- お役立ち記事
- Application of TPM (Total Productive Maintenance) to the manufacturing industry
Application of TPM (Total Productive Maintenance) to the manufacturing industry
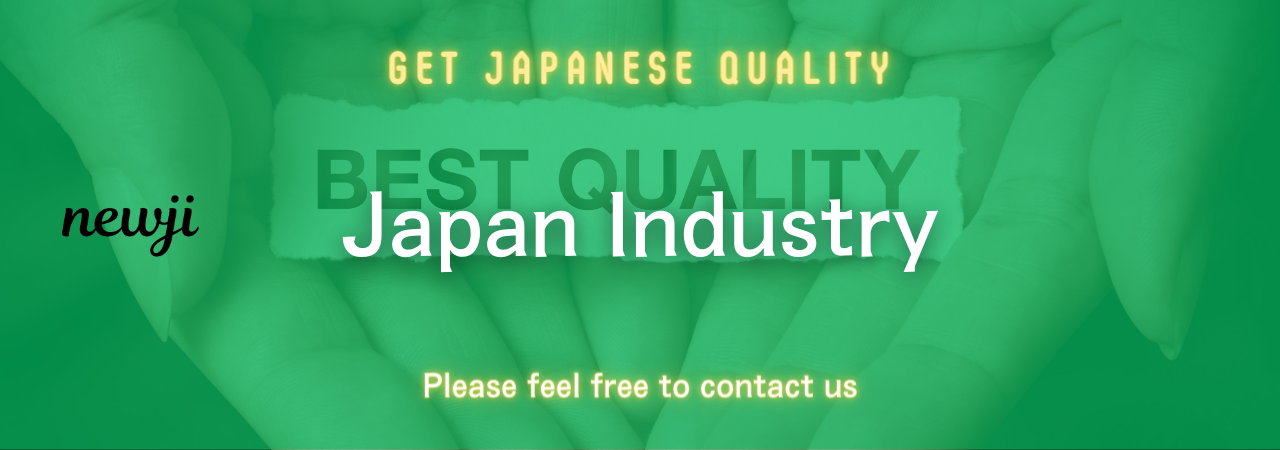
目次
Understanding Total Productive Maintenance
Total Productive Maintenance, often abbreviated as TPM, is a holistic approach designed to enhance the productivity and efficiency of the manufacturing sector.
It’s not just about maintaining equipment; it’s a comprehensive method that involves everyone in the organization to contribute to the upkeep of machinery and processes.
The ultimate goal is to improve overall equipment effectiveness (OEE) and eliminate production losses.
The Core Pillars of TPM
TPM is built upon eight foundational pillars, each of which plays a critical role in achieving production efficiency.
Let’s delve into these pillars to understand their significance.
1. Autonomous Maintenance
Operators are given the responsibility to maintain their equipment daily.
This means cleaning, inspecting, and undertaking minor repairs.
By empowering operators, it reduces downtime and ensures that issues are identified and addressed swiftly.
2. Planned Maintenance
This involves scheduling and performing maintenance activities based on equipment usage and historical performance data.
It prevents unexpected breakdowns and extends the life of machinery.
3. Quality Maintenance
Here, the focus is on maintaining the quality of the products manufactured.
Any variations in production processes are identified and rectified to ensure the final product meets quality standards.
4. Focused Improvement
This pillar encourages small, incremental improvements.
Teams work together to identify inefficiencies and implement changes to optimize processes continuously.
5. Early Equipment Management
The introduction of new equipment is crucial.
This pillar emphasizes the importance of designing machinery that is easy to operate and maintain.
By involving maintenance and operations teams in the design phase, potential issues are minimized.
6. Education and Training
Continuous education and training ensure that everyone from operators to managers is equipped with the necessary skills to maintain efficiency.
Well-trained employees can handle equipment more effectively and address issues promptly.
7. Safety, Health, and Environment
A safe working environment is paramount.
This pillar focuses on creating safe and healthy working conditions and reducing the environmental impact.
Safety is integrated into every aspect of the manufacturing process.
8. TPM in Administration
The administrative aspect of TPM ensures that support functions such as procurement, finance, and HR are aligned with production goals.
Streamlining these operations enhances overall productivity.
Benefits of Implementing TPM
The manufacturing industry can reap many benefits from implementing TPM.
These advantages extend beyond just improved equipment efficiency.
Increased Equipment Availability
By adopting TPM, machinery is maintained more effectively, reducing unexpected breakdowns and increasing operational uptime.
This means less interruption in production and higher equipment availability.
Enhanced Product Quality
Consistent maintenance ensures that manufacturing processes run smoothly.
As a result, product defects decline, leading to higher quality output and customer satisfaction.
