- お役立ち記事
- A must-see for project leaders in the auto parts manufacturing industry! How to achieve stable quality using the PPAP method
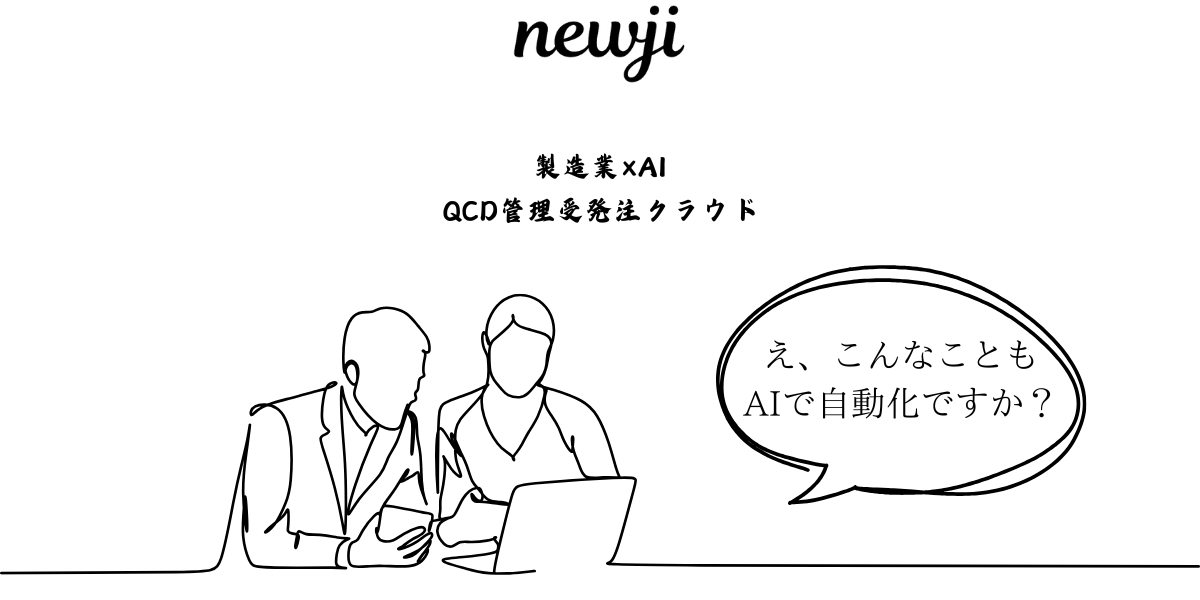
A must-see for project leaders in the auto parts manufacturing industry! How to achieve stable quality using the PPAP method
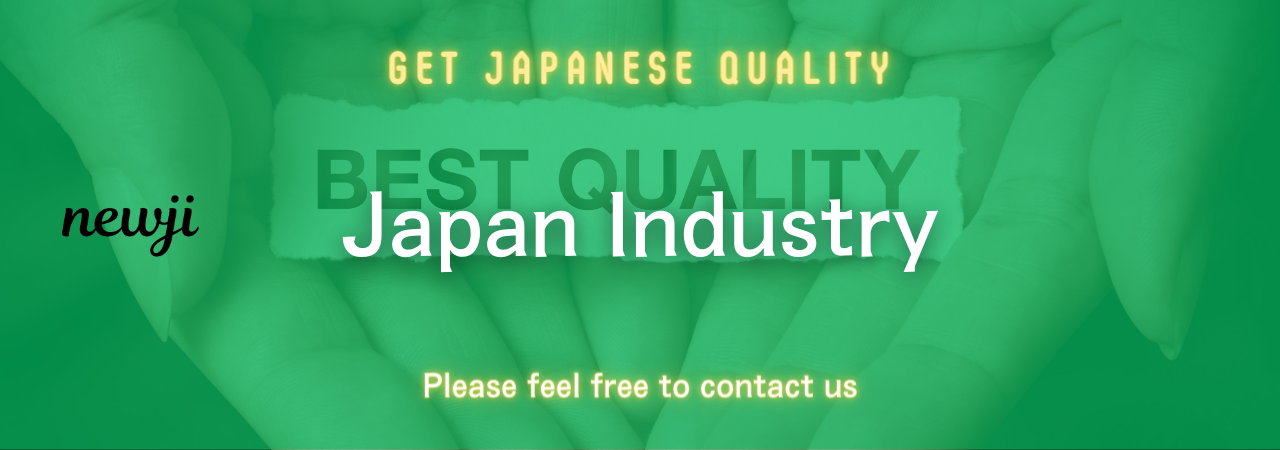
目次
Introduction to PPAP in Auto Parts Manufacturing
The automotive industry is one of the most competitive and quality-driven sectors in the world.
Within this industry, auto parts manufacturers play a critical role in ensuring the safety and reliability of vehicles on the road.
Quality assurance is paramount, and one effective way to achieve it is through the Production Part Approval Process (PPAP).
For project leaders striving for excellence, understanding and implementing the PPAP method is a must.
What is PPAP?
PPAP stands for Production Part Approval Process.
It is a standardized framework used to verify that a supplier’s production process can consistently deliver parts that meet all customer requirements.
Initially developed by the automotive industry, PPAP consists of a series of documents that demonstrate a manufacturing process’s capability and readiness to mass-produce parts or components.
