- お役立ち記事
- A must-see for the purchasing department! Benchmarking and analysis methods necessary for cost improvement
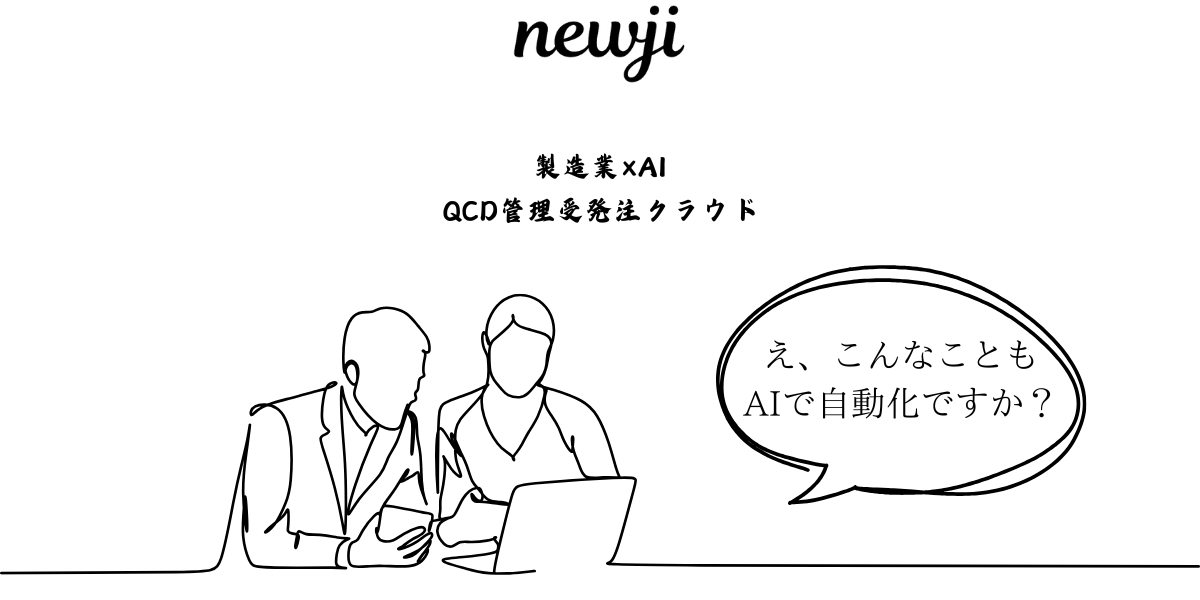
A must-see for the purchasing department! Benchmarking and analysis methods necessary for cost improvement
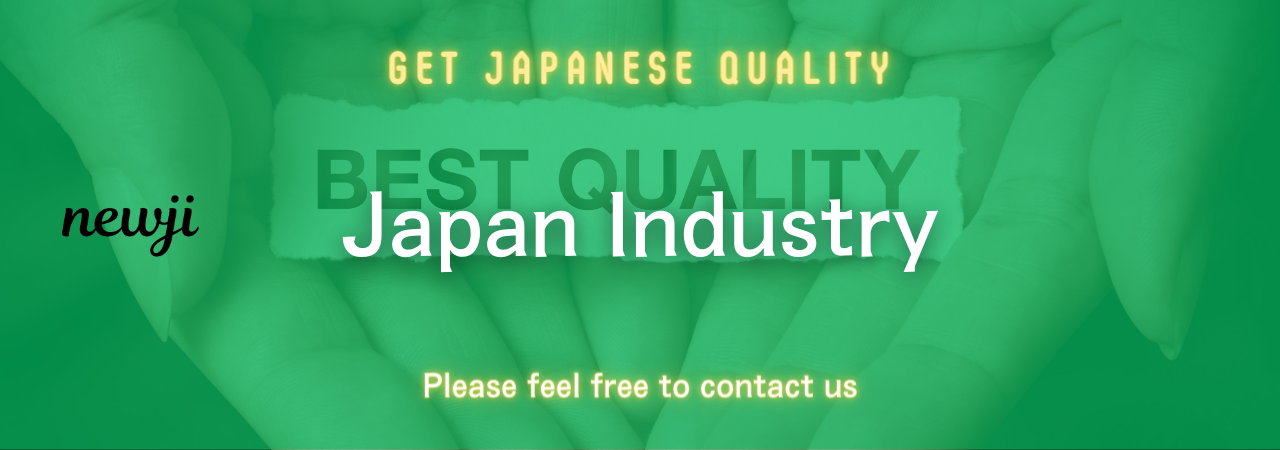
目次
Understanding Benchmarking
For the purchasing department, cost improvement is a crucial aspect that requires continuous attention and analysis.
One of the most effective ways to achieve this is through benchmarking.
Benchmarking is the process of comparing your own practices, processes, and performance metrics to those recognized as industry standards.
This strategic evaluation helps identify areas where improvements can be made, ensuring that you are operating as efficiently as possible.
Benchmarking helps the purchasing team understand where they stand in the competitive landscape.
It enables organizations to evaluate their performance against competitors and identify best practices that can be adopted or adapted for cost improvement.
