- お役立ち記事
- Best practices for supply chain collaboration suggested by purchasing departments
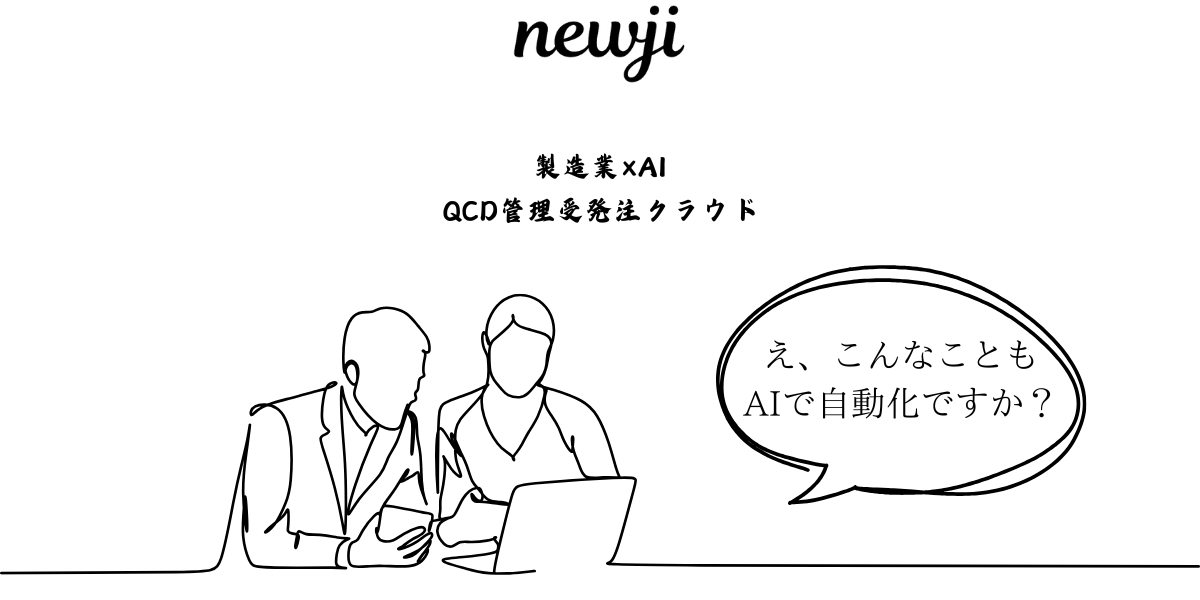
Best practices for supply chain collaboration suggested by purchasing departments
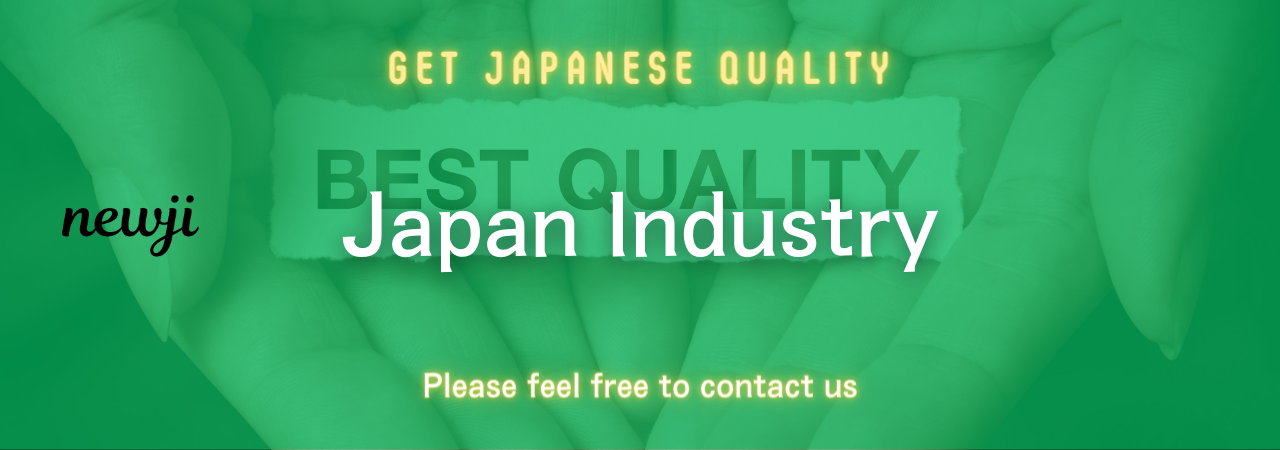
目次
Understanding Supply Chain Collaboration
Supply chain collaboration involves multiple organizations working together harmoniously to achieve a common goal.
The collaborative process can include sharing information, resources, and making joint decisions to enhance efficiency and improve overall performance.
Collaboration is essential in today’s fast-paced and tightly interconnected global market.
