- お役立ち記事
- A must-see for the purchasing department! Key points of supplier audits that should be kept in mind during risk assessment
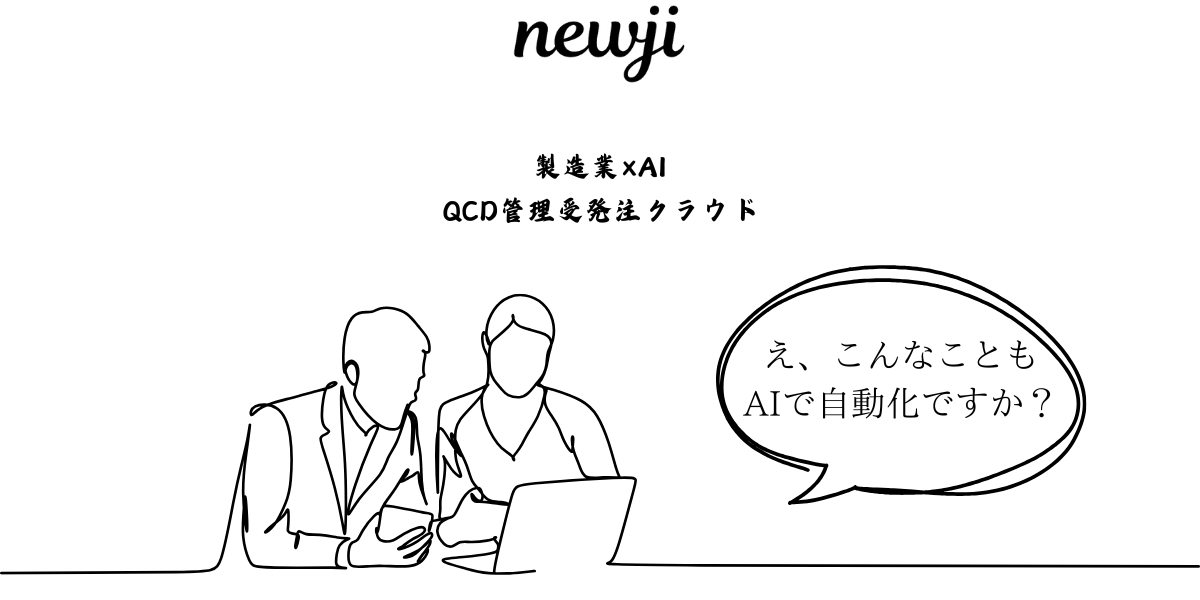
A must-see for the purchasing department! Key points of supplier audits that should be kept in mind during risk assessment
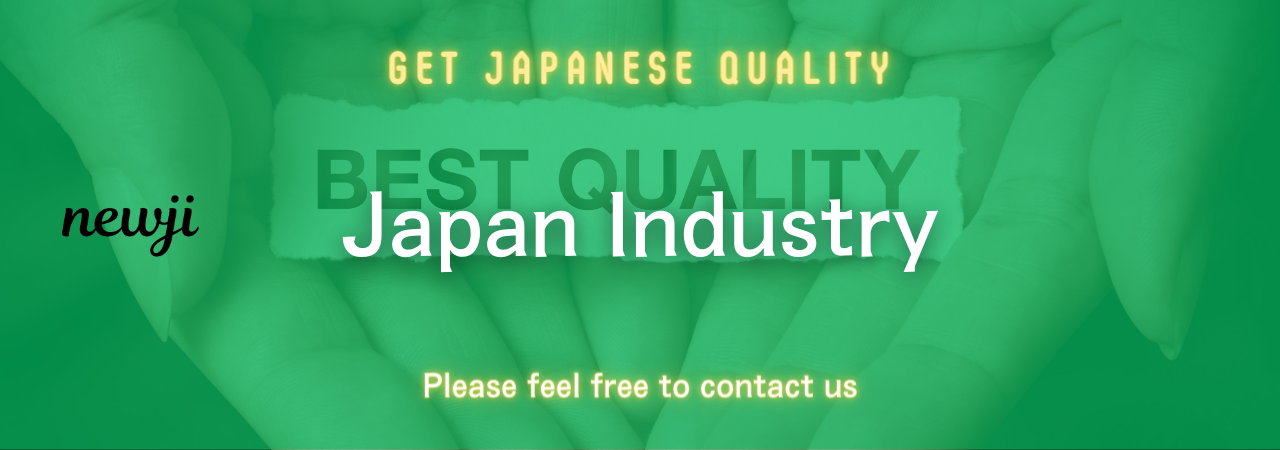
目次
Understanding Supplier Audits
Supplier audits are an essential part of the procurement process, serving as a key tool for managing risks and ensuring compliance with quality standards.
These audits help identify potential issues before they affect the supply chain and enable companies to maintain strong relationships with their suppliers.
By conducting thorough audits, companies can avoid costly disruptions and ensure that their suppliers adhere to necessary regulations and standards.
Why Supplier Audits Are Important
The importance of supplier audits cannot be overstated.
They are crucial for verifying that suppliers meet the contractual and regulatory requirements expected by the purchasing company.
