- お役立ち記事
- Basics of 5S activities and points for success that new employees in the production operations department should learn
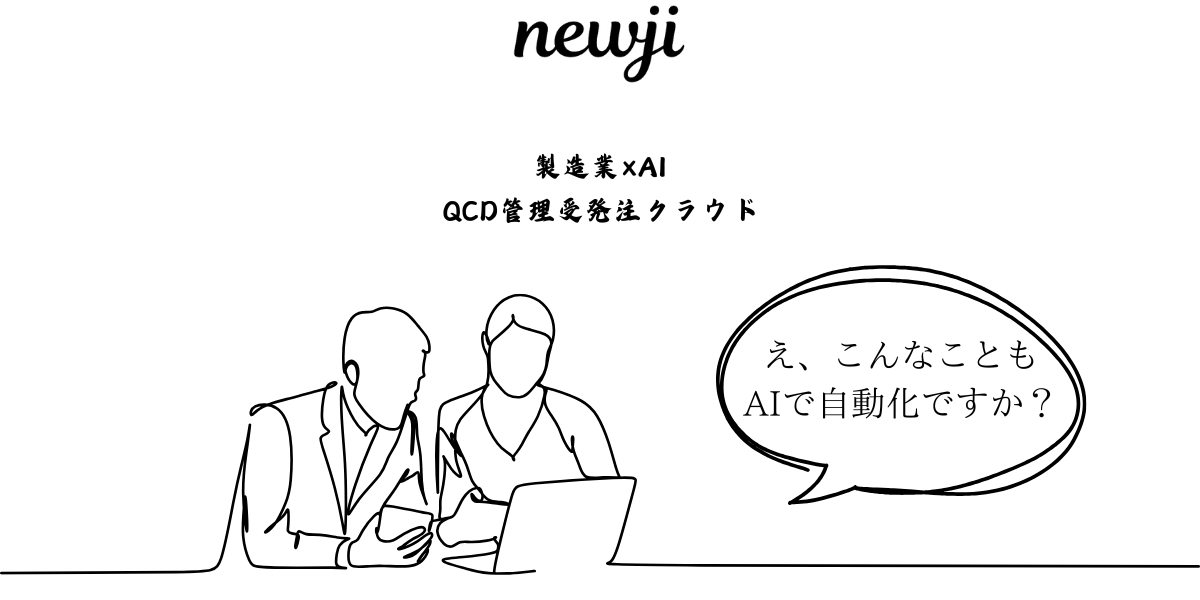
Basics of 5S activities and points for success that new employees in the production operations department should learn
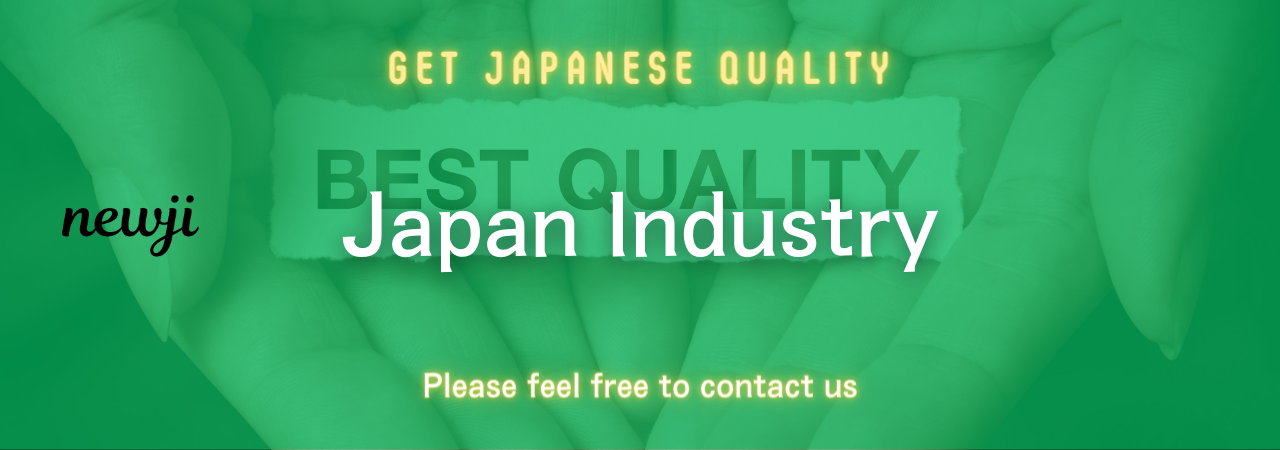
目次
Understanding the Basics of 5S Activities
The concept of 5S activities stems from Japanese management practices, specifically from the philosophy of Kaizen, which means continuous improvement.
These activities are well-known for boosting efficiency, safety, and productivity within an organization, especially in production operations.
5S stands for Seiri (Sort), Seiton (Set in order), Seiso (Shine), Seiketsu (Standardize), and Shitsuke (Sustain).
Each step plays a vital role in creating a well-organized and efficient workplace.
New employees in the production operations department are encouraged to familiarize themselves with these steps and their significance.
Seiri (Sort)
The first step, Seiri, involves decluttering the workspace.
Unnecessary items should be removed from the area, ensuring that only essential tools and materials remain.
This process helps in identifying valuable assets and reducing distractions that can lead to inefficiencies.
A workplace free of clutter is easier to navigate and can significantly reduce the time spent searching for tools or materials.
