- お役立ち記事
- “Automation Line and Layout Design” for Doubling Productivity: Practical Improvements and Layout Design for Factory Automation Before Robot Implementation
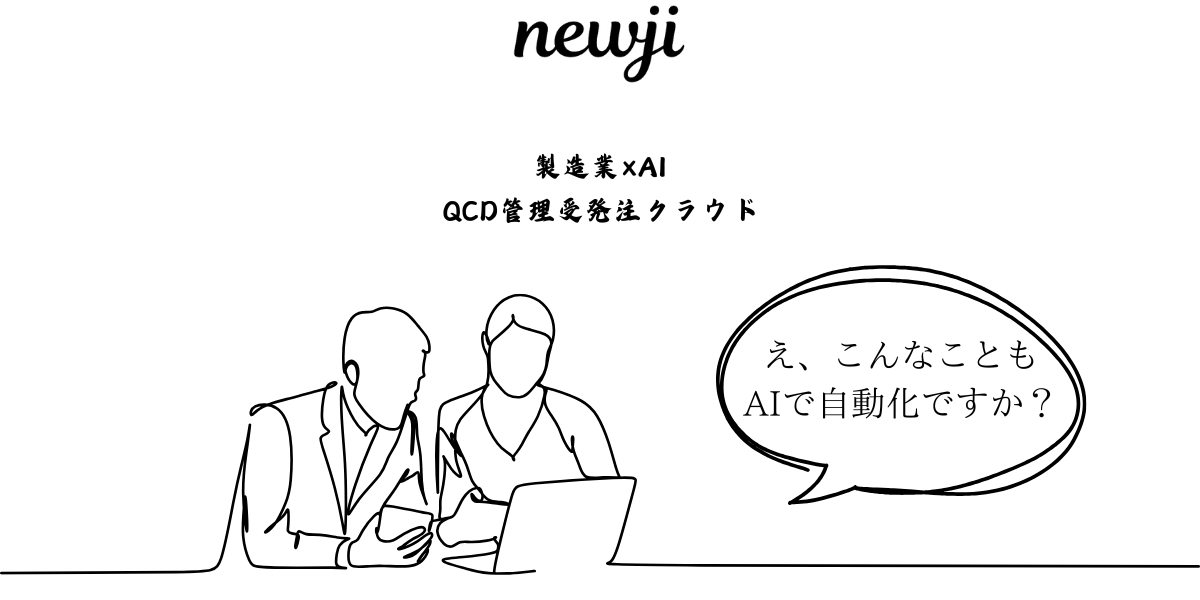
“Automation Line and Layout Design” for Doubling Productivity: Practical Improvements and Layout Design for Factory Automation Before Robot Implementation
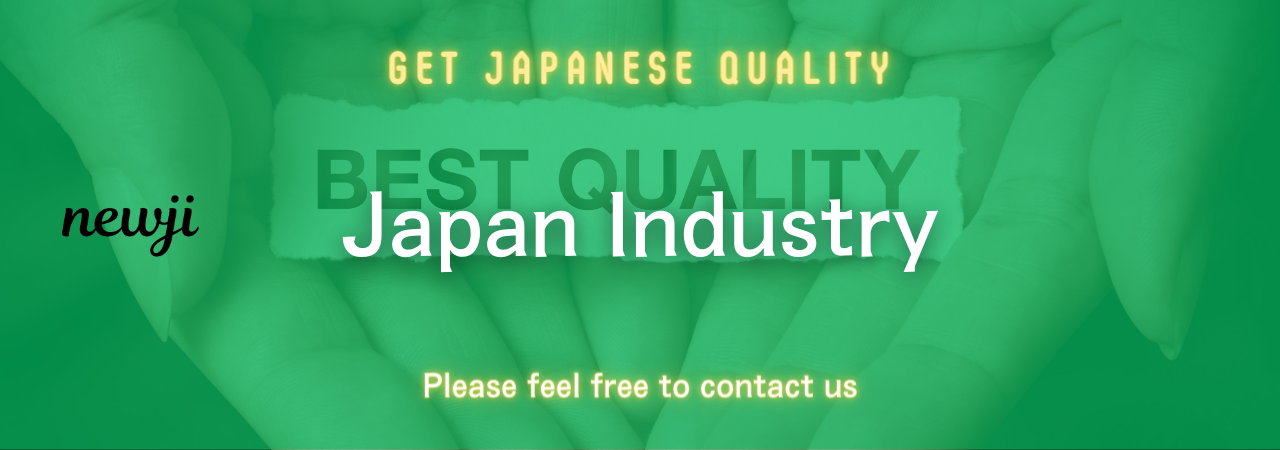
目次
Understanding Automation Line and Layout Design
Before diving into the world of robotics, it’s essential to first grasp the fundamentals of automation line and layout design.
Often, businesses rush into implementing robots hoping for immediate productivity boosts.
While robots are indeed transformative, their full potential can only be harnessed when the underlying automation lines and layouts are optimized.
Properly designed automation lines form the backbone of a robotic operation, providing consistency, efficiency, and reliability.
Initial Steps towards Effective Layout Design
Assessing Current Operations
Begin by evaluating your current operational setup.
This involves studying the flow of materials, the movement of workers, the placement of machinery, and the overall environment.
Identify any bottlenecks, redundant movements, or poorly utilized spaces.
A careful examination will present areas ripe for improvement.