By studying other organizations, the purchasing department can gain insights into their own processes, uncover inefficiencies, and discover opportunities for cost savings.
Types of Benchmarking
There are different types of benchmarking, each serving a unique purpose.
Understanding these types will help your team select the most appropriate method for your goals.
Operational Benchmarking: Focuses on comparing the internal processes and operations to improve efficiency.
This can often lead to cost reductions and improved productivity in the purchasing department.
Competitive Benchmarking: This involves comparing your company’s standards and performance against direct competitors.
It helps to highlight areas where your company is lagging and provides a roadmap for improvement.
Strategic Benchmarking: Examines how others compete to provide strategic insights.
This might include broad financial strategies or approaches to market share growth.
Internal Benchmarking: Compares processes and performance within different departments of the same organization.
This can uncover best practices that are already functioning well within the company and can be implemented more widely.
Steps Involved in Benchmarking
The process of benchmarking requires a methodical approach.
Here are the essential steps involved in conducting a successful benchmarking exercise:
Step 1: Identify What to Benchmark
First, decide what areas need improvement.
Since we’re focusing on cost improvement within the purchasing department, it might be helpful to target aspects like vendor management, procurement processes, or inventory control.
Step 2: Choose Benchmarking Partners
Select organizations known for excellence in the areas you wish to improve.
These can be industry leaders, direct competitors, or organizations recognized for their efficiency and innovation.
Step 3: Collect Data
Gather data from your own operations and from the chosen benchmarking partners.
This might involve internal audits, surveys, or utilizing industry reports and databases.
Step 4: Analyze the Data
Analyze the information collected to identify gaps in your performance compared to the benchmark.
Look for trends, patterns, and specific areas where costs can be reduced.
Step 5: Implement Improvements
Based on the analysis, develop a plan to implement necessary changes.
This might involve adopting new technologies, streamlining procurement processes, or renegotiating vendor contracts.
Step 6: Monitor and Review
After implementing changes, monitor the progress and impact on costs.
Regularly review the benchmarking process and outcomes to ensure improvement is sustained and make adjustments as needed.
Analysis Methods for Cost Improvement
In addition to benchmarking, employing the right analysis methods is crucial for achieving cost improvements.
Cost-Benefit Analysis
This involves comparing the costs and benefits of different courses of action.
The objective is to ensure that the benefits outweigh the costs and to decide between multiple alternatives to optimize spending.
Spend Analysis
This process involves analyzing procurement data to identify spending patterns and trends.
It helps in understanding how money is being spent, highlighting opportunities for cost savings and better resource allocation.
Supplier Performance Analysis
Evaluating supplier performance is essential for cost control.
Assess suppliers based on delivery reliability, quality, and cost-effectiveness to make informed decisions about vendor selection and negotiation.
Value Chain Analysis
Examining each step of the value chain can help identify inefficiencies and opportunities for cost reduction.
Understanding how each part of the purchasing process adds value is essential for making meaningful cost improvements.
Embracing Technology for Enhanced Analysis
Technology plays a vital role in modern benchmarking and cost analysis efforts.
Advanced software tools and platforms can automate data collection and analysis, providing actionable insights more efficiently.
Implementing e-procurement solutions, for instance, can streamline the purchasing process, reduce errors, and enhance cost efficiency.
Using AI-driven analytics, the purchasing department can predict trends, assess risks, and simulate scenarios to better manage costs.
Conclusion
Effective benchmarking and analysis methods are indispensable for the purchasing department’s efforts toward cost improvement.
By understanding and implementing the right benchmarking processes and analysis techniques, your organization can identify inefficiencies, explore best practices, and achieve significant cost reductions.
Combining these strategies with technological solutions can further enhance the ability to make data-driven decisions, ensuring long-term success and competitiveness in the market.
Remember, cost improvement is an ongoing endeavor and requires regular evaluations to adapt to changing market conditions and internal growth.
資料ダウンロード
QCD調達購買管理クラウド「newji」は、調達購買部門で必要なQCD管理全てを備えた、現場特化型兼クラウド型の今世紀最高の購買管理システムとなります。
ユーザー登録
調達購買業務の効率化だけでなく、システムを導入することで、コスト削減や製品・資材のステータス可視化のほか、属人化していた購買情報の共有化による内部不正防止や統制にも役立ちます。
NEWJI DX
製造業に特化したデジタルトランスフォーメーション(DX)の実現を目指す請負開発型のコンサルティングサービスです。AI、iPaaS、および先端の技術を駆使して、製造プロセスの効率化、業務効率化、チームワーク強化、コスト削減、品質向上を実現します。このサービスは、製造業の課題を深く理解し、それに対する最適なデジタルソリューションを提供することで、企業が持続的な成長とイノベーションを達成できるようサポートします。
オンライン講座
製造業、主に購買・調達部門にお勤めの方々に向けた情報を配信しております。
新任の方やベテランの方、管理職を対象とした幅広いコンテンツをご用意しております。
お問い合わせ
コストダウンが利益に直結する術だと理解していても、なかなか前に進めることができない状況。そんな時は、newjiのコストダウン自動化機能で大きく利益貢献しよう!
(Β版非公開)