- お役立ち記事
- Basics of surface hardening heat treatment technology and countermeasures against defects and troubles
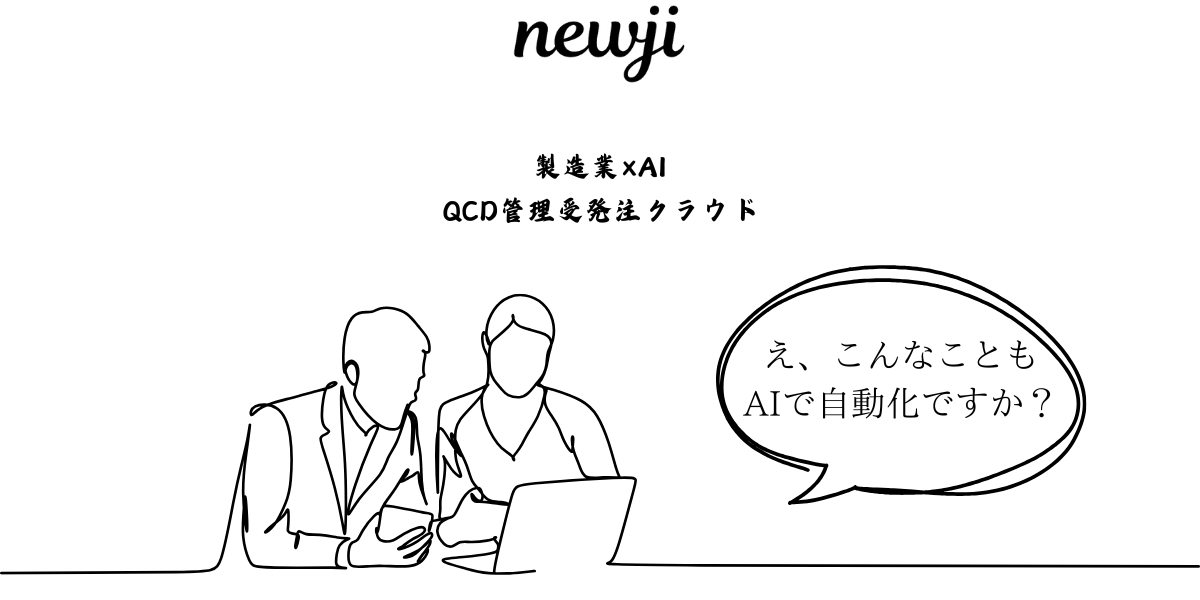
Basics of surface hardening heat treatment technology and countermeasures against defects and troubles
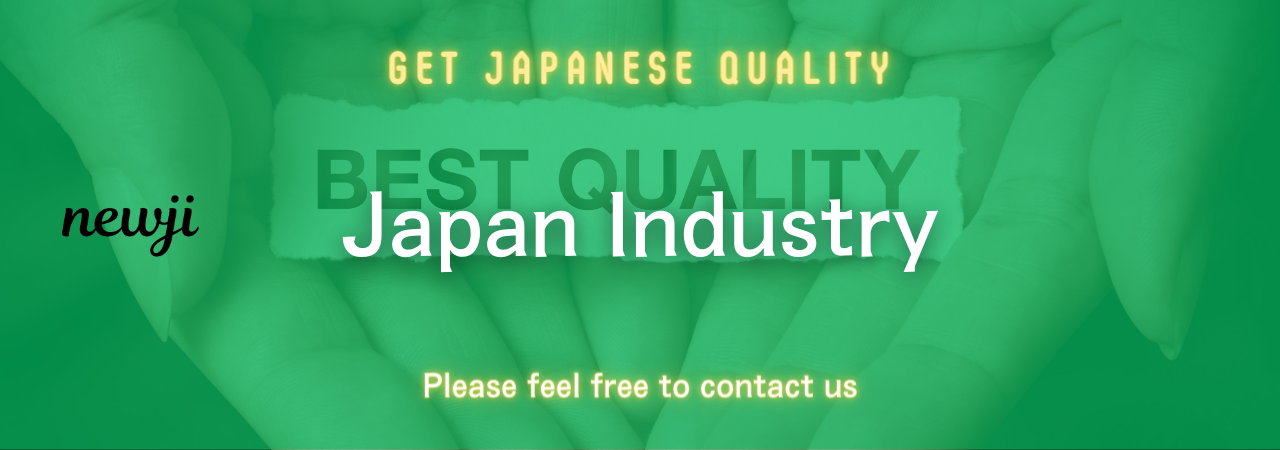
目次
Understanding Surface Hardening Heat Treatment
Surface hardening is a crucial process in the field of metallurgy and manufacturing, aimed at enhancing the hardness and wear resistance of a metal surface.
By applying this technique, the life span and durability of components are significantly increased, especially those subject to friction and wear.
