- お役立ち記事
- A must-see for project leaders in the feeder roller manufacturing industry for welding robots! Technology that achieves both high precision and durability
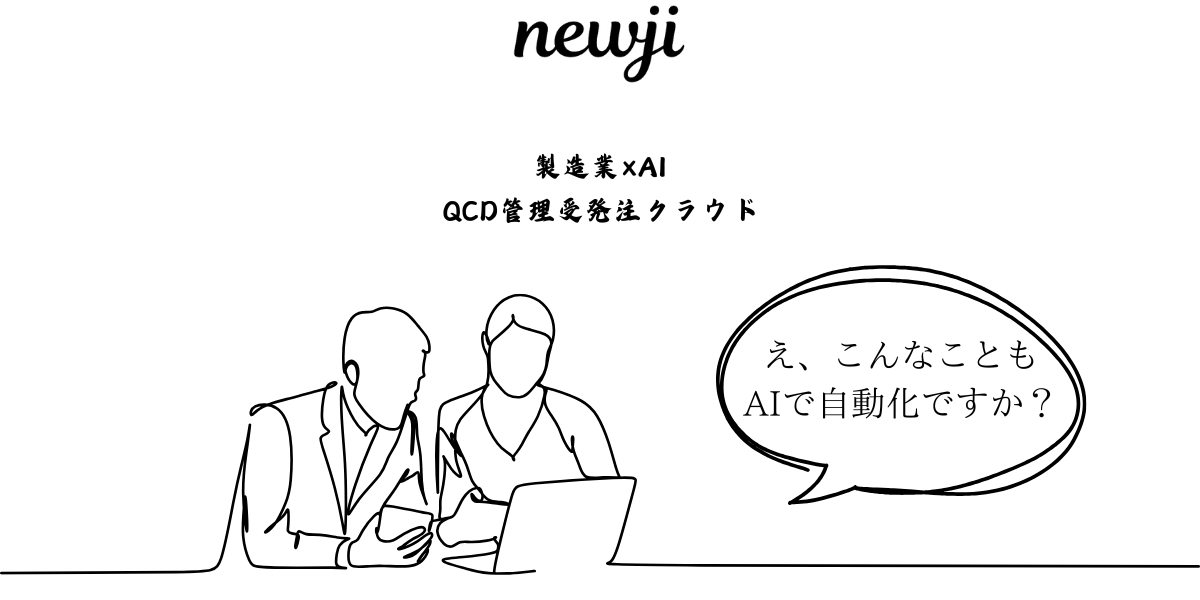
A must-see for project leaders in the feeder roller manufacturing industry for welding robots! Technology that achieves both high precision and durability
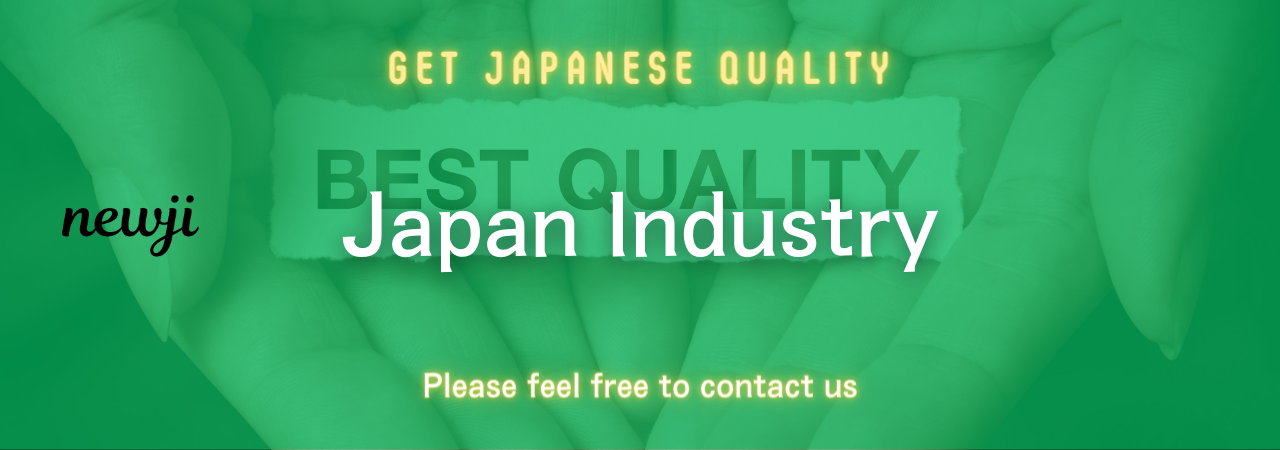
目次
Introduction to Feeder Roller Manufacturing for Welding Robots
Feeder rollers play a crucial role in the manufacturing of welding robots.
As a project leader in this industry, it is essential to focus not only on the development and innovation of these components but also on their precision and durability.
Balancing these two aspects can be challenging, but with the right technology and approach, it is entirely achievable.