Purchasing departments play a crucial role in fostering this collaboration as they manage relationships with suppliers and coordinate procurement strategies.
The Importance of Effective Collaboration
Effective collaboration leads to improved supply chain transparency, reduced costs, and minimized risks.
When all parties have visibility into the supply chain, they can respond swiftly to disruptions or changes.
This proactive approach helps maintain a steady flow of goods and services.
Streamlined communication between purchase departments and suppliers ensures that inventory levels are optimized.
This reduces excess stock, thereby lowering costs and improving cash flow.
Collaboration also minimizes risks by pooling expertise and resources.
This collective approach can help foresee potential issues and develop mitigation strategies well in advance.
Key Practices for Successful Collaboration
There are several best practices suggested by purchasing departments to achieve effective supply chain collaboration.
Build Strong Relationships
Start by developing strong, trust-based relationships with suppliers.
Building trust necessitates consistent communication and delivering on commitments.
Mutual respect and understanding can transform supplier relationships from transactional to strategic partnerships.
This mindset encourages suppliers to engage more deeply and share insights that can benefit the overall supply chain.
Implement Transparent Communication
Transparent communication is the backbone of any successful collaboration.
Ensure there is a platform where stakeholders can openly share information, forecasts, and any challenges they might be facing.
Frequent updates keep everyone aligned, reducing misunderstandings and inefficiencies.
Using technology like integrated supply chain management systems can facilitate seamless communication pathways.
Encourage Joint Decision-Making
Engage suppliers in joint decision-making processes, particularly for major projects or when entering new markets.
Their unique insights and expertise can be incredibly beneficial in formulating strategies.
When suppliers are part of the decision-making team, they are more invested in the outcomes, leading to better cooperation and shared successes.
Leverage Technology
Digital tools can significantly enhance supply chain collaboration.
From real-time data analytics to automated systems, technology can help streamline operations, improve accuracy, and promote efficient communication.
Purchasing departments should invest in technology that allows for data sharing, effective monitoring, and improved forecasting.
This helps bridge gaps between stakeholders, promoting a unified approach to tackling supply chain challenges.
Focus on Flexibility and Agility
The modern supply chain environment is dynamic, with changes happening rapidly due to external and internal factors.
Therefore, it’s vital for purchasing departments to instill flexibility and agility into the collaboration framework.
This flexibility ensures that strategies and operations can pivot quickly to accommodate changes in demand, supply, and unforeseen disruptions.
Set Clear Objectives and Metrics
Clearly defined objectives and metrics are crucial for measuring the effectiveness of collaboration efforts.
Purchasing departments should establish key performance indicators (KPIs) that align with both supplier and internal goals.
These metrics could focus on delivery times, cost efficiencies, quality standards, and innovation.
Regularly reviewing these objectives ensures continuous improvement and alignment with larger business goals.
Conduct Regular Training and Workshops
Finally, regular training and workshops can provide the necessary understanding and skills to adapt to new collaborative strategies.
Educational sessions can cover best practices, new technologies, and ways to improve current processes.
This fosters a culture of continuous improvement and innovation within the supply chain.
Conclusion
Effective supply chain collaboration can be a game-changer for businesses looking to enhance their competitiveness in the market.
With the purchasing department at the helm, companies can implement these best practices for improved collaboration.
Trust, communication, technology, adaptability, clear objectives, and training form the foundation of a robust collaborative framework.
By embracing these strategies, businesses can ensure their supply chains are resilient, efficient, and poised to succeed in ever-changing market conditions.
資料ダウンロード
QCD調達購買管理クラウド「newji」は、調達購買部門で必要なQCD管理全てを備えた、現場特化型兼クラウド型の今世紀最高の購買管理システムとなります。
ユーザー登録
調達購買業務の効率化だけでなく、システムを導入することで、コスト削減や製品・資材のステータス可視化のほか、属人化していた購買情報の共有化による内部不正防止や統制にも役立ちます。
NEWJI DX
製造業に特化したデジタルトランスフォーメーション(DX)の実現を目指す請負開発型のコンサルティングサービスです。AI、iPaaS、および先端の技術を駆使して、製造プロセスの効率化、業務効率化、チームワーク強化、コスト削減、品質向上を実現します。このサービスは、製造業の課題を深く理解し、それに対する最適なデジタルソリューションを提供することで、企業が持続的な成長とイノベーションを達成できるようサポートします。
オンライン講座
製造業、主に購買・調達部門にお勤めの方々に向けた情報を配信しております。
新任の方やベテランの方、管理職を対象とした幅広いコンテンツをご用意しております。
お問い合わせ
コストダウンが利益に直結する術だと理解していても、なかなか前に進めることができない状況。そんな時は、newjiのコストダウン自動化機能で大きく利益貢献しよう!
(Β版非公開)