- お役立ち記事
- Accelerating Product Development with QFD: Innovation Strategies in Manufacturing
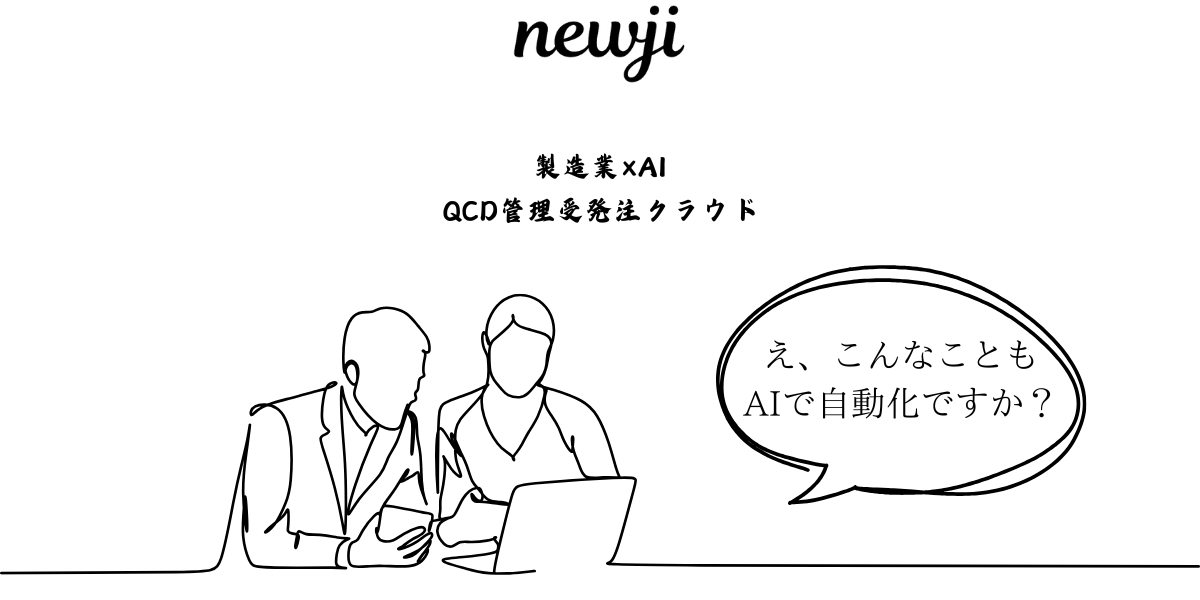
Accelerating Product Development with QFD: Innovation Strategies in Manufacturing
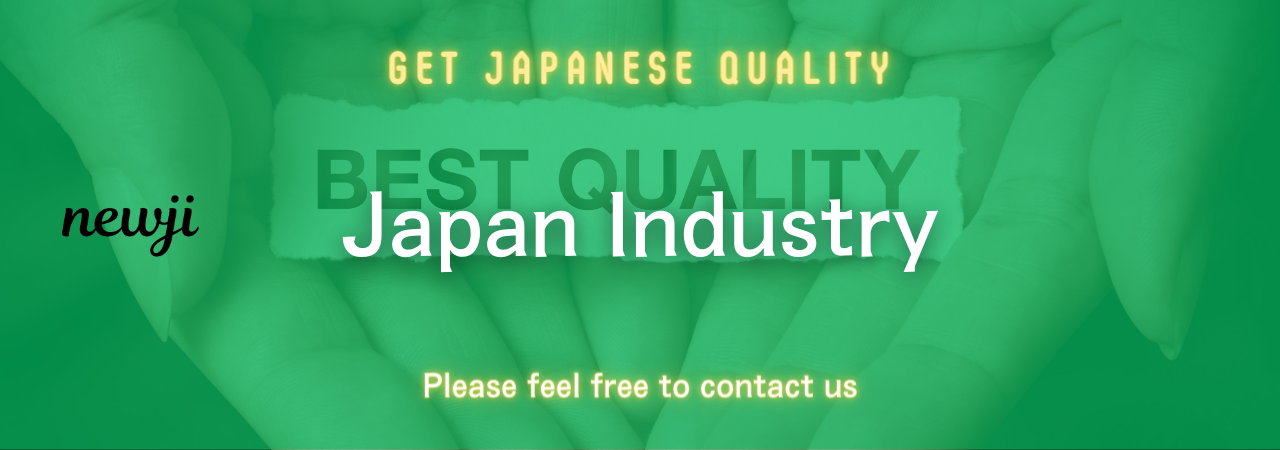
Quality Function Deployment (QFD) is a powerful tool in the world of product development that can significantly enhance innovation within the manufacturing sector.
This comprehensive methodology focuses on understanding and prioritizing customer needs to create superior products.
By accelerating product development with QFD, companies can achieve higher levels of efficiency, reduce development cycles, and ultimately deliver products that meet or exceed customer expectations.
Let’s dive into the intricacies of QFD and explore how it fosters innovation in manufacturing.
目次
Understanding Quality Function Deployment (QFD)
Quality Function Deployment is a structured approach that translates customer requirements into detailed engineering specifications and production plans.
It was first introduced in Japan in the late 1960s and has since gained widespread adoption across various industries.
By systematically capturing and analyzing customer needs, QFD ensures that products are designed with a customer-centric approach.