In this article, we will explore technologies and techniques that project leaders can employ to achieve high precision and durability in feeder roller manufacturing.
Understanding the Importance of Precision and Durability
Precision is pivotal in feeder roller manufacturing as it directly impacts the performance of welding robots.
Accurate feeder rollers ensure that materials are fed smoothly and consistently, resulting in high-quality welds.
Any deviation in precision can lead to substandard welds and increased machine downtime.
Durability is equally important as it affects the lifespan and reliability of the rollers.
Feeder rollers must endure constant movement and high temperatures, necessitating robust materials and construction.
Improving durability not only reduces maintenance costs but also enhances the overall efficiency of the welding process.
Technologies Enhancing Precision in Feeder Rollers
Numerous technologies can enhance precision in the manufacturing of feeder rollers.
Project leaders should consider integrating the following methods:
1. CNC Machining
Computer Numerical Control (CNC) machining is instrumental in achieving high precision.
It allows for the manufacture of feeder rollers with exact dimensions and specifications.
CNC machines follow programmed instructions to cut and shape materials with high accuracy, minimizing human error.
This technology is particularly beneficial in producing complex roller designs that require meticulous detail.
2. Advanced Material Analysis
Using advanced material analysis, project leaders can select materials that deliver optimal performance.
Understanding the properties of different materials ensures that the chosen substance provides the necessary hardness and flexibility for precision.
Techniques such as spectroscopy and scanning electron microscopy help in analyzing the microstructure and composition of materials, contributing to informed decision-making.
3. Precision Grinding and Finishing
Precision grinding and finishing techniques are critical for achieving the exact surface finish required for feeder rollers.
Grinding machines equipped with high-precision tools can smooth out surfaces to the minutest details.
Finishing processes like polishing and lapping further enhance the roller’s surface integrity, contributing to better material handling.
Enhancing Durability Through Innovative Approaches
1. Quality Heat Treatments
Heat treatment processes such as annealing, quenching, and tempering modify the physical properties of metals, adding to their strength and toughness.
These treatments increase the hardness of the feeder rollers, making them more resistant to wear and tear.
By carefully controlling temperatures and cooling rates, project leaders can optimize the durability of the rollers.
2. Coating Technologies
Applying specialized coatings to feeder rollers significantly enhances their durability.
Coatings like ceramic, Teflon, and titanium nitride can reduce friction and improve resistance to corrosion and high temperatures.
These protective layers extend the rollers’ lifespan, ensuring long-term efficiency in the welding process.
3. Regular Maintenance and Testing
Implementing a stringent maintenance and testing regime is vital for monitoring the condition of feeder rollers.
Regular inspections help identify potential wear or damage early, allowing for timely repairs or replacements.
Advanced diagnostic tools such as ultrasonic testing or surface wave techniques can detect imperfections that may compromise durability.
Integrating Technology and Skilled Workforce
A sophisticated technological framework can only achieve its full potential when paired with a skilled workforce.
Project leaders must invest in training programs that enhance the abilities of their technicians and engineers.
Educating the workforce on the latest manufacturing technologies ensures they can operate equipment efficiently and maintain high standards in production.
Additionally, fostering a culture of innovation encourages workers to contribute ideas that can further improve the precision and durability of feeder rollers.
Conclusion
Project leaders in the feeder roller manufacturing industry must strive to achieve the perfect blend of precision and durability.
Through the adoption of advanced technologies such as CNC machining, heat treatments, and coating applications, it is possible to manufacture high-quality rollers that meet industry demands.
By investing in both technological advancements and workforce skill-building, companies can maintain a competitive edge and contribute to the superior performance of welding robots.
By focusing on these key aspects, project leaders can successfully navigate the challenges of the industry and drive their companies toward innovation and excellence.
資料ダウンロード
QCD調達購買管理クラウド「newji」は、調達購買部門で必要なQCD管理全てを備えた、現場特化型兼クラウド型の今世紀最高の購買管理システムとなります。
ユーザー登録
調達購買業務の効率化だけでなく、システムを導入することで、コスト削減や製品・資材のステータス可視化のほか、属人化していた購買情報の共有化による内部不正防止や統制にも役立ちます。
NEWJI DX
製造業に特化したデジタルトランスフォーメーション(DX)の実現を目指す請負開発型のコンサルティングサービスです。AI、iPaaS、および先端の技術を駆使して、製造プロセスの効率化、業務効率化、チームワーク強化、コスト削減、品質向上を実現します。このサービスは、製造業の課題を深く理解し、それに対する最適なデジタルソリューションを提供することで、企業が持続的な成長とイノベーションを達成できるようサポートします。
オンライン講座
製造業、主に購買・調達部門にお勤めの方々に向けた情報を配信しております。
新任の方やベテランの方、管理職を対象とした幅広いコンテンツをご用意しております。
お問い合わせ
コストダウンが利益に直結する術だと理解していても、なかなか前に進めることができない状況。そんな時は、newjiのコストダウン自動化機能で大きく利益貢献しよう!
(Β版非公開)