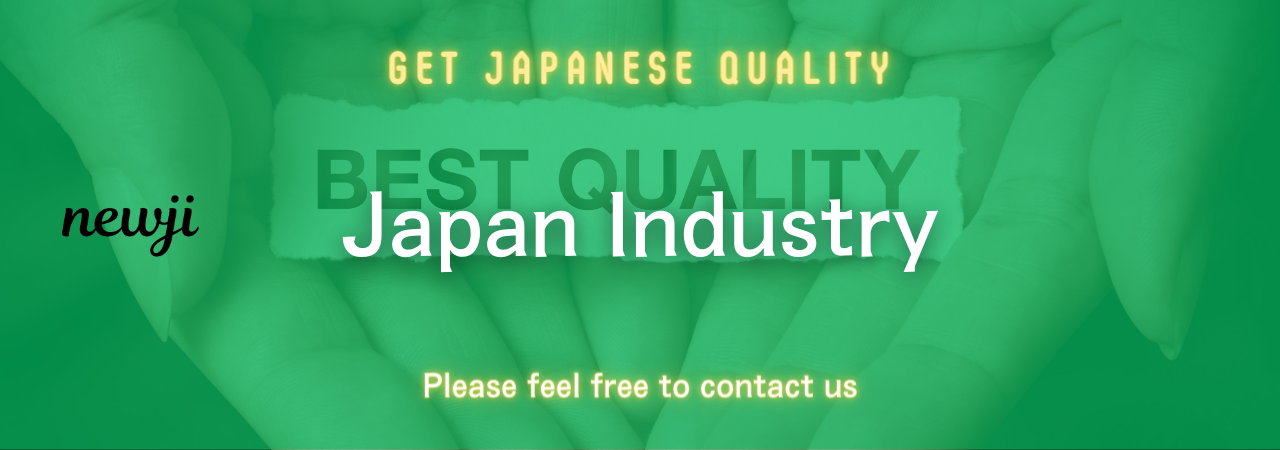
目次
Introduction to Coolant Nozzles for Precision Cutting Machines
In the world of manufacturing, precision cutting machines play a pivotal role in producing high-quality components.
To ensure optimal performance, these machines rely heavily on coolant nozzles.
Coolant nozzles are essential in regulating the temperature during cutting processes, thereby enhancing the machine’s efficiency and prolonging its lifespan.
The Importance of Cooling Effect
The primary purpose of a coolant nozzle is to facilitate the removal of heat generated during cutting operations.
Excessive heat can lead to a range of problems, including tool wear, thermal expansion, and even catastrophic failure of cutting tools.
By providing a steady stream of coolant, these nozzles help maintain an optimal temperature, thus ensuring the integrity of both the machine and the workpiece.
Moreover, an effective cooling system reduces the likelihood of thermal deformation.
This is crucial for precision applications, where even the slightest distortion can lead to inaccuracies.
Manufacturers who focus on achieving a superior cooling effect can, therefore, deliver components with tight tolerances and superior finish quality.
Advancements in Wear Resistance Technology
Besides cooling, another critical factor that impacts the performance of coolant nozzles is wear resistance.
Nozzles are subjected to high pressure and abrasive environments, which can lead to accelerated wear and tear.
Recent technological advancements have significantly improved the wear resistance of these nozzles.
Using durable materials like ceramics and advanced composites, manufacturers are now producing nozzles that can withstand harsh operating conditions for extended periods.
Moreover, innovative coating technologies have emerged, offering an additional layer of protection against wear.
These advancements not only decrease the frequency of nozzle replacements but also contribute to the overall reliability and efficiency of precision cutting machines.
Materials Used in Coolant Nozzles
The choice of material for coolant nozzles plays a significant role in determining their effectiveness and longevity.
Traditional nozzles made from metals such as steel and brass were prone to corrosion and wear over time.
However, modern nozzles incorporate materials that offer better performance under demanding conditions.
Ceramics, for example, are highly resistant to wear and corrosion, making them an ideal choice for heavy-duty applications.
Other composite materials are engineered to enhance the durability and thermal properties of nozzles, striking a balance between cost and performance.
Additionally, the use of advanced polymers in nozzle construction has gained popularity, providing excellent wear resistance while being lightweight and cost-effective.
Design Innovations for Enhanced Performance
The design of coolant nozzles is another area where significant improvements have been made.
Innovative designs focus on optimizing the flow and distribution of coolant to cover the cutting zone effectively.
This ensures that heat is dissipated efficiently and uniformly, preventing hot spots that could compromise the quality of the cut.
Some designs now incorporate adjustable features that allow operators to customize the direction and flow rate of the coolant.
This adaptability is particularly beneficial in multi-purpose machines that handle a variety of materials and thicknesses.
Furthermore, the integration of smart technology in nozzle design is becoming more prevalent.
These smart nozzles can monitor parameters such as flow rate and temperature in real-time, providing engineers with valuable data to fine-tune the cutting process further.
Environmental and Cost Considerations
While technology advancements have improved the functionality of coolant nozzles, manufacturers also consider environmental and cost factors in their designs.
Reducing coolant waste and recycling are now integral parts of sustainable manufacturing practices.
Modern coolant nozzles are designed to minimize over-spray and splashing, which helps in reducing coolant consumption and waste.
Efficient designs ensure that more coolant reaches the cutting zone, decreasing the need for additional resources.
From a cost perspective, the use of durable materials and coatings extends the life of nozzles, reducing the need for frequent replacements and minimizing downtime.
This not only saves money but also contributes to a more seamless production process.
Conclusion
In the field of precision cutting machines, the importance of coolant nozzles cannot be overstated.
With the latest technology, these nozzles achieve an exceptional cooling effect while exhibiting enhanced wear resistance.
By investing in advanced materials, innovative designs, and smart integration, manufacturers can ensure their cutting machines operate efficiently and sustainably.
For production engineers, staying abreast of these technological advancements is crucial.
It not only enhances the quality of their output but also aligns with the global push for more sustainable and cost-effective manufacturing solutions.
Coolant nozzles represent a key area where small changes can lead to significant improvements in production outcomes.
資料ダウンロード
QCD調達購買管理クラウド「newji」は、調達購買部門で必要なQCD管理全てを備えた、現場特化型兼クラウド型の今世紀最高の購買管理システムとなります。
ユーザー登録
調達購買業務の効率化だけでなく、システムを導入することで、コスト削減や製品・資材のステータス可視化のほか、属人化していた購買情報の共有化による内部不正防止や統制にも役立ちます。
NEWJI DX
製造業に特化したデジタルトランスフォーメーション(DX)の実現を目指す請負開発型のコンサルティングサービスです。AI、iPaaS、および先端の技術を駆使して、製造プロセスの効率化、業務効率化、チームワーク強化、コスト削減、品質向上を実現します。このサービスは、製造業の課題を深く理解し、それに対する最適なデジタルソリューションを提供することで、企業が持続的な成長とイノベーションを達成できるようサポートします。
オンライン講座
製造業、主に購買・調達部門にお勤めの方々に向けた情報を配信しております。
新任の方やベテランの方、管理職を対象とした幅広いコンテンツをご用意しております。
お問い合わせ
コストダウンが利益に直結する術だと理解していても、なかなか前に進めることができない状況。そんな時は、newjiのコストダウン自動化機能で大きく利益貢献しよう!
(Β版非公開)