This not only increases customer satisfaction but also enhances overall product quality.
The QFD Process: An Overview
The QFD process typically involves several key phases.
Each phase is vital to ensure that the final product aligns closely with customer requirements.
Phase 1: Voice of the Customer (VoC)
The initial phase centers on gathering detailed information about what customers truly want and need.
This information can be obtained through various means such as surveys, interviews, focus groups, and market research.
Phase 2: Product Planning
Once customer needs are identified, they are translated into specific product characteristics.
This phase involves creating a House of Quality (HoQ), a matrix that links customer requirements to product features.
Phase 3: Product Design
In this phase, the team develops detailed engineering specifications and design parameters based on the HoQ.
These specifications guide the development and ensure that all customer requirements are met.
Phase 4: Process Planning
With the product design in place, the next step is to plan the manufacturing process.
This phase ensures that the designed product can be manufactured efficiently and effectively.
Phase 5: Production
The final phase involves the actual production of the product.
Continuous monitoring and quality control are essential to ensure that the product meets the desired standards.
Benefits of Using QFD in Manufacturing
QFD offers numerous benefits that make it a valuable tool in the product development arsenal.
Enhanced Customer Satisfaction
By directly incorporating customer feedback into the product design, QFD ensures that the final product meets or exceeds customer expectations.
This greatly enhances customer satisfaction and loyalty.
Improved Efficiency
QFD aids in identifying and addressing potential issues early in the development process, leading to faster development cycles and reduced time to market.
This improved efficiency can result in significant cost savings.
Higher Quality Products
With a focus on meeting detailed customer requirements, QFD helps in designing high-quality products.
This not only reduces the risk of product failures but also enhances brand reputation.
Better Team Collaboration
QFD fosters collaboration among various departments such as marketing, design, engineering, and manufacturing.
This integrated approach ensures that all team members are aligned and working towards a common goal.
Strategies to Accelerate Product Development with QFD
Incorporating QFD into the product development process can significantly accelerate the pace of innovation.
Here are some strategies to achieve this:
Engage Customers Early and Often
Involving customers early in the development process helps in gathering accurate and comprehensive requirements.
Regular feedback loops ensure that the product development stays aligned with customer expectations.
Use Cross-functional Teams
Forming cross-functional teams that include members from marketing, design, engineering, and manufacturing can greatly enhance collaboration.
These teams can work together to identify and resolve potential issues quickly, thereby speeding up the development process.
Utilize Advanced Tools and Technologies
Leveraging advanced tools such as CAD software, simulation models, and prototyping technologies can streamline the product design and testing phases.
These tools enable faster iterations and help in identifying issues before they become costly problems.
Implement Continuous Improvement Practices
Continuous improvement is a core principle of QFD.
Regularly reviewing and refining the QFD process ensures that the development team is always optimizing for better performance and efficiency.
Train Team Members
Providing training on QFD methodology for all team members ensures that everyone understands the process and its benefits.
This knowledge empowers the team to effectively apply QFD principles in their daily work.
Challenges and Solutions
While QFD offers numerous benefits, it also presents certain challenges that need to be addressed for successful implementation.
Challenge: Complexity of the QFD Process
QFD can be complex and time-consuming, especially for teams new to the methodology.
Solution: Simplified Tools and Training
Utilizing simplified QFD tools and providing comprehensive training can help teams understand and implement QFD more effectively.
Challenge: Resistance to Change
Teams might resist adopting a new methodology due to existing workflows and habits.
Solution: Leadership and Communication
Strong leadership and clear communication about the benefits of QFD can help in overcoming resistance and ensuring buy-in from all team members.
Conclusion
Accelerating product development with QFD is a strategic move that can significantly enhance innovation in manufacturing.
By focusing on customer needs, improving efficiency, and fostering team collaboration, QFD helps in creating high-quality products that stand out in the market.
While there are challenges, they can be effectively managed with the right strategies and commitment.
Embracing QFD can propel manufacturing companies towards a future of sustained innovation and success.
資料ダウンロード
QCD調達購買管理クラウド「newji」は、調達購買部門で必要なQCD管理全てを備えた、現場特化型兼クラウド型の今世紀最高の購買管理システムとなります。
ユーザー登録
調達購買業務の効率化だけでなく、システムを導入することで、コスト削減や製品・資材のステータス可視化のほか、属人化していた購買情報の共有化による内部不正防止や統制にも役立ちます。
NEWJI DX
製造業に特化したデジタルトランスフォーメーション(DX)の実現を目指す請負開発型のコンサルティングサービスです。AI、iPaaS、および先端の技術を駆使して、製造プロセスの効率化、業務効率化、チームワーク強化、コスト削減、品質向上を実現します。このサービスは、製造業の課題を深く理解し、それに対する最適なデジタルソリューションを提供することで、企業が持続的な成長とイノベーションを達成できるようサポートします。
オンライン講座
製造業、主に購買・調達部門にお勤めの方々に向けた情報を配信しております。
新任の方やベテランの方、管理職を対象とした幅広いコンテンツをご用意しております。
お問い合わせ
コストダウンが利益に直結する術だと理解していても、なかなか前に進めることができない状況。そんな時は、newjiのコストダウン自動化機能で大きく利益貢献しよう!
(Β版非公開)