- お役立ち記事
- Basics of APQP and quality control practices that new employees in quality control departments in the automotive industry should know
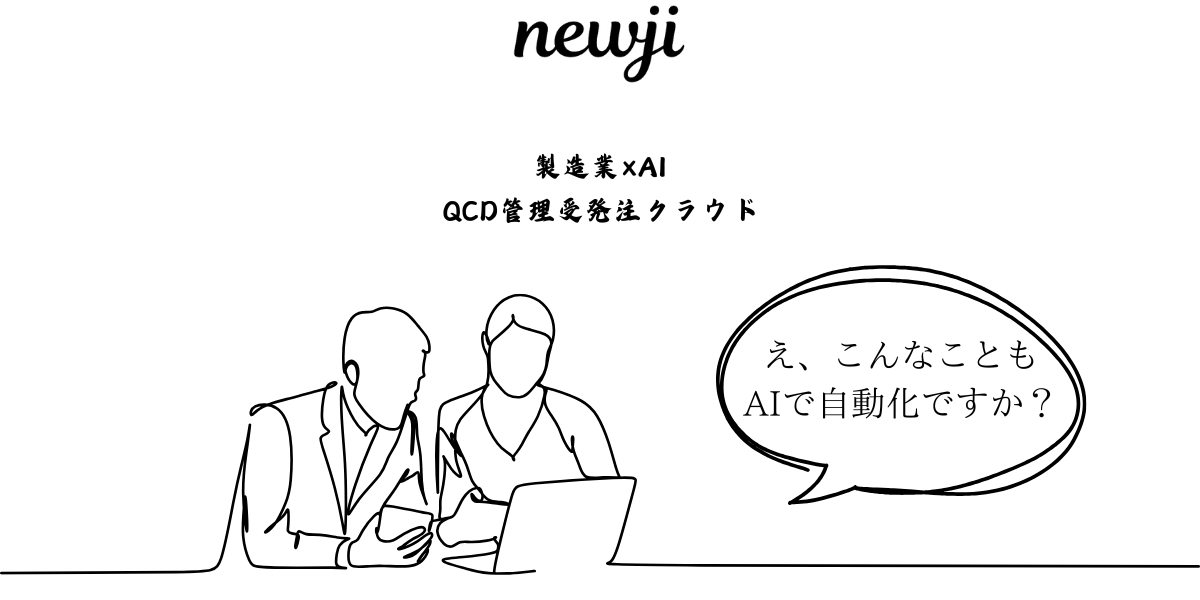
Basics of APQP and quality control practices that new employees in quality control departments in the automotive industry should know
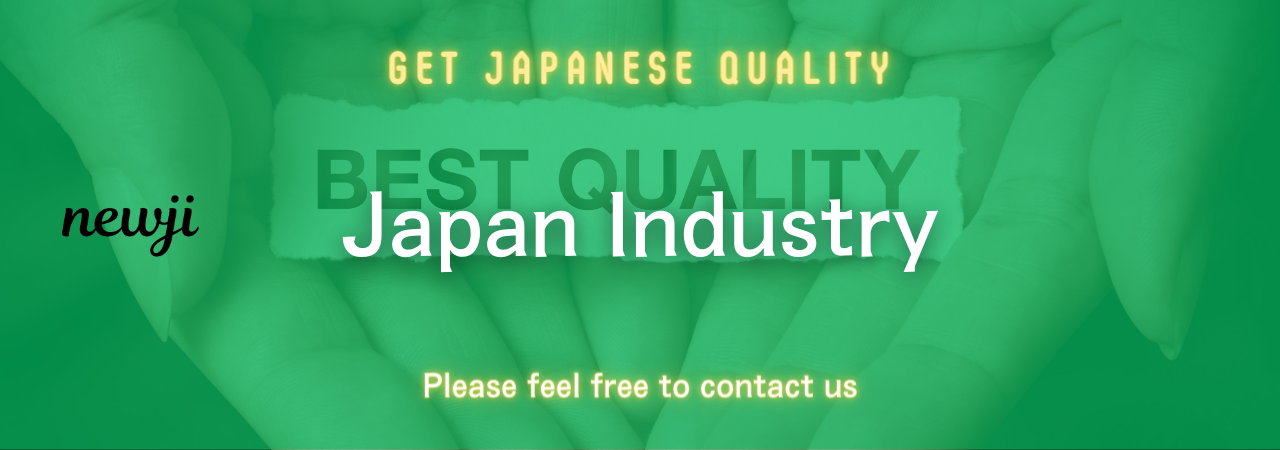
目次
Understanding APQP: A Key Component of Quality Control
APQP, or Advanced Product Quality Planning, is an essential framework utilized in the automotive industry to ensure the highest quality standards during product development.
For those new to the quality control departments, grasping the fundamentals of APQP is crucial as it forms the backbone of quality assurance processes.