The Importance of PPAP in Auto Parts Manufacturing
In the auto parts manufacturing industry, quality is non-negotiable.
A single substandard part can lead to significant failures, costly recalls, and, at times, serious safety issues.
PPAP helps ensure that suppliers meet the stringent quality requirements before they begin full-scale production.
This process builds confidence between automotive manufacturers and their suppliers, ensuring product reliability and consistency.
The Five Key Elements of PPAP
PPAP involves several key elements used to evaluate the production readiness.
These elements do not only focus on the parts themselves but also assess the processes behind their production.
1. Design Documentation
This element ensures that all design records are in place and meet the customer’s specifications.
It includes engineering drawings, CAD models, and engineering change documents.
2. Process Flow Diagrams
Process flow diagrams illustrate the entire production process from the receiving of raw materials to the finished product.
These diagrams help in evaluating the production cycle efficiency and highlight potential problem areas.
3. Process Failure Mode and Effects Analysis (PFMEA)
PFMEA is a structured approach used to identify and prioritize potential failures in the production process and their impacts.
By addressing these potential failures early, manufacturers can minimize risks and improve process reliability.
4. Control Plans
Control plans outline how to monitor and control critical aspects of the production process.
This ensures that production remains within specification and that any deviations are quickly identified and addressed.
5. Measurement System Analysis (MSA)
MSA evaluates the accuracy and precision of measurement systems used in the production process.
Reliable measurement systems are essential for consistent quality assurance.
Implementing PPAP in Your Manufacturing Process
Successfully implementing the PPAP method requires careful planning and dedication.
Here are steps to guide project leaders:
1. Understand Your Customer’s Requirements
Work closely with your customers to understand their quality requirements and expectations thoroughly.
This will form the foundation of your PPAP documentation and processes.
2. Organize Your Documentation
Gather all necessary documents, including design records, process flow diagrams, and control plans.
Ensure they are comprehensive and up-to-date.
3. Conduct Internal Reviews
Before submitting PPAP documentation to customers, conduct internal reviews.
Engage cross-functional teams to ensure the accuracy and completeness of all information.
4. Continuous Improvement
PPAP is not a one-time activity.
Foster an environment of continuous improvement by regularly reviewing and updating processes.
Address any identified issues proactively to maintain high-quality standards.
Benefits of Adopting PPAP
Utilizing the PPAP method brings numerous benefits to auto parts manufacturers:
1. Enhanced Quality Assurance
PPAP helps in achieving consistent quality, reducing defects, and ensuring products meet customer specifications from the outset.
2. Cost Savings
By preventing quality issues before mass production, manufacturers save on costs associated with recalls, rework, and scrap.
3. Strengthened Customer Confidence
When manufacturers demonstrate commitment to quality through PPAP, it strengthens trust with customers, leading to long-term relationships.
4. Streamlined Communication
PPAP provides a clear communication channel between customers and suppliers regarding requirements and expectations.
Challenges in Implementing PPAP
While PPAP offers many advantages, it also presents challenges that project leaders must address:
1. Resource Intensive
Implementing the PPAP method requires time, effort, and resources.
Project leaders must allocate sufficient resources to meet PPAP requirements.
2. Need for Skilled Personnel
PPAP requires knowledgeable personnel to prepare, review, and update documentation accurately.
Investing in training and skills development is crucial.
3. Keeping Up with Changes
Constantly evolving industry standards can lead to frequent updates in documentation and practices.
Staying current with these changes is essential for compliance.
Conclusion
For project leaders in the auto parts manufacturing industry, the PPAP method is an indispensable tool for maintaining stable quality.
By understanding and implementing its key elements, manufacturers can mitigate risks, enhance product reliability, and foster strong customer relationships.
Although there are challenges, the benefits of PPAP in achieving consistent quality and improving customer satisfaction are considerable.
Incorporating PPAP into your manufacturing processes is a strategic step towards excellence in the competitive auto parts market.
資料ダウンロード
QCD調達購買管理クラウド「newji」は、調達購買部門で必要なQCD管理全てを備えた、現場特化型兼クラウド型の今世紀最高の購買管理システムとなります。
ユーザー登録
調達購買業務の効率化だけでなく、システムを導入することで、コスト削減や製品・資材のステータス可視化のほか、属人化していた購買情報の共有化による内部不正防止や統制にも役立ちます。
NEWJI DX
製造業に特化したデジタルトランスフォーメーション(DX)の実現を目指す請負開発型のコンサルティングサービスです。AI、iPaaS、および先端の技術を駆使して、製造プロセスの効率化、業務効率化、チームワーク強化、コスト削減、品質向上を実現します。このサービスは、製造業の課題を深く理解し、それに対する最適なデジタルソリューションを提供することで、企業が持続的な成長とイノベーションを達成できるようサポートします。
オンライン講座
製造業、主に購買・調達部門にお勤めの方々に向けた情報を配信しております。
新任の方やベテランの方、管理職を対象とした幅広いコンテンツをご用意しております。
お問い合わせ
コストダウンが利益に直結する術だと理解していても、なかなか前に進めることができない状況。そんな時は、newjiのコストダウン自動化機能で大きく利益貢献しよう!
(Β版非公開)