- お役立ち記事
- A must-see for quality control department leaders in the electrical equipment manufacturing industry! How to ensure the safety of electrical products with insulation testing
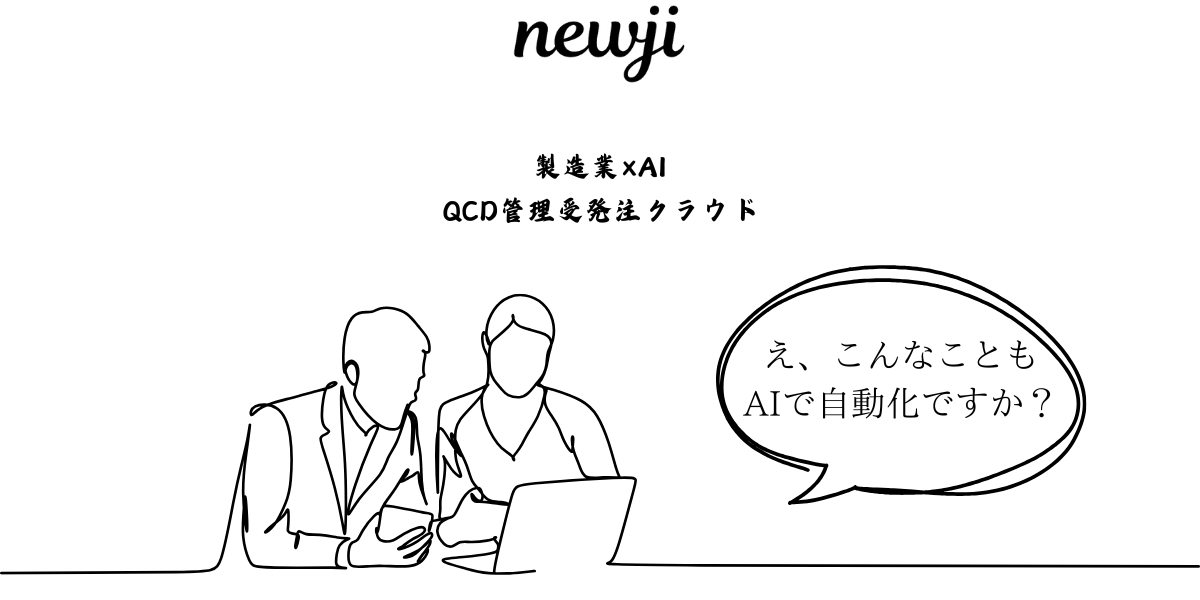
A must-see for quality control department leaders in the electrical equipment manufacturing industry! How to ensure the safety of electrical products with insulation testing
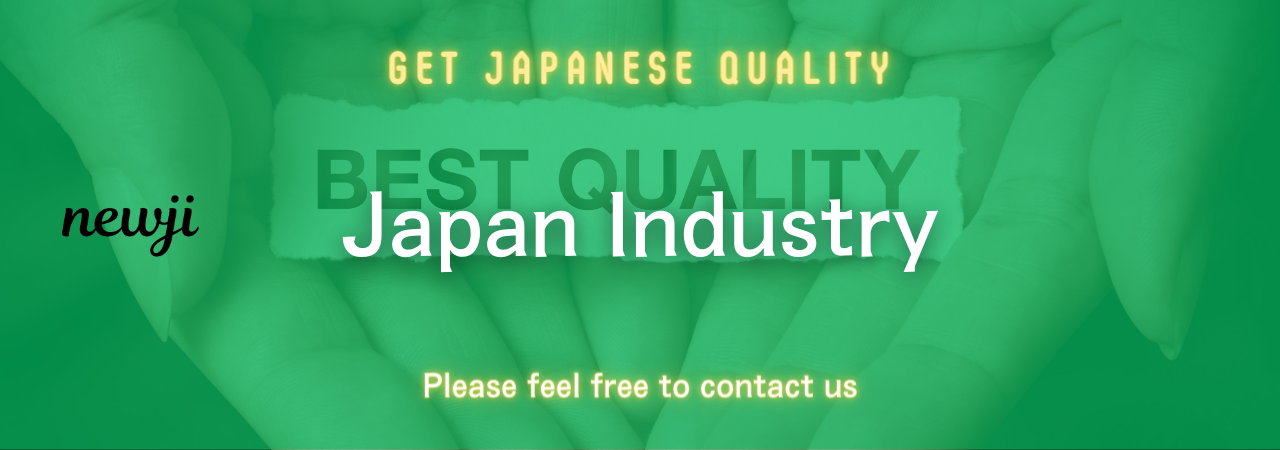
In the world of electrical equipment manufacturing, ensuring the safety and reliability of products is paramount.
This responsibility predominantly falls on the shoulders of quality control department leaders who must consistently uphold rigorous safety standards.
One crucial method for maintaining these standards is through insulation testing.
Proper insulation testing not only guarantees that the electrical products are safe for consumer use but also helps in avoiding potential failures and costly recalls.
目次
Understanding Insulation Testing
Insulation testing involves examining the insulating components of electrical devices to ensure they function correctly under varying operating conditions.
The primary goal of this test is to measure the resistance of the insulation material against electric current.
By doing this, manufacturers can predict the possibility of current leakages and short circuits that could lead to malfunctions.