There are several methods used to achieve surface hardening, each with unique advantages depending on the material and the desired properties.
The process involves hardening only the outer layer of a component while keeping the core soft and ductile.
This is essential for applications like gears, bearings, and cutting tools, where a hard exterior guards against wear while a tough core absorbs impact.
Methods of Surface Hardening
Several techniques are employed for surface hardening, each suitable for different applications:
1. **Carburizing:**
This involves adding carbon to the surface of steel at high temperatures.
The steel is exposed to a carbon-rich atmosphere, allowing carbon atoms to diffuse into the surface.
Once cooled, the surface becomes hard.
2. **Nitriding:**
In this method, nitrogen is used instead of carbon.
The component is treated in an ammonia atmosphere at lower temperatures than carburizing.
This produces a very hard surface without the need for quenching.
3. **Induction Hardening:**
A heat treatment process where the metal is heated by induction heating and then quenched.
This method is advantageous because it is quick and allows for precise control over the area to be hardened.
4. **Flame Hardening:**
Similar to induction hardening but uses a direct flame.
The surface is rapidly heated and then quenched.
5. **Laser Hardening:**
This modern technique uses a laser beam as a heat source.
The intense heat hardens the surface, which is then cooled with air or water.
Benefits of Surface Hardening
Surface hardening impart several advantages such as:
– **Increased Wear Resistance:**
The hardened surface resists wear from friction and contact, which is particularly useful for parts in constant motion.
– **Improved Fatigue Strength:**
Hardened surfaces withstand cyclical stresses better, increasing the fatigue life of the component.
– **Localized Hardening:**
Only the areas that need to be hardened are treated, saving time and resources, and preserving the flexibility of the core material.
– **Cost Efficiency:**
By extending the life of components and reducing replacement frequency, surface hardening is a cost-effective solution.
Common Defects and Troubles in Surface Hardening
While surface hardening offers numerous benefits, it’s not without potential issues.
Identifying and mitigating these problems is crucial for ensuring the success of the process:
– **Distortion:**
The application of high temperatures and subsequent rapid cooling can cause components to warp.
Careful control of process parameters and choosing the right quenching medium can minimize this risk.
– **Cracking:**
If the material is too brittle post-treatment, it can crack.
Proper selection of steel grade and heat treatment technique is essential to avoid this.
– **Inadequate Hardening:**
Sometimes, the penetration of carbon or nitrogen is not uniform, leading to uneven hardness.
This can be mitigated by ensuring consistent temperature and atmosphere conditions during treatment.
– **Decarburization:**
Loss of carbon from the surface can occur, softening the outer layer unintentionally.
This can be prevented by maintaining a controlled atmosphere with sufficient carbon potential.
Strategies for Avoiding Defects
To ensure the best outcome of surface hardening, several strategies can be adopted:
1. **Pre-Process Analysis:**
Conduct thorough analysis of material properties and component design to select the most appropriate hardening method.
2. **Process Control:**
Employ precise control over temperatures, timing, and atmospheres to ensure consistent results.
3. **Quality Monitoring:**
Introduce quality checks at various stages of the treatment to catch any defects early.
4. **Post-Process Treatments:**
Implement secondary processes like tempering to relieve stresses and reduce the risk of cracking.
Conclusion
Surface hardening is a vital technology in manufacturing, providing the dual benefits of durability and toughness through a hardened surface layer.
By understanding the methods, benefits, and potential problems associated with this process, manufacturers can optimize their operations and deliver superior products.
Continuous innovation and process improvement will only enhance these benefits, pushing the boundaries of what components can achieve in terms of performance and longevity.
資料ダウンロード
QCD調達購買管理クラウド「newji」は、調達購買部門で必要なQCD管理全てを備えた、現場特化型兼クラウド型の今世紀最高の購買管理システムとなります。
ユーザー登録
調達購買業務の効率化だけでなく、システムを導入することで、コスト削減や製品・資材のステータス可視化のほか、属人化していた購買情報の共有化による内部不正防止や統制にも役立ちます。
NEWJI DX
製造業に特化したデジタルトランスフォーメーション(DX)の実現を目指す請負開発型のコンサルティングサービスです。AI、iPaaS、および先端の技術を駆使して、製造プロセスの効率化、業務効率化、チームワーク強化、コスト削減、品質向上を実現します。このサービスは、製造業の課題を深く理解し、それに対する最適なデジタルソリューションを提供することで、企業が持続的な成長とイノベーションを達成できるようサポートします。
オンライン講座
製造業、主に購買・調達部門にお勤めの方々に向けた情報を配信しております。
新任の方やベテランの方、管理職を対象とした幅広いコンテンツをご用意しております。
お問い合わせ
コストダウンが利益に直結する術だと理解していても、なかなか前に進めることができない状況。そんな時は、newjiのコストダウン自動化機能で大きく利益貢献しよう!
(Β版非公開)