- お役立ち記事
- A must-see for quality control department leaders in the high-temperature furnace refractory brick manufacturing industry! Manufacturing technology to improve heat resistance and insulation
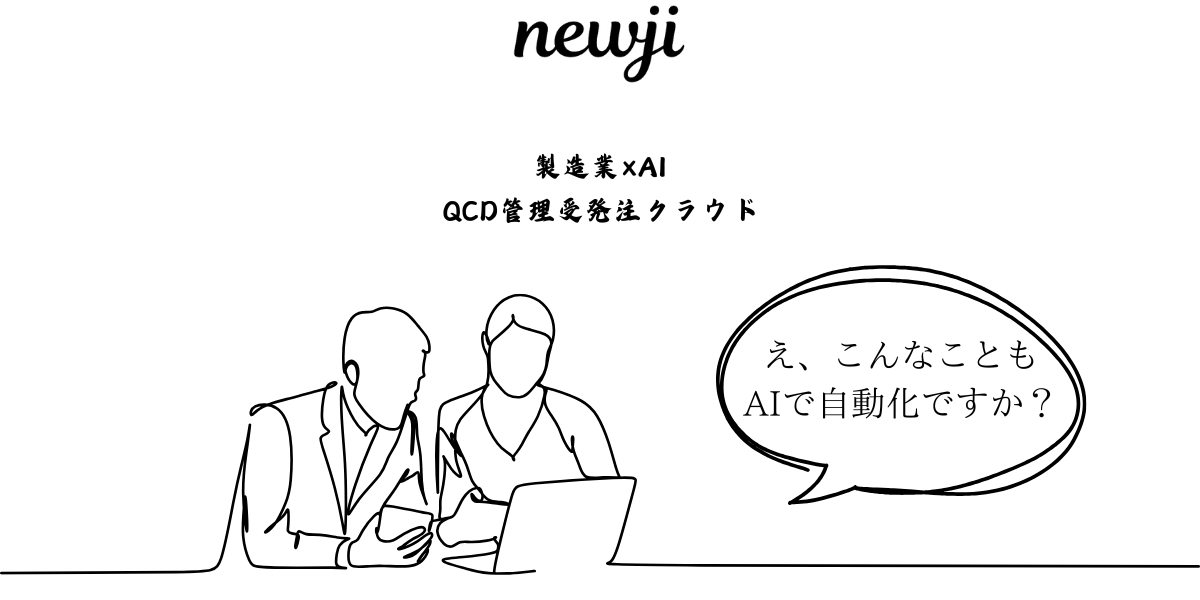
A must-see for quality control department leaders in the high-temperature furnace refractory brick manufacturing industry! Manufacturing technology to improve heat resistance and insulation
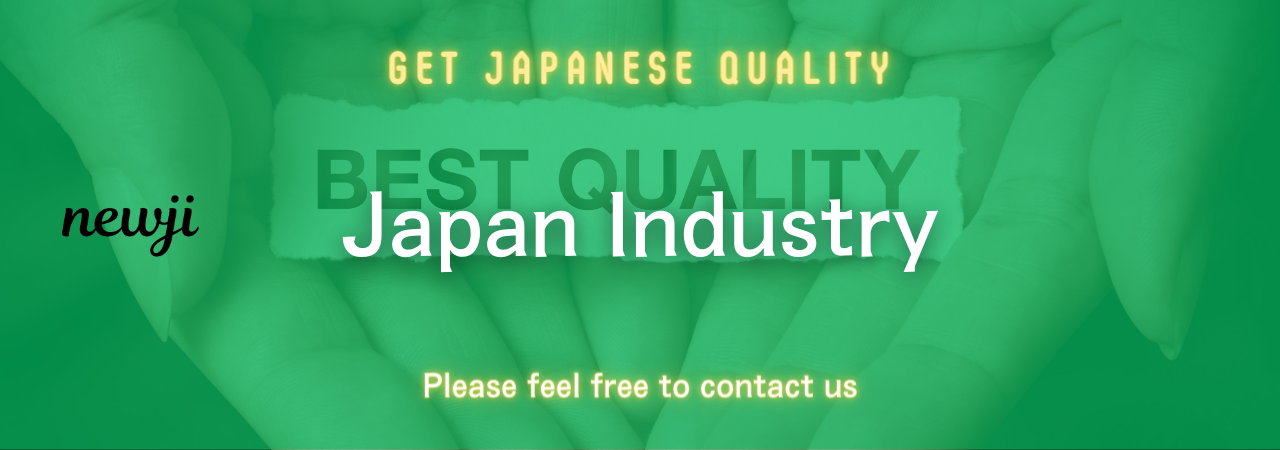
目次
Introduction to High-Temperature Furnace Refractory Bricks
The manufacturing of high-temperature furnace refractory bricks is a specialized field that demands precise quality control and cutting-edge technology.
These bricks are crucial components in industries like steel, glass, and cement manufacturing, where furnaces operate at extremely high temperatures.
The quality and performance of refractory bricks directly impact the efficiency and safety of these industrial processes.
In this article, we will explore the manufacturing technologies that can significantly improve the heat resistance and insulation properties of refractory bricks.
Understanding the Basics of Refractory Bricks
Refractory bricks, also known as firebricks, are specifically designed to withstand high temperatures without losing their structural integrity.
They are primarily made from ceramic materials like alumina, silica, and fire clay.
