- お役立ち記事
- A process mapping method to strengthen collaboration between manufacturing sites and purchasing departments
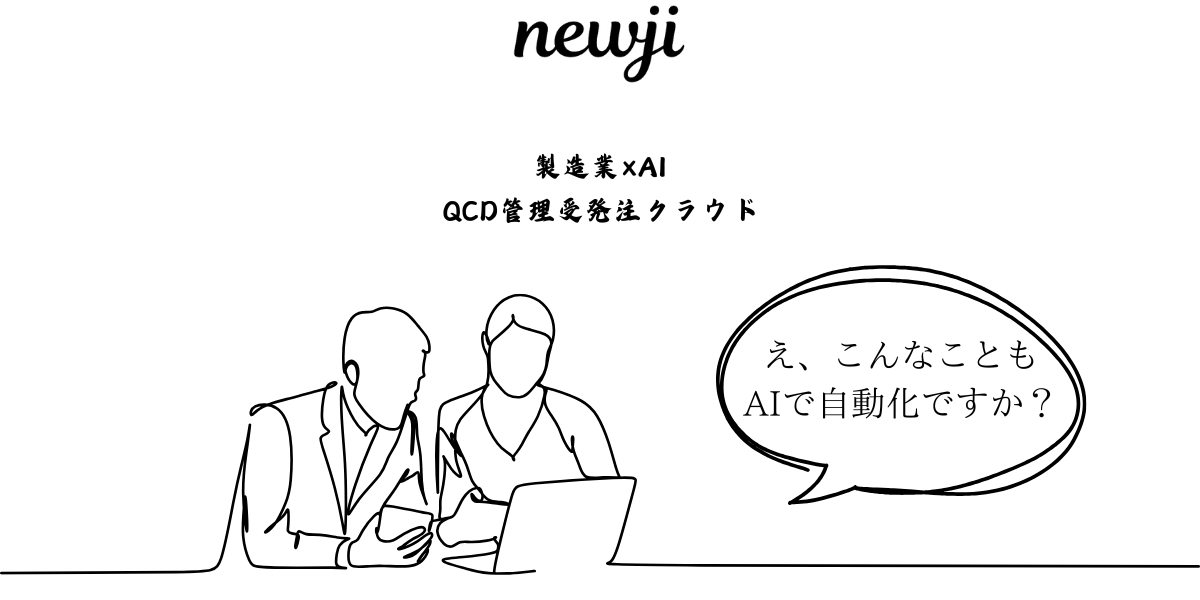
A process mapping method to strengthen collaboration between manufacturing sites and purchasing departments
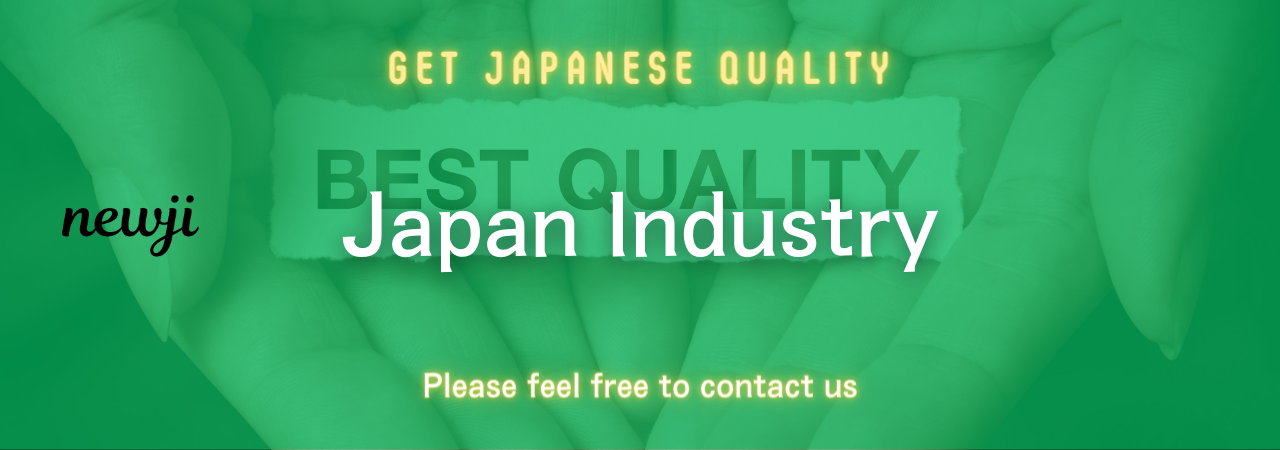
目次
Understanding Process Mapping
Process mapping is a visual tool that helps organizations understand the workflow of their processes.
It involves creating a detailed diagram that outlines each step of a process, identifying who does what and when.
This serves to provide a clear view of how the different components of a process interact with each other.
In the context of manufacturing and purchasing, process mapping can be used to illustrate and analyze the flow of materials, information, and responsibilities between these departments.
The ultimate goal is to strengthen collaboration and improve efficiency, reducing the risk of miscommunication and errors.
