- お役立ち記事
- A must-see for production engineers in the pharmaceutical manufacturing industry! A method to achieve uniform mixing of chemicals using a multi-stage mixer
A must-see for production engineers in the pharmaceutical manufacturing industry! A method to achieve uniform mixing of chemicals using a multi-stage mixer
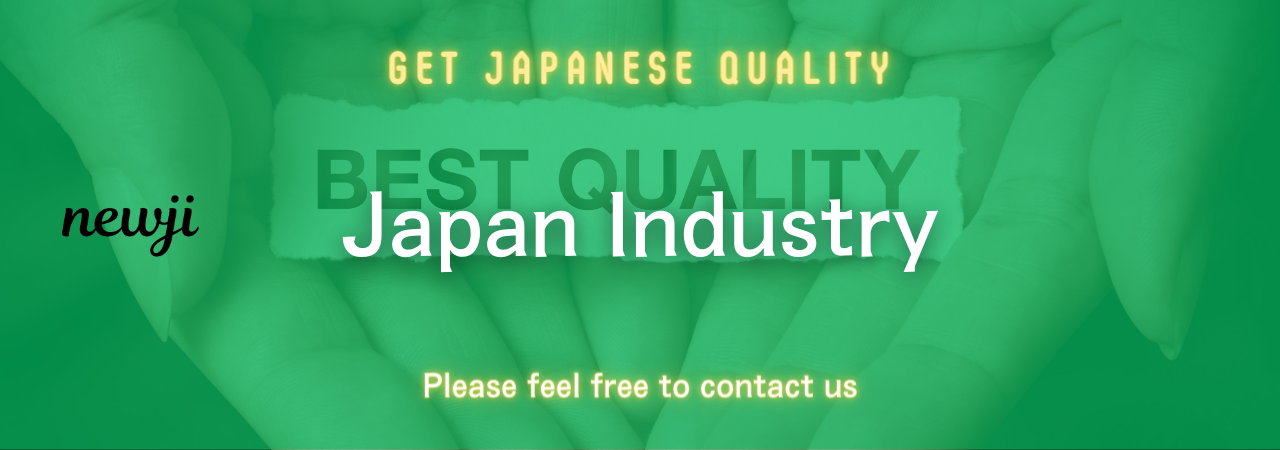
目次
Introduction to Mixing Challenges in Pharmaceutical Manufacturing
In the pharmaceutical manufacturing industry, achieving uniform mixing of chemicals is crucial.
The process entails blending multiple ingredients to ensure consistent quality and efficacy of the final product.
However, mixing is not as simple as tossing all ingredients together.
Different substances have varying properties and behaviors that can pose challenges.
This is where a multi-stage mixer becomes a valuable asset for production engineers.
Understanding the Importance of Uniform Mixing
Uniform mixing is vital in pharmaceuticals because it directly affects product quality and safety.
Whether creating tablets, capsules, or liquid formulations, ingredients must be evenly distributed to guarantee the intended therapeutic effects.
Inconsistent mixing can lead to uneven dosage distribution and compromised product effectiveness.
This can ultimately affect patient health and diminish brand reputation.
Therefore, achieving uniform mixing is a non-negotiable aspect of pharmaceutical production.
Challenges of Traditional Mixing Methods
Traditional mixing methods often struggle with several issues that can hinder uniformity.
These include varying particle sizes, densities, and viscosities of raw materials.
Agglomeration, where particles stick together, and segregation, where components separate, are common problems.
Moreover, mixing processes that require extended times can lead to heat build-up, affecting temperature-sensitive materials.
The Role of Multi-Stage Mixers in the Mixing Process
Multi-stage mixers are designed specifically to address the challenges posed by traditional methods.
They consist of multiple stages, each optimizing different aspects of the mixing process.
These mixers can handle a range of ingredient properties efficiently, ensuring better distribution of particles.
How Multi-Stage Mixers Work
Multi-stage mixers are engineered to perform specific functions at each stage.
