- お役立ち記事
- A strategic approach to aim for the Japan Management Quality Award, which quality departments cannot afford to miss.
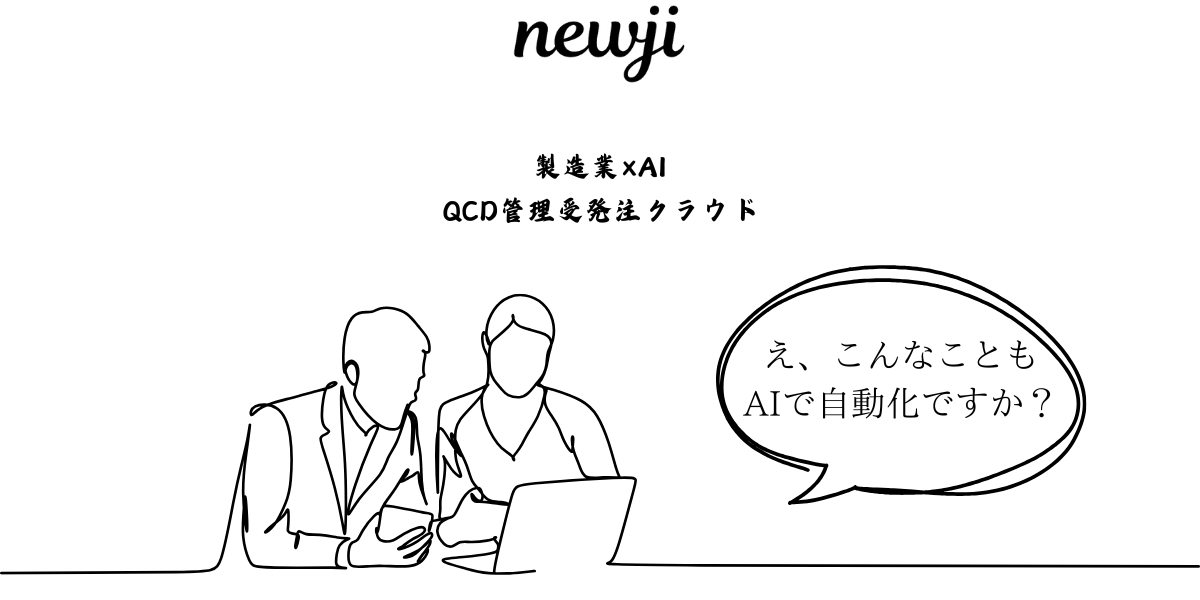
A strategic approach to aim for the Japan Management Quality Award, which quality departments cannot afford to miss.
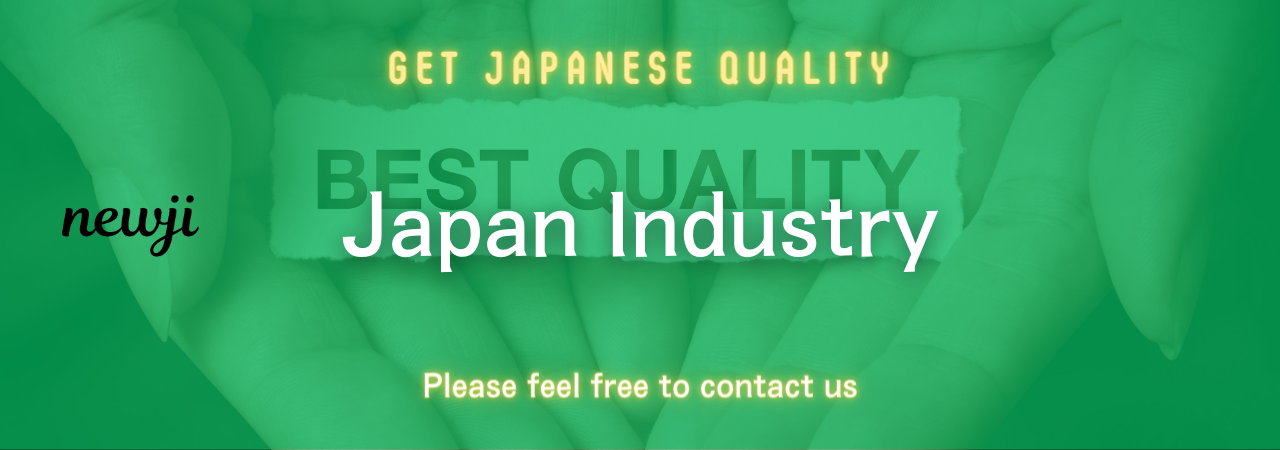
目次
Understanding the Japan Management Quality Award
The Japan Management Quality Award (JMQA) is highly revered in the field of business management across Japan.
It serves as a benchmark for organizations striving for excellence in management and operational quality.
The award is not only a recognition of outstanding management practices but also an opportunity for companies to drive continuous improvement and innovation.
Quality departments within organizations play a crucial role in steering their companies towards achieving this prestigious accolade.
The Importance of the JMQA
Winning the JMQA is a testament to an organization’s commitment to high management standards.
