- お役立ち記事
- Basics and applications of the LEAN production method that new employees in the production technology department of the pharmaceutical manufacturing industry should know
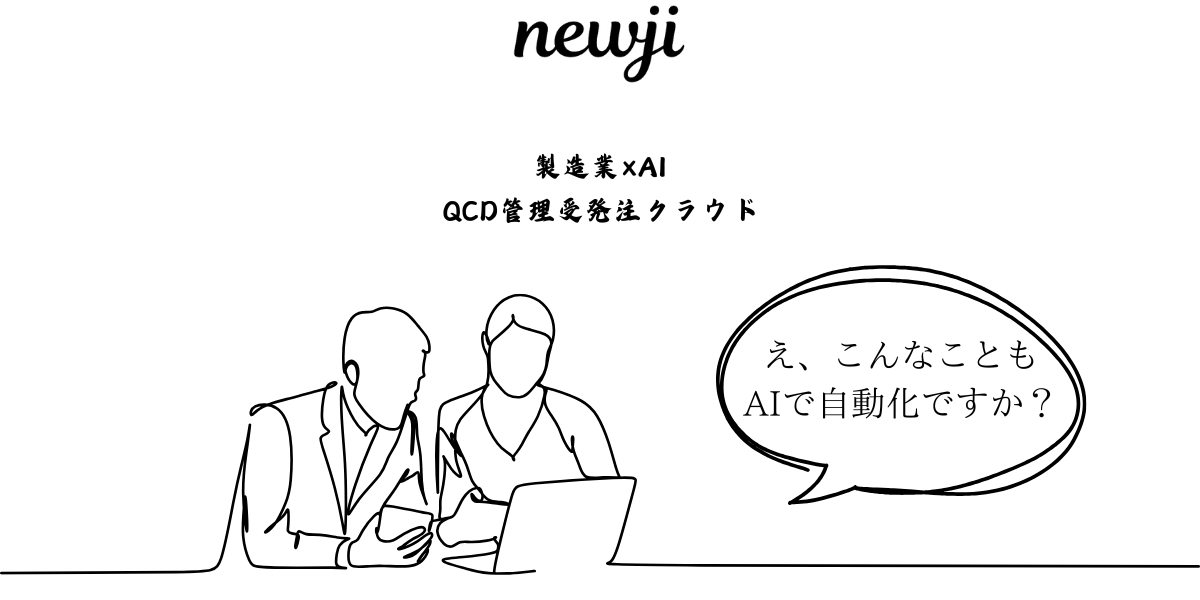
Basics and applications of the LEAN production method that new employees in the production technology department of the pharmaceutical manufacturing industry should know
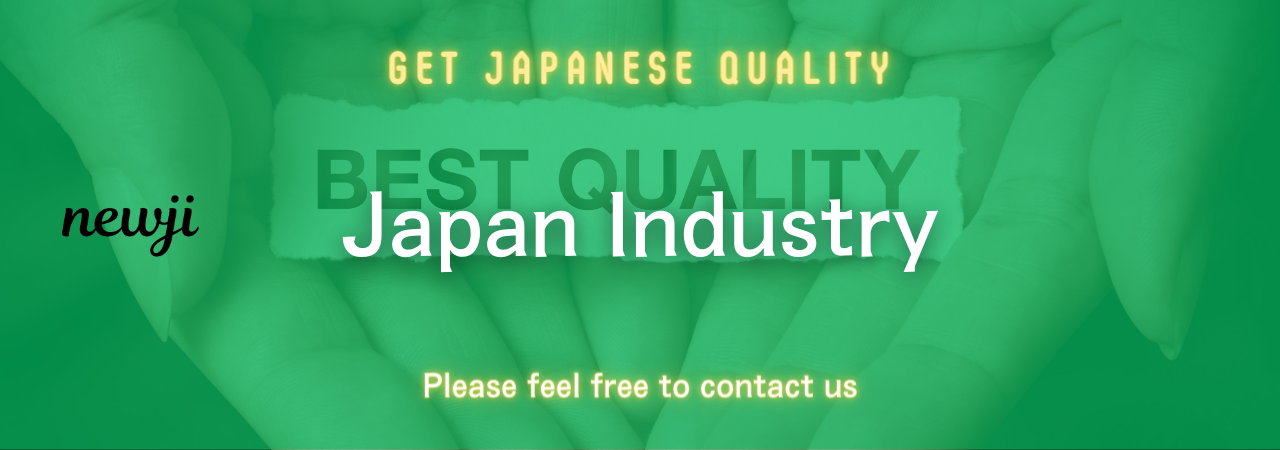
目次
Understanding the Basics of the LEAN Production Method
New employees in the production technology department of the pharmaceutical manufacturing industry often face the challenge of familiarizing themselves with various production methodologies.
Among these, the LEAN production method stands out due to its effectiveness in optimizing processes and enhancing productivity.
Originally developed by Toyota, LEAN has now transcended its automotive roots, finding significant applications in industries such as pharmaceuticals.
Let’s dive into the basics of the LEAN production method and understand why it is vital for new employees in this field.
What is LEAN Production?
At its core, the LEAN production method is centered around maximizing value for the customer while minimizing waste.
The aim is to create more value with fewer resources, focusing on efficiency across the entire production process.
In the context of pharmaceuticals, this means reducing waste, streamlining processes, and ensuring that each step in drug production adds value.
