- お役立ち記事
- Basics of tool selection and cutting technology that new employees in the mechanical engineering department should learn
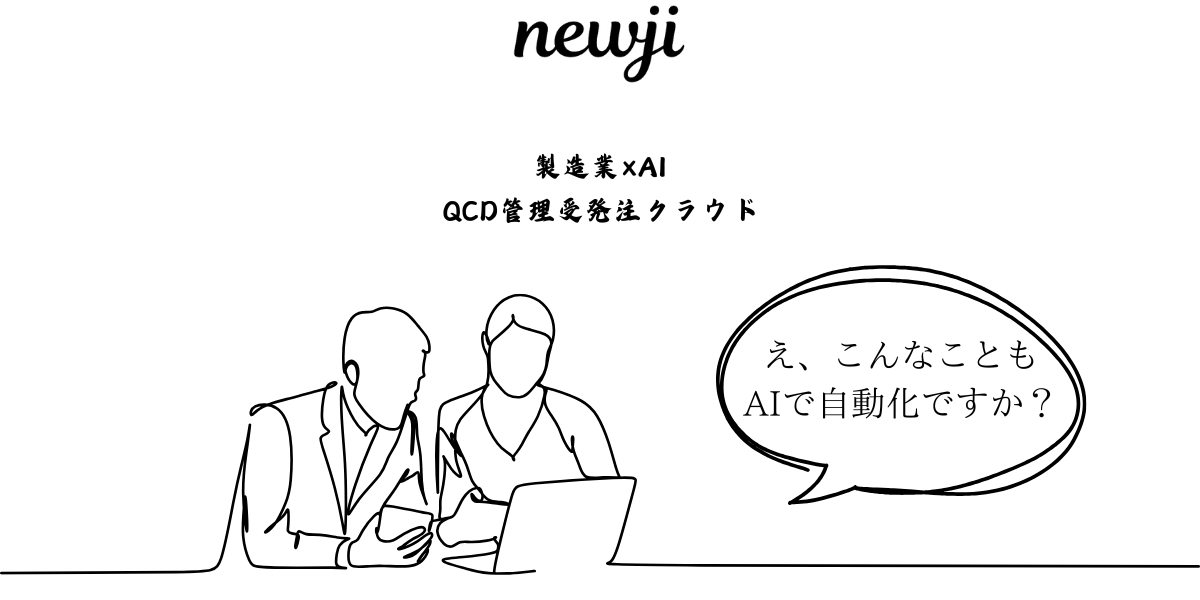
Basics of tool selection and cutting technology that new employees in the mechanical engineering department should learn
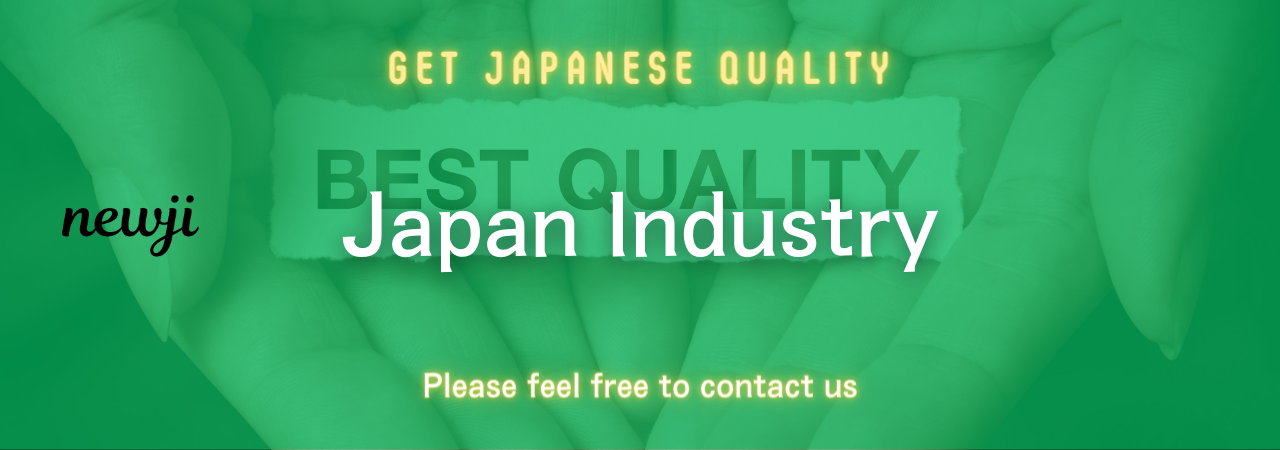
目次
Understanding Cutting Tools in Mechanical Engineering
New employees stepping into the realm of mechanical engineering often find themselves overwhelmed by the vast array of tools and technologies available.
One of the core skills to master in this field is understanding and selecting the right cutting tools.
This knowledge is crucial as it directly impacts the quality, efficiency, and cost-effectiveness of manufacturing processes.
In this guide, we’ll delve into the basics of tool selection and cutting technology to provide a strong foundation for newcomers in the mechanical engineering department.
What Are Cutting Tools?
Cutting tools are implements used to remove material from a workpiece through deformation.
