- お役立ち記事
- Adjustment of Die Clearance in Press Forming and Its Effectiveness
Adjustment of Die Clearance in Press Forming and Its Effectiveness
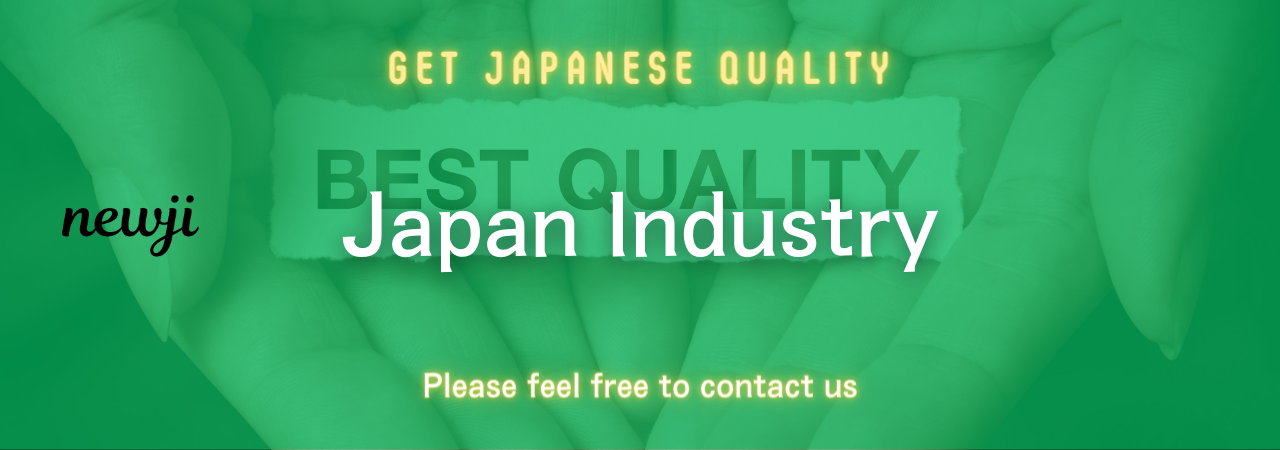
When it comes to press forming, a multitude of factors influence the final quality of the product.
One of the critical aspects is the adjustment of die clearance.
Understanding how to manipulate this can lead to significant improvements in product quality and manufacturing efficiency.
目次
What is Die Clearance in Press Forming?
Die clearance refers to the gap between the punch and the die in a press forming machine.
This gap is deliberate and designed for various purposes, such as reducing the pressure required to cut or shape the material.
Too little clearance can result in excessive wear and tear on the machinery, while too much clearance can lead to poor-quality products.
Therefore, finding the right balance is crucial for optimal performance.
Importance of Proper Die Clearance Adjustment
Material Integrity
Proper adjustment of die clearance ensures that the material retains its integrity.
Incorrect clearance can cause issues like tearing, warping, or other forms of deformation.
By maintaining the right gap, manufacturers can produce higher-quality parts that meet stringent industry standards.
Extended Tool Life
Another significant benefit of adjusting die clearance properly is the extended life of the tooling.
Excessive stress or friction caused by improper clearance can lead to premature wear and damage to both the punch and the die.
By optimizing die clearance, you minimize the need for frequent tool replacements, thereby reducing downtime and maintenance costs.
Efficient Material Utilization
Adjusting the die clearance appropriately ensures efficient use of raw materials.
This can help in minimizing waste, making the manufacturing process more sustainable and cost-effective.
Efficient material utilization also translates into lower production costs and higher profit margins.
How to Adjust Die Clearance for Maximum Effectiveness
Evaluate Material Type and Thickness
The type and thickness of the material greatly influence the required die clearance.
For instance, thinner materials generally need smaller clearances, while thicker materials require larger gaps.
Conducting tests to determine the optimal clearance for each material type and thickness can yield excellent results.
Use Proper Measurement Tools
Utilizing precise measurement tools is essential for accurate die clearance adjustment.
Calipers, micrometers, and feeler gauges are some of the common tools used for this purpose.
