- お役立ち記事
- Basic Knowledge of Wire Electrical Discharge Machining in Machining Centers
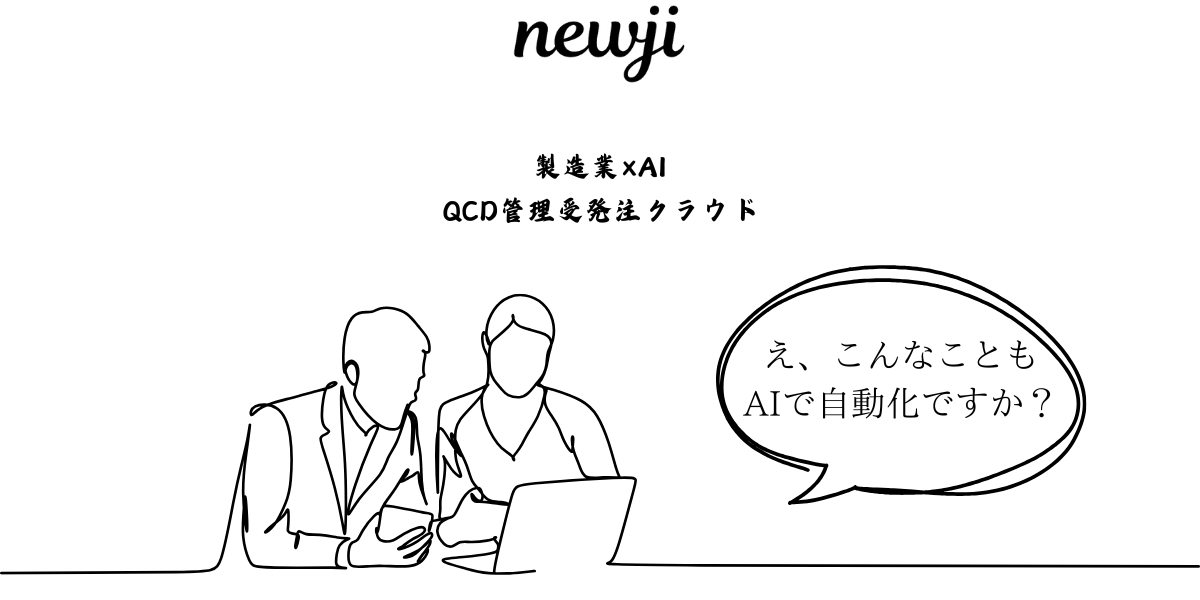
Basic Knowledge of Wire Electrical Discharge Machining in Machining Centers
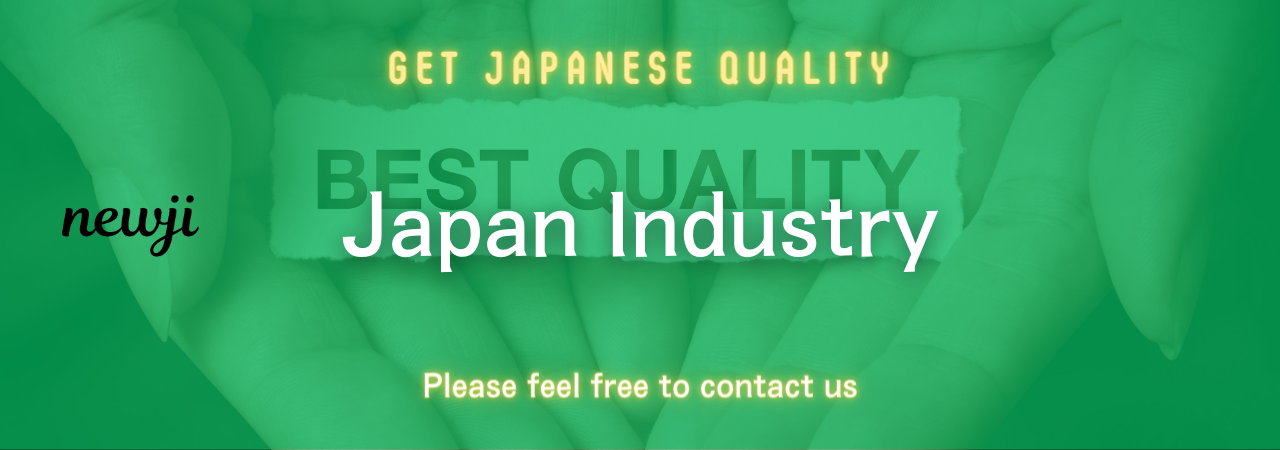
目次
Understanding Wire Electrical Discharge Machining (EDM)
Wire Electrical Discharge Machining, often abbreviated as Wire EDM, is a unique and sophisticated process used in machining centers to cut intricate designs and shapes in hard metals and other materials.
Wire EDM uses electrical discharges, or sparks, to cut through materials, unlike traditional cutting tools such as saws or drills.
This process involves a wire made of conductive material, typically brass or tungsten, that acts as an electrode.
During the process, an electrical current passes between the wire and the workpiece, generating a series of rapid, controlled electrical discharges.
These discharges occur in a dielectric fluid, which cools the material and carries away eroded particles.
The precision of Wire EDM allows for the creation of complex shapes with tight tolerances, which is particularly beneficial for industries such as aerospace, medical devices, and tool manufacturing.
How Wire EDM Works
To grasp how Wire EDM operates, it’s essential to understand its setup and function.
