- お役立ち記事
- Basics of casting technology and its application in manufacturing
Basics of casting technology and its application in manufacturing
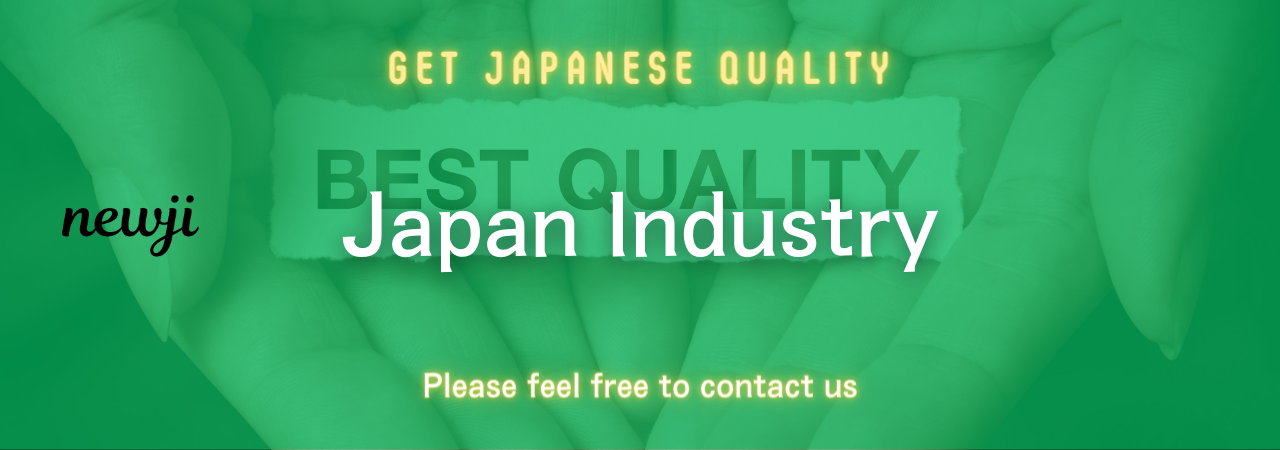
Casting technology is an intricate and fascinating field that plays a vital role in modern manufacturing.
Essentially, it involves pouring a liquid material into a mold where it cools and solidifies into a specific shape.
This process has been fundamental in producing intricate and complex parts for various industries, including automotive, aerospace, and construction.
目次
Understanding Casting Technology
What is Casting?
Casting is a manufacturing process where a liquid material, commonly metal, but also plastic, is poured into a mold.
The mold contains a hollow cavity of the desired shape.
Once the material cools and hardens, it adopts the shape of the mold.
This technique allows for the production of complex shapes that would be difficult or even impossible to achieve through other methods like machining or forging.
Materials Used in Casting
Different materials are used in casting based on the end-use of the product.
Commonly, materials like metals (iron, aluminum, steel, bronze), plastics, ceramics, and even concrete are used.
Each material has its own set of properties that make it suitable for specific applications.
For example, aluminum is lightweight and corrosion-resistant, making it ideal for the automotive and aerospace industries.
The Casting Process: Step-by-Step Guide
Pattern Making
The first step in the casting process is creating a pattern.
This pattern is essentially a replica of the final product.
It’s used to form the mold cavity.
Patterns are usually made from materials like wood, plastic, or metal.
The choice of material depends on factors like the complexity of the design and the number of castings to be produced.
Mold Making
Once the pattern is prepared, it’s used to create the mold.
There are various types of molds, including sand molds, ceramic molds, and metal molds.
The mold must be designed to handle the high temperatures and pressures involved in the casting process.
In some cases, molds are disposable and destroyed after the casting, while in other cases, they are designed to be reusable.
Pouring
With the mold ready, the next step is the actual pouring of the liquid material.
This requires carefully controlling the temperature to ensure the material flows properly and fills the entire mold cavity.
Special equipment, like crucibles and furnaces, is used to melt and handle the material safely.
Once poured, the material needs time to cool and solidify.
This step is crucial as it determines the final properties of the cast product.
Cooling and Solidification
After pouring, the material is left to cool and solidify within the mold.
The rate of cooling can significantly affect the mechanical properties of the finished product.
In some cases, cooling is accelerated using techniques like forced air or water cooling.
