- お役立ち記事
- Basics of etching technology in semiconductor manufacturing, the latest technology, and troubleshooting
月間76,176名の
製造業ご担当者様が閲覧しています*
*2025年3月31日現在のGoogle Analyticsのデータより
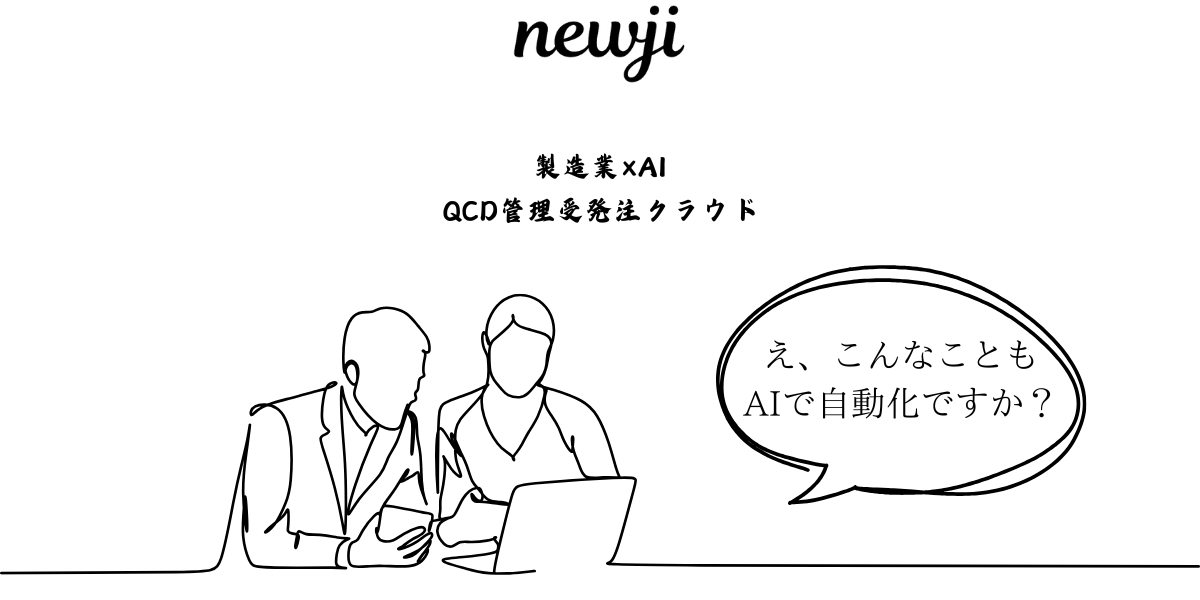
Basics of etching technology in semiconductor manufacturing, the latest technology, and troubleshooting
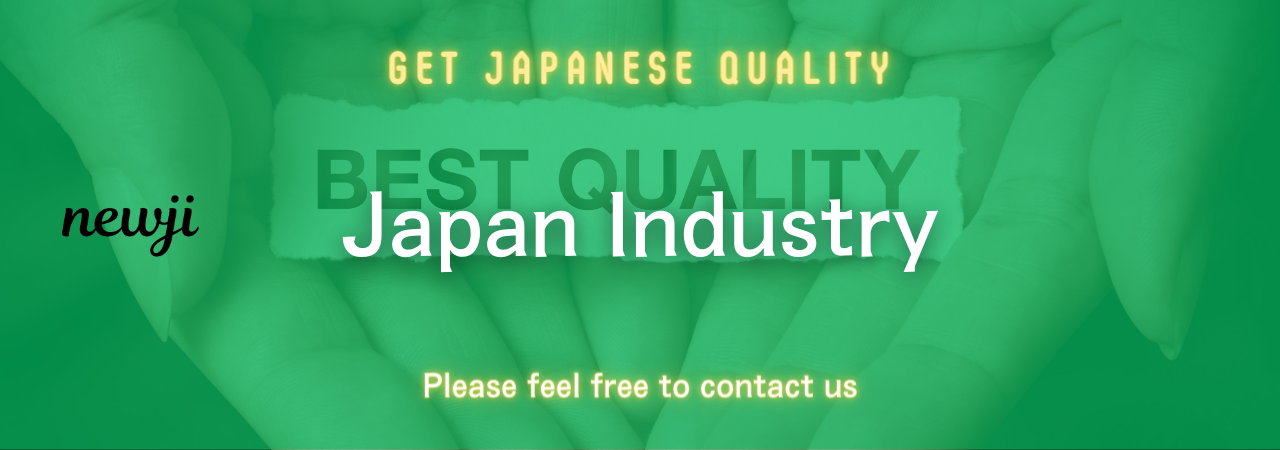
目次
Understanding Etching in Semiconductor Manufacturing
Semiconductor manufacturing is a complex process that involves multiple steps to create the tiny chips powering modern electronic devices.
One of the critical steps in this process is etching, a technology that shapes and defines the intricate patterns on semiconductor wafers.