This process shapes objects precisely and is essential in manufacturing industries.
There are various types of cutting tools designed for different operations and materials.
Common examples include drills, saws, milling cutters, and turning tools.
Each tool is engineered to enhance efficiency, accuracy, and finish quality.
Types of Cutting Tools
Cutting tools can be broadly categorized into two types: single-point and multi-point.
Single-point tools have a single cutting edge and are used for operations like turning or planing.
They are typically found in lathe machines.
Multi-point tools, such as milling cutters and drills, have multiple cutting edges.
These tools are used for high-speed and large-scale material removal.
Considerations for Tool Selection
Choosing the right tool is a critical step in any machining operation.
Here are some factors to consider:
1. **Material of the Workpiece**: Different materials require different tool properties.
For instance, cutting hard metals like steel requires tools made from carbide or coated with ceramics to withstand the heat and pressure.
2. **Type of Machining Operation**: Understand whether you need roughing (large material removal) or finishing (fine precision).
Tools designed for roughing have a different geometric profile than those for finishing.
3. **Tool Material and Coating**: The material and coating of the tool affect its durability and efficiency.
Common materials include high-speed steel (HSS), carbide, and ceramics.
Coatings such as titanium nitride improve wear resistance and prolong tool life.
4. **Tool Geometry**: The design of the tool, including its angles and shape, should align with the operation’s efficiency and accuracy.
Cutting Technology Basics
Understanding the basics of cutting technology involves comprehending how cutting actions occur.
This includes angles, speeds, and feeds – the rates at which the tool moves across or into the workpiece.
**Cutting Speed** refers to how fast the cutting edge moves.
The speed directly influences the tool’s temperature and lifespan.
**Feed Rate** is the distance the tool advances during one revolution or pass.
Proper feed rates ensure a smooth surface finish and prevent excessive tool wear.
**Depth of Cut** is the material thickness removed in one pass of the tool.
Determining the appropriate depth is essential to balancing efficiency and tool longevity.
Understanding Tool Wear and Maintenance
Tool wear is a natural result of friction and heat during the cutting process.
Recognizing the signs of wear extends working life and maintains quality.
Types of wear include:
– **Flank Wear**: Occurs on the tool’s flank face and can lead to a loss of cutting efficiency.
– **Crater Wear**: Happens on the rake face, affecting the tool’s strength and surface finish.
– **Built-Up Edge (BUE)**: Material sticks to the cutting edge, altering the tool’s geometry.
Regular maintenance and timely replacement of tools are vital to ensure consistent performance.
This involves regular inspection and cleaning of the tools, as well as following manufacturer guidelines for sharpening or replacing.
The Importance of Safety in Tool Handling
Safety is paramount in any machining environment.
New employees must understand safety protocols to prevent accidents.
Misuse or improper handling can lead to personal injury or damage to the machinery.
Key safety practices include:
– Always use the right tool for the task and ensure it is in good condition.
– Wear appropriate personal protective equipment (PPE) such as gloves and safety goggles.
– Keep work areas clean and free of obstructions.
– Use machine guards and ensure all machines have emergency stop features.
Continuing Education and Skill Development
The field of mechanical engineering is ever-evolving, with new tools and technologies constantly emerging.
It’s crucial for employees, especially newcomers, to engage in continuous learning.
Participating in workshops, seminars, and online courses can keep you updated with the latest advancements.
Networking with experienced professionals can also provide invaluable insights and tips.
Understanding the nuances of tool selection and cutting technology is an ongoing journey.
New employees should remain curious and proactive in honing their skills.
In conclusion, mastering the basics of tool selection and cutting technology forms the backbone of any successful mechanical engineering career.
By understanding the types, applications, and maintenance of tools, new employees can contribute effectively to their teams, ensuring efficient and safe operations.
With continual learning and adherence to safety practices, they will not only excel in their roles but also drive technological progress in the industry.
資料ダウンロード
QCD調達購買管理クラウド「newji」は、調達購買部門で必要なQCD管理全てを備えた、現場特化型兼クラウド型の今世紀最高の購買管理システムとなります。
ユーザー登録
調達購買業務の効率化だけでなく、システムを導入することで、コスト削減や製品・資材のステータス可視化のほか、属人化していた購買情報の共有化による内部不正防止や統制にも役立ちます。
NEWJI DX
製造業に特化したデジタルトランスフォーメーション(DX)の実現を目指す請負開発型のコンサルティングサービスです。AI、iPaaS、および先端の技術を駆使して、製造プロセスの効率化、業務効率化、チームワーク強化、コスト削減、品質向上を実現します。このサービスは、製造業の課題を深く理解し、それに対する最適なデジタルソリューションを提供することで、企業が持続的な成長とイノベーションを達成できるようサポートします。
オンライン講座
製造業、主に購買・調達部門にお勤めの方々に向けた情報を配信しております。
新任の方やベテランの方、管理職を対象とした幅広いコンテンツをご用意しております。
お問い合わせ
コストダウンが利益に直結する術だと理解していても、なかなか前に進めることができない状況。そんな時は、newjiのコストダウン自動化機能で大きく利益貢献しよう!
(Β版非公開)