Typically, the first stage involves rough handling to reduce particle size and break up agglomerates.
As the material progresses through consecutive stages, finer blending occurs, facilitating smaller-scale distribution.
These stages collectively produce a homogenous mixture, even with complex ingredient compositions.
Benefits of Multi-Stage Mixers
1. **Enhanced Uniformity:** By systematically breaking down materials and blending them across various stages, multi-stage mixers ensure more uniform distribution than single-stage systems.
2. **Improved Efficiency:** Multi-stage mixers process ingredients faster, reducing overall production time and lowering energy consumption.
3. **Reduced Risk of Segregation:** Continuous and controlled blending minimizes the risk of components separating after mixing.
4. **Temperature Control:** Efficient design allows better control over heat generation, safeguarding sensitive materials from thermal degradation.
Practical Application in Pharmaceutical Manufacturing
Incorporating multi-stage mixers can significantly enhance the efficiency and reliability of pharmaceutical production facilities.
Steps to Implement Multi-Stage Mixing Technology
1. **Assessment of Existing Processes:** Production engineers should first evaluate current mixing procedures and identify bottlenecks or inefficiencies.
2. **Customization and Selection:** Choose a multi-stage mixer tailored to the specific properties of the pharmaceutical products being manufactured.
3. **Pilot Testing:** Conduct small-scale trials to assess performance and make necessary adjustments to optimize the setup.
4. **Scalability Considerations:** Once efficacy is confirmed, plan the transition to full-scale operations while ensuring continuity in quality assurance protocols.
5. **Training and Maintenance:** Staff should be trained to operate the new system efficiently, and routine maintenance schedules established to ensure long-term reliability.
Case Study: Success with Multi-Stage Mixers
A pharmaceutical company previously struggled with inconsistent mixing results due to ingredient segregation.
By integrating a multi-stage mixer into their production line, they witnessed a remarkable improvement in uniformity.
The time required for mixing was cut by 30%, and their product consistency improved, reducing the frequency of quality rechecks.
This transition also led to a decrease in energy consumption, offering an added cost-saving benefit.
Conclusion: Embracing Innovation for Better Outcomes
For production engineers in the pharmaceutical industry, harnessing the capabilities of multi-stage mixers is a strategic move.
The methodical approach to blending complex materials not only guarantees uniformity but also bolsters the efficiency and sustainability of production processes.
In a competitive sector where quality and precision are paramount, adopting such innovative technologies can set businesses apart.
By prioritizing effective mixing solutions, pharmaceutical manufacturers can ensure their products meet high standards and continue to build trust with consumers.
資料ダウンロード
QCD調達購買管理クラウド「newji」は、調達購買部門で必要なQCD管理全てを備えた、現場特化型兼クラウド型の今世紀最高の購買管理システムとなります。
ユーザー登録
調達購買業務の効率化だけでなく、システムを導入することで、コスト削減や製品・資材のステータス可視化のほか、属人化していた購買情報の共有化による内部不正防止や統制にも役立ちます。
NEWJI DX
製造業に特化したデジタルトランスフォーメーション(DX)の実現を目指す請負開発型のコンサルティングサービスです。AI、iPaaS、および先端の技術を駆使して、製造プロセスの効率化、業務効率化、チームワーク強化、コスト削減、品質向上を実現します。このサービスは、製造業の課題を深く理解し、それに対する最適なデジタルソリューションを提供することで、企業が持続的な成長とイノベーションを達成できるようサポートします。
オンライン講座
製造業、主に購買・調達部門にお勤めの方々に向けた情報を配信しております。
新任の方やベテランの方、管理職を対象とした幅広いコンテンツをご用意しております。
お問い合わせ
コストダウンが利益に直結する術だと理解していても、なかなか前に進めることができない状況。そんな時は、newjiのコストダウン自動化機能で大きく利益貢献しよう!
(Β版非公開)