Audits ensure the supplier’s operational processes, financial stability, and compliance levels are in alignment with the company’s expectations.
They mitigate risks by uncovering hidden compliance issues, quality control problems, or financial instability that could threaten supply chain fluidity.
Preparing for a Supplier Audit
Preparation is key to conducting a successful supplier audit.
Before starting, gather all relevant documentation, such as supplier contracts, previous audit reports, and internal quality standards.
Identify what specific areas need focus during the audit, depending on the nature of the supplier relationship and the level of risk they pose to the company.
By doing so, businesses can ensure that audits are both efficient and comprehensive.
Critical Areas to Assess During an Audit
Quality Management Systems
One of the primary focuses during a supplier audit is assessing the quality management system in place.
Ensure that the supplier has processes for managing quality that meet your company’s standards and those dictated by industry regulations.
Evaluate how they handle non-conformances, continuous improvement initiatives, and customer feedback.
This step is crucial for reducing the risk of defects and recalls.
Financial Stability
A supplier’s financial health is critical to their ability to provide consistent service and products.
During the audit, assess financial documents to gauge their stability and ability to meet demand.
A financially unstable supplier might struggle to fulfill large or urgent orders, causing bottlenecks in your supply chain.
Compliance with Regulations
Supplier audits should include a thorough review of the supplier’s compliance with legal and regulatory standards relevant to your industry.
This can include environmental regulations, worker safety standards, or industry-specific certifications.
Non-compliance can lead to significant legal and financial penalties for both the supplier and your company.
Operational Performance
Evaluating a supplier’s operational performance helps you understand their capacity to deliver products or services as required.
Assess their production capabilities, supply chain management, and logistical efficiency.
Look into previous delivery records to check for promptness and any recurring issues in fulfilling orders.
Common Challenges in Supplier Audits
Lack of Transparency
A major challenge can be a lack of transparency from suppliers.
Suppliers may not willingly disclose issues related to product quality or compliance.
Developing a strong relationship and open communication can help in gaining their trust and ensuring that they provide honest information during audits.
Resource Constraints
Conducting comprehensive supplier audits requires adequate resources, including dedicated personnel and technology.
Companies with limited resources might struggle to perform thorough audits.
To overcome this, prioritize high-risk suppliers and perhaps use external auditors to assist in covering all necessary bases.
Maintaining Objectivity
Bias can creep into audits if there is an over-reliance on supplier self-audits or if relationships between buyers and suppliers blur professional boundaries.
Maintaining objectivity is essential to ensure that the audit results are accurate and unbiased.
Involvement of third-party auditors can provide an added layer of impartiality.
Key Strategies for Effective Supplier Audits
Regular Engagement
Plan to hold supplier audits at regular intervals to keep information up to date.
Unexpected audits can also reveal how suppliers handle situations under unstipulated conditions and provide a more accurate view of their operations.
Use of Quality Metrics
Implement measurable quality metrics that help in comparing supplier performances quantitatively.
Metrics such as defect rates, delivery times, and customer satisfaction levels can provide valuable insights into supplier reliability and performance.
Collaboration and Feedback
Foster a culture of collaboration and feedback with your suppliers.
Encouraging suppliers to share their challenges and successes allows for learning and improvement on both sides.
Consider giving positive incentives for suppliers who consistently meet or exceed audit standards.
Conclusion
Supplier audits are a critical step in securing and managing a successful supply chain, mitigating risks, and ensuring compliance with necessary standards.
By focusing on key areas of assessment and overcoming common challenges with strategic planning, purchasing departments can conduct effective audits that protect their interests.
Regular engagement, clear metrics, and a collaborative approach all contribute to a more streamlined and reliable supplier relationship.
Ultimately, effective supplier audits lead to better quality products, reduced risks, and stronger supply chain resilience.
資料ダウンロード
QCD調達購買管理クラウド「newji」は、調達購買部門で必要なQCD管理全てを備えた、現場特化型兼クラウド型の今世紀最高の購買管理システムとなります。
ユーザー登録
調達購買業務の効率化だけでなく、システムを導入することで、コスト削減や製品・資材のステータス可視化のほか、属人化していた購買情報の共有化による内部不正防止や統制にも役立ちます。
NEWJI DX
製造業に特化したデジタルトランスフォーメーション(DX)の実現を目指す請負開発型のコンサルティングサービスです。AI、iPaaS、および先端の技術を駆使して、製造プロセスの効率化、業務効率化、チームワーク強化、コスト削減、品質向上を実現します。このサービスは、製造業の課題を深く理解し、それに対する最適なデジタルソリューションを提供することで、企業が持続的な成長とイノベーションを達成できるようサポートします。
オンライン講座
製造業、主に購買・調達部門にお勤めの方々に向けた情報を配信しております。
新任の方やベテランの方、管理職を対象とした幅広いコンテンツをご用意しております。
お問い合わせ
コストダウンが利益に直結する術だと理解していても、なかなか前に進めることができない状況。そんな時は、newjiのコストダウン自動化機能で大きく利益貢献しよう!
(Β版非公開)