The result is not only an efficient production process but also improved quality of pharmaceutical products and faster delivery to the market.
The Principles of LEAN Production
To grasp the LEAN production method, one must first understand its five fundamental principles.
These principles serve as a guiding framework for implementing LEAN in any organization:
1. **Value**: Determine what constitutes value from the customer’s perspective.
In pharmaceuticals, this might mean effective medication, on-time delivery, or affordable prices.
2. **Value Stream**: Identify all the steps in the process that create value and eliminate those that do not.
Mapping the value stream helps visualize where inefficiencies lie.
3. **Flow**: Ensure that the production steps flow smoothly without interruptions, delays, or bottlenecks.
This might involve rearranging processes or tasks to improve efficiency.
4. **Pull**: Adopt a pull-based production system where processes are initiated based on demand, not forecasts.
This prevents overproduction, a common issue in pharmaceutical manufacturing.
5. **Perfection**: Continually strive for perfection by improving processes and systems, ensuring all waste is eliminated over time.
Applications of LEAN in Pharmaceutical Manufacturing
While the LEAN production method is invaluable across various industries, its application in pharmaceutical manufacturing comes with unique advantages and challenges.
Benefits of LEAN in Pharmaceuticals
The application of LEAN principles in the pharmaceutical industry offers several benefits:
– **Improved Quality**: By focusing on processes that add value, LEAN helps ensure the highest quality standards in drug production.
– **Reduced Waste**: Minimizing waste is crucial in pharmaceuticals, where resources like raw materials and time are precious.
– **Increased Productivity**: Streamlined processes mean that production units can achieve more output with the same or fewer resources.
– **Faster Time-to-Market**: Efficient operations ensure that medications reach consumers rapidly, crucial in times of health crises.
Challenges and Solutions
Implementing LEAN methodologies isn’t without its challenges, especially in the complex environment of pharmaceutical manufacturing.
However, recognizing common hurdles and adapting strategies is critical for successful LEAN implementation:
– **Regulatory Compliance**: The pharmaceutical industry is heavily regulated, which can sometimes clash with LEAN’s flexible approach.
Maintaining compliance while streamlining processes requires a careful balance.
– **Cultural Shift**: Transitioning to a LEAN culture necessitates a mindset change across the organization.
Education and training are vital for employees to embrace and effectively apply LEAN principles.
– **Flexibility vs. Rigidity**: LEAN requires a flexible approach to problem-solving, which can be at odds with the rigid processes of pharmaceutical manufacturing.
Introducing modular systems can help mitigate this challenge.
Implementing LEAN as a New Employee
As a new employee in the production technology department of a pharmaceutical company, embracing the LEAN methodology can be a career-defining move.
Understanding a few key implementation steps can help ease the transition:
Personal Development
First, invest time in understanding the nuances of LEAN production and its specific implications in pharmaceutical manufacturing.
Books, online courses, and industry workshops can be valuable resources.
Building a network with other LEAN professionals is also beneficial for exchanging knowledge and experiences.
Identifying Opportunities
As a fresh set of eyes in your department, you can provide valuable insights into processes that may have inefficiencies.
Seek early opportunities to contribute by suggesting small, manageable improvements within your team.
Data Utilization
Make data-driven decisions to identify waste and inefficiencies accurately.
Understanding data analytics and its applications in LEAN production can significantly enhance your ability to suggest impactful changes.
Collaborative Efforts
LEAN is a team effort, and collaboration is key to success.
Engage with your colleagues, share your insights, and encourage a culture of continuous improvement.
Facilitating workshops and discussions around LEAN can be a simple yet effective way to foster this environment.
The Future of LEAN in Pharmaceuticals
As the pharmaceutical industry continues to grow, the LEAN production method will remain a crucial component for maintaining competitive advantage.
Its emphasis on efficiency and waste reduction aligns well with the industry’s ongoing quest for innovation and quality.
For new employees entering the field, adopting and mastering LEAN production principles can provide significant personal and professional rewards.
The possibilities are vast, from accelerating career growth to contributing to life-changing advancements in pharmaceutical manufacturing.
資料ダウンロード
QCD調達購買管理クラウド「newji」は、調達購買部門で必要なQCD管理全てを備えた、現場特化型兼クラウド型の今世紀最高の購買管理システムとなります。
ユーザー登録
調達購買業務の効率化だけでなく、システムを導入することで、コスト削減や製品・資材のステータス可視化のほか、属人化していた購買情報の共有化による内部不正防止や統制にも役立ちます。
NEWJI DX
製造業に特化したデジタルトランスフォーメーション(DX)の実現を目指す請負開発型のコンサルティングサービスです。AI、iPaaS、および先端の技術を駆使して、製造プロセスの効率化、業務効率化、チームワーク強化、コスト削減、品質向上を実現します。このサービスは、製造業の課題を深く理解し、それに対する最適なデジタルソリューションを提供することで、企業が持続的な成長とイノベーションを達成できるようサポートします。
オンライン講座
製造業、主に購買・調達部門にお勤めの方々に向けた情報を配信しております。
新任の方やベテランの方、管理職を対象とした幅広いコンテンツをご用意しております。
お問い合わせ
コストダウンが利益に直結する術だと理解していても、なかなか前に進めることができない状況。そんな時は、newjiのコストダウン自動化機能で大きく利益貢献しよう!
(Β版非公開)