A thin wire is tensioned between guides, and the machine moves the workpiece along controlled paths dictated by numerical control systems or CNC.
As the wire approaches the workpiece, electrical pulses are released, which create intense heat and vaporize small particles of the material.
The dielectric fluid, usually deionized water, plays a critical role in the machine’s operation.
It acts as a coolant, preventing heat buildup that could potentially damage the workpiece.
Additionally, the fluid serves as an insulator to ensure electrical discharge happens only in the intended areas.
The wire itself doesn’t make direct contact with the workpiece, preventing any mechanical stress or distortion—crucial for maintaining the integrity of complex or delicate designs.
Advantages of Wire EDM
Wire EDM boasts several advantages that make it an ideal choice for specific applications:
1. **Precision and Accuracy**: EDM can achieve extremely tight tolerances, often in the micrometer range.
This level of precision is vital for high-tech industries where accuracy is paramount.
2. **Complex Shapes**: The process can cut intricate and complex shapes that would be challenging or impossible with conventional machining techniques.
3. **Hard Materials**: Wire EDM can cut through hard materials, including hardened steels and superalloys, without the wear typical in traditional cutting tools.
4. **No Tool Wear**: Since there’s no physical contact, the wire doesn’t experience wear as seen in traditional cutting processes.
5. **Smooth Finishes**: The resulting surface finish is smooth, reducing the need for additional finishing processes.
Applications of Wire EDM
Wire EDM is utilized across various industries due to its distinctive benefits:
– **Aerospace**: In manufacturing components like turbine blades, where intricate shapes and high precision are required.
– **Medical Devices**: For producing surgical tools and implants that demand high accuracy and are often made from tough materials.
– **Tool and Die Making**: To produce dies and molds with complex geometries.
– **Automotive**: In the creation of high-performance components requiring intricate shapes and durable construction.
Each of these applications leverages the wire EDM’s ability to handle complex geometries and maintain dimensional accuracy, ensuring the final product meets stringent industry standards.
Challenges and Considerations
While Wire EDM offers numerous advantages, certain challenges and considerations must be acknowledged.
Material and Thickness Limitations
Wire EDM is effective primarily on conductive materials.
Non-conductive materials cannot be processed directly without additional techniques, such as coating with a conductive layer.
Moreover, while Wire EDM can process various material thicknesses, very thick pieces might require extended processing times or multiple setups, which could increase costs and lead times.
Wire Consumption and Costs
Wire EDM involves continuous wire consumption, which can become a significant expense, especially in large production runs.
Selecting the appropriate wire material and diameter is crucial to balance cost and cutting efficiency.
Surface Integrity
One potential concern with Wire EDM is the impact on surface integrity due to thermal stresses during the cutting process.
Although EDM generally produces smooth finishes, the presence of micro-cracks or a heat-affected zone on the surface of the workpiece can occasionally occur, necessitating additional finishing operations.
Future Trends in Wire EDM
As technology continues to advance, the capabilities of Wire EDM are expanding, offering new possibilities and improvements in various industries.
Enhanced Automation
The integration of advanced computer control systems and automation is becoming increasingly prevalent in Wire EDM machines.
These systems enhance precision and reduce manual intervention, facilitating more efficient and reliable operations, especially in environments where high-volume production is essential.
Improved Wire Materials
Research and development in wire materials aim to reduce wire costs, increase cutting speeds, and improve performance on challenging materials.
Advancements may lead to longer-lasting wires, reducing operational downtime and expenses.
Environmental Considerations
Efforts to minimize the environmental impact of Wire EDM involve optimizing dielectric fluid usage and disposal.
Innovations in eco-friendly dielectric fluids are underway, aligning with broader sustainability goals in manufacturing.
Conclusion
Wire Electrical Discharge Machining represents a vital component of modern machining centers, offering unmatched precision and capabilities for complex and challenging cutting tasks.
As industries continue to pursue greater accuracy and complexity in their products, Wire EDM will remain a crucial tool, driven by technological advancements and evolving industry needs.
Understanding the basics and staying informed about the latest trends can ensure that manufacturers make the most of this innovative machining process.
資料ダウンロード
QCD調達購買管理クラウド「newji」は、調達購買部門で必要なQCD管理全てを備えた、現場特化型兼クラウド型の今世紀最高の購買管理システムとなります。
ユーザー登録
調達購買業務の効率化だけでなく、システムを導入することで、コスト削減や製品・資材のステータス可視化のほか、属人化していた購買情報の共有化による内部不正防止や統制にも役立ちます。
NEWJI DX
製造業に特化したデジタルトランスフォーメーション(DX)の実現を目指す請負開発型のコンサルティングサービスです。AI、iPaaS、および先端の技術を駆使して、製造プロセスの効率化、業務効率化、チームワーク強化、コスト削減、品質向上を実現します。このサービスは、製造業の課題を深く理解し、それに対する最適なデジタルソリューションを提供することで、企業が持続的な成長とイノベーションを達成できるようサポートします。
オンライン講座
製造業、主に購買・調達部門にお勤めの方々に向けた情報を配信しております。
新任の方やベテランの方、管理職を対象とした幅広いコンテンツをご用意しております。
お問い合わせ
コストダウンが利益に直結する術だと理解していても、なかなか前に進めることができない状況。そんな時は、newjiのコストダウン自動化機能で大きく利益貢献しよう!
(Β版非公開)