- お役立ち記事
- Application and effectiveness of the taguchi method in quality control in manufacturing
Application and effectiveness of the taguchi method in quality control in manufacturing
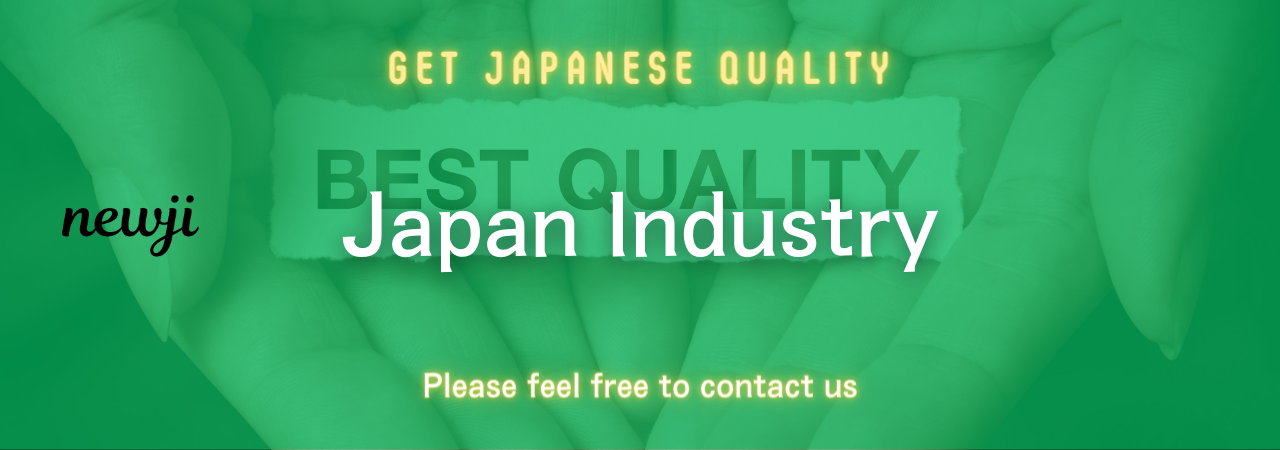
The Taguchi Method is a powerful tool used to improve the quality of products in manufacturing. It is named after Dr. Genichi Taguchi, who developed this method to make the production process more efficient and to reduce the variability and defects in products.
目次
What is the Taguchi Method?
The Taguchi Method is a statistical approach that focuses on optimizing the design and process of manufacturing to produce high-quality products at a lower cost. The main goal is to identify the factors that can affect the performance of a product and to find the best combination of these factors to achieve the desired quality.
Key Concepts of the Taguchi Method
One of the central aspects of the Taguchi Method is the use of orthogonal arrays to systematically and efficiently test the multiple variables that can affect production. This helps manufacturers determine which variables have the most significant impact on the product’s quality and which do not.
Benefits of Using the Taguchi Method
Applying the Taguchi Method in manufacturing comes with several key advantages. By focusing on reducing variability, manufacturers can ensure more consistent product quality. This can significantly reduce the costs associated with rework, scrap, and customer complaints.
Improved Product Quality
One of the most significant benefits of the Taguchi Method is improved product quality. By carefully selecting and testing different variables, manufacturers can identify the optimal conditions for producing their products. This ensures that the final products meet or exceed customer expectations in terms of performance and reliability.
Cost Savings
By reducing the variability in the production process, the Taguchi Method helps lower production costs. This is achieved through more efficient use of materials and resources, as well as a reduction in waste and defective products. With improved processes, manufacturers can also expect fewer delays and increased efficiency in the production line.
Enhanced Problem-Solving
The structured approach of the Taguchi Method enhances problem-solving capabilities within manufacturing processes. This method encourages a thorough understanding of the factors affecting production, enabling engineers to pinpoint and address issues more effectively.
Application of the Taguchi Method in Manufacturing
The application of the Taguchi Method involves a few key steps:
Step 1: Define the Problem
The first step is to clearly define the problem that needs to be addressed. This could be anything from reducing the number of defects in a product to improving the overall efficiency of the production process.
Step 2: Identify the Factors
Next, identify the various factors that could impact the product quality. These factors can include materials, machine settings, environmental conditions, and operator skills.
Step 3: Design the Experiment
Using orthogonal arrays, design an experiment that systematically tests the different combinations of factors. This step allows manufacturers to understand the interactions between the variables and how they affect the outcome.
Step 4: Conduct the Experiment
Conduct the experiments as per the designed orthogonal array. Collect data and measure the outcomes for each combination of factors.
Step 5: Analyze the Data
Analyze the experimental data to identify the optimal combination of factors that will produce the best results. Statistical analysis tools are often used at this stage to ensure accuracy.
Step 6: Implement the Optimal Conditions
Finally, implement the optimal conditions identified through the analysis in the manufacturing process. This will help to achieve the highest possible quality and efficiency in production.
Real-World Examples
Many renowned companies have successfully used the Taguchi Method to enhance their manufacturing processes.
Toyota
Toyota, a global leader in automobile manufacturing, has extensively applied the Taguchi Method in its production lines. By identifying and optimizing critical factors, Toyota has been able to produce vehicles with exceptional quality and reliability.
Motorola
Motorola used the Taguchi Method to significantly improve the quality of its electronic products. By systematically evaluating and optimizing various factors, Motorola successfully reduced defects and enhanced product performance.
Conclusion
The Taguchi Method is a transformative tool for manufacturers, offering a structured approach to optimize production processes and improve product quality. By focusing on identifying and optimizing critical factors, manufacturers can reduce variability, minimize production costs, and enhance overall efficiency. Real-world applications from companies like Toyota and Motorola showcase the effectiveness of this method in delivering high-quality products. Implementing the Taguchi Method can lead to significant improvements in manufacturing outcomes, benefiting both the producers and their customers.
資料ダウンロード
QCD調達購買管理クラウド「newji」は、調達購買部門で必要なQCD管理全てを備えた、現場特化型兼クラウド型の今世紀最高の購買管理システムとなります。
ユーザー登録
調達購買業務の効率化だけでなく、システムを導入することで、コスト削減や製品・資材のステータス可視化のほか、属人化していた購買情報の共有化による内部不正防止や統制にも役立ちます。
NEWJI DX
製造業に特化したデジタルトランスフォーメーション(DX)の実現を目指す請負開発型のコンサルティングサービスです。AI、iPaaS、および先端の技術を駆使して、製造プロセスの効率化、業務効率化、チームワーク強化、コスト削減、品質向上を実現します。このサービスは、製造業の課題を深く理解し、それに対する最適なデジタルソリューションを提供することで、企業が持続的な成長とイノベーションを達成できるようサポートします。
オンライン講座
製造業、主に購買・調達部門にお勤めの方々に向けた情報を配信しております。
新任の方やベテランの方、管理職を対象とした幅広いコンテンツをご用意しております。
お問い合わせ
コストダウンが利益に直結する術だと理解していても、なかなか前に進めることができない状況。そんな時は、newjiのコストダウン自動化機能で大きく利益貢献しよう!
(Β版非公開)