Cost Reduction
With fewer breakdowns and defects, the costs associated with repairs, rework, and scrap materials decrease significantly.
Moreover, efficient machinery uses less energy, reducing utility bills.
Employee Morale and Engagement
TPM fosters a sense of ownership among employees as they are actively involved in maintaining and improving the production processes.
This increases job satisfaction and reduces employee turnover.
Increased Overall Productivity
With equipment running efficiently and fewer disruptions in production, the overall productivity of the manufacturing process improves.
This leads to higher output and potentially increased profits.
Steps to Implement TPM in the Manufacturing Industry
While the benefits are clear, the implementation of TPM requires a structured approach.
Here are the steps to effectively incorporate TPM into a manufacturing setup.
Step 1: Initial Assessment
Conduct a comprehensive assessment of current equipment and processes.
Identify areas with frequent breakdowns and inefficiencies.
This baseline evaluation helps determine where to focus initial efforts.
Step 2: Form a TPM Team
Create a cross-functional team that includes members from various departments such as maintenance, operations, and quality assurance.
This team will lead the TPM initiatives and ensure company-wide participation.
Step 3: Training and Awareness
Educate all employees about TPM principles and the importance of their roles in the process.
Provide specialized training to ensure they have the skills needed to perform maintenance and improvement tasks.
Step 4: Develop a Roadmap
Create a clear roadmap detailing the steps for implementing TPM, including timelines, milestones, and responsibilities.
This plan should be realistic and include provisions for ongoing evaluation and adjustment.
Step 5: Implement Autonomous Maintenance
Begin with autonomous maintenance practices, where operators take charge of daily maintenance tasks.
Provide them with the necessary tools and training.
Step 6: Establish Planned Maintenance
Set up a scheduled maintenance plan based on equipment usage and performance data.
This should include routine inspections and preventive measures to avoid unexpected failures.
Step 7: Focus on Continuous Improvement
Encourage teams to identify potential improvements continuously.
Implement small changes and measure their impact on production processes.
Step 8: Monitor and Adjust
Regularly review the progress of TPM initiatives.
Use key performance indicators (KPIs) to measure success and make adjustments as necessary to keep the program on track.
Challenges in Implementing TPM
While TPM offers numerous benefits, the implementation process can present challenges.
Being aware of these obstacles helps in devising strategies to overcome them.
Resistance to Change
Employees may be resistant to new practices and roles.
To mitigate this, ensure clear communication about the benefits of TPM and involve employees in decision-making processes.
Training Requirements
TPM requires continuous education, which can be resource-intensive.
Investing in a strong training program is crucial for long-term success.
Initial Costs
The initial setup of TPM, including training, new tools, and equipment modifications, can be costly.
However, the long-term benefits and cost savings typically outweigh these initial expenses.
Consistency in Implementation
Maintaining consistency in TPM practices across departments can be challenging.
Regular audits and reviews help ensure that all teams adhere to TPM principles.
Conclusion
Implementing Total Productive Maintenance in the manufacturing industry is a strategic move that can yield significant benefits.
From increasing equipment efficiency to boosting employee morale and reducing costs, TPM offers a comprehensive solution to many manufacturing challenges.
While the implementation process requires dedication and effort, the long-term gains in productivity, quality, and profitability make it a worthwhile investment.
By understanding the core pillars and carefully planning the implementation steps, manufacturers can successfully integrate TPM into their operations and achieve sustained improvements.
資料ダウンロード
QCD調達購買管理クラウド「newji」は、調達購買部門で必要なQCD管理全てを備えた、現場特化型兼クラウド型の今世紀最高の購買管理システムとなります。
ユーザー登録
調達購買業務の効率化だけでなく、システムを導入することで、コスト削減や製品・資材のステータス可視化のほか、属人化していた購買情報の共有化による内部不正防止や統制にも役立ちます。
NEWJI DX
製造業に特化したデジタルトランスフォーメーション(DX)の実現を目指す請負開発型のコンサルティングサービスです。AI、iPaaS、および先端の技術を駆使して、製造プロセスの効率化、業務効率化、チームワーク強化、コスト削減、品質向上を実現します。このサービスは、製造業の課題を深く理解し、それに対する最適なデジタルソリューションを提供することで、企業が持続的な成長とイノベーションを達成できるようサポートします。
オンライン講座
製造業、主に購買・調達部門にお勤めの方々に向けた情報を配信しております。
新任の方やベテランの方、管理職を対象とした幅広いコンテンツをご用意しております。
お問い合わせ
コストダウンが利益に直結する術だと理解していても、なかなか前に進めることができない状況。そんな時は、newjiのコストダウン自動化機能で大きく利益貢献しよう!
(Β版非公開)