In other scenarios, controlled cooling is preferred to prevent internal stresses or cracks.
Mold Removal
Once the material has fully solidified, the mold is removed.
This step can involve breaking and removing the mold material (for disposable molds) or carefully extracting the cast part (for reusable molds).
Advanced techniques like automated mold ejection systems can help streamline this process in high-volume production environments.
Finishing
The final step in the casting process is finishing.
This involves cleaning, grinding, or machining the cast part to remove any excess material and achieve the desired surface finish.
Sometimes, additional treatments like heat treatment or coating are applied to enhance the properties of the cast part further.
Applications of Casting Technology in Manufacturing
Automotive Industry
Casting technology is widely used in the automotive industry to produce engine blocks, crankshafts, brake drums, and various other parts.
The ability to create complex shapes with high precision makes casting an ideal choice for automotive manufacturers.
Moreover, materials like aluminum and steel are preferred for their strength and durability.
Aerospace Industry
In the aerospace industry, casting is utilized to produce lightweight yet strong components necessary for aircraft and spacecraft.
Parts like turbine blades, engine housings, and structural components are often cast to ensure they meet stringent safety and performance standards.
Construction Industry
The construction industry also benefits significantly from casting technology.
From structural components like beams and columns to aesthetic elements like decorative panels, casting provides the versatility to produce a wide range of products.
Materials like concrete and metal are commonly used in construction casting applications.
Medical Devices
Casting plays a crucial role in the medical field by producing components for medical devices and implants.
High-precision casting techniques ensure that parts like artificial joints, dental implants, and surgical instruments meet the strict regulatory requirements for medical applications.
Consumer Goods
From household appliances to electronics, casting technology is employed to manufacture various consumer goods.
The ability to mass-produce complex parts quickly and cost-effectively makes casting an attractive option for consumer goods manufacturers.
Advantages and Challenges of Casting Technology
Advantages
Casting offers numerous advantages that make it a preferred choice for many manufacturers.
It allows for the creation of complex shapes that would be difficult or impossible to achieve through other methods.
Casting also enables high-volume production, making it cost-effective for mass manufacturing.
Additionally, the flexibility to use various materials means that manufacturers can choose the best material for specific applications.
Challenges
Despite its advantages, casting technology also presents certain challenges.
Controlling the cooling rate and preventing defects like porosity, shrinkage, or cracks requires careful process management.
Moreover, the need for specialized equipment and the initial cost of creating molds can be significant.
The Future of Casting Technology
The future of casting technology is promising, with ongoing advancements aimed at improving the efficiency and quality of the casting process.
Innovations like 3D printing for mold creation, automated casting systems, and the development of new materials are set to revolutionize the industry.
These advancements will not only enhance the capabilities of casting technology but also open up new possibilities for its application in manufacturing.
Casting technology is a cornerstone of modern manufacturing, providing the means to produce complex and high-quality parts across various industries.
By understanding the basics of casting and its applications, manufacturers can leverage this versatile technology to meet the growing demands of an ever-evolving market.
資料ダウンロード
QCD調達購買管理クラウド「newji」は、調達購買部門で必要なQCD管理全てを備えた、現場特化型兼クラウド型の今世紀最高の購買管理システムとなります。
ユーザー登録
調達購買業務の効率化だけでなく、システムを導入することで、コスト削減や製品・資材のステータス可視化のほか、属人化していた購買情報の共有化による内部不正防止や統制にも役立ちます。
NEWJI DX
製造業に特化したデジタルトランスフォーメーション(DX)の実現を目指す請負開発型のコンサルティングサービスです。AI、iPaaS、および先端の技術を駆使して、製造プロセスの効率化、業務効率化、チームワーク強化、コスト削減、品質向上を実現します。このサービスは、製造業の課題を深く理解し、それに対する最適なデジタルソリューションを提供することで、企業が持続的な成長とイノベーションを達成できるようサポートします。
オンライン講座
製造業、主に購買・調達部門にお勤めの方々に向けた情報を配信しております。
新任の方やベテランの方、管理職を対象とした幅広いコンテンツをご用意しております。
お問い合わせ
コストダウンが利益に直結する術だと理解していても、なかなか前に進めることができない状況。そんな時は、newjiのコストダウン自動化機能で大きく利益貢献しよう!
(Β版非公開)