Understanding the basics of etching technology is essential for anyone involved in semiconductor manufacturing.
What is Etching?
Etching is a process used to remove layers from the surface of a semiconductor wafer.
This is done to create the desired patterns and structures used in integrated circuits.
The process involves selectively removing material, leaving behind the required shapes while protecting other areas.
There are two main types of etching: wet etching and dry etching.
Wet Etching
Wet etching involves using chemical solutions to remove material from the wafer surface.
This method is typically used for materials that can be dissolved easily with the right chemical mixture.
Wet etching has the advantage of being cost-effective and easy to implement.
However, it also has limitations, such as difficulty in controlling isotropy, which can lead to undercutting.
Dry Etching
Dry etching, on the other hand, uses gases and plasmas to etch materials from the wafer.
This method offers greater precision compared to wet etching and is preferred for applications requiring fine control.
Dry etching includes techniques like plasma etching, reactive ion etching (RIE), and deep reactive ion etching (DRIE).
The choice between wet and dry etching depends on the material being processed and the specific requirements of the semiconductor design.
The Latest Technology in Etching
The semiconductor industry continually seeks to improve etching processes to keep pace with the demand for more powerful and efficient devices.
Recent advances in etching technology have led to finer feature sizes, better process control, and increased efficiency.
Atomic Layer Etching (ALE)
One of the latest breakthroughs in etching technology is Atomic Layer Etching (ALE).
ALE is a highly precise technique that allows for etching at the atomic level.
This method improves accuracy and uniformity, making it ideal for the ever-decreasing sizes of semiconductor features.
ALE enables manufacturers to finely control etching processes, crucial for creating next-generation electronics.
High Aspect Ratio Etching (HARE)
High Aspect Ratio Etching (HARE) has also seen significant advancements.
HARE is essential for creating deep structures with high aspect ratios on semiconductor wafers.
It involves finely tuned processes that ensure uniformity and accuracy, even at deep levels.
These technologies allow manufacturers to produce components required for advanced microelectronics with high precision.
Advancements in Gas Chemistry
The development of new gases and chemistries has also played a role in pushing etching technology forward.
These innovations help achieve cleaner and more efficient reactions during the etching process.
By carefully selecting gas chemistry, manufacturers can enhance the selectivity and precision of etching processes, leading to better performance in semiconductor devices.
Troubleshooting Common Etching Issues
Despite the advancements in etching technology, challenges still exist.
Troubleshooting issues is an essential aspect of ensuring high-quality semiconductor manufacturing.
Undercutting
Undercutting occurs when etching removes material beyond the intended boundaries, potentially damaging the device’s structure.
To minimize this issue, precise control over etching parameters and careful selection of etching techniques are vital.
Advanced simulation tools and monitoring systems can help identify and mitigate undercutting problems.
Non-uniform Etching
Non-uniform etching can lead to inconsistent device performance.
Regular maintenance, calibration of equipment, and uniform process conditions are vital to achieving consistent results.
Utilizing modern etching technologies, such as ALE, can help improve uniformity across the wafer.
Resist Erosion
Resist erosion happens when the protective layer used in etching becomes compromised.
Optimizing etching conditions and materials ensures that the resist layer maintains its integrity throughout the process.
Proper selection of resist materials and periodic evaluations can prevent erosion-related issues.
Conclusion
Understanding the basics of etching technology in semiconductor manufacturing is crucial for producing reliable and efficient electronic devices.
With advancements such as Atomic Layer Etching and High Aspect Ratio Etching, manufacturers can achieve unparalleled precision and performance.
However, maintaining optimal conditions and addressing common etching issues are essential for successful semiconductor manufacturing.
As the industry continues to evolve, staying updated on the latest etching technologies will ensure ongoing improvements in device fabrication.
資料ダウンロード
QCD管理受発注クラウド「newji」は、受発注部門で必要なQCD管理全てを備えた、現場特化型兼クラウド型の今世紀最高の受発注管理システムとなります。
ユーザー登録
受発注業務の効率化だけでなく、システムを導入することで、コスト削減や製品・資材のステータス可視化のほか、属人化していた受発注情報の共有化による内部不正防止や統制にも役立ちます。
NEWJI DX
製造業に特化したデジタルトランスフォーメーション(DX)の実現を目指す請負開発型のコンサルティングサービスです。AI、iPaaS、および先端の技術を駆使して、製造プロセスの効率化、業務効率化、チームワーク強化、コスト削減、品質向上を実現します。このサービスは、製造業の課題を深く理解し、それに対する最適なデジタルソリューションを提供することで、企業が持続的な成長とイノベーションを達成できるようサポートします。
製造業ニュース解説
製造業、主に購買・調達部門にお勤めの方々に向けた情報を配信しております。
新任の方やベテランの方、管理職を対象とした幅広いコンテンツをご用意しております。
お問い合わせ
コストダウンが利益に直結する術だと理解していても、なかなか前に進めることができない状況。そんな時は、newjiのコストダウン自動化機能で大きく利益貢献しよう!
(β版非公開)