The goal of APQP is to facilitate communication between all stakeholders, including suppliers and customers, to avert issues related to design and manufacturing.
This proactive approach prioritizes the prevention of defects, providing a smoother transition from concept to production.
The Five Phases of APQP
APQP is structured into five distinct phases, each serving a specific purpose in the quality planning process.
Phase 1: Planning and Definition
This initial phase focuses on understanding the customer’s needs and expectations.
New employees should pay particular attention to the importance of thorough planning and customer feedback to set the groundwork for success.
This phase involves risk assessment, feasibility studies, and defining the project scope.
Phase 2: Product Design and Development
Here, the focus is on translating customer requirements into precise design specifications.
New entrants should understand how design failure mode and effects analysis (DFMEA) is used to anticipate potential failures.
Also, they should learn about design verification and validation, which ensures that the design meets all predetermined criteria before moving forward.
Phase 3: Process Design and Development
In this phase, the spotlight shifts to designing the processes that will produce the final product.
A robust process flow diagram and process failure mode and effects analysis (PFMEA) are vital components.
Employees should learn how these tools are used to identify and mitigate risks in the manufacturing process.
Process validations are also performed here to confirm that processes are capable of producing compliant products consistently.
Phase 4: Product and Process Validation
This stage ensures that the product and processes perform as expected under actual conditions.
It involves conducting a production run, where quality control measures such as measurement system analysis (MSA) and statistical process control (SPC) are implemented.
New employees should become familiar with these tools to understand their role in maintaining product quality.
Phase 5: Feedback, Assessment, and Corrective Action
The final phase focuses on continuous improvement.
Feedback from the production process is assessed to identify areas of improvement.
Corrective actions are then implemented to enhance product quality and process efficiency.
For those new to quality control, understanding how to analyze this feedback is crucial for making informed improvements.
Quality Control Practices Every New Employee Should Master
In addition to understanding APQP, new employees should familiarize themselves with core quality control practices fundamental to the automotive industry.
Employee Training and Involvement
An effective quality control program begins with well-trained employees who understand their roles in maintaining product quality.
Continual training ensures that everyone is knowledgeable about the latest quality standards and techniques.
Standard Operating Procedures (SOPs)
SOPs are detailed guidelines designed to ensure consistency and uniformity in product quality.
New employees should recognize the importance of adhering to these procedures to reduce variability and maintain quality.
Inspection and Testing
Regular inspection and testing are pivotal in catching defects early in the production process.
Learning the key testing methods and tools, such as non-destructive testing (NDT) and dimensional inspections, is beneficial for new personnel.
Corrective and Preventive Actions (CAPA)
CAPA is critical for addressing and preventing future production issues.
As part of their role, employees should become adept at identifying root causes and implementing solutions.
Documentation and Record Keeping
Accurate record-keeping is necessary for tracking quality performance and meeting regulatory requirements.
Employees should understand how to document quality control activities effectively.
The Importance of Communication in Quality Control
Clear and effective communication is crucial in ensuring that all team members are aware of quality standards and process changes.
For new employees, building strong communication skills is essential for coordinating with different departments and stakeholders.
Embracing Continuous Improvement
Quality control is not a one-time event but a continuous process.
Encouraging an environment that prioritizes continuous improvement can lead to innovative solutions and enhanced product quality.
As a new employee in the automotive industry’s quality control sector, embracing APQP and mastering key quality practices will set the foundation for a successful career.
These principles not only help in understanding the manufacturing process but also ensure that every product meets the rigorous standards expected in the automotive industry.
資料ダウンロード
QCD調達購買管理クラウド「newji」は、調達購買部門で必要なQCD管理全てを備えた、現場特化型兼クラウド型の今世紀最高の購買管理システムとなります。
ユーザー登録
調達購買業務の効率化だけでなく、システムを導入することで、コスト削減や製品・資材のステータス可視化のほか、属人化していた購買情報の共有化による内部不正防止や統制にも役立ちます。
NEWJI DX
製造業に特化したデジタルトランスフォーメーション(DX)の実現を目指す請負開発型のコンサルティングサービスです。AI、iPaaS、および先端の技術を駆使して、製造プロセスの効率化、業務効率化、チームワーク強化、コスト削減、品質向上を実現します。このサービスは、製造業の課題を深く理解し、それに対する最適なデジタルソリューションを提供することで、企業が持続的な成長とイノベーションを達成できるようサポートします。
オンライン講座
製造業、主に購買・調達部門にお勤めの方々に向けた情報を配信しております。
新任の方やベテランの方、管理職を対象とした幅広いコンテンツをご用意しております。
お問い合わせ
コストダウンが利益に直結する術だと理解していても、なかなか前に進めることができない状況。そんな時は、newjiのコストダウン自動化機能で大きく利益貢献しよう!
(Β版非公開)