- お役立ち記事
- Basics of material mechanics and its application to mechanical strength design
Basics of material mechanics and its application to mechanical strength design
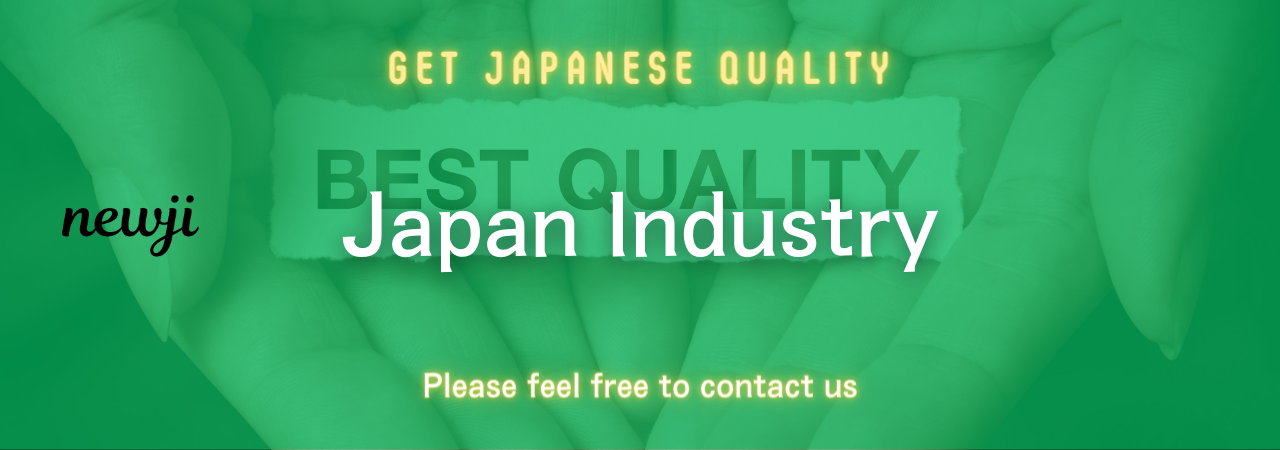
目次
Understanding Material Mechanics
Material mechanics is a fundamental aspect of engineering that deals with the behavior of materials under various forces and conditions.
This field plays a crucial role in the design and analysis of structures, machines, and products.
By understanding the principles of material mechanics, engineers can predict how materials will respond to different loads, thereby ensuring safety and efficiency.
The Basics of Material Mechanics
At the core of material mechanics are concepts that explain how materials deform and fail under stress.
Some of the key concepts include stress, strain, elasticity, and plasticity.
Stress refers to the internal force per unit area within a material that arises due to externally applied forces.
It is often measured in Pascals (Pa) or Megapascals (MPa).
Strain, on the other hand, describes the deformation of a material in response to applied stress.
It is a dimensionless quantity, representing the relative change in shape or size.
Elasticity is the property of materials to return to their original shape after the removal of stress.
Materials that display high elasticity are capable of significant deformation without permanent damage.
Plasticity, conversely, is the ability of a material to undergo permanent deformation without breaking when stress exceeds its elastic limit.
This behavior is crucial for processes like metal forming and molding.
Material Properties and Their Importance
Materials are characterized by their mechanical properties, which are inherent attributes influencing their response to external forces.
These properties include tensile strength, compressive strength, hardness, toughness, and ductility.
Tensile strength is the maximum stress a material can withstand while being stretched or pulled before breaking.
Compressive strength, similarly, is the ability of a material to resist being crushed.
Hardness measures a material’s resistance to deformation, scratching, or wear.
Hard materials like diamonds are used in applications where wear resistance is paramount.
Toughness is the ability of a material to absorb energy and plastically deform without fracturing.
It combines strength and ductility, making it crucial in impact applications.
Ductility refers to a material’s capability to be drawn into thin wires or sheets without breaking.
Metals like copper and aluminum exhibit excellent ductility, making them suitable for various industrial applications.
Applications of Material Mechanics in Mechanical Strength Design
Designing for Strength and Durability
Mechanical strength design involves creating components and structures that can endure operational loads without failure.
By applying principles of material mechanics, engineers can optimize designs for strength and durability.
One key application is in the automotive industry, where components must meet rigorous safety and performance standards.
Engineers use material mechanics to design car frames that absorb impact energy efficiently in case of collisions, protecting passengers.
In aerospace, the challenge is to design lightweight yet strong structures to minimize fuel consumption and maximize payload.
Material mechanics informs the selection of materials and structural design to achieve these goals, leading to the use of composite materials and alloys.
Failure Analysis and Prevention
Material mechanics is also critical in failure analysis, which involves examining and understanding material failures to prevent recurrences.
By studying stress and strain patterns, engineers can identify root causes of failures, such as fatigue or stress concentrations.
Fatigue is the progressive and localized structural damage that occurs when a material is subjected to cyclic loading.
Engineers use material mechanics to predict the lifespan of components under repetitive stress, tailoring designs to improve fatigue resistance.
Stress concentrations, areas where stress is significantly higher than the surrounding material, can lead to failure.
Designers apply principles of material mechanics to minimize these concentrations, often by altering geometry or introducing fillets.
Innovations in Material Mechanics
Advancements in material mechanics are driving innovation across industries.
The development of new materials, such as smart materials and metamaterials, are expanding the possibilities of design and functionality.
Smart materials can change properties in response to external stimuli like temperature, pressure, or electric fields.
Incorporating these materials into mechanical designs leads to adaptive systems that improve performance and safety.
Metamaterials, engineered with unique structures at micro and nano scales, exhibit properties not found in naturally occurring materials.
These materials open new avenues for innovation in optics, acoustics, and mechanical engineering.
Conclusion
Material mechanics serves as the backbone of mechanical strength design, providing the knowledge and tools necessary to create safe, efficient, and innovative products.
By understanding the behavior of materials under different conditions, engineers can predict performance, design for longevity, and innovate with new materials and technologies.
Whether in automotive, aerospace, construction, or consumer products, the principles of material mechanics continue to shape the future of engineering design.
資料ダウンロード
QCD調達購買管理クラウド「newji」は、調達購買部門で必要なQCD管理全てを備えた、現場特化型兼クラウド型の今世紀最高の購買管理システムとなります。
ユーザー登録
調達購買業務の効率化だけでなく、システムを導入することで、コスト削減や製品・資材のステータス可視化のほか、属人化していた購買情報の共有化による内部不正防止や統制にも役立ちます。
NEWJI DX
製造業に特化したデジタルトランスフォーメーション(DX)の実現を目指す請負開発型のコンサルティングサービスです。AI、iPaaS、および先端の技術を駆使して、製造プロセスの効率化、業務効率化、チームワーク強化、コスト削減、品質向上を実現します。このサービスは、製造業の課題を深く理解し、それに対する最適なデジタルソリューションを提供することで、企業が持続的な成長とイノベーションを達成できるようサポートします。
オンライン講座
製造業、主に購買・調達部門にお勤めの方々に向けた情報を配信しております。
新任の方やベテランの方、管理職を対象とした幅広いコンテンツをご用意しております。
お問い合わせ
コストダウンが利益に直結する術だと理解していても、なかなか前に進めることができない状況。そんな時は、newjiのコストダウン自動化機能で大きく利益貢献しよう!
(Β版非公開)