The key to their effectiveness lies in their ability to retain strength and insulate against intense heat, preventing energy loss and protecting furnace linings.
The manufacturing process of these bricks involves mixing raw materials, shaping them into desired forms, and firing them at high temperatures to achieve the desired properties.
The choice of raw materials and the manufacturing process significantly influence the final product’s performance.
Challenges in Manufacturing Refractory Bricks
Manufacturers face several challenges when producing high-quality refractory bricks.
These include ensuring consistent quality, achieving optimal heat resistance, and providing effective insulation.
Additionally, maintaining the structural integrity of bricks under cyclic thermal stress and corrosive conditions poses a significant challenge.
The development of advanced manufacturing technologies is essential to overcome these hurdles and produce bricks that meet industrial demands.
Improving Heat Resistance
Improving the heat resistance of refractory bricks is a primary focus for manufacturers.
Several technologies can be employed to enhance this important property.
Optimizing Raw Material Selection
The selection of raw materials plays a crucial role in determining a brick’s heat resistance.
High-alumina refractories are known for their exceptional heat-resistant properties and are commonly used in demanding applications.
In recent years, the use of synthetic raw materials such as fused alumina and magnesia has gained traction due to their superior performance.
Advanced Shaping and Firing Techniques
The shaping process, including pressing and extrusion methods, can significantly influence the brick’s heat resistance.
Innovations in these techniques, such as the adoption of isostatic pressing, help in achieving greater density and uniformity.
Moreover, advancements in firing technology, like high-temperature and controlled-atmosphere furnaces, ensure optimal bonding of the material, leading to improved thermal stability.
Nano-Technology Integration
The integration of nano-technology into the manufacturing process is a game-changer for refractory bricks.
By incorporating nano-sized particles, manufacturers can improve heat resistance by optimizing microstructural properties.
Nano-materials enhance thermal shock resistance, reduce porosity, and improve the overall strength of the bricks.
Enhancing Insulation Properties
In addition to heat resistance, effective insulation is critical for the performance of refractory bricks.
Insulation minimizes heat loss and saves energy, making it a significant aspect of improving furnace efficiency.
Developing Lightweight Refractory Materials
Lightweight refractory bricks are gaining popularity due to their superior insulation properties.
They are made using foaming techniques that create a porous structure, reducing density while maintaining insulating capability.
These lightweight bricks are especially beneficial in applications where weight reduction leads to energy savings and easier installation.
Incorporating High-Performance Insulating Materials
To further enhance insulation, high-performance materials such as ceramic fibers and insulating firebricks can be incorporated into the design.
These materials provide additional layers of insulation, retaining heat and reducing energy consumption.
Innovative Coating Technologies
Coating technologies have made significant strides in improving the insulation properties of refractory bricks.
The application of heat-reflective coatings can minimize heat absorption and promote energy efficiency.
This innovative approach not only enhances insulation but also extends the lifespan of furnace linings.
Quality Control in Refractory Brick Manufacturing
Ensuring the quality of refractory bricks is paramount for their performance in high-temperature applications.
Implementing robust quality control measures helps in identifying defects early and maintaining product consistency.
State-of-the-Art Testing Facilities
Investing in state-of-the-art testing facilities allows manufacturers to accurately assess properties like thermal conductivity, mechanical strength, and resistance to thermal shock.
Advanced testing methods ensure that only bricks meeting stringent quality standards make it to the market.
Automation and Data-Driven Production
Automation in the manufacturing process reduces human error and enhances precision.
Data-driven production techniques involve collecting real-time data and using it to optimize manufacturing parameters, leading to improved product consistency and quality.
Conclusion
The manufacturing of high-temperature furnace refractory bricks is a dynamic field requiring constant innovation and quality control.
By focusing on advanced technologies, manufacturers can significantly improve the heat resistance and insulation properties of their products.
This not only enhances the efficiency and safety of industrial processes but also contributes to energy conservation.
As the industry continues to evolve, embracing these technological advancements will ensure that refractory brick manufacturers remain competitive and capable of meeting the demands of modern industry.
資料ダウンロード
QCD調達購買管理クラウド「newji」は、調達購買部門で必要なQCD管理全てを備えた、現場特化型兼クラウド型の今世紀最高の購買管理システムとなります。
ユーザー登録
調達購買業務の効率化だけでなく、システムを導入することで、コスト削減や製品・資材のステータス可視化のほか、属人化していた購買情報の共有化による内部不正防止や統制にも役立ちます。
NEWJI DX
製造業に特化したデジタルトランスフォーメーション(DX)の実現を目指す請負開発型のコンサルティングサービスです。AI、iPaaS、および先端の技術を駆使して、製造プロセスの効率化、業務効率化、チームワーク強化、コスト削減、品質向上を実現します。このサービスは、製造業の課題を深く理解し、それに対する最適なデジタルソリューションを提供することで、企業が持続的な成長とイノベーションを達成できるようサポートします。
オンライン講座
製造業、主に購買・調達部門にお勤めの方々に向けた情報を配信しております。
新任の方やベテランの方、管理職を対象とした幅広いコンテンツをご用意しております。
お問い合わせ
コストダウンが利益に直結する術だと理解していても、なかなか前に進めることができない状況。そんな時は、newjiのコストダウン自動化機能で大きく利益貢献しよう!
(Β版非公開)