Why Use Process Mapping?
The use of process mapping is crucial for several reasons.
First, it helps identify inefficiencies and bottlenecks in workflows.
When manufacturing sites and purchasing departments work together, there can be overlaps or delays in processes due to unclear roles or responsibilities.
With a visual map, these issues can be pinpointed and addressed.
Second, process mapping facilitates better communication.
By providing a shared reference point, it ensures that all parties involved have a common understanding of the processes and their interdependencies.
This is especially important in manufacturing, where even small misunderstandings can lead to significant disruptions.
Finally, process mapping supports continuous improvement.
It provides a baseline against which changes can be measured, making it easier to assess the impact of process improvements and drive further enhancements.
Steps to Create an Effective Process Map
Creating a process map involves several key steps.
Each step is crucial for ensuring that the map accurately reflects the real-world process it is intended to describe.
1. Define the Scope
The first step in creating a process map is to define the scope of the process you want to map.
This involves identifying the start and end points of the process, as well as any inputs and outputs.
In the context of manufacturing and purchasing, this might include defining how a purchase order is generated and processed through to when the materials are received and used in production.
2. Gather Information
Once the scope is defined, gather all necessary information about the process.
This can involve interviewing stakeholders, observing workflows, and reviewing existing documentation.
The goal is to get a comprehensive understanding of each step of the process, including who is involved and what resources are required.
3. Identify Key Steps and Relationships
With the information gathered, identify the key steps involved in the process and the relationships between them.
These might include decision points, approvals, or transfers of information.
For manufacturing and purchasing, it is crucial to identify where dependencies exist between these departments, as these areas often require the most collaboration.
4. Create the Process Map
Use a tool like flowchart software or even a whiteboard to create your process map.
Represent each step of the process with a symbol, such as an arrow for a process flow or a diamond for a decision point.
Connect these symbols with lines or arrows to illustrate the sequence of activities and relationships.
5. Validate the Map
Once the process map is created, share it with the stakeholders involved and validate it.
Ensure that it accurately reflects the real-world process, and make adjustments as necessary.
This step is critical for gaining buy-in from those who will be using the map to guide their work.
Strengthening Collaboration Between Manufacturing and Purchasing
By implementing process mapping, manufacturing sites and purchasing departments can significantly enhance their collaboration.
This collaboration results in a more streamlined and efficient workflow, with fewer disruptions and increased responsiveness.
Improving Communication
Process mapping provides a clear and unified view of the roles and responsibilities of each department, reducing the likelihood of miscommunication.
By having a shared understanding, teams can communicate more effectively and make more informed decisions.
Increasing Transparency
The visual nature of process maps makes processes more transparent.
This transparency allows both manufacturing and purchasing teams to see how their work affects others, fostering a greater appreciation of each department’s contributions.
Facilitating Better Decision-Making
With clearer insights into process flows and dependencies, decision-makers can more easily identify areas for improvement.
This enables them to allocate resources more effectively and prioritize initiatives that will yield the greatest benefits.
Enabling Continuous Improvement
Lastly, process mapping sets the foundation for continuous improvement.
Having a visual representation of processes allows for easy identification of areas that need enhancement.
Organizations can experiment with changes and measure the outcomes against the process map, driving ongoing improvements in collaboration and efficiency.
Conclusion
Process mapping is a powerful tool for strengthening collaboration between manufacturing sites and purchasing departments.
By providing clarity, improving communication, and enabling transparency, it helps organizations work more efficiently and effectively.
As you embark on creating process maps, remember that the key is in the detail: understanding the specifics of each process and representing them accurately in the map.
With this approach, you will set the stage for enhanced collaboration and a more productive, streamlined workflow.
資料ダウンロード
QCD調達購買管理クラウド「newji」は、調達購買部門で必要なQCD管理全てを備えた、現場特化型兼クラウド型の今世紀最高の購買管理システムとなります。
ユーザー登録
調達購買業務の効率化だけでなく、システムを導入することで、コスト削減や製品・資材のステータス可視化のほか、属人化していた購買情報の共有化による内部不正防止や統制にも役立ちます。
NEWJI DX
製造業に特化したデジタルトランスフォーメーション(DX)の実現を目指す請負開発型のコンサルティングサービスです。AI、iPaaS、および先端の技術を駆使して、製造プロセスの効率化、業務効率化、チームワーク強化、コスト削減、品質向上を実現します。このサービスは、製造業の課題を深く理解し、それに対する最適なデジタルソリューションを提供することで、企業が持続的な成長とイノベーションを達成できるようサポートします。
オンライン講座
製造業、主に購買・調達部門にお勤めの方々に向けた情報を配信しております。
新任の方やベテランの方、管理職を対象とした幅広いコンテンツをご用意しております。
お問い合わせ
コストダウンが利益に直結する術だと理解していても、なかなか前に進めることができない状況。そんな時は、newjiのコストダウン自動化機能で大きく利益貢献しよう!
(Β版非公開)