Ensuring that these tools are calibrated correctly will allow for precise adjustments, leading to better quality outcomes.
Utilize Software and Simulation
Modern manufacturing often employs software and simulation tools to predict and optimize die clearance settings.
These tools can provide invaluable insights by simulating various scenarios and suggesting the best clearance settings based on the results.
This can save both time and resources by removing much of the guesswork involved.
Challenges in Adjusting Die Clearance
Material Variation
One of the challenges in setting die clearance is the variation in material properties.
Sometimes, raw materials delivered may slightly differ from the specifications, affecting the ideal clearance.
Regularly testing batches of material can help identify and address these inconsistencies.
Tool Wear
As tools wear down over time, the optimal clearance settings may change.
Monitoring tool wear and making necessary adjustments to die clearance is essential for maintaining high-quality production.
Implementing a scheduled maintenance program can help catch and rectify these issues before they escalate.
Machine Precision
The precision of the press forming machine itself can impact the effectiveness of die clearance adjustments.
Machines that are not calibrated correctly or have mechanical issues can compromise the quality despite the best clearance settings.
Regular machine maintenance and calibration are crucial for ensuring consistency.
Case Studies: Real-World Applications
Automotive Industry
In the automotive industry, die clearance adjustment plays a pivotal role in the production of vehicle parts.
A major car manufacturer found that optimizing die clearance led to a 15% reduction in material waste and a 10% increase in production speed.
This translated to substantial cost savings and improved product quality.
Electronics Manufacturing
Electronic components often require precise tolerances.
A leading electronics manufacturer implemented a die clearance optimization program and saw a dramatic decrease in product defects.
This not only enhanced quality but also boosted their market reputation and customer trust.
Best Practices for Die Clearance Adjustment
Regular Training
Ensuring that staff involved in the adjustment and maintenance of die clearance are well-trained is essential.
Periodic training sessions can keep the team updated on the latest techniques and technologies, thereby ensuring consistent quality.
Implementing Feedback Loops
Feedback loops can be instrumental in adjusting die clearance.
Collecting data on production quality and tool wear can provide insights that allow for timely adjustments.
This proactive approach helps in maintaining high-quality standards and reduces the likelihood of defects.
Automation and Monitoring
Integrating automation and real-time monitoring systems can significantly enhance the efficiency of die clearance adjustment.
Automated systems can make minute adjustments in real-time, optimizing the process and improving overall quality.
In conclusion, the adjustment of die clearance in press forming is not just a technical requirement; it is a strategic imperative for quality and efficiency.
By understanding the principles and implementing best practices, manufacturers can achieve significant improvements in product quality and operational efficiency.
Whether it is in the automotive, electronics, or any other industry, paying attention to die clearance can yield substantial benefits.
資料ダウンロード
QCD調達購買管理クラウド「newji」は、調達購買部門で必要なQCD管理全てを備えた、現場特化型兼クラウド型の今世紀最高の購買管理システムとなります。
ユーザー登録
調達購買業務の効率化だけでなく、システムを導入することで、コスト削減や製品・資材のステータス可視化のほか、属人化していた購買情報の共有化による内部不正防止や統制にも役立ちます。
NEWJI DX
製造業に特化したデジタルトランスフォーメーション(DX)の実現を目指す請負開発型のコンサルティングサービスです。AI、iPaaS、および先端の技術を駆使して、製造プロセスの効率化、業務効率化、チームワーク強化、コスト削減、品質向上を実現します。このサービスは、製造業の課題を深く理解し、それに対する最適なデジタルソリューションを提供することで、企業が持続的な成長とイノベーションを達成できるようサポートします。
オンライン講座
製造業、主に購買・調達部門にお勤めの方々に向けた情報を配信しております。
新任の方やベテランの方、管理職を対象とした幅広いコンテンツをご用意しております。
お問い合わせ
コストダウンが利益に直結する術だと理解していても、なかなか前に進めることができない状況。そんな時は、newjiのコストダウン自動化機能で大きく利益貢献しよう!
(Β版非公開)