For new employees, understanding the importance of Seiri is crucial.
It results in a safer working environment, minimizing the risk of accidents that occur due to misplaced or unused items.
Seiton (Set in Order)
Once the unnecessary items have been sorted, the next step, Seiton, ensures that everything that remains has a designated place.
This step focuses on organizing the tools and materials in a manner that enhances workflow.
For beginners, it may be helpful to label storage locations and provide visual guides to assist in identifying where things belong.
Efficiency increases as workers do not need to waste time searching for what they need.
Seiton keeps everything accessible and consistently arranged, enabling a smooth workflow.
Seiso (Shine)
The third step, Seiso, involves cleaning the workspace and maintaining its cleanliness.
A tidy work environment not only promotes hygiene but also helps in identifying potential problems such as leakages or deteriorating machinery at an early stage.
New employees should embrace the habit of cleaning as part of their daily routine.
Maintaining cleanliness should not be a one-time event but a continuous process that everyone participates in.
Seiso creates a safer work area and fosters a sense of pride among workers, motivating them to maintain high standards.
Seiketsu (Standardize)
Seiketsu, the fourth step, focuses on standardizing the processes within the production operations.
Setting standard procedures ensures that tasks are performed consistently and efficiently.
For newcomers, understanding the value of standardization means recognizing the importance of uniformity.
Clear guidelines and checklists can aid in maintaining consistent practices across various departments.
Documenting best practices and establishing protocols is crucial.
This step not only enhances efficiency but also simplifies training processes for new employees, providing them with clear expectations and reducing errors.
Shitsuke (Sustain)
The final element of 5S, Shitsuke, is about sustaining the improvements made.
It involves fostering a culture of discipline and continuously improving work processes.
New employees should strive to adopt 5S practices as part of their daily routine.
Regular audits and routine check-ups can help reinforce these practices, ensuring long-term success in the organization.
Promoting a culture that values discipline and continuous improvement makes it easier for everyone to adhere to these practices consistently.
Points for Success in 5S Implementation
Implementing 5S activities requires more than just understanding each step.
Success depends on various factors that ensure everybody in the organization is on board.
Here are some crucial points to consider:
Commitment from Leadership
The role of leadership is pivotal in the success of 5S activities.
Managers and supervisors should demonstrate their commitment to the process.
When leaders are actively involved, it sets an example and encourages employees to follow suit.
Support from management ensures that adequate resources, such as time and training, are dedicated to 5S activities.
This commitment indicates to employees that the organization values these practices.
Training and Education
Educating employees about 5S activities is vital for their effective implementation.
Training sessions should focus on explaining the philosophy behind 5S, the benefits it brings, and techniques for executing each step successfully.
For new employees, hands-on training sessions and regular workshops can aid in understanding and embedding the 5S mindset.
Education empowers employees to identify areas for improvement, fostering a culture of continuous enhancement.
Continuous Evaluation and Feedback
To ensure the prolonged success of 5S activities, consistent evaluation and feedback mechanisms should be in place.
Regular assessments and audits help in determining the effectiveness of the implementation process.
Feedback from employees can offer valuable insights into potential adjustments needed to improve efficiency.
By encouraging employees to share their experiences, companies can continuously adapt their 5S activities to suit evolving circumstances.
Encouraging Employee Involvement
Engaging employees at all levels is key to the success of 5S activities.
Workers are more likely to embrace and implement these practices when they feel they are part of the process.
Hosting regular meetings where staff can voice concerns and suggest improvements creates a sense of ownership of the 5S process.
Recognizing and rewarding employees for their contributions can further motivate them to maintain high standards.
Conclusion
For new employees in production operations, understanding 5S activities provides a solid foundation for enhancing efficiency and productivity in the workplace.
Adopting practices such as sorting, organizing, cleaning, standardizing, and sustaining efforts leads to a more structured, safe, and efficient environment.
Successful implementation of 5S activities relies on commitment from leadership, effective training, regular evaluation, and active participation from employees.
By embedding the principles of 5S into the organizational culture, companies can ensure long-term improvements and set the stage for ongoing success in their operations.
資料ダウンロード
QCD調達購買管理クラウド「newji」は、調達購買部門で必要なQCD管理全てを備えた、現場特化型兼クラウド型の今世紀最高の購買管理システムとなります。
ユーザー登録
調達購買業務の効率化だけでなく、システムを導入することで、コスト削減や製品・資材のステータス可視化のほか、属人化していた購買情報の共有化による内部不正防止や統制にも役立ちます。
NEWJI DX
製造業に特化したデジタルトランスフォーメーション(DX)の実現を目指す請負開発型のコンサルティングサービスです。AI、iPaaS、および先端の技術を駆使して、製造プロセスの効率化、業務効率化、チームワーク強化、コスト削減、品質向上を実現します。このサービスは、製造業の課題を深く理解し、それに対する最適なデジタルソリューションを提供することで、企業が持続的な成長とイノベーションを達成できるようサポートします。
オンライン講座
製造業、主に購買・調達部門にお勤めの方々に向けた情報を配信しております。
新任の方やベテランの方、管理職を対象とした幅広いコンテンツをご用意しております。
お問い合わせ
コストダウンが利益に直結する術だと理解していても、なかなか前に進めることができない状況。そんな時は、newjiのコストダウン自動化機能で大きく利益貢献しよう!
(Β版非公開)