The process typically involves applying a high voltage to the electrical circuits or components for a specific duration.
The outcome of this test provides crucial insights into the quality and effectiveness of the insulation, helping manufacturers detect any degradation or weaknesses.
Why Is Insulation Testing Important?
Insulation testing is vital because it directly impacts the safety and efficiency of electrical products.
When electrical equipment operates, it generates heat and is subject to environmental factors such as humidity and dust, which can deteriorate the insulation over time.
Regular testing helps identify these issues early, preventing accidents that could harm users or damage surrounding equipment.
Beyond safety, insulation testing affects the longevity and performance of electrical products.
Any weakness in insulation could lead to energy losses, reducing the product’s efficiency.
For companies in the electrical equipment manufacturing industry, maintaining product reliability is essential for customer satisfaction and maintaining competitive advantage in the market.
Steps for Conducting Insulation Testing
1. Preparation
Before starting the insulation test, ensure that all equipment is appropriately calibrated and in good working condition.
Check the manufacturer’s guidelines for any specific requirements related to your products.
Also, verify that the environment where the testing will occur is stable, with minimal temperature and humidity fluctuations to ensure accurate results.
2. Isolation
Turn off all power sources connected to the equipment and isolate the product under test.
It’s crucial to have a clear plan for disconnecting the necessary components, ensuring that no unintentional connections could skew the test results.
3. Application of Test Voltage
Select the appropriate test voltage based on the product specifications and begin the test.
Typically, this involves gradually increasing the voltage to the desired level, holding it for the specified duration, and monitoring the insulation resistance closely.
Record the readings throughout the period to capture any fluctuations that might indicate issues.
4. Analysis
After completing the test, analyze the results to determine the insulation condition.
Compare the resistance values against industry standards and historical data from previous tests.
If the insulation resistance falls below acceptable levels, it may indicate possible defects or degradation that need addressing.
Best Practices for Insulation Testing
Regular Testing Schedule
Establish a regular testing schedule to ensure consistent monitoring of insulation integrity.
Performing tests only during product development stages isn’t enough; periodic evaluations during the product lifecycle are necessary to catch potential issues before they become critical.
Proper Training for Personnel
Ensure that all personnel involved in insulation testing are adequately trained to handle the equipment and interpret results accurately.
This includes understanding the safety protocols to prevent accidents during high-voltage testing and knowing how to diagnose potential issues from the test data.
Documentation and Traceability
Maintain thorough documentation of all insulation testing procedures and results.
This archive should include details such as date, time, environmental conditions, equipment used, and test outcomes.
Keeping detailed records aids in traceability and helps identify long-term trends in product performance or recurring issues.
Upgrading Testing Equipment
Regularly review and upgrade testing equipment to keep up with technological advancements and industry standards.
Outdated equipment may not provide accurate readings or could fail to detect subtle insulation issues, jeopardizing product safety and performance.
Challenges and Solutions
Detecting Complex Insulation Issues
In some cases, insulation problems may not be straightforward to identify.
Complex issues often require advanced testing methods or a combination of different tests to pinpoint.
Using state-of-the-art diagnostic tools and techniques, such as partial discharge measurements or infrared thermography, can help uncover hidden insulation defects.
Environmental Factors
The environment in which the testing is conducted can affect the results.
Fluctuations in temperature and humidity can skew resistance measurements, leading to inaccurate conclusions.
To mitigate these issues, always conduct tests in a controlled environment and, if possible, use temperature and humidity compensating correction methods during analysis.
Interpreting Test Results
Understanding the test results can sometimes be challenging, especially when dealing with borderline cases.
Investing in advanced software solutions that provide data visualization and diagnostic analysis can simplify the interpretation process significantly.
In conclusion, insulation testing is a crucial aspect of ensuring the safety and reliability of electrical products in the manufacturing sector.
By following a structured approach and embracing best practices, quality control department leaders can significantly reduce risks and enhance product integrity.
Ultimately, consistent and accurate insulation testing safeguards against failures, protecting both the consumer and the company’s reputation.
資料ダウンロード
QCD調達購買管理クラウド「newji」は、調達購買部門で必要なQCD管理全てを備えた、現場特化型兼クラウド型の今世紀最高の購買管理システムとなります。
ユーザー登録
調達購買業務の効率化だけでなく、システムを導入することで、コスト削減や製品・資材のステータス可視化のほか、属人化していた購買情報の共有化による内部不正防止や統制にも役立ちます。
NEWJI DX
製造業に特化したデジタルトランスフォーメーション(DX)の実現を目指す請負開発型のコンサルティングサービスです。AI、iPaaS、および先端の技術を駆使して、製造プロセスの効率化、業務効率化、チームワーク強化、コスト削減、品質向上を実現します。このサービスは、製造業の課題を深く理解し、それに対する最適なデジタルソリューションを提供することで、企業が持続的な成長とイノベーションを達成できるようサポートします。
オンライン講座
製造業、主に購買・調達部門にお勤めの方々に向けた情報を配信しております。
新任の方やベテランの方、管理職を対象とした幅広いコンテンツをご用意しております。
お問い合わせ
コストダウンが利益に直結する術だと理解していても、なかなか前に進めることができない状況。そんな時は、newjiのコストダウン自動化機能で大きく利益貢献しよう!
(Β版非公開)