- お役立ち記事
- Best practices for materials management and order quantity adjustment that support stable operations at manufacturing sites
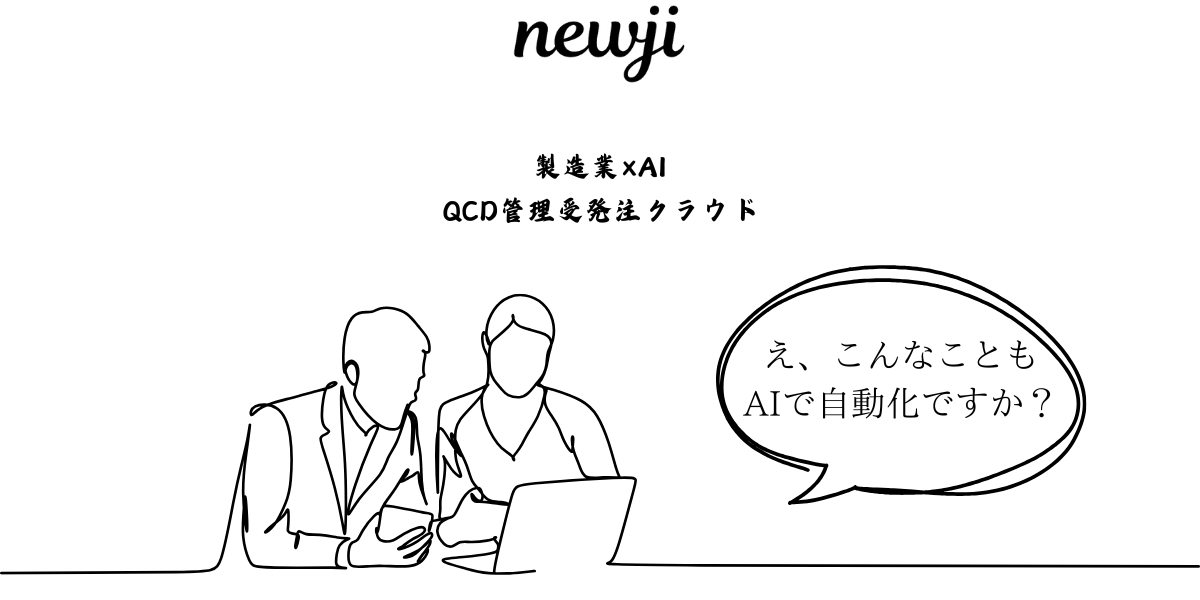
Best practices for materials management and order quantity adjustment that support stable operations at manufacturing sites
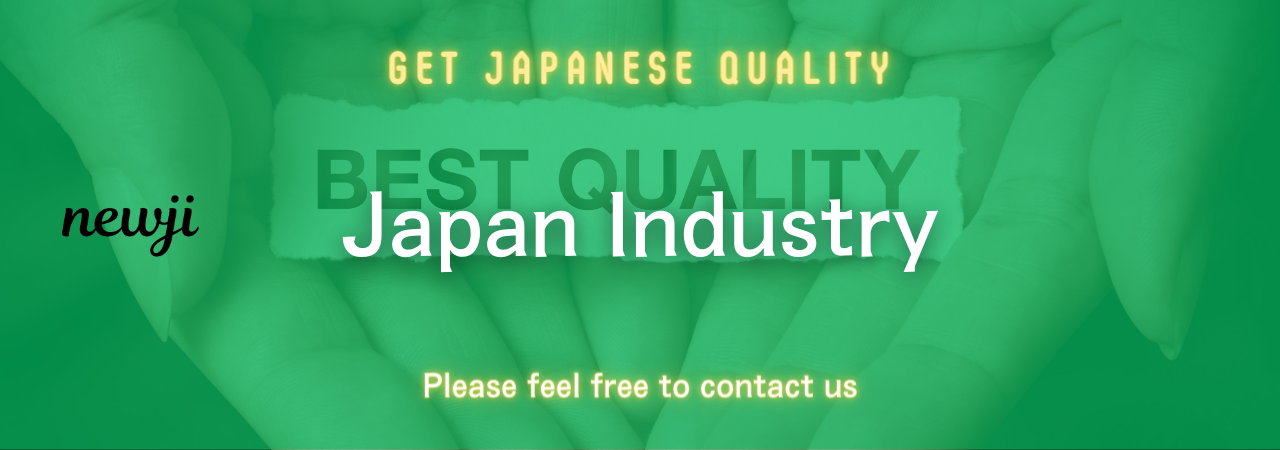
目次
Understanding Materials Management in Manufacturing
In the complex world of manufacturing, effective materials management is crucial for ensuring smooth operations.
Materials management involves the planning, sourcing, purchasing, moving, and storing of materials used during production.
Without a streamlined process, delays can occur, leading to cost spikes, decreased efficiency, and even project shutdowns.
Implementing best practices in materials management is key in overcoming these challenges.
By optimizing how materials are handled, manufacturers can minimize waste, reduce costs, and ensure that production schedules are met.