Mapping Out the Workflow
Creating a detailed workflow diagram is crucial.
This visual representation of your current processes highlights inefficiencies.
This diagram should depict every step in the production process, from raw material intake to the finished product.
Include paths taken by materials and personnel to spot unnecessary crossings and delays.
Setting Clear Objectives
Determine what you aim to achieve with your automation line and layout design.
Are you looking to reduce production time?
Do you need to minimize waste?
Or perhaps you’re aiming to improve worker safety and ergonomics?
Clearly defining your goals will guide your design choices and ensure that every change aligns with your overall strategy.
Design Principles for Efficient Automation Lines
Simplicity and Consistency
Keep your design as simple as possible.
Complex layouts can lead to confusion, errors, and higher maintenance costs.
Consistency in layout ensures that workers can easily navigate the space and understand the process flow without extensive training.
Minimize Movement
One of the main objectives of a well-designed automation line is to minimize movement—both of materials and workers.
Strategically place machinery and workstations to create a smooth, linear flow of materials.
Reducing unnecessary movements not only speeds up production but also reduces the chances of errors and accidents.
Flexible Design
Flexibility is key in today’s fast-changing manufacturing environment.
Design your layout to be adaptable to future changes in product lines or volume increases.
Modular setups and easily reconfigurable workstations are excellent approaches to achieving flexibility.
Incorporating Lean Manufacturing Principles
Lean manufacturing principles can significantly influence effective automation line and layout design.
These principles focus on maximizing value while minimizing waste.
Incorporating them into your design process ensures more efficient operations.
Value Stream Mapping
Value stream mapping (VSM) is a lean tool that helps visualize the flow of materials and information through your production process.
It highlights value-adding and non-value-adding activities, making it easier to identify areas for improvement.
By integrating VSM into your design process, you ensure that every step of your layout contributes to the overall value of your product.
Just-In-Time Production
Just-in-time (JIT) production aims to produce only what is needed, when it’s needed, and in the amount needed.
Designing your layout for JIT means reducing inventory, cutting down on storage space, and ensuring a steady flow of materials through your automation line.
Technology Integration for Enhanced Performance
While robots may be the final piece in the automation puzzle, various other technologies can improve your automation line and layout before introducing robots.
Automated Guided Vehicles (AGVs)
AGVs are excellent for material handling, reducing the need for manual transport.
They can move materials efficiently through your facility, following predefined paths.
Integrating AGVs into your layout design enhances material flow and reduces the need for fixed conveyor systems.
Sensors and IoT Devices
Incorporating sensors and IoT devices within your automation line allows for real-time monitoring of processes, equipment health, and production metrics.
These devices provide valuable data that can be used to fine-tune your layout and ensure optimal performance.
Predictive maintenance, enabled by IoT, further reduces downtime and extends the lifespan of your machinery.
Real-World Examples of Successful Layout Designs
Real-world examples provide practical insights into the application of these principles.
Case Study: Automotive Industry
In the automotive industry, Toyota’s production system exemplifies effective automation line and layout design.
Toyota’s assembly lines are renowned for their efficiency, simplicity, and adherence to lean principles.
Their layout ensures minimal movement and clear, standardized processes, resulting in high productivity and low defect rates.
Case Study: Food and Beverage Industry
Another sector that benefits greatly from well-designed automation lines and layouts is the food and beverage industry.
One example is a leading beverage manufacturer that restructured its layout to integrate AGVs and conveyors, drastically reducing the time taken to move raw materials to production lines and finished products to storage.
The result was a significant boost in production capacity and a reduction in operational costs.
Final Thoughts on Pre-Robot Implementation
Investing in automation line and layout design before incorporating robots is a strategic move that can double productivity.
A thorough evaluation and restructuring of your current operations ensure that when robots are introduced, they operate in the most efficient environment possible.
Using principles of simplicity, lean manufacturing, and flexibility, along with integrating technologies like AGVs and IoT, will set the stage for successful automation.
Remember, the goal is not just to employ robots but to create a harmonious, efficient, and productive environment where robots can thrive.
Careful planning and thoughtful design are the building blocks of a successful robotic future in manufacturing.
資料ダウンロード
QCD調達購買管理クラウド「newji」は、調達購買部門で必要なQCD管理全てを備えた、現場特化型兼クラウド型の今世紀最高の購買管理システムとなります。
ユーザー登録
調達購買業務の効率化だけでなく、システムを導入することで、コスト削減や製品・資材のステータス可視化のほか、属人化していた購買情報の共有化による内部不正防止や統制にも役立ちます。
NEWJI DX
製造業に特化したデジタルトランスフォーメーション(DX)の実現を目指す請負開発型のコンサルティングサービスです。AI、iPaaS、および先端の技術を駆使して、製造プロセスの効率化、業務効率化、チームワーク強化、コスト削減、品質向上を実現します。このサービスは、製造業の課題を深く理解し、それに対する最適なデジタルソリューションを提供することで、企業が持続的な成長とイノベーションを達成できるようサポートします。
オンライン講座
製造業、主に購買・調達部門にお勤めの方々に向けた情報を配信しております。
新任の方やベテランの方、管理職を対象とした幅広いコンテンツをご用意しております。
お問い合わせ
コストダウンが利益に直結する術だと理解していても、なかなか前に進めることができない状況。そんな時は、newjiのコストダウン自動化機能で大きく利益貢献しよう!
(Β版非公開)