It signifies that a company has successfully integrated quality management principles into every aspect of its operations.
This award can enhance a company’s reputation, attract potential partnerships, and lead to a cemented trust among stakeholders.
For quality departments, understanding the significance of the JMQA is the first step in creating a roadmap to winning the award.
Integrating Quality Management Principles
To aim for the JMQA, quality departments must focus on integrating quality management principles into the company’s framework.
These principles are the foundation upon which exceptional management practices are built.
The effective use of tools like Total Quality Management (TQM), Six Sigma, and Lean management can propel a company towards improving its operational and management quality.
Teams need to be well-versed in these methodologies and how to apply them within their specific organizational context.
Aligning with Organizational Goals
Quality departments must ensure that quality initiatives are aligned with the organization’s overall goals and strategic objectives.
This alignment means working closely with other departments to understand broader business aims and how quality improvements can contribute to these aims.
A strategic approach involves understanding key performance indicators (KPIs) related to quality and devising plans to meet these benchmarks effectively.
Engaging Leadership and Employees
Securing top management’s commitment is crucial for any organization aiming for the JMQA.
Quality departments should communicate the benefits and importance of the award to leadership while emphasizing the role their commitment plays in achieving it.
Equally, rallying the entire workforce towards a shared vision of quality excellence can create a culture of quality that permeates through the organization.
Employee engagement initiatives and training programs can help instill quality-oriented mindsets across all levels.
Creating a Culture of Continuous Improvement
The pursuit of the JMQA mandates a culture of continuous improvement.
Innovation and evolution in practices should be encouraged to keep up with the dynamic nature of market demands and technologies.
Regular audits and feedback mechanisms can provide insights into areas for improvement and innovation.
By fostering an environment where feedback is encouraged and acted upon, an organization can effectively move towards the high standards required by the JMQA.
Comprehensive Evaluation and Benchmarking
A thorough evaluation process is fundamental in identifying the gaps in quality management practices.
Quality departments should regularly compare their practices against the JMQA criteria to identify areas needing improvement.
Benchmarking against other industries and organizations recognized for quality excellence can also provide valuable insights.
Using these evaluations as a basis, strategic improvements and innovations can be planned and implemented effectively.
Documenting and Reporting Progress
To demonstrate tangible progress towards meeting the criteria for the JMQA, a robust documentation process is essential.
Quality departments must meticulously record processes, improvements, outcomes, and lessons learned.
Transparent reporting mechanisms enable organizations to track their progress and adjust their strategies accordingly.
These records are also crucial for the application process for the award, where evidence of excellence in management quality is required.
The Application Process
Applying for the JMQA involves a comprehensive evaluation process where each aspect of an organization’s management practices is scrutinized.
Quality departments need to ensure that all documentation is in adherence to the award requirements.
A well-prepared application showcases the efforts and achievements of the company in maintaining superior management practices.
It’s important to clearly articulate how the company meets each award criterion, with documented evidence to support each claim.
Preparing for the Evaluation
Preparation for the evaluation stage is critical for any organization aspiring for the JMQA.
Quality departments should anticipate the rigorous assessment process and be well-prepared to present their best practices effectively.
Workshops, mock audits, and evaluation drills can help in preparing the organization for the final assessment.
By simulating the evaluation process, companies can ensure that every team member understands their role and is prepared for the questions and scrutiny they will face.
Conclusion: A Journey Toward Excellence
Aiming for the Japan Management Quality Award is more than just about achieving recognition; it’s a journey towards management excellence.
It involves a strategic approach by integrating quality management principles, aligning them with organizational goals, engaging leadership, and fostering a culture of improvement.
For quality departments, this journey is an opportunity to push the boundaries of their organization’s capabilities and create lasting value.
By striving for the JMQA, businesses not only aim to win an accolade but also cement their position as leaders in exceptional management quality.
資料ダウンロード
QCD調達購買管理クラウド「newji」は、調達購買部門で必要なQCD管理全てを備えた、現場特化型兼クラウド型の今世紀最高の購買管理システムとなります。
ユーザー登録
調達購買業務の効率化だけでなく、システムを導入することで、コスト削減や製品・資材のステータス可視化のほか、属人化していた購買情報の共有化による内部不正防止や統制にも役立ちます。
NEWJI DX
製造業に特化したデジタルトランスフォーメーション(DX)の実現を目指す請負開発型のコンサルティングサービスです。AI、iPaaS、および先端の技術を駆使して、製造プロセスの効率化、業務効率化、チームワーク強化、コスト削減、品質向上を実現します。このサービスは、製造業の課題を深く理解し、それに対する最適なデジタルソリューションを提供することで、企業が持続的な成長とイノベーションを達成できるようサポートします。
オンライン講座
製造業、主に購買・調達部門にお勤めの方々に向けた情報を配信しております。
新任の方やベテランの方、管理職を対象とした幅広いコンテンツをご用意しております。
お問い合わせ
コストダウンが利益に直結する術だと理解していても、なかなか前に進めることができない状況。そんな時は、newjiのコストダウン自動化機能で大きく利益貢献しよう!
(Β版非公開)