A structured approach not only supports stable operations but also improves overall productivity.
The Importance of Order Quantity Adjustment
Order quantity adjustment plays a central role in efficient materials management.
Ordering the right amount of materials is critical; too little and you risk halting production, too much and you tie up capital that could be used elsewhere.
Balancing these dynamics is essential for achieving operational efficiency.
Order quantity affects inventory levels, cash flow, and production timelines.
By continually adjusting order quantities, manufacturers can respond to changing market demands, reduce excess inventory, and streamline operating expenses.
Best Practices for Materials Management
Adhering to best practices can transform materials management from a logistical headache into a process-driven operation that supports manufacturing goals.
Here are some key practices to consider:
1. Implement a Centralized Inventory System
A centralized inventory system consolidates data and provides an overview of all materials.
This system ensures that information is accurate and up to date, reducing the risk of errors.
With a centralized system, manufacturers can track inventory levels in real-time, facilitating better decision-making.
2. Forecast Demand Accurately
Accurate demand forecasting allows companies to align their inventory with customer needs.
Utilizing historical data, market trends, and predictive analytics can generate reliable forecasts.
This helps in planning for peak periods and avoiding discrepancies that can lead to overproduction or insufficient supply.
3. Build Strong Supplier Relationships
Suppliers are key partners in the manufacturing process.
Fostering strong relationships with reliable suppliers ensures consistent quality and timely deliveries.
Establishing agreements on lead times and quality standards can prevent delays and maintain production schedules.
4. Conduct Regular Audits
Regular audits of inventory practices help identify inefficiencies and areas for improvement.
Audits provide insight into inventory levels, accuracy, and turnover rates.
By evaluating and adjusting processes, manufacturers can maintain optimal inventory levels and address potential issues proactively.
5. Implement Lean Manufacturing Techniques
Lean manufacturing principles focus on minimizing waste and maximizing value.
Adopting lean techniques such as Just-in-Time (JIT) can optimize materials management processes.
JIT reduces inventory costs by ensuring materials arrive only as needed, thus minimizing excess inventory and storage costs.
Adjusting Order Quantities for Better Outcomes
Finding the optimal order quantity requires a balance between inventory costs and demand fulfillment.
This involves strategic adjustments based on several factors:
1. Economic Order Quantity (EOQ) Model
The EOQ model helps determine the ideal order quantity that minimizes total inventory costs, including holding and ordering expenses.
By calculating EOQ, manufacturers can determine the most cost-effective ordering strategy to support smooth operations.
2. Monitor Inventory Turnover
Inventory turnover measures how often inventory is sold and replaced over a period.
High turnover indicates efficient management and synchronization with market demand.
By monitoring turnover rates, manufacturers can adjust order quantities to maintain inventory health and ensure products are fresh and in-demand.
3. Adopt a Reorder Point Strategy
Setting reorder points ensures that materials are reordered at the right time to prevent stockouts.
The reorder point is determined by understanding lead times, demand rates, and the safety stock needed to cover unexpected fluctuations.
This strategy keeps inventory levels balanced and production lines running smoothly.
4. Use Technology and Automation
Technology and automation tools streamline materials management by providing detailed insights into inventory operations.
Automated systems can alert managers when levels fall below reorder points or predict changes in demand.
Incorporating technology enhances accuracy, reduces manual errors, and improves responsiveness to changes in the supply chain.
Conclusion: Supporting Stable Operations
Implementing best practices in materials management and continuously adjusting order quantities are pivotal to supporting stable operations at manufacturing sites.
These strategies not only prevent disruptions but also lead to substantial cost savings and increased operational efficiency.
By applying these methods, manufacturers can better align their inventory management processes with organizational objectives.
Ultimately, optimizing materials management contributes to a more resilient and agile manufacturing environment capable of weathering the ever-evolving market conditions.
資料ダウンロード
QCD調達購買管理クラウド「newji」は、調達購買部門で必要なQCD管理全てを備えた、現場特化型兼クラウド型の今世紀最高の購買管理システムとなります。
ユーザー登録
調達購買業務の効率化だけでなく、システムを導入することで、コスト削減や製品・資材のステータス可視化のほか、属人化していた購買情報の共有化による内部不正防止や統制にも役立ちます。
NEWJI DX
製造業に特化したデジタルトランスフォーメーション(DX)の実現を目指す請負開発型のコンサルティングサービスです。AI、iPaaS、および先端の技術を駆使して、製造プロセスの効率化、業務効率化、チームワーク強化、コスト削減、品質向上を実現します。このサービスは、製造業の課題を深く理解し、それに対する最適なデジタルソリューションを提供することで、企業が持続的な成長とイノベーションを達成できるようサポートします。
オンライン講座
製造業、主に購買・調達部門にお勤めの方々に向けた情報を配信しております。
新任の方やベテランの方、管理職を対象とした幅広いコンテンツをご用意しております。
お問い合わせ
コストダウンが利益に直結する術だと理解していても、なかなか前に進めることができない状況。そんな時は、newjiのコストダウン自動化機能で大きく利益貢献しよう!
(Β版非公開)